Are you wondering about copper 3D printing, its limitations, and its specific features? At Imprimy.com, we’re here to answer all your questions.
Copper 3D printing makes it possible to create metal objects with exceptional electrical and thermal conductivity, often used in fields like electronics and aerospace.
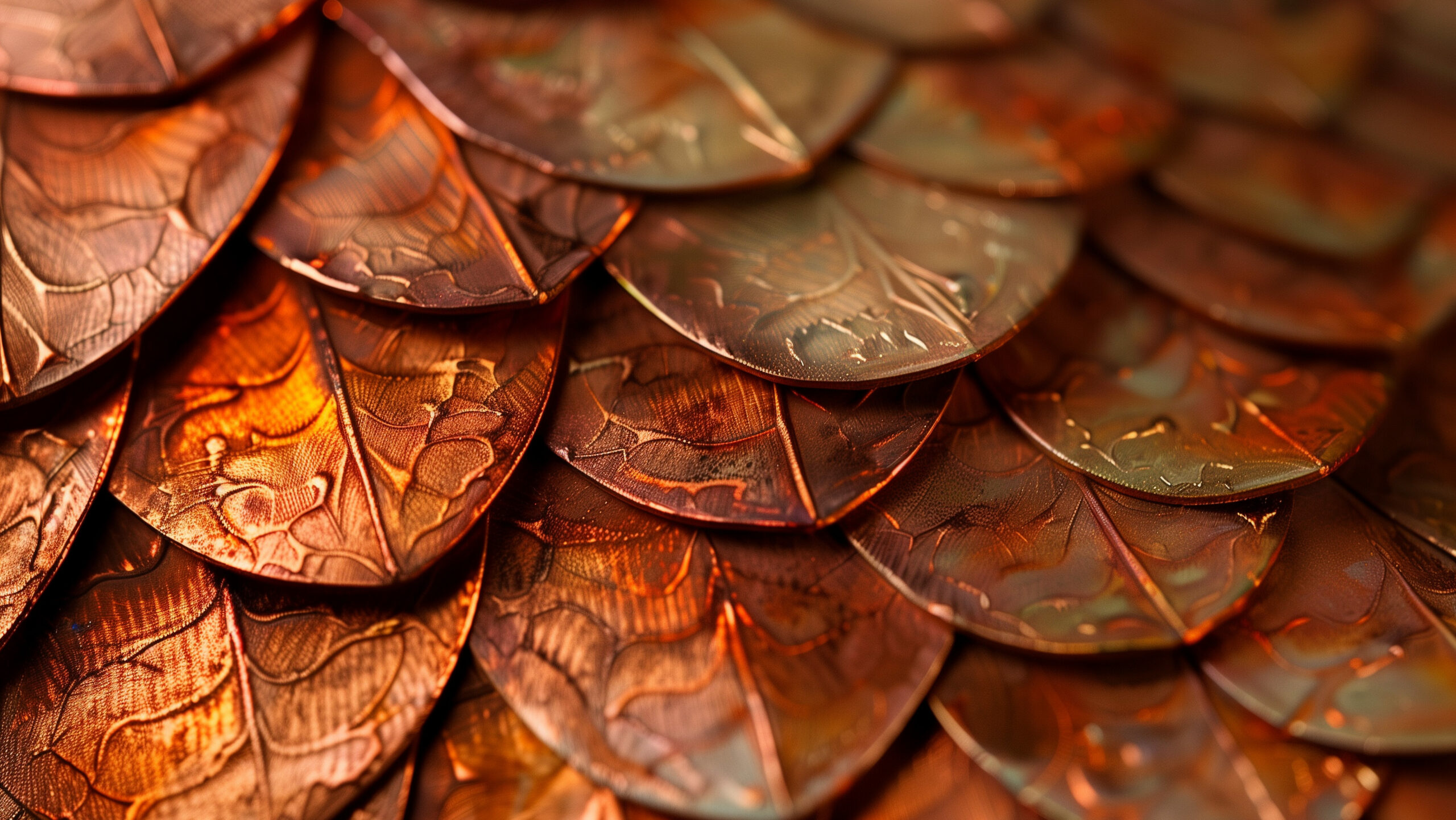
Is copper used in 3D printing?
Yes, copper is used in 3D printing, especially for its electrical and thermal conductivity, and it is often used in applications related to electronics and industry.
The different properties of copper
Copper has several properties that make it attractive for 3D printing, although its use is still limited to certain specific technologies such as laser powder bed fusion. It stands out for its excellent thermal and electrical conductivity, which makes it a preferred material in the electronics and thermal sectors.
However, its high reflectivity makes it difficult to melt with standard lasers, requiring high-power lasers or specially adapted systems. In addition, pure copper has high density and low mechanical strength, which can limit some structural applications, although alloys are sometimes used to compensate for these weaknesses.
Copper-based 3D printing
Copper-based 3D printing is an emerging technology that enables the production of complex parts while leveraging the unique properties of this metal. Mainly used in processes like selective laser melting (SLM) or binder jetting, it allows the creation of objects in pure copper or copper alloys, offering excellent thermal and electrical conductivity.
This capability is especially valuable in the aerospace, automotive, and electronics sectors, for manufacturing heat exchangers, induction coils, or connectors. However, copper presents technical challenges in 3D printing, mainly due to its high reflectivity and thermal conductivity, which can interfere with laser melting.
Recent technological advancements, such as the use of green lasers or high-energy systems, have improved control over copper printing, paving the way for more efficient and precise production of high-performance components.
Which 3D printing technologies are compatible with copper?
The 3D printing technologies compatible with copper include Selective Laser Melting (SLM), Fused Deposition Modeling (FDM) with copper-based filaments, and Electron Beam Melting (EBM). These methods enable the creation of objects in pure copper or copper alloys.
Laser Powder Bed Fusion 3D Printing
Laser Powder Bed Fusion 3D printing, also known as Selective Laser Melting (SLM) or Direct Metal Laser Sintering (DMLS), is an additive manufacturing technology that uses a high-power laser to selectively melt metal powder particles, layer by layer, to create solid 3D objects. This process is particularly suited for metals such as stainless steel, titanium, aluminum, or copper, although copper requires specific adjustments due to its high reflectivity and thermal conductivity.
Laser fusion enables the production of complex, lightweight, and highly precise parts, while reducing material waste. It is widely used in demanding sectors like aerospace, medical, and automotive, especially for functional prototypes, custom implants, or thermal components. This technique stands out for its ability to produce parts with excellent density and strong mechanical properties, comparable to those of machined parts.
Extrusion-based manufacturing with copper composite filament
Extrusion-based manufacturing using copper composite filament is a 3D printing method based on the Fused Deposition Modeling (FDM) process, using a thermoplastic filament loaded with copper particles. This filament, often made from PLA or another polymer, can contain a high percentage of metal powder (up to 80% in some cases), allowing the production of objects with the appearance, density, and sometimes even certain thermal properties of copper.
Although these parts are not as conductive as those produced with pure copper processes, they offer a more accessible solution, especially for aesthetic prototyping, decorative accessories, or objects where a metallic look is desired. The presence of metal in the filament requires reinforced nozzles (often made of hardened steel) to prevent rapid wear of the extruder. This technique thus combines the benefits of FDM printing, such as low cost and ease of use, with the visual and tactile appeal of copper.
Binder Jetting and Sintering
Binder Jetting, also known as liquid binder deposition, is a 3D printing technology that selectively deposits a liquid binder onto a layer of metal powder, such as copper, to build a 3D part layer by layer. Unlike laser melting processes, the metal is not melted during printing, making this method faster and more energy-efficient.
Once the object is printed, it is in what’s called a “green state“—still fragile and not yet solidified. It must then undergo a sintering step, where the part is heated to high temperatures in a furnace to fuse the metal particles without reaching their full melting point. Sintering results in a dense, strong part with improved mechanical properties.
This combination of processes is particularly well-suited to metals that are difficult to print using melting techniques, such as copper, by avoiding issues related to its reflectivity and thermal conductivity. It is used in industry, especially for series production of functional, complex, and cost-effective parts.
What are the advantages of copper 3D printing?
Copper 3D printing offers several advantages, such as high electrical and thermal conductivity, high precision in the production of complex parts, cost reduction for prototypes and custom components, as well as greater design flexibility for components.
Design freedom
The design freedom offered by 3D printing is one of its major advantages, especially in the production of copper or other metal parts. Unlike traditional manufacturing methods, which impose geometric constraints related to machining or molding, 3D printing allows the creation of complex, lightweight, customized, and topologically optimized shapes, such as lattice structures, internal cooling channels, or organic geometries that are impossible to produce otherwise.
This freedom not only allows for the lightening of parts without compromising their strength, but also enables the integration of multiple functions into a single component, reducing the need for assembly. In the case of copper, it paves the way for custom heat exchangers or induction coils, with enhanced performance thanks to over-optimized geometries.
Performance optimization
Performance optimization through 3D printing, especially with materials like copper, relies on the ability to design custom parts tailored to specific functional and thermal constraints. With generative design tools and digital simulation, it is possible to create geometries that significantly improve aspects such as thermal dissipation, mechanical strength, and weight reduction, while maintaining strength.
In the case of copper, this optimization allows for the design of heat exchangers, complex cooling circuits, or high-performance inductors, often more efficient than their counterparts made with traditional methods. 3D printing also enables functional integration, combining multiple components into a single part, which reduces waste, improves reliability, and decreases the overall volume.
Waste reduction
Waste reduction is one of the major advantages of 3D printing, especially in the production of metal parts such as those made from copper. Unlike traditional machining or casting processes, which are often subtractive, 3D printing is an additive process that only uses the amount of material needed to build the part. This results in a significant reduction in material waste, which is particularly important when dealing with expensive metals like copper.
Additionally, unused powder or excess filament can often be reused, further enhancing the eco-friendly aspect of this technology. This ability to manufacture in a cleaner and more efficient manner contributes to better industrial sustainability, while also reducing costs associated with scrap and waste management.
What are the current limitations of copper 3D printing?
The current limitations of copper 3D printing include limited resolution, sometimes difficult layer adhesion, a risk of warping during printing, and a relatively slow printing speed compared to other materials, which can make large-scale production less efficient.
The costs and accessibility of copper 3D printing
The costs and accessibility of copper 3D printing remain significant barriers to its large-scale adoption, although the technology is advancing rapidly. Processes like laser fusion require specialized equipment (often very expensive), including powerful lasers capable of processing a metal as reflective and conductive as copper. Additionally, high-purity metal powders, which are essential for achieving good properties, are themselves costly. On top of this, there are the costs related to post-processing, such as sintering, de-powdering, or heat treatment.
However, more accessible solutions are emerging, particularly through the extrusion of copper composite filaments, which allow consumer-grade FDM printers to produce parts at a lower cost, although the mechanical and thermal performance may be lower. The development of technologies like Binder Jetting is also helping to democratize metal printing, offering a faster and more cost-effective alternative.
Technical difficulties
Copper 3D printing faces several technical challenges related to its unique properties, which complicate its implementation. One of the main challenges lies in its high reflectivity, making copper difficult to melt using conventional lasers, as used in processes like laser fusion. This reflectivity prevents effective absorption of the laser energy, requiring high-power systems or special lasers (such as green lasers), which increases both costs and the complexity of the printing process.
Additionally, copper has a high thermal conductivity, which can lead to rapid heat dissipation during printing, disrupting the fusion process and resulting in warping or imperfections in the parts. Moreover, its low mechanical strength in its pure form limits its use in structural applications without the addition of alloys or other materials.
Furthermore, the sintering process or post-processing steps required to solidify the part add an extra layer of complexity and extend production times. These technical challenges require specialized equipment, precise settings, and high-quality materials, which raise the barrier to entry for many companies.
Complex post-processing
Complex post-processing is a key aspect of copper 3D printing, as the parts produced after printing are often in a fragile and unfinished state, requiring several steps to make them functional and durable. After printing, especially with processes like Binder Jetting or laser fusion, the metal parts are still malleable and must undergo a series of treatments to enhance their mechanical and aesthetic properties.
- Sintering: After printing, the parts must be heated to high temperatures in a furnace to fuse the metal particles together, which is especially crucial for copper. This step improves the density and mechanical strength of the part, but can lead to warping if not properly controlled.
- De-powdering: When metal powders are used, as in Binder Jetting, it is necessary to remove the residual unfused powder, which can be a delicate operation, especially for parts with complex shapes.
- Heat treatment (annealing): To reduce internal stresses and improve ductility of the copper, annealing may be required, involving extended treatment times and precise temperature control.
- Polishing and finishing: Finally, the parts may require polishing or surface finishing to achieve a uniform and aesthetic appearance, especially if the goal is to produce a decorative product or a smooth conductive surface.
Thus, post-processing adds considerable complexity to the copper 3D printing process, requiring both technical skills and specialized equipment. These steps influence not only the production time, but also the final cost and the quality of the parts produced.
What are the concrete applications of copper 3D printing?
The concrete applications of copper 3D printing include the creation of electronic components such as printed circuit boards, heat exchangers, antennas for telecommunications, as well as custom parts in aerospace and automotive industries for optimized performance.
Copper 3D printing in aerospace and space industries
Copper 3D printing is finding increasingly interesting applications in demanding sectors like aerospace and space, where the thermal and electrical properties of copper are essential. In these fields, copper is mainly used for its excellent thermal and electrical conductivity, making it particularly suited for components exposed to high temperatures or requiring efficient cooling.
- Heat exchangers and cooling systems: In aerospace and space, engines and electronic systems generate vast amounts of heat. Copper, with its excellent thermal conductivity, is used to make heat exchangers or complex cooling channels, directly integrated into components to optimize thermal dissipation. 3D printing allows for the creation of custom geometries, such as complex internal channels, that would not be achievable with traditional manufacturing methods.
- Electronic components: Since copper is an excellent electrical conductor, it is used to manufacture printed circuits or connectors in environments where electrical performance is critical. Thanks to 3D printing, miniaturized or complex components can be produced more quickly and with optimized geometries, thus reducing the weight and volume of the equipment while enhancing their efficiency.
- Weight and optimization: Since aerospace and space industries require every gram to count, 3D printing helps reduce the weight of parts while maintaining high mechanical properties. Complex and lightweight geometries, such as those optimized through generative design, allow for a minimized use of materials while ensuring the strength and functionality of parts.
- Rapid prototyping: Copper 3D printing allows for the production of functional prototypes at a reduced cost and faster than traditional methods, which is crucial for the development of new technologies in these highly competitive sectors.
Copper 3D printing in electronics and electrical industries
Copper 3D printing in the electronics and electrical sectors opens new possibilities for manufacturing more performant and customized components. Thanks to this technology, it is now possible to create complex printed circuits, electrical conductors, and antennas with high precision and increased efficiency.
Since copper is an excellent conductor of electrical current, it helps enhance the performance of devices while reducing production costs. The use of 3D printing for these applications offers unprecedented flexibility, especially for rapid prototyping and the integration of innovative designs, which is a major advantage for innovation in the field of power electronics and electrical systems.
Copper 3D printing in the medical field
Copper 3D printing in the medical field is generating significant interest due to its unique properties, including its biocompatibility and thermal and electrical conductivity capabilities. This technology allows for the creation of custom implants and medical devices tailored to the specific needs of patients, while ensuring better integration into the human body.
For example, 3D printing of catheters or prosthetics in copper could improve treatments by providing more effective and customized solutions. Additionally, copper, with its antibacterial properties, can reduce the risk of infections, making it a key material for designing safe and durable medical devices. This approach opens new avenues for innovation in medicine, while improving patient care quality.
Conclusion: Copper 3D Printing
In conclusion, copper 3D printing represents a significant advancement in various sectors, including electronics, electricity, and medicine, due to its exceptional characteristics such as conductivity, biocompatibility, and design flexibility. It allows for the creation of more performant, customized, and specific components, while offering considerable possibilities for innovation.
The use of copper in 3D printing paves the way for innovative applications, whether for medical devices, electronic circuits, or custom implants, thus contributing to the technological evolution in these fields. This material offers multiple advantages, from improving performance to reducing production costs, marking a turning point in the manufacturing of smarter and more efficient products.
Picture by Freepik.
The articles published on Imprimy.com are for informational purposes only. They are intended to provide general advice and information related to 3D printing. Imprimy.com cannot be held responsible for the results obtained or the consequences arising from the application of the shared information. We recommend always checking the specific instructions for your hardware and materials before use.