Vous avez des questions sur les slicer d’impression 3D et sur leur fonctionnement ? Imprimy est là pour tout vous expliquer
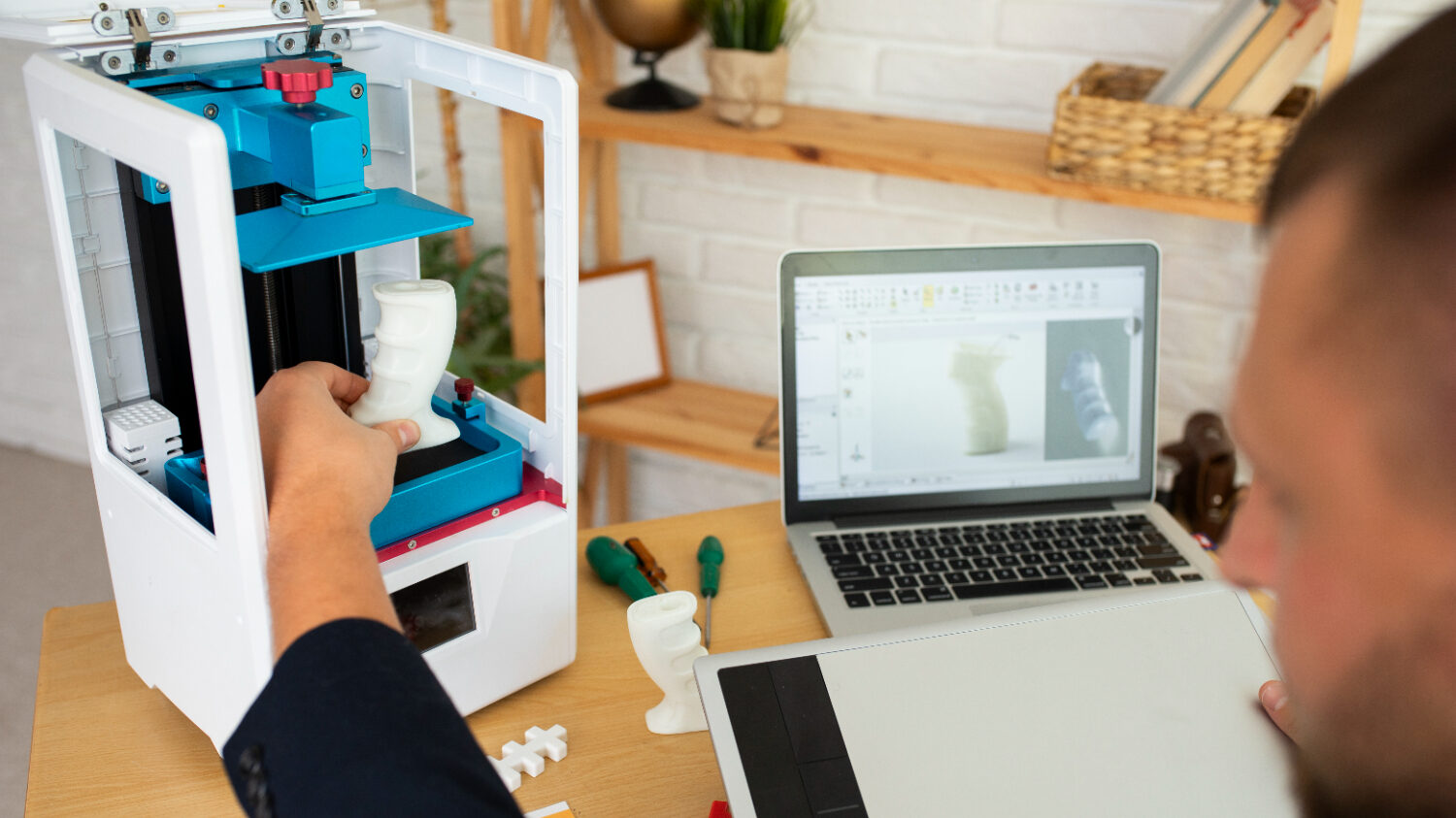
Qu’est-ce qu’un slicer pour l’impression 3D et comment ça fonctionne ?
Un slicer est un logiciel permettant de trancher couche par couche un modèle 3D afin de permettre sa traduction en commandes qui se transformeront en un objet physique.
- Qu'est-ce qu'un slicer pour l'impression 3D et comment ça fonctionne ?
- Quels sont les différents types de slicers disponibles?
- Comment utiliser un slicer ?
- Quels sont les réglages essentiels d’un slicer ?
- Quelles astuces pour optimiser les paramètres dans votre slicer ?
- Quels sont les problèmes courants pouvant être rencontrés avec les slicers ?
- Conclusion : slicer pour l'impression 3D
Rôle principal du slicer pour l’impression 3D
Le rôle principal du slicer pour l’impression 3D est de convertir un modèle 3D, généralement au format STL, en un fichier compréhensible par l’imprimante 3D. Le logiciel découpe le modèle en couches horizontales successives (d’où le terme « slicing ») et génère le G-code, un ensemble d’instructions détaillant les mouvements de l’extrudeuse, les paramètres de température, la vitesse d’impression et la gestion du remplissage et des supports.
Le slicer permet ainsi d’optimiser la qualité de l’impression tout en ajustant les paramètres pour obtenir le meilleur résultat en fonction des matériaux et des caractéristiques de l’imprimante.
Processus de découpe
Le processus de découpe dans un slicer consiste à diviser un modèle 3D en tranches horizontales, ou « couches« , qui seront ensuite imprimées une à une par l’imprimante 3D. Le slicer analyse la géométrie du modèle et détermine la manière dont chaque couche sera imprimée, en générant des trajets pour la tête d’impression, des mouvements précis pour déposer le filament.
Il prend également en compte des paramètres comme l’épaisseur de chaque couche, le type de remplissage, la vitesse d’impression, et l’utilisation éventuelle de supports pour les parties en surplomb. Ce processus permet de traduire un modèle virtuel en instructions exploitables par l’imprimante.
Les paramètres à définir
Les paramètres à définir dans un slicer sont essentiels pour garantir la qualité et la réussite de l’impression 3D. Parmi les plus importants, on trouve l’épaisseur des couches, qui influence la résolution et la vitesse d’impression, la température de la tête d’impression et du plateau, cruciales pour l’adhésion du filament et la fluidité de l’impression.
La vitesse d’impression doit également être ajustée en fonction du matériau et du niveau de détail souhaité. Le type et la densité du remplissage (infill) déterminent la solidité de l’objet, tandis que l’utilisation des supports est nécessaire pour les impressions avec des zones en surplomb. Enfin, des paramètres comme le retrait (retraction) et la ventilation sont cruciaux pour éviter les défauts comme le stringing ou le warping.
Quels sont les différents types de slicers disponibles?
Les logiciels open-source et les logiciels propriétaires
Les logiciels de slicing, essentiels pour l’impression 3D, se divisent en deux grandes catégories : les logiciels open-source et les logiciels propriétaires.
Les logiciels open-source offrent une grande flexibilité et sont souvent gratuits, permettant aux utilisateurs de personnaliser les paramètres et de contribuer à leur amélioration grâce à une communauté active. En revanche, les logiciels propriétaires sont développés par des entreprises qui en gardent le code source fermé et proposent souvent des fonctionnalités spécifiques ou une optimisation avancée en échange d’une licence payante. Le choix entre ces deux types dépend des besoins, des compétences techniques et du budget de l’utilisateur.
Les critères de choix d’un slicer
Le choix d’un slicer pour l’impression 3D repose sur plusieurs critères essentiels. Tout d’abord, la compatibilité avec l’imprimante 3D est primordiale, car certains slicers sont conçus pour des modèles spécifiques. Ensuite, l’expérience utilisateur joue un rôle clé : les débutants privilégieront des interfaces simples tandis que les experts pourraient rechercher des logiciels offrant un contrôle avancé des paramètres.
Les fonctionnalités disponibles, telles que les options de support, la gestion des matériaux et les profils prédéfinis, influencent également la décision. Enfin, le coût, les mises à jour régulières ainsi que le support technique ou communautaire sont des éléments importants à considérer pour assurer un usage optimal.
Comment utiliser un slicer ?
Pour utiliser un slicer, vous devez importer un modèle 3D puis régler certains paramètres. Vous pourrez alors prévisualiser le parcours de l’imprimante et générer les commandes sous la forme d’un G-code, qui sera envoyé à l’imprimante 3D.
Importation du modèle 3D
L’importation d’un modèle 3D dans un slicer est une étape essentielle du processus d’impression 3D. Cette opération commence par l’utilisation d’un fichier au format compatible, tel que STL, OBJ ou parfois 3MF, qui contient les données géométriques du modèle. Une fois le fichier importé, le slicer permet de visualiser le modèle, de vérifier sa taille, son orientation et sa position sur le plateau virtuel de l’imprimante.
Il est important de s’assurer que le modèle est correctement orienté pour minimiser les supports nécessaires et optimiser la qualité d’impression. Certains slicers offrent également des outils de réparation automatique pour corriger les erreurs géométriques éventuelles avant de passer à l’étape suivante, celle du paramétrage et de la génération du fichier G-code.
Réglages des paramètres d’impression
Les réglages des paramètres d’impression dans un slicer sont cruciaux pour garantir une impression 3D réussie et adaptée au projet. Parmi les principaux paramètres, on trouve la hauteur de couche, qui détermine la résolution et la finesse des détails, ainsi que la vitesse d’impression, influençant à la fois la qualité et le temps nécessaire. Le réglage de la température d’extrusion et du plateau est essentiel pour assurer une bonne adhérence et éviter les défauts liés au matériau utilisé.
D’autres paramètres incluent le remplissage, permettant de définir la solidité de l’objet, ainsi que la gestion des supports et des bordures, utiles pour stabiliser les pièces complexes. Un réglage minutieux de ces options en fonction du matériau et du modèle garantit un équilibre optimal entre qualité, vitesse et consommation de filament.
Prévisualisation du parcours d’impression
La prévisualisation du parcours d’impression est une étape essentielle avant de lancer l’impression 3D, permettant de vérifier et d’optimiser les paramètres configurés. Cette fonctionnalité, disponible dans la majorité des slicers, offre une représentation graphique du trajet de la buse couche par couche, mettant en évidence des aspects tels que les remplissages, les supports, les mouvements de rétraction et les transitions.
Elle permet de repérer des erreurs potentielles, comme des zones mal supportées, des épaisseurs incohérentes ou des déplacements inutiles qui pourraient allonger le temps d’impression ou affecter la qualité finale. Grâce à cette vue détaillée, l’utilisateur peut ajuster les réglages avant de générer le fichier G-code, garantissant ainsi une impression plus précise et efficace.
Génération du G-code
La génération du G-code est l’étape finale dans un slicer avant l’impression 3D, consistant à traduire le modèle 3D et les paramètres configurés en instructions compréhensibles pour l’imprimante. Ce code contient des commandes précises, telles que les déplacements de la buse, les vitesses d’impression, les températures d’extrusion et de plateau, ainsi que les ordres liés au remplissage et à la gestion des supports.
Chaque ligne de G-code correspond à une action spécifique, permettant à l’imprimante de construire l’objet couche par couche. Une fois généré, le fichier est sauvegardé et transféré à l’imprimante, généralement via une carte SD, une clé USB ou une connexion réseau, prêt à être exécuté pour produire le modèle physique.
Envoi à l’imprimante 3D
L’envoi du fichier G-code à l’imprimante 3D constitue la dernière étape avant le lancement de l’impression. Selon le modèle d’imprimante, cela peut se faire de différentes manières : par carte SD ou clé USB pour les imprimantes dotées de ports physiques, ou par connexion réseau (Wi-Fi, Ethernet) pour les modèles plus récents et connectés.
Certains slicers intègrent des options d’envoi direct, permettant de transmettre le fichier depuis un ordinateur via une interface dédiée. Une fois le fichier chargé dans l’imprimante, il est crucial de vérifier que tous les réglages matériels, tels que le nivellement du plateau et la disponibilité du filament, sont correctement effectués. Une fois ces vérifications terminées, l’imprimante peut être démarrée pour exécuter les instructions du G-code et produire l’objet en 3D.
Quels sont les réglages essentiels d’un slicer ?
Les réglages essentiels des slicer incluent l’épaisseur de couche, la vitesse d’impression, la génération des supports, le choix de la bonne température ou encore du taux de remplissage.
Gérer l’épaisseur des couches
Gérer l’épaisseur des couches est un paramètre clé en impression 3D, car il influence directement la qualité, la solidité et le temps d’impression. Une épaisseur de couche fine, généralement entre 0,1 mm et 0,2 mm, offre une meilleure résolution et des détails plus précis, ce qui est idéal pour des objets décoratifs ou complexes.
En revanche, des couches plus épaisses, autour de 0,3 mm ou plus, permettent une impression plus rapide et conviennent mieux aux pièces fonctionnelles où la finesse des détails est moins critique. Ce réglage doit être adapté à la taille de la buse (par exemple, une buse de 0,4 mm fonctionne bien avec des couches de 0,2 mm) et au matériau utilisé, afin de garantir un équilibre entre qualité et performance.
Définir la vitesse d’impression
La vitesse d’impression en impression 3D détermine la rapidité avec laquelle la buse se déplace pour déposer le filament, influençant à la fois la qualité et la durée de l’impression. Elle est généralement exprimée en millimètres par seconde (mm/s) et peut varier en fonction des besoins et du type de filament utilisé. Une vitesse plus lente, autour de 30 à 50 mm/s, est recommandée pour obtenir des détails fins ou pour des matériaux difficiles comme le TPU ou l’ABS.
À l’inverse, une vitesse plus élevée, jusqu’à 100 mm/s ou plus, convient pour des impressions rapides, mais peut entraîner une diminution de la précision. Il est important de trouver un équilibre en tenant compte des capacités de l’imprimante, de la qualité souhaitée et du comportement du filament pour éviter des défauts tels que des débordements ou des sous-extrusions.
Générer des supports
La génération de supports est une fonctionnalité essentielle dans l’impression 3D, permettant de créer des structures temporaires pour soutenir les parties du modèle qui dépassent ou sont suspendues dans l’air pendant l’impression. Les supports sont particulièrement utiles pour imprimer des objets avec des porte-à-faux, des ponts ou des formes complexes.
Les slicers offrent différentes options de génération de supports, notamment les supports en structure arborescente (tree-like) ou en lignes régulières, et permettent de choisir la densité, l’angle d’inclinaison des supports et le type de matériau utilisé (par exemple, le même filament que celui du modèle ou un matériau soluble comme le PVA). Ces supports sont ensuite retirés après l’impression, soit manuellement, soit par dissolution si le matériau utilisé est soluble. Une gestion fine des supports permet de réduire la consommation de matériau, le temps d’impression et la difficulté de post-traitement.
Choisir la bonne température d’impression
Choisir la bonne température d’impression est crucial pour obtenir des résultats optimaux en impression 3D. La température d’extrusion, c’est-à-dire celle de la buse, varie en fonction du matériau utilisé. Par exemple, pour des plastiques courants comme le PLA, une température d’extrusion entre 190°C et 220°C est généralement recommandée, tandis que pour des matériaux comme l’ABS, la température doit être réglée entre 230°C et 250°C.
La température du plateau est également importante, car elle aide à assurer une bonne adhésion de la première couche. Pour le PLA, un plateau chauffant à 50°C à 60°C est suffisant, alors que pour l’ABS, il doit être chauffé à 90°C ou plus. Un mauvais choix de température peut entraîner des problèmes comme la sous-extrusion, le warping ou une mauvaise adhérence. Il est donc essentiel de consulter les recommandations du fabricant de filament et d’ajuster la température en fonction des spécificités de l’imprimante et des conditions d’impression.
Indiquer le bon type et le bon taux de remplissage
Le type et le taux de remplissage (ou « infill ») sont des paramètres clés pour déterminer la solidité, le poids et la durée d’impression d’un objet 3D. Le type de remplissage dépend de l’application et de la géométrie de l’objet : les motifs classiques incluent les lignes (rectilignes), les grilles, les structures en nid d’abeille (honeycomb) ou les motifs plus complexes comme les triangles ou les gyros. Les structures en nid d’abeille offrent un bon compromis entre solidité et légèreté, tandis que les motifs linéaires ou en grilles sont plus rapides à imprimer mais peuvent être moins solides.
Le taux de remplissage, exprimé en pourcentage, détermine la densité interne de l’objet. Un taux faible, autour de 10 à 20 %, est suffisant pour des objets décoratifs ou légers, tandis qu’un taux plus élevé, entre 40 % et 100 %, est nécessaire pour des pièces fonctionnelles nécessitant une solidité accrue. Un taux de remplissage plus élevé augmente le temps d’impression et la consommation de filament, mais améliore la résistance mécanique de l’objet. Il est donc important de choisir un type et un taux adaptés aux besoins spécifiques de l’impression, en équilibrant qualité, performance et coût de matériaux.
Quelles astuces pour optimiser les paramètres dans votre slicer ?
Vous pouvez améliorer votre slicer en optimisant la vitesse d’impression, en retirant les supports inutiles, en contrôlant les défauts courants ou bien encore en réalisant des impressions tests.
Optimiser la vitesse d’impression sans perte de qualité
Optimiser la vitesse d’impression sans sacrifier la qualité nécessite d’ajuster plusieurs paramètres clés. Tout d’abord, il est essentiel de définir la vitesse d’impression de manière adéquate en fonction du matériau et des caractéristiques du modèle. Réduire la vitesse d’impression des couches plus détaillées tout en maintenant une vitesse plus élevée pour les couches moins complexes peut améliorer l’efficacité sans compromettre la précision.
Il est également possible d’augmenter la largeur de la première couche, ce qui favorise une meilleure adhésion au plateau, tout en réduisant le nombre de couches nécessaires. Utiliser un taux de remplissage adapté (moins élevé pour des objets moins soumis à des contraintes mécaniques) et opter pour un motif de remplissage plus simple ou moins dense peuvent également réduire le temps d’impression. De plus, l’optimisation de la température de la buse et du plateau peut permettre une extrusion plus rapide sans sous-extrusion ou autres défauts.
Enfin, en utilisant un profil de couche plus épaisse et une buse de plus grand diamètre, il est possible de réduire le nombre de couches tout en maintenant une bonne qualité d’impression.
Retirer les supports inutiles
Retirer les supports inutiles est une étape cruciale pour améliorer l’esthétique et réduire le temps de post-traitement en impression 3D. Pour éviter la création de supports inutiles, il est important de bien configurer les paramètres du slicer. Par exemple, ajuster l’angle minimal de surplomb pour que le slicer génère des supports uniquement là où ils sont réellement nécessaires, comme les porte-à-faux importants.
De plus, certains slicers offrent des options pour ajuster la densité ou la forme des supports, permettant ainsi de les rendre plus faciles à retirer et de réduire leur consommation de filament. Dans certains cas, l’utilisation de supports « à contact léger » ou « en ligne » permet de minimiser la surface de contact avec la pièce et facilite leur retrait. Enfin, l’optimisation de la géométrie du modèle 3D, en réduisant les zones difficiles à imprimer, peut également diminuer le besoin de supports, permettant de réaliser des impressions de meilleure qualité sans trop de post-traitement.
Contrôler les défauts courants
Contrôler les défauts courants en impression 3D est essentiel pour garantir une qualité d’impression optimale. Parmi les défauts fréquents, on trouve le warping (déformation des coins de l’objet), souvent causé par une température du plateau trop basse ou un refroidissement trop rapide. Pour l’éviter, il est conseillé de chauffer correctement le plateau et d’utiliser une base d’adhésion comme un raft ou un brim.
- La sous-extrusion, où l’imprimante ne dépose pas assez de filament, peut être due à une température d’extrusion trop basse, une buse partiellement bouchée ou une vitesse d’impression trop rapide ; il est important de vérifier l’état de la buse et d’ajuster les températures et vitesses.
- Le stringing (formation de fils entre les parties du modèle) survient souvent à cause d’une température trop élevée ou d’une mauvaise rétraction ; une optimisation des paramètres de rétraction et une réduction de la température d’extrusion peuvent résoudre ce problème.
- Les bulles d’air dans les impressions peuvent être causées par une vitesse trop élevée ou des paramètres de remplissage inadaptés, qu’il convient d’ajuster pour améliorer la solidité.
- Enfin, un mauvais nivellement du plateau peut entraîner une mauvaise adhésion de la première couche ou une extrusion irrégulière, ce qui peut être corrigé par un calibrage précis du plateau.
Une attention aux paramètres, ainsi qu’une vérification régulière de l’imprimante, permettent de limiter ces défauts et d’obtenir des impressions de meilleure qualité.
Réaliser des impressions test
Réaliser des impressions test est une étape essentielle pour s’assurer que les paramètres d’impression sont correctement configurés avant de lancer une production plus importante. Ces impressions permettent de vérifier la qualité d’impression, d’ajuster les paramètres et d’identifier d’éventuels défauts sans gaspiller de matériel. Parmi les tests les plus courants, on trouve l’impression d’un cube de calibration (par exemple, un cube de 20x20x20 mm), qui permet de vérifier la précision des dimensions et l’adhérence des premières couches.
D’autres tests incluent des pièces plus complexes comme un benchy, qui permettent d’évaluer la qualité de finition, les supports, la gestion des surplombs et le remplissage. En fonction des résultats, des ajustements peuvent être effectués sur les paramètres de température, de vitesse d’impression, de rétraction, ou encore de type de support. En effectuant plusieurs impressions test, il devient plus facile de perfectionner les réglages et d’obtenir des résultats optimaux pour des impressions plus grandes et plus complexes.
Quels sont les problèmes courants pouvant être rencontrés avec les slicers ?
Les problèmes associés aux slicers peuvent être associés à des erreurs de G-code, à de l’incompatibilité avec certains modèles 3D ou bien encore par une optimisation insuffisante des supports.
Une erreur de génération du G-code
Une erreur de génération du G-code peut survenir pour diverses raisons et entraîner des problèmes lors de l’impression 3D. Les erreurs les plus courantes incluent des commandes incorrectes, des paramètres mal configurés ou des fichiers corrompus. Par exemple, si le slicer utilise un mauvais profil d’imprimante ou des paramètres incompatibles avec le modèle 3D (comme une taille de buse incorrecte ou une température inappropriée), le G-code généré peut ne pas être exécuté correctement par l’imprimante, provoquant des erreurs d’impression, telles que des sous-extrusions, des couches manquantes ou des mouvements erratiques de la tête d’impression.
Pour résoudre cette erreur, il est important de vérifier les paramètres du slicer, s’assurer que le modèle est bien préparé (par exemple, en le réparant via un outil spécifique) ou choisir le bon profil d’imprimante et de matériau. Si le problème persiste, il peut être utile de réinitialiser le slicer ou de tester un autre logiciel pour générer un nouveau G-code. Enfin, certaines imprimantes disposent de journaux d’erreurs ou de rapports qui peuvent aider à identifier précisément la source du problème.
L’incompatibilité avec certains modèles 3D
L’incompatibilité avec certains modèles 3D peut survenir pour plusieurs raisons. Parmi les problèmes courants, on trouve des erreurs géométriques dans le modèle, telles que des trous, des faces inversées ou des éléments non manchés, qui peuvent empêcher une bonne génération du G-code ou provoquer des défauts d’impression. Les modèles 3D peuvent aussi contenir des surfaces non fermées (par exemple, des objets qui ne forment pas un volume solide), ce qui empêche le slicer de les analyser correctement.
Pour résoudre ce problème, il est conseillé d’utiliser des logiciels de réparation de modèle 3D qui détectent et corrigent ces erreurs. Une autre source d’incompatibilité peut être liée à la complexité du modèle, avec des zones difficiles à imprimer (comme des porte-à-faux sans support adéquat), qui nécessitent des ajustements dans les paramètres de support du slicer. Enfin, la taille du modèle ou son orientation sur le plateau peut entraîner des erreurs si elle dépasse les limites de l’imprimante ou si la première couche n’adhère pas correctement. Vérifier et ajuster ces éléments dans le slicer permet souvent de résoudre ces problèmes d’incompatibilité.
Une optimisation insuffisante des supports
Une optimisation insuffisante des supports peut entraîner divers problèmes pendant l’impression 3D, comme une mauvaise adhésion aux surfaces de l’objet, des artefacts ou des résidus difficiles à retirer. Cela se produit souvent lorsque les paramètres de support ne sont pas correctement ajustés, par exemple, une densité trop élevée qui augmente la consommation de filament et le temps d’impression, ou une densité trop faible qui ne fournit pas un soutien suffisant, surtout pour les porte-à-faux importants.
Pour optimiser les supports, il est essentiel de définir correctement leur type (arborescent, lignes, grille) en fonction de la géométrie de l’objet, de régler l’angle de surplomb au-delà duquel les supports sont générés (généralement entre 45° et 60°), et d’ajuster la distance entre les supports et le modèle pour faciliter leur retrait sans endommager la surface. De plus, certains slicers offrent des options pour générer des supports uniquement dans les zones nécessaires, ce qui réduit le matériau utilisé et le post-traitement. Enfin, l’utilisation de matériaux solubles pour les supports, comme le PVA, peut grandement faciliter le retrait des structures de support complexes tout en améliorant la finition de l’objet imprimé.
Conclusion : slicer pour l’impression 3D
En conclusion, le slicer est un outil essentiel pour l’impression 3D, transformant un modèle 3D en instructions compréhensibles par l’imprimante, tout en permettant un contrôle précis des paramètres d’impression. Le choix du slicer, ainsi que la configuration adéquate des paramètres comme la vitesse, la température, le type de support et le taux de remplissage, jouent un rôle crucial dans la qualité finale de l’impression.
Une bonne maîtrise des fonctionnalités du slicer, y compris la prévisualisation du parcours d’impression, l’optimisation des supports et la gestion des défauts courants, permet de maximiser l’efficacité et de minimiser les erreurs. Que ce soit pour des impressions simples ou complexes, l’utilisation d’un slicer bien réglé, accompagné d’impressions test et d’une attention particulière aux détails, est indispensable pour obtenir des objets 3D précis, solides et esthétiques.
Photo par Freepik.
Les articles publiés sur Imprimy.com ont uniquement une vocation informative. Ils sont destinés à fournir des conseils généraux et des informations relatives à l’impression 3D. Imprimy.com ne saurait être tenu responsable des résultats obtenus ou des conséquences découlant de l’application des informations partagées. Nous recommandons de toujours vérifier les instructions spécifiques à votre matériel et à vos matériaux avant toute utilisation.