Are you wondering about PETG and its applications in 3D printing? We at Imprimy are here to provide all the answers you’re looking for.
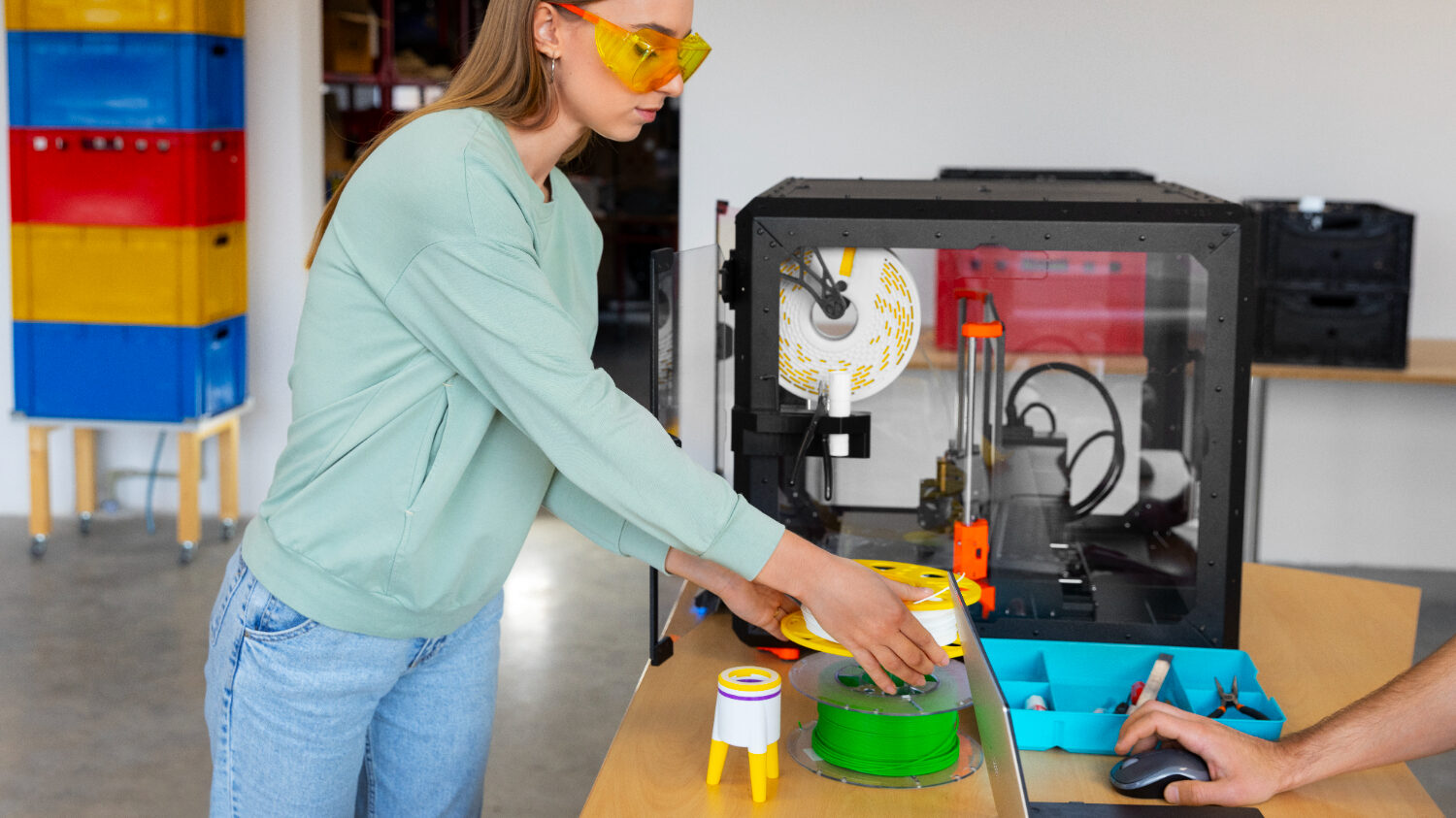
What is PETG?
PETG is a type of thermoplastic used in 3D printing and is particularly valued for its strength and some of its unique characteristics.
The Definition of PETG
PETG (Polyethylene Terephthalate Glycol) is a type of thermoplastic polymer that is widely used in 3D printing due to its combination of strength, durability, and ease of use. It is a modified version of PET (Polyethylene Terephthalate), which is commonly used for beverage bottles, but with the addition of glycol to improve its processing properties.
PETG is known for being impact-resistant, flexible, and chemical-resistant, making it ideal for both functional and aesthetic applications in 3D printing. It also has the benefit of low warping, making it easier to print compared to other materials like ABS. Additionally, PETG is often available in transparent forms, which is useful for applications where visibility or light diffusion is needed.
Overall, PETG is a versatile material that strikes a balance between the ease of PLA and the strength of ABS, making it a popular choice for a wide range of 3D printing projects.
History and Development of PETG
PETG (Polyethylene Terephthalate Glycol) is a variation of PET (Polyethylene Terephthalate), a widely used plastic that was first developed in the 1940s. The original PET was created as a polymer for synthetic fibers and later evolved to be used in packaging, particularly for beverage bottles. PET quickly became popular because of its strength, clarity, and recyclability.
The development of PETG began as a modification to the standard PET polymer by introducing glycol into the production process. This addition of glycol reduces the crystallinity of the material, making it more transparent, easier to process, and less prone to warping. PETG also has enhanced impact resistance compared to regular PET, which made it an attractive material for a variety of uses in different industries.
The primary goal of developing PETG was to create a plastic that maintained the strength and chemical resistance of PET but with better processing characteristics, including improved flexibility and ease of molding. This made it easier to manufacture more intricate shapes and products, particularly in industries like packaging, medical equipment, and consumer goods.
With the rise of 3D printing in the 21st century, PETG gained significant popularity in the additive manufacturing community. Its unique combination of strength, durability, and ease of use made it a go-to filament for functional parts, prototypes, and mechanical components. Today, PETG is commonly used not only in industrial applications but also in 3D printing, where it is appreciated for its low warping properties and versatility.
In summary, PETG’s development began with the goal of improving PET’s processing and mechanical properties. Over the years, it has found a strong place in both traditional manufacturing and modern 3D printing due to its desirable features.
Properties of PETG
PETG is known as a 3D printing material that is particularly durable, while also offering significant aesthetic qualities.
Mechanical Strength of PETG in 3D Printing
The mechanical strength of PETG in 3D printing is one of its main advantages, making it a popular choice for applications requiring solid and durable parts. Compared to materials like PLA, PETG offers better impact resistance, meaning it is less likely to break under pressure or shock. Additionally, it combines both rigidity and flexibility, allowing it to withstand moderate loads without easily deforming or cracking.
This mechanical strength is especially valued in applications such as the production of functional parts, robust prototypes, or in environments where parts are subjected to regular stresses and strains. PETG also features excellent layer adhesion, which enhances the strength of printed objects and reduces the risk of delamination or cracking over time.
Heat Resistance of PETG
The heat resistance of PETG is superior to that of PLA, making it a preferred choice for applications requiring some thermal stability. PETG has a glass transition temperature (Tg) of about 80 to 85°C, meaning it can withstand moderate temperatures without deforming, unlike PLA, which begins to soften at lower temperatures (around 60°C).
However, while PETG is more heat-resistant than PLA, it still performs less well than other materials like ABS or nylon, which can withstand higher temperatures. In practice, PETG is suitable for applications where printed parts are not exposed to extreme temperatures, such as in the production of functional prototypes, automotive parts, or objects used in mildly heated environments.
Transparency and Finish of PETG
The transparency and finish of PETG are highly valued in 3D printing. PETG can be printed with excellent clarity, making it an ideal choice for applications requiring clear visibility, such as display cases, product prototypes, or decorative objects. Its ability to produce a smooth and glossy finish gives it a high-quality aesthetic, which is often sought after for objects meant to be visible or showcased.
Furthermore, unlike other materials like ABS, PETG tends to offer a more uniform surface with fewer signs of excessive shrinkage. This combination of transparency and refined finish makes PETG a preferred choice for projects where appearance is key, while still maintaining remarkable strength and durability.
Chemical Resistance of PETG in 3D Printing
The chemical resistance of PETG in 3D printing is one of its major advantages, making it suitable for a wide range of industrial and practical applications. PETG offers good resistance to many chemicals, such as diluted acids, bases, solvents, as well as certain cleaning products and detergents. This allows it to maintain its integrity even when exposed to moderate chemical substances, making it a popular choice for manufacturing parts used in industrial or medical environments where contact with chemicals is frequent.
However, although PETG provides enhanced resistance compared to materials like PLA, it can be affected by more powerful solvents or extreme conditions. Therefore, it is important to consider the types of chemicals the printed parts will be exposed to in order to determine whether PETG is the most suitable material.
Ease of Use of PETG in 3D Printing
PETG is renowned for its ease of use in 3D printing, making it an accessible choice for both beginners and more experienced users. Compared to other materials like ABS, PETG has a lower risk of warping and does not require as high of a heated bed temperature, although a bed temperature around 70-80°C is recommended for better adhesion. It does not emit strong fumes or odors, improving the comfort of use compared to ABS. Additionally,
PETG adheres well to various bed surfaces, including masking tape or glass. The printing process is generally stable and predictable, with fewer risks of delamination between layers, resulting in solid and consistent parts. However, it is important to store the filament properly to prevent it from absorbing moisture, which could affect print quality. Overall, PETG combines interesting technical properties with ease of use, making it a popular material in 3D printing.
Advantages of Using PETG in 3D Printing
The main advantages of PETG are related to its strength, layer adhesion, and low emissions of fumes during printing.
The Strength of Objects Printed in PETG
The strength of PETG-printed objects is one of its most appreciated characteristics. PETG offers excellent mechanical resistance, combining both rigidity and flexibility, making it particularly well-suited for functional parts subjected to moderate physical stress. Thanks to its exceptional layer adhesion, PETG-printed objects are less likely to crack or delaminate over time, unlike other materials like PLA. Additionally, PETG has good impact resistance, meaning it can withstand shocks or pressures without breaking easily.
This durability is ideal for applications requiring long-lasting and resilient parts, such as functional prototypes, mechanical components, specialized tools, or automotive parts. In summary, the strength of PETG allows for the creation of objects that are robust, durable, and reliable, while still offering enough flexibility to resist slight deformations.
Excellent Layer Adhesion in PETG Printing
The excellent layer adhesion is one of the main advantages of PETG in 3D printing. This material ensures optimal fusion between successive layers, significantly reducing the risks of delamination or separation over time. This characteristic is especially important for the strength and durability of printed objects, as it ensures a consistent structure that can withstand mechanical stresses.
Thanks to this improved adhesion, PETG prints exhibit smoother and more uniform surfaces, contributing to a higher quality aesthetic finish. Additionally, this property makes PETG a preferred choice for functional applications and parts that require increased resistance to wear or impact. It makes PETG more reliable for long-term projects, compared to other materials that may present higher risks of deformation or cracking under stress.
Less Pollution and Low Odor Thanks to PETG
PETG is a 3D printing material that has the advantage of generating less pollution and emitting fewer odors compared to other plastics like ABS. During printing, PETG releases few volatile substances and does not emit toxic fumes or strong odors, making it a more pleasant and safer choice for indoor use, especially in poorly ventilated spaces.
Unlike ABS, which can release irritating styrene vapors during printing, PETG is considered an environmentally friendlier material, making it ideal for users concerned with air quality and safety. This low emission of harmful particles and gases contributes to a healthier working environment, particularly in home workshops or shared workspaces.
Disadvantages of PETG
Despite all its advantages, PETG does have several issues, particularly related to its sensitivity to moisture, adhesion problems to the build plate, and its higher purchase cost.
The Sensitivity of PETG to Moisture
One of the main challenges with PETG in 3D printing is its sensitivity to moisture. As a hygroscopic material, PETG readily absorbs water from the air. When the filament absorbs moisture, it can significantly affect the quality of your prints. Here’s how moisture can impact PETG:
- Print Quality Issues: When PETG absorbs moisture, it can cause bubbling or popping sounds during printing as the water turns into steam and escapes from the filament. This can result in a less smooth extrusion, leading to imperfections in the print surface, stringing, or poor layer bonding.
- Increased Stringing and Oozing: Moisture can exacerbate issues like stringing and oozing, which are already common challenges with PETG. When the filament is wet, it may not extrude properly, causing unwanted strings between parts of the print.
- Poor Adhesion Between Layers: Excess moisture can also affect the adhesion between the layers of the print, leading to weaker prints that might delaminate or fail under stress.
Adhesion of PETG to the Print Bed
The adhesion of PETG to the print bed is generally very good, but it can vary depending on the type of surface used and printing conditions. PETG has excellent bed adhesion, which reduces the risk of warping compared to materials like ABS. For optimal results, it is recommended to heat the bed to between 70 and 80°C, which helps PETG adhere better.
In terms of surface, a glass bed or one covered with masking tape works well with PETG. Additionally, using a light adhesive spray or a specific adhesive can further enhance adhesion, especially if the bed is cold or if detachment issues occur. However, it is important not to overheat the bed, as this could lead to excessive adhesion, making it more difficult to remove printed objects.
The brittleness of PETG under certain pressure angles
Although PETG is a relatively strong and flexible material, it can exhibit some brittleness under certain pressure angles. While it offers good impact resistance and excellent layer adhesion, PETG can be prone to breaking or cracking when subjected to significant forces or excessive pressure in a specific direction. This brittleness is particularly noticeable when printed parts are subjected to repeated loads or pressure angles that exceed the material’s flexibility limits.
Unlike softer plastics like TPU, PETG retains some rigidity, making it less suitable for applications requiring very high flexibility or significant deformations. However, for applications where mechanical strength is paramount and the parts are not subjected to extreme stresses, PETG remains an excellent choice.
The higher cost of PETG filament
The cost of PETG filaments is generally higher than that of other materials like PLA, mainly due to its superior technical properties and manufacturing process. PETG offers better resistance to heat, impact, and chemicals, making it a more durable and functional material for specific applications. This superior quality is reflected in its price, which can be a limiting factor for some users, especially in projects requiring large quantities of filament.
However, despite its higher cost, PETG can be seen as a worthwhile investment for prints requiring greater strength or particular characteristics, as it produces more durable and resistant objects compared to cheaper materials like PLA. In summary, while its cost is higher, PETG can offer a better cost-performance ratio depending on the project’s requirements.
What are the printing parameters to apply for PETG?
To ensure your PETG prints correctly, you must apply specific settings regarding the temperature and print speed, the heated bed temperature, and the humidity level of your filaments.
The extrusion temperature for PETG
The extrusion temperature for PETG should generally be set between 230°C and 250°C. This range ensures proper melting and flow of the filament, allowing it to adhere well to the print bed and produce smooth layers. It’s important to experiment within this range depending on the brand and type of PETG you’re using, as slight adjustments might be necessary for optimal results.
The bed temperature
For PETG, the recommended print bed temperature is typically between 70°C and 80°C. This helps ensure good adhesion to the print bed, preventing warping and ensuring that the printed layers bond properly. You may need to fine-tune this temperature depending on your specific setup and the type of surface you’re using (like glass or tape). Some users may find success even with lower bed temperatures, but generally, staying in this range helps maintain optimal adhesion.
The print speed to apply for PETG
The recommended print speed for PETG typically ranges between 40 and 60 mm/s, though it can be adjusted based on your printer and filament specifications. A slower speed can be beneficial for achieving better print quality, especially for the first layers, as it allows for better adhesion to the bed and reduces the risk of delamination or defects.
On the other hand, printing too quickly can lead to issues such as poor layer fusion, irregular extrusion, or poor-quality prints. It’s advised to start with a moderate speed and adjust it according to the print quality observed, taking into account parameters such as extrusion temperature and bed temperature.
Retraction settings
Retraction settings for PETG are crucial to avoid unwanted strings, such as stringing, and achieve a clean print. Generally, PETG retraction settings are slightly different from those for PLA due to its material properties.
The recommended retraction distance usually ranges from 4 to 6 mm, while the retraction speed should be set around 30 to 50 mm/s. Excessive or too fast retraction can lead to clogs in the nozzle or extrusion problems, while insufficient retraction can cause stringing. Therefore, it’s important to test and adjust these settings to find a balance between preventing stringing and ensuring smooth extrusion.
Storage and humidity management of PETG
PETG is sensitive to humidity, which can affect its print quality. When it absorbs moisture, the filament can become more difficult to extrude, leading to issues such as prints with bubbles, a rough surface, or layer adhesion defects. To avoid these problems, it is important to store PETG properly in a dry environment. It is recommended to keep it in airtight bags with desiccant packets to absorb moisture, or use storage boxes specifically designed to maintain a dry atmosphere.
If the filament has already absorbed moisture, it may be necessary to dry it before printing, by placing it in an oven at a low temperature or a filament dryer for several hours, according to the manufacturer’s recommendations. By reducing the moisture level, you can preserve the quality of your prints and extend the lifespan of your PETG filament.
What are the applications of PETG in 3D printing?
PETG is used to create functional prototypes, durable tools, or even aesthetically pleasing artistic objects.
The creation of functional prototypes
PETG is an excellent choice for creating functional prototypes in 3D printing due to its mechanical properties, impact resistance, and good layer adhesion. Its strength, combined with some flexibility, allows for the production of prototypes that are not only functional but also durable, capable of withstanding moderate physical stress.
Additionally, PETG’s ease of printing and the quality of its finish allow for the creation of high-precision prototypes with fine details. Thanks to its resistance to moisture and chemicals, PETG is also a good choice for prototypes that need to be exposed to specific environments, such as in the automotive, medical, or food industries. In summary, PETG enables the production of high-quality, reliable, and robust functional prototypes while offering great design freedom.
The manufacturing of mechanical parts and tools
PETG is particularly well-suited for the manufacturing of mechanical parts and tools due to its combination of mechanical strength, flexibility, and durability. This material offers good resistance to shocks and impact, making it ideal for parts subjected to moderate stress or frequent handling. Its ability to withstand pressure without cracking makes it a solid choice for functional tools such as supports, adapters, handles, or even more complex parts used in mechanical assemblies. Additionally, the layer adhesion of PETG is excellent, ensuring the long-term strength of the parts while minimizing the risk of delamination.
Thanks to its chemical resistance, it can also be used in environments where tools are exposed to chemicals or moisture. In summary, PETG is a versatile and reliable material for manufacturing robust mechanical parts and high-quality tools, offering both performance and reliability for functional applications.
Applications of PETG in the automotive and aerospace industries
PETG is increasingly finding applications in the automotive and aerospace industries due to its mechanical strength, durability, and moderate heat resistance.
In the automotive industry, it is used to create functional prototypes, internal components such as cable supports, and enclosures for electronic equipment.
In aerospace, although PETG is not yet widely used for flight parts, it is used for prototypes, models, tools, or jigs, thanks to its low weight and good impact resistance, making it an ideal material for applications where every gram counts, especially in the design and manufacturing phases of parts.
Transparent and decorative objects made of PETG
PETG is particularly popular for creating transparent and decorative objects due to its ability to offer exceptional optical clarity and a smooth finish. This material allows the production of shiny, translucent pieces, ideal for applications such as lamps, interior décor elements, display cases, or customized objects. Due to its transparency and ease of printing,
PETG is also used to create visual prototypes or models with a refined aesthetic appearance. Furthermore, its mechanical strength and durability make it an excellent alternative for decorative objects that need to combine functionality with visual appeal while being able to withstand daily wear. Thanks to its thermal stability, PETG also allows the creation of decorative objects that can be exposed to moderate temperatures without warping, while maintaining their transparent and crisp appearance.
How does it compare to other 3D printing materials?
PETG can be compared to PLA, ABS, or even TPU to determine whether its use is appropriate compared to other materials.
PLA vs PETG
PLA and PETG are two popular materials in 3D printing, each with specific advantages. PLA, easy to use, cost-effective, and with low fumes emission, is ideal for beginners and simple projects. However, its limited resistance to heat, moisture, and fragility make it a less suitable choice for functional applications.
In contrast, PETG offers better mechanical, chemical, and thermal resistance, making it the preferred choice for durable and functional parts, such as industrial prototypes or objects subjected to stress. However, PETG is more difficult to print than PLA, as it is sensitive to moisture and requires precise settings. In summary, PLA is suitable for simple and decorative prints, while PETG is better for applications requiring strength and durability.
ABS vs PETG
ABS and PETG are two materials whose characteristics differ based on application needs. ABS is known for its toughness, heat and chemical resistance, making it an ideal choice for mechanical parts or objects used in demanding environments. However, it is difficult to print, requiring a heated bed and an enclosed chamber to prevent warping, and it emits potentially toxic fumes.
PETG, on the other hand, is easier to print, with good layer adhesion and less tendency to warp, making it more accessible for users. While it doesn’t match ABS in terms of thermal resistance, it offers excellent impact resistance, some flexibility, and is less toxic, emitting almost no fumes during printing. In summary, ABS is preferable for heat and chemical-resistant parts, while PETG is better suited for applications where ease of printing, durability, and impact resistance are essential.
PETG vs TPU
PETG and TPU are two distinct 3D printing materials with different characteristics that make them suitable for different applications. PETG is a durable, rigid material with good impact resistance, thermal stability, and moderate flexibility. It’s ideal for applications that require strength and durability, such as prototypes, mechanical parts, or functional tools.
On the other hand, TPU (Thermoplastic Polyurethane) is a flexible, rubber-like material, offering excellent elasticity and abrasion resistance. It’s ideal for producing flexible parts, such as gaskets, seals, phone cases, or wear-resistant components. While PETG is easier to print compared to TPU, TPU is more challenging due to its flexibility, which can cause issues with extrusion and filament feeding. In summary, PETG is best suited for parts that require rigidity and impact resistance, while TPU is ideal for applications needing flexibility and wear resistance.
Conclusion: PETG in 3D Printing
PETG is a versatile and reliable material for 3D printing, offering a great balance between durability, flexibility, and ease of use. Its excellent mechanical, thermal, and chemical properties make it suitable for a wide range of applications, including functional prototypes, mechanical parts, and decorative objects.
While it requires more precise printing settings compared to PLA, its resistance to warping, strong layer adhesion, and low toxicity make it an appealing option for users looking for a material that offers both strength and ease of printing. PETG is a great choice for applications where durability, impact resistance, and ease of handling are essential, making it an excellent alternative to other common 3D printing materials like PLA, ABS, and TPU.
Picture by Freepik.
The articles published on Imprimy.com are for informational purposes only. They are intended to provide general advice and information related to 3D printing. Imprimy.com cannot be held responsible for the results obtained or the consequences arising from the application of the shared information. We recommend always checking the specific instructions for your hardware and materials before use.