Are you wondering whether it is possible to 3D print boats fully or partially? At Imprimy.com, we are here to answer all your questions about boat 3D printing.
3D printing of boats allows for the creation of prototypes or custom parts with enhanced precision and efficiency.
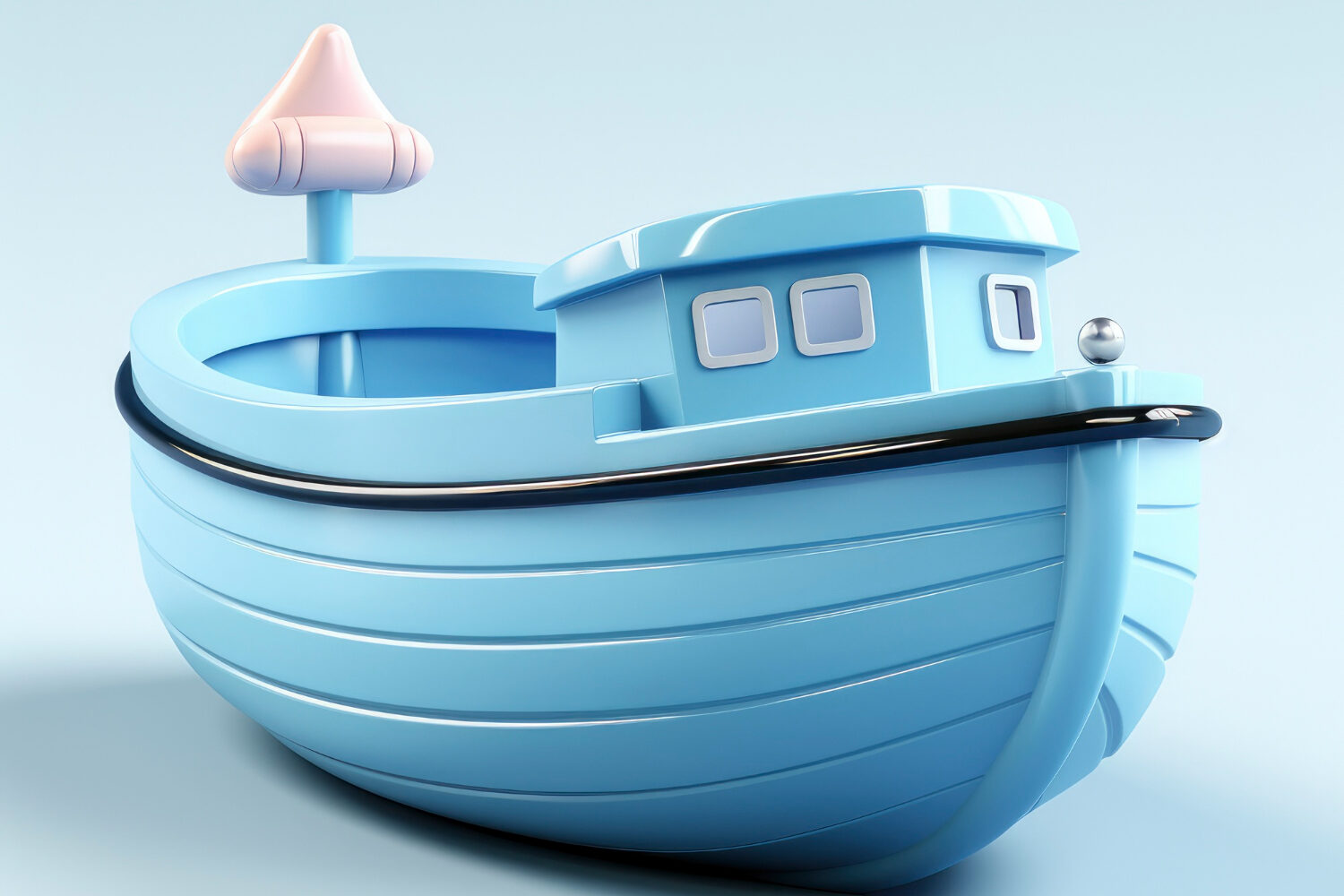
What are the advantages of 3D printing applied to boats?
3D printing applied to boats offers advantages such as cost reduction, customized parts, fast production, and optimized shapes to enhance performance.
The cost reduction in boat production through 3D printing
3D printing offers an innovative solution for cost reduction in boat production by enabling the manufacturing of complex parts in a single step, eliminating the need for expensive molds and multiple manufacturing processes. This technology also minimizes material waste by using only the exact amount needed for each component.
Additionally, 3D printing lowers storage costs by enabling on-demand production, eliminating the need for large spare part inventories. Finally, the ability to quickly and locally produce custom parts reduces transportation costs and lead times, contributing to a more efficient and cost-effective supply chain in the naval industry.
Boat customization through 3D printing
3D printing is revolutionizing boat customization by enabling the creation of unique, bespoke components tailored to the specific needs of each vessel. This technology offers unmatched flexibility in design, allowing manufacturers to produce complex, personalized parts without the limitations of traditional manufacturing methods.
Boat owners can thus benefit from custom solutions that enhance the performance, comfort, and efficiency of their vessels. Moreover, 3D printing makes it easier to produce custom spare parts, reducing downtime and ensuring that each boat remains operational with components perfectly suited to its unique characteristics.
The speed of producing 3D-printed elements for boats
3D printing significantly accelerates the production speed of boat components by enabling the direct manufacturing of complex parts from digital models. Unlike traditional methods that require specific tooling and lengthy manufacturing processes, 3D printing can produce components in just a few hours.
This reduction in lead times is especially beneficial for prototype production, allowing designers to quickly test and iterate their designs. Moreover, the ability to produce spare parts on demand reduces downtime for vessels, ensuring increased availability and more efficient maintenance. This speed contributes to a more agile and responsive supply chain, which is crucial in an industry where every day matters.
The durability of 3D-printed devices for boats
3D printing contributes to the durability of boat devices by optimizing material use and reducing production waste. Unlike traditional manufacturing methods that often generate significant scraps, 3D printing uses only the necessary amount of material to create each part, minimizing waste.
Furthermore, 3D-printed parts can be designed to be lighter and more resistant, enhancing the energy efficiency of vessels and reducing their carbon footprint. 3D printing also allows for the quick repair and replacement of damaged parts, extending the lifespan of equipment and reducing the need for frequent replacements.
Finally, the use of recyclable and biodegradable materials in the 3D printing process strengthens the maritime industry’s commitment to more environmentally friendly practices.
What are the concrete applications of 3D printing for boats?
The concrete applications of 3D printing for boats include the manufacturing of spare parts, the creation of models for testing, the optimization of structures for better hydrodynamics, and the production of lightweight and durable components.
3D printing prototyping for boat parts
3D printing is transforming the prototyping of parts for boats by offering a fast and cost-effective method to create physical models from digital designs. This technology allows engineers and designers to produce functional prototypes within a few hours, making testing and design adjustments easier.
Thanks to 3D printing, designers can explore different shapes and structures without the constraints of traditional tooling, speeding up the innovation process. Furthermore, 3D printed prototypes can be used to validate the performance of parts before mass production, thus reducing the risks and costs associated with later modifications.
This agile approach enables shipbuilders to respond more quickly to market demands and continuously improve the quality and functionality of their products.
3D printed spare parts for boats
3D printing is revolutionizing the production of spare parts for boats by offering a fast, cost-effective, and customizable solution. Thanks to this technology, it is possible to manufacture custom parts directly on board or nearby, reducing wait times and costs associated with storage and transportation.
For example, parts such as bitts can be 3D printed and installed on ships, demonstrating resistance and durability comparable to, or even exceeding, traditional parts. This approach also allows for the production of obsolete or hard-to-find parts, thereby extending the lifespan of marine equipment.
3D printing is thus becoming a valuable tool for the maintenance and repair of boats, ensuring continuous ship availability and reducing downtime.
3D printed complete structures for boats
3D printing is revolutionizing shipbuilding by enabling the creation of complete boat structures. For example, the University of Maine printed the 3Dirigo, a 7.62-meter-long boat, in just 72 hours, setting a world record for the largest solid object 3D printed. This boat was made from a blend of wood cellulose and plastic, demonstrating the viability of 3D printing for functional maritime structures.
Moreover, companies are using 3D printing to create complex and optimized parts, integrating features directly into the structure, such as cordage passages and drainage details. These advancements show that 3D printing can not only produce individual components but also entire boats, offering new possibilities for innovation and efficiency in the shipbuilding industry.
What are the challenges and limitations of 3D printing for a boat?
The challenges and limitations of 3D printing for a boat include material strength, durability in marine environments, printer size, high costs, and design constraints related to current printing technologies.
Materials used to 3D print boat parts
3D printing of boat parts uses a variety of materials suited to the specific demands of the maritime sector. Commonly used materials include:
- Recycled polypropylene (PP) with 30% glass fibers: This material is appreciated for its mechanical properties and durability, ensuring the longevity of printed parts. It is often used for structures requiring high strength.
- ER70S-6 steel: Used to print maritime parts like bitts, this material offers high strength and can be certified for maritime use, ensuring the quality and reliability of the produced parts.
- PLA, PETG, and ABS: These materials are used for various applications, ranging from models to functional parts. PLA is often preferred for models due to its ease of printing, while PETG and ABS are used for parts requiring better chemical and mechanical resistance.
- ASA: Commonly used in the automotive industry, ASA is also suitable for printing boat parts due to its UV resistance and sturdiness, making it ideal for demanding marine environments.
These materials allow for the creation of robust and durable parts, designed to withstand the harsh conditions encountered at sea.
Regulation around 3D printed parts for boats
The regulation around 3D printed parts for boats is an evolving field, as 3D printing technology continues to develop and integrate into various industrial sectors, including the maritime industry. Here are some key points regarding this regulation:
- Certification and standards: 3D printed parts intended for use on boats often need to be certified to ensure they meet safety and performance standards. For example, parts like bitts printed in 3D have been certified for maritime use, demonstrating they can perform as well as traditional parts.
- Approved materials: The materials used for 3D printing must meet specific criteria for strength and durability. Parts printed in steel or fiber-reinforced polymers are often subjected to rigorous testing to verify their ability to withstand maritime conditions.
- Quality control: 3D printed parts are often subjected to mechanical testing and microstructure analysis to ensure they meet the necessary quality and safety requirements. These checks are essential to obtain the certifications needed for the parts to be used on vessels.
- Local regulations: Regulations can vary depending on the jurisdiction. For instance, some regions may have specific requirements regarding the use of 3D printed parts in safety-critical applications.
- Innovation and development: The maritime sector is actively exploring the possibilities offered by 3D printing, which may lead to regular updates in regulations to keep pace with technological advancements and ensure the safety of innovations.
These aspects show that while 3D printing offers many opportunities for the maritime industry, it must be carefully regulated to ensure the safety and reliability of the parts produced.
Investment in industrial-grade 3D printers for printing boat parts
Investment in industrial-grade 3D printers for boat part manufacturing is a growing field, supported by technological advancements and research initiatives. Here are some key points regarding this investment:
- Investment: Acquiring industrial 3D printers represents a significant investment.
- Technological advantages: Industrial 3D printers allow for the creation of complex, customized parts with high precision, reducing production costs and lead times compared to traditional methods. They also offer the ability to produce parts on demand, which is particularly beneficial for spare parts or prototypes.
- Materials and durability: The use of composite and durable materials, such as fiber-reinforced polymers, allows for the production of robust parts suited to demanding marine conditions. These materials contribute to the longevity and performance of the printed structures.
- Innovation and flexibility: Industrial 3D printers provide great design flexibility, enabling the creation of complex geometric shapes that would be difficult or impossible to achieve with traditional manufacturing methods. This opens up new possibilities for innovation in boat design and construction.
- Reduction in production lead time: Thanks to additive manufacturing, production timelines can be significantly reduced.
These aspects show that investing in industrial-grade 3D printers can offer significant advantages for boat part production, in terms of costs, flexibility, and performance.
What could be the future of 3D printing for boats?
The future of 3D printing for boats could include more innovative materials with higher strength, a reduction in production costs, custom manufacturing, as well as eco-friendly concepts promoting recycling and hydrodynamic optimization.
Upcoming innovations in 3D printing for boat parts
Creative applications. Here are some notable trends and innovations:
- Advanced materials: The use of composite materials, such as recycled polypropylene reinforced with glass fibers, allows for the creation of more durable and resistant parts, suitable for harsh marine environments. These materials contribute to the longevity of the printed structures.
- Printing large structures: Some projects showcase the ability of 3D printing to produce large structures in a single piece, reducing the need for assembly and post-processing. This will save more time and lower production costs.
- Customization and flexibility: 3D printing technology offers great design freedom, allowing for custom parts and boat personalization based on specific client needs. This flexibility is particularly appreciated in the construction of high-value boats.
- Sustainability and ecology: The use of recycled materials and the optimization of resource use through 3D printing contribute to more sustainable manufacturing practices, reducing the ecological footprint of the shipbuilding industry.
These innovations show that 3D printing is transforming the way boats are designed and built, offering more efficient, durable, and customized solutions.
The potential impact of 3D printing on the shipbuilding industry
The impact of 3D printing on the shipbuilding industry is significant and promises to transform several aspects of ship construction and maintenance. Here are some key points:
- Cost and production time reduction: 3D printing allows for parts to be manufactured directly from digital models, eliminating the need for costly molds and traditional manufacturing processes. This reduces production costs and accelerates time to market, a crucial competitive advantage in the shipbuilding industry.
- Rapid prototyping: 3D printing enables the quick creation of functional prototypes, facilitating testing and adjustments before final production. This is particularly useful for innovations in ship design.
- Automation and robotics: The integration of robots into the 3D printing process allows for the production of complex geometric shapes with great precision, opening up new design possibilities for boat builders.
- Supply chain optimization: 3D printing can help optimize the supply chain in the maritime industry for spare parts, reducing the costs associated with acquiring new parts or components.
These advancements show that 3D printing has the potential to revolutionize the shipbuilding industry by offering more efficient, sustainable, and customized solutions.
Conclusion: 3D Printing for Boats
3D printing is poised to significantly impact the shipbuilding industry, offering innovative solutions that improve both the design and manufacturing processes. From cost reduction and faster production times to customization and enhanced sustainability, the technology offers numerous advantages. As materials continue to improve and 3D printing techniques evolve, boats can be built with greater precision, strength, and efficiency.
Furthermore, rapid prototyping and the ability to print parts on-demand are revolutionizing the way boats are designed, built, and maintained. This approach not only helps streamline production but also offers new possibilities for innovative designs and eco-friendly practices.
In the future, 3D printing is expected to play a pivotal role in reducing the environmental impact of shipbuilding, while enhancing the flexibility and performance of maritime vessels. Overall, the continued development of 3D printing technology will likely redefine the shipbuilding industry, enabling more efficient, customized, and sustainable solutions for the marine sector.
Picture by Freepik.
The articles published on Imprimy.com are for informational purposes only. They are intended to provide general advice and information related to 3D printing. Imprimy.com cannot be held responsible for the results obtained or the consequences arising from the application of the shared information. We recommend always checking the specific instructions for your hardware and materials before use.