Do you want to know everything about 3D metal printing? At Imprimy.com, are here to explain it all to you and describe the future prospects of these innovations.
3D metal printing is an additive manufacturing technology that allows the creation of complex and customized parts by layering metal powder fused by a laser or an electron beam.
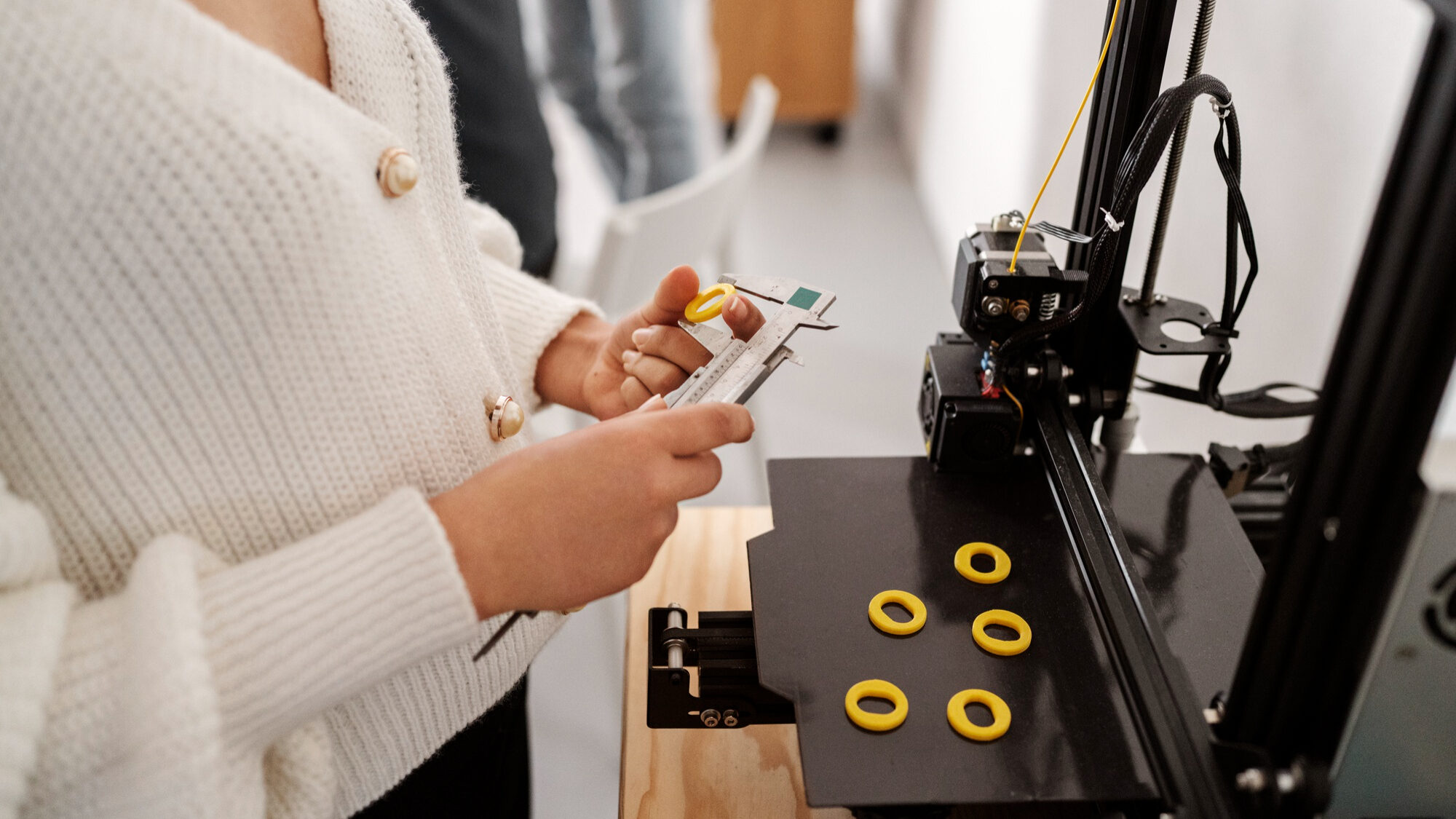
What is 3D metal printing?
3D metal printing is a specific form of 3D printing that uses metal materials instead of traditional plastic filaments or liquid resins.
- What is 3D metal printing?
- What are the advantages of 3D metal printing?
- What are the applications of metal 3D printing?
- What are the challenges and limitations of metal 3D printing?
- What are the future prospects of metal 3D printing?
- Conclusion: Metal 3D Printing
- Check our other contents about 3D printing materials
The principle of 3D metal printing
The principle of 3D metal printing is based on additive manufacturing, which involves layering metal powder fused by a laser or an electron beam.
This technique allows you to create complex parts directly from a digital file. Unlike traditional methods, it minimizes material waste. It also offers high precision and advanced customization of metal objects.
The metal materials used for 3D metal printing
The metal materials used in 3D metal printing mainly include titanium alloys, stainless steel, aluminum, and nickel alloys such as Inconel. These materials are chosen for their mechanical properties and corrosion resistance.
The metal powder must be perfectly fine and homogeneous to ensure optimal fusion. Each metal offers specific advantages depending on the application, such as lightweight or high-temperature resistance. Thus, the material choice directly influences the performance and durability of the printed part.
What are the advantages of 3D metal printing?
3D metal printing offers many advantages, including product customization, reduced production costs, and high-quality finished products.
Customization and complex design
3D metal printing allows total customization of parts, tailored to the specific needs of each user. It offers the possibility to create complex and organic shapes, often impossible to achieve with traditional methods.
Thanks to 3D modeling software, designers can optimize structures to reduce weight while maintaining strength. This design freedom promotes innovation in sectors such as aerospace and medical. Finally, it reduces costs and lead times related to prototypes and small production runs.
Reduction of costs and manufacturing lead times
3D metal printing significantly reduces costs by limiting material waste and avoiding complex machining operations. It speeds up manufacturing times through direct production from the digital model, without the need for molds or special tooling.
This technology also facilitates the creation of rapid prototypes and customized small batches. The simplification of production steps improves efficiency and flexibility. Thus, companies can innovate faster while controlling their budget.
Performance and quality of the finished product
3D metal printing guarantees high performance thanks to a dense and homogeneous internal structure of the parts. The quality of the finished product is optimized by precise control of the layer-by-layer fusion process. The parts exhibit excellent mechanical strength and good durability, often comparable to traditionally manufactured parts.
Moreover, finishes can be improved through post-printing treatments to meet specific requirements. This technology thus enables the production of metal objects that are both reliable and high-performing.
What are the applications of metal 3D printing?
Metal 3D printing is used in many industrial fields such as aerospace, automotive, medicine, and industry.
Metal 3D Printing in the Aerospace Industry
In the aerospace industry, 3D metal printing is revolutionizing the manufacturing of lightweight and durable parts. It allows the design of complex components, such as engine injectors or internal structures, optimized to reduce weight and improve performance.
Customization and fast production are crucial to meet the strict requirements of this sector. Additionally, this technology helps reduce maintenance costs by facilitating the manufacturing of spare parts. Finally, it promotes innovation by accelerating the development of new technical solutions.
Metal 3D printing in the automotive industry
In the automotive industry, 3D metal printing is used to produce lightweight, durable, and often custom-made parts. It enables the rapid manufacturing of functional prototypes and complex components, thereby reducing development cycles.
This technology also supports the production of customized small batches, ideal for exclusive or racing models. 3D metal printing helps optimize vehicle performance while limiting manufacturing costs. Finally, it paves the way for innovations in design and automotive engineering.
3D metal printing in medicine and surgery
In medicine and surgery, 3D metal printing allows the creation of customized implants perfectly adapted to the patient’s anatomy. It is used to manufacture prostheses, orthopedic plates, and custom surgical devices.
This technology improves the precision of interventions and promotes better biological integration. Additionally, it reduces production times, enabling faster treatment. Finally, 3D metal printing contributes to more effective and personalized care.
3D metal printing in the manufacturing and production industry
In the manufacturing and production industry, 3D metal printing facilitates the creation of complex and functional parts without the need for expensive tooling. It enables the production of rapid prototypes and small batches with great flexibility.
This technology optimizes industrial processes by reducing assembly times and waste-related costs. It also offers the possibility to improve component performance through innovative designs. Thus, 3D metal printing boosts production while enhancing the competitiveness of companies.
3D Printing in Other Industries
3D metal printing also finds its place in various sectors such as jewelry, where it enables the creation of fine and customized designs. In architecture, it facilitates the fabrication of detailed models and innovative structural elements.
The energy sector uses this technology to produce parts resistant to extreme conditions, like turbines. In education and research, it accelerates prototyping and experimentation. Finally, art and industrial design benefit from this method to create unique and technical works.
What are the challenges and limitations of metal 3D printing?
Metal 3D printing currently faces a number of obstacles, including the cost of equipment and materials, slower production speeds, and tedious post-processing steps.
The cost of the equipment and materials used
3D metal printing equipment is generally expensive, with industrial machines costing up to several hundred thousand euros. The materials, such as high-quality metal powders, also represent a significant part of the budget due to their high price and purity requirements. These costs often limit access to this technology to large companies or specialized sectors.
However, the gradual price reduction and technological advancements are making 3D metal printing increasingly accessible. Finally, the investment is often offset by savings in time, material, and the complexity of produced parts.
The production speed
The production speed in 3D metal printing depends on the process used and the complexity of the part. Generally, it is faster than traditional methods for complex or customized parts because it eliminates several intermediate steps.
However, the layer-by-layer construction can be slower for large, massive parts. Technological advancements continue to improve this speed. Thus, 3D metal printing offers a good balance between speed and precision for industrial manufacturing.
The limitations of the materials used
The materials used in 3D metal printing have certain limitations, notably a limited range of alloys suitable for fine powder and laser fusion. Some heat-sensitive metals may experience deformations or internal stresses during the process.
Porosity and microscopic defects can affect the mechanical strength of parts. Additionally, some materials remain expensive and difficult to recycle. Finally, the final properties can sometimes be inferior to those achieved by traditional metallurgical processes.
The post-processing required for metal 3D printing
Post-processing of parts in 3D metal printing is essential to improve their quality and performance. It often includes steps such as de-powdering to remove residual powder and polishing to achieve a smooth surface.
Heat treatments are performed to reduce internal stresses and optimize the metallic structure. Sometimes, additional machining is necessary to achieve precise tolerances. These operations ensure final parts that meet technical and aesthetic requirements.
What are the future prospects of metal 3D printing?
Metal 3D printing promises technological innovations and an impact that will revolutionize many fields of activity.
The upcoming technological innovations in metal 3D printing
Upcoming innovations in 3D metal printing promise increased speed and better part quality thanks to more powerful lasers and advanced control systems. The development of new specialized alloys will offer improved mechanical properties and a greater diversity of applications.
The integration of artificial intelligence will enable real-time optimization of manufacturing parameters to reduce defects. Moreover, hybrid processes combining 3D printing and machining will become more common. Finally, the rise of decentralized manufacturing could transform industrial supply chains.
The impact of metal 3D printing on production lines
3D metal printing transforms production chains by enabling more flexible and faster manufacturing. It reduces dependence on traditional tooling, thereby facilitating the production of small batches and customized parts.
This technology also decreases inventory and logistics delays thanks to on-demand production. It promotes innovation by shortening the product development cycle. Finally, it contributes to a more sustainable industry by limiting waste and transportation.
Conclusion: Metal 3D Printing
3D metal printing is revolutionizing industrial manufacturing thanks to its ability to produce complex, customized, and high-performance parts. This technology offers significant gains in speed, cost, and flexibility, opening new opportunities across many sectors.
Despite some limitations related to materials and post-processing, technological advancements promise continuous improvement. Its impact on production chains and innovation is major, making 3D metal printing essential for the future. It represents a true industrial revolution with multiple benefits.
Picture by Freepik.
The articles published on Imprimy.com are for informational purposes only. They are intended to provide general advice and information related to 3D printing. Imprimy.com cannot be held responsible for the results obtained or the consequences arising from the application of the shared information. We recommend always checking the specific instructions for your hardware and materials before use.
Check our other contents about 3D printing materials
Silicone 3D printing: a revolution in custom manufacturing
Are you curious about silicone 3D printing and want to learn more about it? At…
3D printing textile
Are you wondering about 3D textile printing and its capabilities? At Imprimy.com, we are here…
3D printing of wax
Do you want to know more about 3D printing of wax? At Imprimy.com, we are…