Want to learn more about 3D printing in watchmaking? At Imprimy, we’re here to answer all your questions on this topic.
3D printing in watchmaking enables the creation of customized and complex components with enhanced precision, revolutionizing the manufacturing of watches.
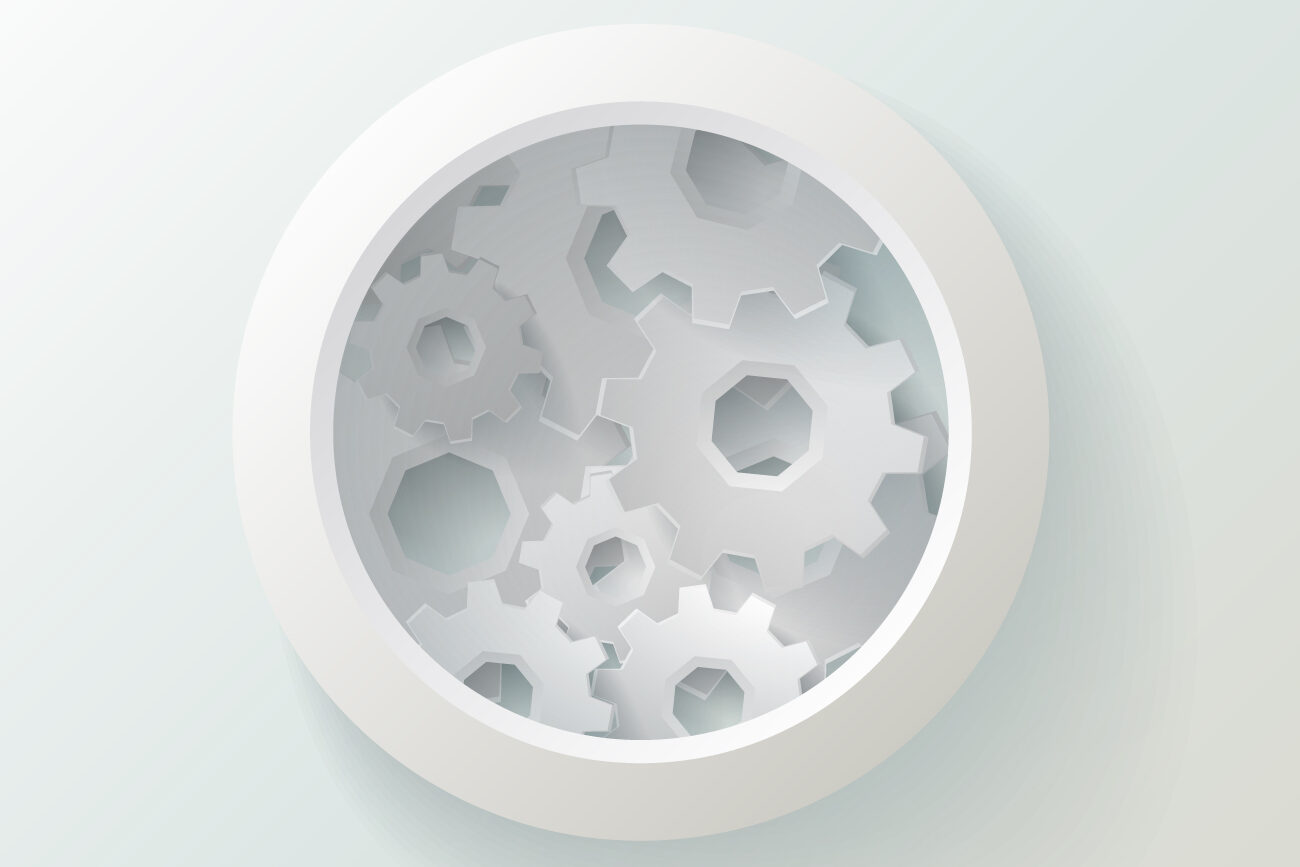
What are the applications of 3D printing in watchmaking ?
The applications of 3D printing in watchmaking include rapid prototyping, manufacturing of custom components, repairing of obsolete parts, and innovation in watch.
Rapid prototyping of watches in 3D
Rapid prototyping of watches in 3D enables the creation of functional models in record time, thus optimizing the design and development process. This technique uses advanced technologies such as 3D printing to produce watch components with extreme precision, facilitating testing and adjustments before mass production.
It offers increased flexibility in design, allowing creators to experiment with different shapes and mechanisms without the traditional manufacturing constraints. Additionally, rapid prototyping reduces the costs associated with multiple iterations and accelerates the market launch of new models while ensuring optimal quality.
The customization of your 3D printed watches
The customization of 3D printed watches offers a unique opportunity to create unique pieces that reflect individual tastes and preferences.
Through 3D printing, designers can incorporate custom design elements, such as personalized engravings, innovative shapes, and varied materials, to meet specific customer demands. This approach also allows for experimentation with different colors and textures, offering unmatched flexibility in the manufacturing process.
Moreover, customization strengthens the emotional attachment of users to their watches, transforming these functional objects into personal works of art.
The manufacturing of complex components for watchmaking
The manufacturing of complex components for watchmaking relies on cutting-edge techniques that ensure exceptional precision and reliability. The use of advanced technologies such as CNC machining and 3D printing enables the creation of parts with extremely fine tolerances, essential for the proper functioning of watch mechanisms.
These methods also allow for the integration of innovative materials and sophisticated designs, thereby meeting the high demands of the watchmaking industry. Additive manufacturing, in particular, offers great design freedom, enabling the production of components with complex shapes that would be difficult, if not impossible, to achieve with traditional methods. This approach fosters innovation and enhances the performance of watches while optimizing production processes.
What are the benefits of 3D printing for watchmakers?
The benefits of 3D printing for watchmakers include cost reduction, faster production, customization of parts, and flexibility in design and repair.
Cost reduction for clock manufacturing
Cost reduction in clock manufacturing can be achieved through production process optimization and the integration of modern technologies. The use of 3D printing and automated machining helps minimize material waste and reduce labor costs.
Additionally, computer-aided design (CAD) and digital simulations allow for virtual prototype testing, avoiding expensive physical iterations. The adoption of alternative materials and supply chain optimization further contribute to lower expenses.
Finally, automation in quality control and assembly processes enhances overall efficiency, enabling manufacturers to produce high-quality clocks at competitive costs.
Time savings through 3D clock manufacturing
Time savings through 3D clock manufacturing are significant, transforming traditional production processes. 3D printing enables rapid prototyping and final part creation, reducing development timelines. This technology eliminates intermediate manufacturing steps and supports quick design iterations, allowing for real-time adjustments.
Moreover, the ability to produce complex components in a single operation reduces manual assembly needs, accelerating product launch. By integrating these advanced methods, manufacturers can respond faster to customer demands and adapt to market trends, all while maintaining high quality.
Innovations and creativity enabled by 3D clock printing
Innovations and creativity enabled by 3D clock printing open new possibilities in the watchmaking industry. This technology allows designers to explore bold designs and unique shapes, free from the constraints of traditional manufacturing methods. 3D printing makes it easier to integrate advanced features, such as complex mechanisms and innovative materials, enhancing both performance and durability.
Additionally, it supports extreme customization, meeting specific client demands and creating one-of-a-kind pieces. This creative freedom fuels innovation, encouraging manufacturers to push the boundaries of design and functionality, while optimizing production processes.
What are the challenges and limitations of 3D printing in watchmaking?
The challenges and limitations of 3D printing in watchmaking include limited precision for very fine parts, restricted material options, high initial costs, and constraints in mass production.
Quality and precision of 3D printed clocks
The quality and precision of 3D printed clocks reach exceptional levels thanks to technological advancements. 3D printing enables the production of components with extremely fine tolerances, ensuring a perfect assembly and optimal mechanism performance. The materials used, often high-performance, contribute to the durability and reliability of the produced parts.
Additionally, the ability to faithfully reproduce complex designs ensures high consistency between prototypes and final products. This increased precision allows manufacturers to meet the high demands of the watchmaking market, offering products that combine both aesthetics and technical performance.
Materials used for 3D printing clocks
The materials used for 3D printing clocks are diverse and selected for their specific properties, ensuring both durability and performance.
Commonly used materials include engineering plastics like PA (polyamide) and PEEK (polyetheretherketone), which offer high mechanical and thermal resistance. Photopolymer resins are also employed for their ability to reproduce fine details, which are essential for complex components.
For applications requiring increased strength, metals like titanium and steel alloys can be printed using advanced technologies such as laser fusion. These materials allow the creation of robust and precise clocks, meeting the high standards of the watchmaking industry..
Regulation and intellectual property associated with 3D printing clocks
Regulation and intellectual property associated with 3D printing clocks are crucial aspects for manufacturers and designers to consider. Intellectual property protects original creations, including clock designs, through patents, copyrights, and trademarks.
Manufacturers must ensure that their creations do not infringe on existing rights and can protect their own innovations to avoid unauthorized copying. Regarding regulation, 3D printing must comply with safety and quality standards, particularly those related to materials used and manufacturing processes.
Clocks must meet technical and environmental requirements, ensuring compliance with both local and international laws. Failure to adhere to these regulations can result in legal and financial penalties, highlighting the importance of diligence in this field.
What are the future prospects for 3D printing in watchmaking?
The future prospects for 3D printing in watchmaking include innovation in advanced materials, the integration of multi-material technologies, improvements in precision and production speed, and the expansion of use in luxury watches.
Emerging trends in 3D printing of clocks
Emerging trends in 3D clock printing reveal a fusion of technological innovation and artistic creativity. 3D printing enables the creation of highly varied clock designs, ranging from classic mechanical models to avant-garde steampunk designs, and even minimalist and aesthetic clocks. Designers can customize each piece to fit various styles and interiors, using materials like PLA or PETG to ensure durability and lightweight characteristics.
Giant wall clocks and compact desk clocks are also gaining popularity, offering practical and aesthetic solutions for various spaces. Additionally, 3D printing makes it easier to create eco-friendly clocks powered by solar energy, as well as projection clocks, adding a futuristic touch to interiors. These innovations demonstrate how 3D printing continues to push the boundaries of creativity in the watchmaking field, enabling the creation of unique, customized designs that combine art and technology.
Environmental impact of 3D printing clocks
The environmental impact of 3D printing clocks is influenced by several factors related to the technology and materials used.
- Waste reduction: 3D printing allows for the production of only the necessary amount of material, minimizing waste compared to traditional manufacturing methods. This contributes to more efficient resource use and a reduction in plastic waste.
- Eco-friendly materials: The use of biodegradable or recycled filaments, such as PLA made from corn starch, reduces the environmental impact. However, some materials like ABS, derived from petroleum, have slower degradation rates and pose environmental challenges.
- Emissions and chemicals: Certain 3D printing processes, like stereolithography, require potentially toxic photopolymer resins. Additionally, printing can emit fine particles or harmful gases, depending on the materials used.
- Circular economy: 3D printing supports a more circular approach by enabling the recycling of materials and the reuse of production waste. This helps reduce the overall carbon footprint of the manufacturing process.
- Carbon emission reduction: By eliminating complex supply chains and reducing transportation needs, 3D printing can lower carbon emissions associated with logistics and material transport.
In summary, while 3D printing offers significant environmental benefits, particularly in terms of waste reduction and the use of eco-friendly materials, challenges remain regarding emissions and the use of chemicals. Adopting sustainable practices and continuing innovation in materials and 3D printing technologies are essential to minimize its environmental impact.
The evolution of the 3D printed clock market
The evolution of the 3D printed clock market is characterized by significant growth and diversification of applications. The 3D printing market is expanding rapidly, with a 22.66% growth over five years. The integration of 3D printing in various industries, including watchmaking, enables the creation of innovative and customized designs, addressing the growing demand for unique and bespoke products.
3D printing offers considerable advantages, such as waste reduction and greater flexibility in design and production. Creators can experiment with different materials and forms, ranging from classic mechanical clocks to avant-garde steampunk designs.
Moreover, 3D printing allows for the integration of advanced technologies to add interactive features, such as LED indicators or rotating movements controlled by code. Challenges remain, particularly in terms of the high costs of the necessary equipment and the need to overcome technical obstacles.
However, ongoing innovation and the growing adoption of 3D printing in the watchmaking industry promise a future where creativity and technology combine to push the boundaries of clock design and functionality.
Conclusion: 3D Printing in Watchmaking
In conclusion, 3D printing has revolutionized the watchmaking industry, offering numerous benefits such as enhanced creativity, customization, and cost reduction. The technology allows for the creation of innovative designs and the use of advanced materials, transforming the way clocks are produced and personalized. It has paved the way for eco-friendly practices, faster production, and the ability to incorporate interactive features in watches.
Despite its challenges, including material limitations, high initial costs, and technical hurdles, the continuous advancement in 3D printing technologies holds great promise. The growing adoption of this technology in the industry is set to reshape the future of watchmaking, where designs and functionality are continually pushed to new heights, allowing for the creation of truly unique and customized timepieces.
With further innovation and sustainable practices, 3D printing will undoubtedly play an even more integral role in the future of horology.
Picture Roverto by Freepik.
The articles published on Imprimy.com are for informational purposes only. They are intended to provide general advice and information related to 3D printing. Imprimy.com cannot be held responsible for the results obtained or the consequences arising from the application of the shared information. We recommend always checking the specific instructions for your hardware and materials before use.