Do you want to know everything about nylon 3D printing and its specific features? At Imprimy, we are here to answer all your questions so you can achieve the most successful nylon 3D prints possible.
Nylon 3D printing allows you to print strong, flexible, and durable parts, ideal for industrial applications and prototyping.
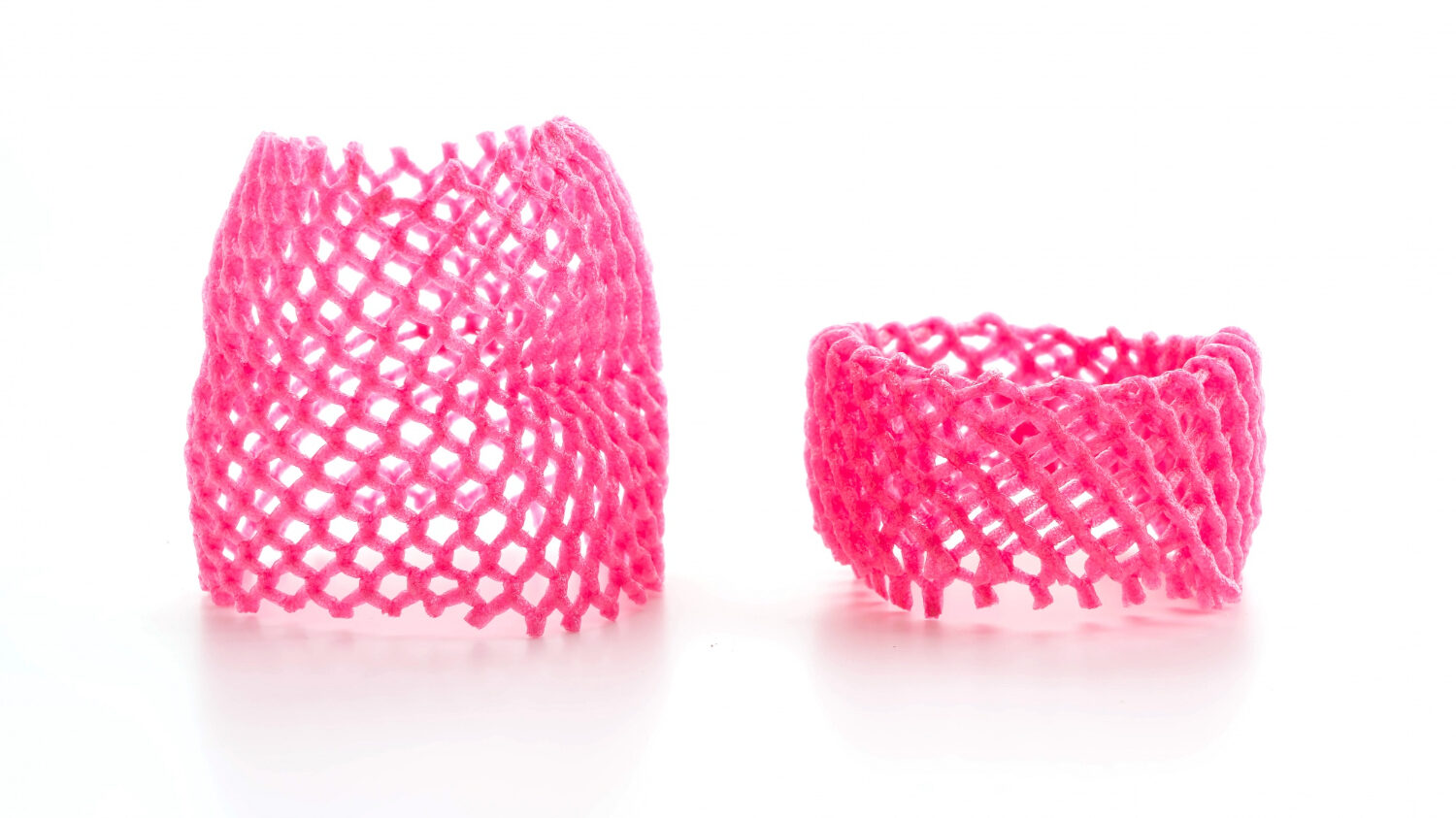
What is nylon in 3D printing?
Nylon in 3D printing is a highly resistant, flexible, and durable thermoplastic, often used for functional parts and prototypes that require strong wear and pressure resistance.
Definition of nylon
Nylon, also known as polyamide, is a synthetic polymer widely used in 3D printing for its excellent mechanical properties and high wear resistance. It is distinguished by its flexibility, durability, and lightness, making it an ideal material for producing functional and technical parts.
In 3D printing, nylon can come in the form of filament for FDM (Fused Deposition Modeling) technology or as powder for the SLS (Selective Laser Sintering) process. Thanks to its ability to withstand mechanical stress while remaining relatively elastic, nylon is especially valued in the fields of industry, design, and technical fashion.
Available printable nylon formats
3D-printable nylon is available in several formats adapted to different printing technologies. As a filament, nylon is used with FDM printers and often requires a heated bed and an enclosed chamber to ensure good adhesion and reduce warping. In powder form, nylon is used in SLS (Selective Laser Sintering) technology, offering excellent precision and support-free parts, ideal for complex geometries.
There are also nylon-based resin formulations for hybrid technologies like Multi Jet Fusion (MJF) or modified DLP, although these are significantly less common.
These different formats allow nylon to be adapted to a wide range of applications, from functional prototyping to serial production of technical parts.
What are the properties of nylon in 3D printing?
Nylon in 3D printing has a number of valuable properties, such as:
- A certain degree of mechanical strength
- Good flexibility
- Strong wear resistance
- Low friction
- High chemical resistance
- Good interlayer adhesion
All these advantages make nylon ideal for functional parts and applications that demand durability and flexibility.
Mechanical properties of nylon
Nylon is known for its exceptional mechanical properties, making it one of the highest-performing materials in 3D printing. It offers excellent tensile strength, making it ideal for parts subjected to high forces or repeated stress.
Its natural flexibility allows it to absorb shocks without breaking, unlike more rigid materials such as PLA. Nylon also shows strong wear and abrasion resistance, making it suitable for moving parts, gears, hinges, or clips.
Moreover, it retains its performance even after multiple bending cycles, making it a top choice for functional and industrial applications.
Thermal and chemical properties of nylon
Nylon has highly valued thermal and chemical properties in 3D printing, especially for technical and industrial applications. It offers good heat resistance, with heat deflection temperatures exceeding 100 °C, allowing it to maintain its shape and performance in moderately hot environments.
Chemically, nylon resists many solvents, oils, and mild chemicals, making it a suitable choice for parts in contact with active substances.
However, nylon tends to absorb moisture from the air, which can negatively affect its mechanical performance and print quality if not stored properly in a dry or dehumidified environment.
Aesthetic properties of nylon
Nylon has interesting aesthetic properties in 3D printing, although it is primarily chosen for its technical performance. Once printed, it typically has a matte or satin finish, with a slightly grainy texture when printed with SLS, or a smoother surface in FDM with optimized settings. Raw nylon is usually white or light gray, making it an excellent base for dyeing or aesthetic post-processing.
Nylon can be easily colored, especially in powder form, allowing for vibrant and uniform finishes. Its light weight and fine layer resolution also make it suitable for producing elegant, delicate, and complex objects, appreciated in design, fashion, and 3D-printed jewelry.
Advantages of 3D printing with nylon
The advantages of 3D printing with nylon include high mechanical strength, increased flexibility, exceptional durability, wear and chemical resistance, as well as a smooth surface finish and strong layer adhesion, making it ideal for industrial applications and functional parts.
The excellent durability of nylon
Nylon is renowned for its excellent durability, making it a top choice for 3D printing strong and long-lasting parts. Thanks to its high mechanical strength, ability to flex without breaking, and good resilience against wear and repeated impacts, it maintains its properties over time, even under demanding usage conditions.
This durability is accompanied by good dimensional stability, especially when stored and printed under controlled conditions (protected from moisture). Nylon also handles continuous mechanical stress, making it ideal for functional parts, such as gears, hinges, or structural components.
The ideal material for functional parts
Nylon is considered the ideal material for functional parts in 3D printing, thanks to its perfect balance of strength, flexibility, and lightweight properties. It performs excellently under mechanical stress, twisting, and impacts, making it perfectly suited for manufacturing technical components like hinges, gears, clips, and machine parts.
Its ability to flex without breaking, combined with its resistance to wear and friction, makes it indispensable in fields such as engineering, advanced prototyping, and finished part production. Additionally, its compatibility with mechanical assembly (such as screws, snap-fits, or interlocking) makes it an excellent choice for moving or articulated parts.
A lightweight yet strong material
Nylon is a lightweight yet strong material, making it a preferred choice for many 3D printing applications. Its low density allows for the creation of light parts, while maintaining high mechanical strength. This means it can withstand significant loads and stresses without deforming or breaking, while keeping a minimal weight.
This combination of lightness and strength makes it ideal for technical parts such as mechanical components, gears, or load-bearing structures in industries like aerospace, automotive, and functional prototyping. Its robustness also allows it to withstand repeated wear, while offering a material that is easy to handle and cost-effective for producing durable objects.
A good balance between performance and cost
Nylon offers an excellent balance between performance and cost, making it a highly valued material in 3D printing. While more affordable than high-end materials like titanium or aluminum, it provides outstanding mechanical and thermal properties, such as wear resistance, flexibility, and durability, which surpass many other polymers.
Nylon is therefore particularly well-suited for creating functional parts, such as gears or moving components, at a much lower cost while maintaining performance comparable to more expensive materials. This cost-performance ratio makes it indispensable for prototyping and small batch production, offering both professional results and optimal cost-effectiveness for budget-conscious projects.
High compatibility with assembly parts
Nylon has strong compatibility with assembly parts, making it an excellent choice for creating components that need to be easily integrated into mechanical assemblies. It can be easily adapted for parts that require screws, snap-fits, or interlocking features, ensuring secure and reliable connections between different components.
Its flexibility and strength allow for precise mechanical assemblies without the need for additional support structures. This makes it ideal for applications involving moving parts, articulated components, or functional assemblies in industries like automotive, engineering, and consumer products. Additionally, nylon’s ability to maintain its performance over time, even with repetitive movement or stress, enhances its suitability for assembly in both prototyping and final product production.
The disadvantages of nylon in 3D printing
The disadvantages of nylon in 3D printing include sensitivity to humidity (which can affect print quality), difficulty in adhesion to the print bed without proper preparation, shrinkage that can cause warping, and increased fragility under certain conditions, making the material more difficult to work with compared to other plastics.
A tendency to absorb moisture during storage
Nylon has a strong tendency to absorb moisture from the air, a phenomenon known as hygroscopicity, which can be problematic during storage and 3D printing. When exposed to ambient moisture, nylon quickly absorbs water, which can alter its mechanical properties, cause bubbles or cracks during printing, and degrade the surface quality of parts.
To avoid this, it is essential to store the filament or powder in a dry environment, ideally in airtight containers with desiccant packets or active drying systems. Pre-drying before printing (usually around 70-80°C for several hours) is often recommended to ensure optimal results. Although efficient, nylon requires rigorous moisture management to fully utilize its potential.
A difficult material to print
Nylon is considered a challenging material to print with due to its high sensitivity to temperature and humidity. It requires precise temperature control during both the extrusion and printing processes. Additionally, its tendency to warp and shrink can make it tricky to achieve consistent results, especially without the proper bed adhesion and environmental conditions. As a result, careful management and experience are needed for successful 3D printing with nylon.
A need for specific printing conditions
Nylon requires specific printing conditions to achieve optimal results. This includes maintaining a high printing temperature (typically around 240–260°C for the extruder) and using a heated bed (usually between 80–100°C) to prevent warping. Additionally, a closed printing environment with controlled humidity is recommended to avoid moisture absorption, which can degrade the print quality. Proper adhesion methods, such as using a glue stick or specialized bed surface, are often necessary to ensure successful prints.
Common uses of nylon in 3D printing
Common uses of nylon in 3D printing include the production of functional parts, complex prototypes, mechanical components such as gears and pulleys, custom tools, manufacturing supports, as well as wear-resistant parts in sectors like automotive, aerospace, and engineering.
Functional prototyping
Functional prototyping is one of the most common and relevant uses of nylon in 3D printing, thanks to its advanced mechanical properties and high durability. Unlike aesthetic or conceptual prototypes, functional prototypes are designed to be tested under real-world conditions in order to validate shapes, assemblies, or mechanical performances before final production.
Nylon, with its tensile strength, flexibility, and shock resistance, allows for the creation of parts that are close to their final version, capable of withstanding stress, repeated movements, or complex assemblies. This makes it a material of choice for sectors such as engineering, automotive, robotics, and mechanics, where prototypes need to be functional, reliable, and representative of the finished product.
Finished products
Nylon is also an excellent choice for the production of finished products in 3D printing, not just for prototyping. Thanks to its strength, wear resistance, and long-term durability, it allows for the creation of durable, functional, and ready-to-use items.
Many creators use it to produce everyday accessories, replacement parts, technical objects, or even design and fashion items such as jewelry, eyeglass frames, or soft articles printed using SLS (Selective Laser Sintering). Its fine detail, lightweight, and ability to withstand mechanical loads make it a material perfectly suited for small-batch production or on-demand manufacturing, for custom, strong, and aesthetic parts. With good finishing or dyeing, nylon parts can even rival those made using traditional industrial processes.
Parts for industry and engineering
Nylon is particularly well-suited for the production of parts intended for industry and engineering, thanks to its robust mechanical properties, wear resistance, and ability to withstand high stresses. In these sectors, it is often used to produce technical components such as gears, supports, fasteners, hinges, machine parts, and even custom tooling. Its resilience to shocks, friction, light solvents, and moderate temperatures makes it a reliable material for functional parts, even in demanding environments.
Furthermore, the ability to print using SLS (Selective Laser Sintering) or with reinforced technical filaments allows for performance levels close to machining, while reducing costs and lead times. Nylon thus enables engineers and manufacturers to design custom solutions that are quickly testable and directly usable in the field.
3D printed nylon for fashion and design
3D printed nylon is increasingly captivating the world of fashion and design, thanks to its lightweight, flexibility, and ability to bring complex, organic shapes to life. Particularly used with SLS technology, it allows for the creation of detailed objects without support structures, offering a level of finesse that appeals to jewelry creators, accessory designers, technical clothing, and interior décor elements. Nylon can be dyed in a wide range of colors, providing great aesthetic freedom while remaining durable and pleasant to the touch.
With its controlled flexibility, it is perfect for pieces like soft necklaces, earrings, or innovative fashion elements that combine functionality and aesthetics. Thus, it represents an ideal bridge between artistic creativity and advanced technology, enabling the production of light, elegant, and customizable pieces on demand.
How to successfully print with nylon in 3D?
To successfully print with nylon, it is essential to use a heated bed (around 80-100°C), maintain an extrusion temperature between 240-260°C, and prepare the bed with an adhesive or nylon-specific adhesive to prevent warping. Additionally, to avoid moisture, store the filament in airtight bags or drying boxes. Lastly, adjust the printing speed for better detail and a smooth finish.
Choosing the right technology for your nylon prints
To fully leverage nylon in 3D printing, it’s essential to choose the right technology based on your needs, as each method offers specific advantages.
FDM technology is ideal for functional prototypes, durable parts, and low-cost projects. It requires good printer calibration, a heated bed, and sometimes a closed chamber, but remains accessible and versatile.
On the other hand, for parts with complex shapes, fine details, and no support structures, SLS technology is the most suitable. It offers excellent precision, great design freedom, and consistent mechanical strength.
Finally, HP’s Multi Jet Fusion (MJF) technology, which is similar to SLS but faster, provides superior surface quality, sharp details, and industrial repeatability, making it ideal for serial production.
Applying the right print settings
To successfully print with nylon, it is crucial to apply the right print settings, as this material requires meticulous configuration to fully express its potential.
The extrusion temperature should generally be set between 240–270°C, depending on the type of nylon used, while the heated bed should be set between 60–90°C to ensure good adhesion.
A closed chamber is highly recommended to maintain a stable temperature and reduce the risk of warping.
It is also essential to print with dry filament, which should be pre-dried at 70–80°C for several hours to avoid bubbles, stringing, or layer defects. As for the print speed, it’s advisable to slow down the printing (around 30–60 mm/s) to improve layer cohesion.
Finally, using an appropriate adhesion surface (such as PA Glue, Magigoo special nylon, or a Garolite plate) will help secure the first layer. These precise settings are essential for ensuring strong, clean, and durable prints.
Properly organizing the storage of your raw materials
To properly organize the storage of your raw materials when 3D printing with nylon, it is essential to ensure a dry, temperature-controlled, and clean environment. Nylon should be stored in airtight packaging or sealed boxes to prevent moisture, which can degrade the quality of the material. It is also recommended to use dehumidifiers in storage areas or silica gel to maintain an optimal humidity level.
Temperature-controlled storage (around 20-25°C) is crucial to prevent any degradation of the nylon. Lastly, it is best to store the spools in a way that avoids excessive pressure or deformation, by placing them on shelves suited to their size and keeping them away from direct sunlight.
Post-processing your 3D nylon prints
Post-processing 3D nylon prints involves improving the finish and strength of the printed parts. After printing, it is often necessary to remove supports or excess material using a precision knife or a Dremel tool. To achieve a smooth and uniform surface, you can also proceed with progressive sanding using fine-grit sandpaper.
A thermal impregnation (or annealing) can be performed to enhance the part’s strength and improve its mechanical properties by heating the part to a temperature close to the melting point of nylon. If the part requires a more aesthetic finish, techniques such as painting or applying coatings (e.g., resin or a special varnish) can be used. For parts exposed to moisture, additional drying in a low-temperature oven may be helpful to ensure better stability of the nylon.
Conclusion: 3D Printing with Nylon
3D printing with nylon offers significant advantages thanks to its properties of strength, flexibility, and durability, making it an ideal choice for applications requiring robust and functional parts. However, to achieve optimal results, it is essential to properly prepare the material, master the printing process, and ensure meticulous post-processing.
Proper storage of nylon, moisture management, and choosing the right print settings are key elements in maximizing the quality of the final parts. Despite certain challenges, such as managing humidity and the need for precise storage temperatures, 3D printing with nylon remains a powerful tool in many fields, including engineering, prototyping, and the production of functional parts.
Picture by topntp26 from Freepik.
The articles published on Imprimy.com are for informational purposes only. They are intended to provide general advice and information related to 3D printing. Imprimy.com cannot be held responsible for the results obtained or the consequences arising from the application of the shared information. We recommend always checking the specific instructions for your hardware and materials before use.