Do you have questions about 3D printing of steel and its specifics? At Imprimy, we are here to answer all your queries on this topic.
3D printing in steel allows for revolutionizing metal manufacturing by offering increased precision, speed, and flexibility, while reducing costs and waste.
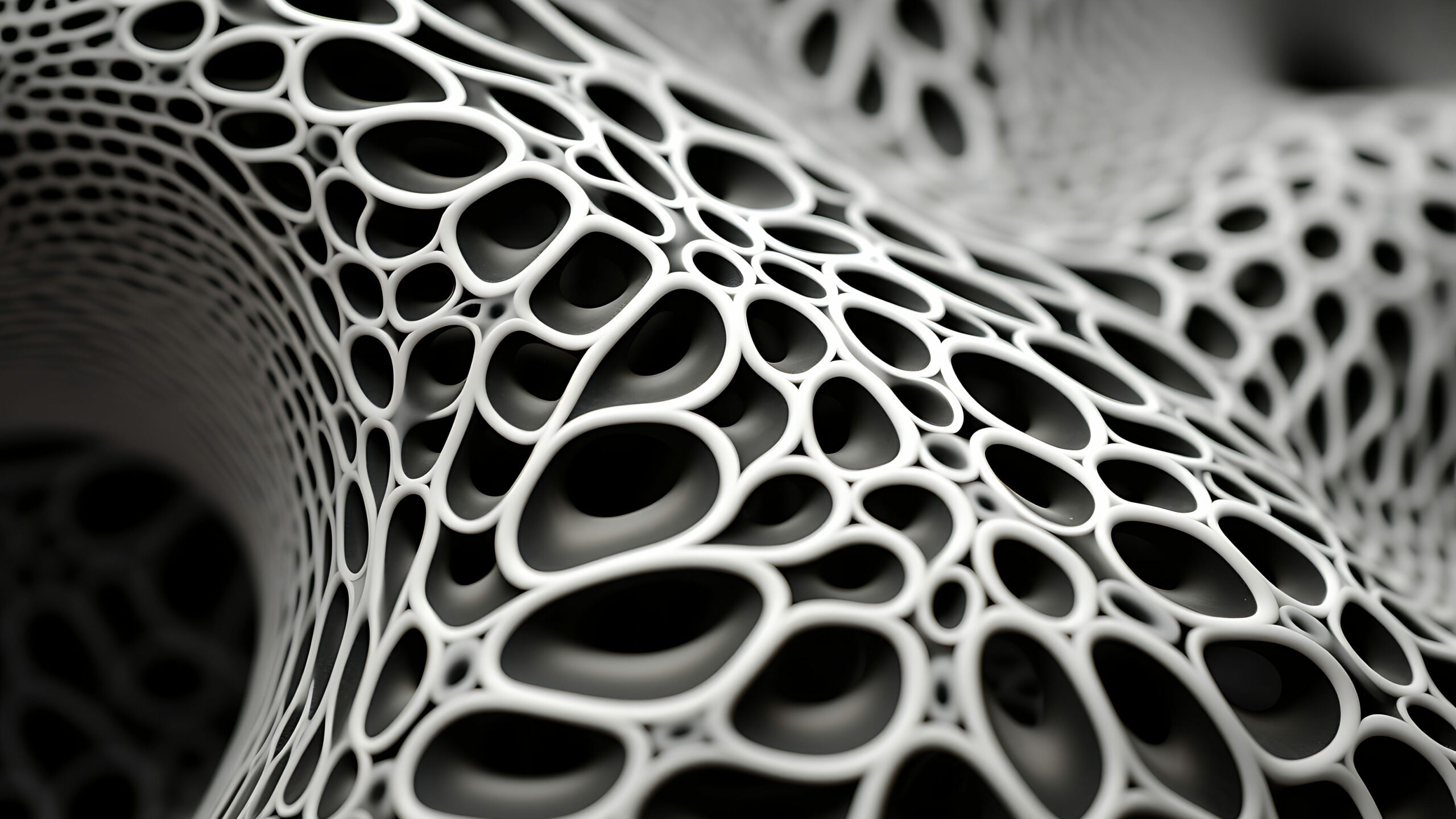
What is 3D printing in steel?
3D printing in steel is an additive manufacturing process that uses metal steel powders to create objects in successive layers, allowing for complex shapes, high strength, and applications in sectors such as aerospace, automotive, and industry.
The general definition of 3D printing in steel
3D printing in steel is an additive manufacturing process that involves creating objects by layering successive layers of metal materials, primarily steel, from a three-dimensional digital model.
Unlike traditional subtractive machining methods, this technology allows for the creation of complex shapes, often impossible to achieve otherwise, while optimizing the use of material. 3D printing in steel uses various techniques, such as laser melting or metal arc deposition, to produce precise, durable parts suitable for demanding sectors like aerospace, automotive, or construction.
The main technologies used in 3D printing in steel
The main technologies used in 3D printing in steel are:
- Laser melting on a powder bed (SLM for Selective Laser Melting) and electron beam melting (EBM for Electron Beam Melting), which melt metal powders layer by layer to form solid parts;
- Direct energy deposition (DED), where a laser or electric arc melts powder or metal wire directly onto the part being manufactured;
- Wire Arc Additive Manufacturing (WAAM), which uses an electric arc to melt a metal wire quickly and economically;
- Binder Jetting, where a liquid binder is sprayed onto a layer of metal powder before a sintering phase.
Why use steel for 3D printing?
Steel is used for 3D printing because of its strength, heat resistance, durability, and its ability to produce parts that are both lightweight and functional, making it ideal for demanding industrial applications.
The properties of 3D printed steel
3D printed steel has remarkable properties that make it a sought-after material in industry: it offers excellent mechanical strength, high hardness, and good corrosion resistance, especially for stainless steels. Moreover, thanks to the precise control of the manufacturing process layer by layer, it is possible to achieve high density and optimized microstructural characteristics.
3D printed steel is also distinguished by its ability to create complex geometries with lightweight internal structures while maintaining high strength, which improves the strength-to-weight ratio. Finally, certain techniques allow for the local adjustment of thermal or mechanical properties according to the needs of the application.
The different types of steels used in 3D printing
In 3D printing, several types of steels are used depending on the specific needs of the applications:
- Stainless steel (such as 316L or 17-4 PH) is widely used for its corrosion resistance and good toughness;
- Maraging steel (e.g., 18Ni300) is valued for its excellent mechanical properties after heat treatment;
- Tool steels (such as H13 or M300) are used to make molds and industrial tooling due to their wear resistance and high hardness;
- High carbon steels or alloyed steels are used for applications requiring specific characteristics such as high heat resistance or mechanical fatigue resistance.
What are the advantages and limitations of 3D printing in steel?
The advantages of 3D printing in steel include high precision, customization of parts, waste reduction, and the ability to create complex structures, while also enabling a reduction in production costs for small batches. However, the limitations include a relatively slow production speed, high costs for materials and machines, as well as challenges related to post-processing and the quality of parts, which can vary.
The different advantages of 3D printing in steel
3D printing in steel offers many advantages: it allows for the manufacture of complex parts with great design freedom, which would be difficult or impossible with traditional methods. It also offers a significant reduction in waste, as material is added only where it is needed, and enables rapid customization of parts and on-demand production, thus limiting storage costs.
Moreover, it can lead to an improvement in mechanical performance thanks to optimized internal structures (such as lattices), and promotes a reduction in production time and greater flexibility in iterating prototypes or adjusting parts for demanding sectors such as aerospace, automotive, or medicine.
The limitations and current challenges of 3D printing in steel
Despite its many advantages, 3D printing in steel still faces certain limitations and challenges: the high cost of equipment, materials, and maintenance is a barrier to wider adoption; production speeds are often slower than those of traditional industrial processes for large batches. There are also constraints on the size of parts, although progress is being made.
Additionally, quality control is complex, as it is necessary to ensure the absence of internal defects (such as porosity or cracks), which are often invisible without thorough analysis. Mechanical properties can also vary depending on the manufacturing parameters and require post-processing (such as machining or heat treatment) to achieve optimal performance.
Finally, the industrial standard for metal 3D printing is still being developed, which can slow down its mass adoption in certain critical sectors.
What are the practical applications of 3D printing in steel?
3D printing in steel finds practical applications in sectors such as aerospace for the production of lightweight and resistant parts, automotive for the creation of custom components, medical for customized implants, as well as in the industrial sector for tools and complex spare parts.
3D printing in steel in the industrial sector
In the industrial sector, 3D printing in steel is revolutionizing the manufacturing of complex parts by enabling the rapid production of functional prototypes, custom parts, and small batches. It is particularly used in aerospace to manufacture lightweight and resistant components, in automotive to develop engine parts or production tooling, and in the energy industry to create optimized turbines or heat exchangers.
3D printing in steel also allows in the medical industry to create customized implants with porous structures that promote bone integration. Finally, it provides innovative solutions in construction and the maritime sector to produce robust structures while reducing manufacturing time and costs associated with customization.
3D printing in steel in aerospace and space
In aerospace and space, 3D printing in steel plays a crucial role by enabling the manufacture of lightweight, robust, and highly complex parts, meeting the extreme demands of these sectors. It is used to produce engine mounts, landing gear parts, fluid ducts, and optimized internal structures through lightweight geometries such as lattices. It also allows for the design of satellite structures, rocket components, and propulsion systems, reducing weight and increasing resistance to extreme temperatures.
It also offers a reduction in manufacturing costs and development time, while allowing for customization tailored to the specific constraints of each mission. Finally, this technology paves the way for additive manufacturing projects in situ, such as on the Moon or Mars, to directly produce the parts needed for space exploration.
3D printing in steel in the medical sector
In the medical sector, 3D printing in steel is a major asset for creating customized implants, custom prosthetics, and complex surgical instruments. Stainless steel is particularly valued for its biocompatible properties, corrosion resistance, and durability in the human body. This technology allows for the production of orthopedic implants, such as bone plates and osteosynthesis screws, perfectly tailored to the patients’ morphology, thus improving comfort and healing.
Moreover, 3D printed porous structures promote better bone integration and reduce rejection, and 3D printing in steel is also used to produce custom surgical tools and precise cutting jigs, optimizing the precision of procedures and reducing operation time. Finally, it contributes to the reduction of costs and the shortening of lead times in the production of complex medical devices.
3D printing in steel in the automotive sector
In the automotive sector, 3D printing in steel offers significant advantages for the manufacturing of complex parts and the reduction of production costs. It is used to create engine components, suspension parts, manufacturing tooling, and lightweight but durable body parts, optimizing the strength-to-weight ratio; the internal structures of parts can be designed to reduce mass while maintaining strength, which helps improve the energy efficiency of vehicles.
3D printing also allows for rapid prototyping and testing of new designs, speeding up the development of innovative models and reducing time to market; moreover, it facilitates on-demand production of custom parts or parts that are difficult to produce using traditional methods, especially in the context of vehicle repairs or small batch production.
What is the future of 3D printing in steel?
The future of 3D printing in steel relies on technological innovations aimed at improving speed, precision, and cost-effectiveness, as well as on growing adoption in industries such as aerospace, automotive, and medicine, with the potential for cost reduction and optimization of manufacturing processes.
Technological advancements expected in 3D printing in steel
The expected technological advancements in 3D printing in steel are set to transform the way metal parts are manufactured, with progress in several key areas.
Firstly, significant improvements in manufacturing speed are anticipated, with techniques that reduce production times, particularly through the use of multi-laser systems or faster deposition. The optimization of materials is also expected, with new metal alloys specifically designed for 3D printing, offering superior mechanical properties or better corrosion resistance and resistance to extreme temperatures.
Increased automation of the process and the integration of artificial intelligence should also allow for better quality control and more precise management of manufacturing parameters. Moreover, the development of hybrid techniques, combining 3D printing with traditional processes, is expected to produce high-performance parts while reducing costs and increasing flexibility.
Finally, the use of 3D printing on-site, particularly in remote environments or for space or marine applications, could become common, enabling the production of metal parts directly where they are needed.
Challenges of industrial production in 3D printing in steel
Industrial production of 3D printing in steel faces several significant challenges. First, the high cost of equipment and materials remains a major obstacle, making this technology still relatively expensive compared to traditional production methods, particularly for large batches. Next, production speed is often slower, limiting the efficiency of 3D printing for applications requiring high volumes.
The quality and reliability of printed parts are also a challenge, as it is essential to maintain strict standards in terms of mechanical properties, dimensional precision, and the absence of defects such as porosity or internal cracks. Additionally, control of manufacturing parameters is complex, and printed parts may require post-processing such as machining or heat treatment to achieve the desired performance. Another major challenge is the management of the supply chain for materials, as the metal powders used in 3D printing are often expensive and need to be carefully stored and handled to avoid contamination.
Finally, the integration of 3D printing into traditional production lines and adapting to industrial standards remain challenges for many companies, who must ensure that this technology is compatible with their existing processes and regulatory requirements.
Challenges to overcome for 3D printing in steel
3D printing in steel presents several major challenges to overcome for large-scale adoption and industrialization. First, there is the issue of high costs, both for the materials (such as metal powders) and the equipment needed for printing, which limits its accessibility for many companies.
Next, production speed is often slower compared to traditional processes, which can make 3D printing less competitive for mass production. Moreover, the quality of printed parts, particularly dimensional precision, density, and mechanical strength, can be affected by variations in manufacturing parameters or internal defects (such as porosity), often requiring post-processing to achieve finished parts with optimal characteristics.
Quality control is therefore a major challenge, especially since defects may not be visible to the naked eye. Another challenge concerns the materials, as 3D printing-specific steel alloys must offer properties suited for industrial applications while remaining cost-competitive. Integration into existing industrial processes remains complex, as 3D printing requires adaptations to production lines, particularly for processing parts on a large scale.
Finally, the management of materials and metal powder stocks, which are sensitive to humidity and contamination, represents another logistical and economic challenge. These obstacles must be overcome for 3D printing in steel to fully develop in industries.
Conclusion: 3D printing in steel
3D printing in steel represents a major technological advancement that is transforming various industrial sectors, including aerospace, automotive, medicine, and the construction industry. It allows for the manufacturing of complex and customized parts with optimized mechanical properties, while reducing waste and offering on-demand production possibilities.
However, despite its numerous advantages, it faces significant challenges, such as high costs, production speed limitations, and strict quality requirements. The integration of this technology into traditional industrial processes and the improvement of materials and equipment are crucial steps for its widespread adoption. As technologies evolve and costs decrease, 3D printing in steel could become an essential solution to meet the needs for flexibility, customization, and performance in industrial production.
Picture by Freepik.
The articles published on Imprimy.com are for informational purposes only. They are intended to provide general advice and information related to 3D printing. Imprimy.com cannot be held responsible for the results obtained or the consequences arising from the application of the shared information. We recommend always checking the specific instructions for your hardware and materials before use.