Are you wondering about stainless steel 3D printing and want to know more about it? At Imprimy, we’re here to answer all your questions.
Stainless steel 3D printing makes it possible to produce strong, corrosion-resistant, and precise parts, ideal for use in the aerospace, medical, and industrial sectors.
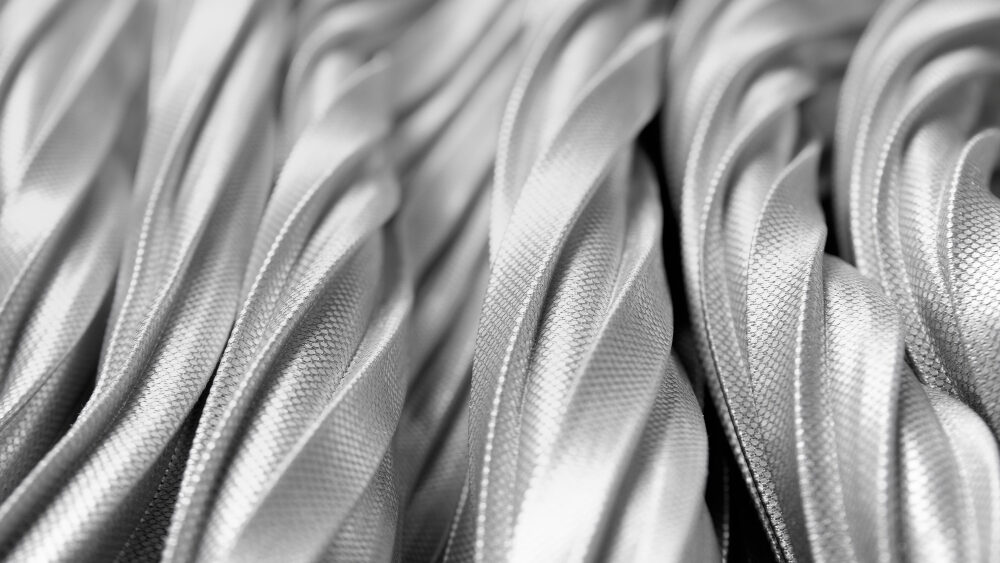
What is stainless steel 3D printing?
Stainless steel 3D printing is an additive manufacturing process that uses stainless steel powder to create, layer by layer, solid, durable, and corrosion-resistant objects, often used in demanding fields such as aerospace, medical, and industrial sectors.
- What is stainless steel 3D printing?
- What are the 3D printing technologies for stainless steel?
- What are the applications of stainless steel 3D printing?
- What are the challenges and limitations of stainless steel 3D printing?
- What is the future of stainless steel 3D printing?
- Conclusion: Stainless Steel 3D Printing
The definition of stainless steel 3D printing
Stainless steel 3D printing is an additive manufacturing process that uses stainless steel as the material to create three-dimensional objects. This process typically involves the use of a 3D printer that deposits successive layers of stainless steel powder or wire, which are fused together using a laser or electron beam.
This technology allows the production of corrosion-resistant, durable, and complex parts, suitable for various industrial, medical, and aerospace applications. The advantages of stainless steel 3D printing include design freedom, material waste reduction, and the ability to create complex geometries that would be difficult or impossible to achieve with traditional manufacturing methods.
Materials used in stainless steel 3D printing
The materials used in stainless steel 3D printing are primarily stainless steel alloys, valued for their corrosion resistance, durability, and strength. Common types of stainless steel used include austenitic stainless steel, such as 316L, which is particularly popular due to its superior corrosion resistance and biodegradability, making it suitable for medical applications.
Other alloys, such as 17-4PH, are also used for applications requiring high mechanical strength. These materials are generally available in fine powder or wire form, suited for different 3D printing technologies, such as laser sintering (SLM) or directed energy deposition (DED).
Advantages of stainless steel 3D printing
Stainless steel 3D printing offers several significant advantages that make it a preferred technology for many industrial and specialized applications. Here are some of its main benefits:
Corrosion resistance: Stainless steel is naturally resistant to rust and corrosion, making 3D printed parts ideal for harsh environments or those exposed to corrosive elements.
- Durability and strength: Stainless steel parts are strong and durable, capable of withstanding heavy loads and extreme conditions, making them suitable for demanding applications.
- Design freedom: 3D printing allows for the creation of complex geometries and internal structures that would be impossible or very costly to achieve with traditional manufacturing methods.
- Waste reduction: Unlike subtractive methods, 3D printing is an additive process that uses only the material necessary to build the part, minimizing material waste.
- Customization and flexibility: The technology allows for easy customization of parts, which is particularly useful for producing custom-made parts or prototypes.
- Diverse applications: Due to its properties, stainless steel 3D printing is used in various sectors, including aerospace, medical, automotive, and food industries.
These advantages make stainless steel 3D printing an attractive solution for producing high-quality and high-performance parts.
What are the 3D printing technologies for stainless steel?
The main 3D printing technologies for stainless steel are: SLM (Selective Laser Melting), DMLS (Direct Metal Laser Sintering), EBM (Electron Beam Melting), Binder Jetting, and DED (Directed Energy Deposition), each using specific methods of fusion or deposition of stainless steel powder or wire to manufacture strong and functional parts.
Available technologies in stainless steel 3D printing
Stainless steel 3D printing uses several advanced technologies to create stainless steel parts. Among the main methods, there is SLM (Selective Laser Melting), which uses a laser to fuse metal powders, and FDM (Fused Deposition Modeling), which is suitable for certain alloys.
Other techniques include Binder Jetting and DED (Directed Energy Deposition). These technologies allow for the production of complex components with high strength and good surface finish, suitable for sectors such as aerospace, medical, and automotive.
How stainless steel 3D printing works
Stainless steel 3D printing works by layering stainless steel powder to build complex parts. The process typically starts with the creation of a 3D model using CAD software. This model is then sliced into thin layers by slicing software. In the case of SLM (Selective Laser Melting) technology, a high-powered laser selectively fuses the stainless steel powder according to the pattern of each layer.
Once a layer is completed, the build platform slightly lowers, and a new layer of powder is spread to repeat the process. This continues until the part is fully built. After printing, the parts may require post-processing treatments such as polishing or heat treatments to enhance their mechanical properties.
Comparison of different stainless steel 3D printing technologies
The comparison of stainless steel 3D printing technologies reveals significant differences in terms of precision, speed, cost, and applications. SLM (Selective Laser Melting) is known for its high precision and its ability to produce parts with complex details, making it ideal for the aerospace and medical industries.
However, it can be more expensive due to the high cost of machines and materials. FDM (Fused Deposition Modeling) technology is generally cheaper and more accessible, but it offers lower resolution and is less suitable for parts requiring high strength. Binder Jetting allows for rapid production and can be used for larger parts, but the parts may require post-processing to achieve the desired mechanical properties.
Finally, DED (Directed Energy Deposition) is excellent for repairing and adding material to existing parts, but it offers lower precision compared to SLM. Each technology thus has its advantages and limitations, and the choice depends on the specific requirements of the project.
What are the applications of stainless steel 3D printing?
The applications of stainless steel 3D printing include the production of complex mechanical parts, medical prostheses, custom tools, aerospace components, food equipment, and heat or corrosion-resistant parts, thanks to the strength and chemical resistance of stainless steel.
Stainless steel 3D printing in aerospace
Stainless steel 3D printing plays a crucial role in the aerospace sector, offering significant advantages in terms of weight reduction, reduced complexity, and component customization. This technology enables the production of complex parts with increased precision, which is essential for aerospace applications where reliability and performance are critical.
Moreover, 3D printing allows for rapid iteration of designs, accelerating the development process and reducing production costs by up to 90% in some cases. Materials like stainless steel are particularly valued for their strength and durability, which are essential in the demanding environments of aerospace.
Stainless steel 3D printing in the medical field
Stainless steel 3D printing plays a transformative role in the medical field, offering innovative and customized solutions. Stainless steel, known for its strength and durability, is widely used to manufacture surgical instruments and other medical devices. This technology allows for the creation of custom prostheses and implants, tailored to the specific needs of patients, thus improving their comfort and quality of life. For example, 3D printing has reduced the number of steps required to produce hearing aids by using 3D scanners to create precise ear impressions.
Additionally, stainless steel 3D printing is used to produce orthopedic parts and surgical tools, benefiting from its biocompatibility and corrosion resistance. Advancements in this field also suggest the potential creation of artificial tissues and organs, opening new avenues for regenerative medicine and grafting. Moreover, 3D printing aids in the training of doctors by allowing for the accurate reproduction of anatomical parts for practice before real-life procedures.
Stainless steel 3D printing in the automotive sector
Stainless steel 3D printing is playing an increasingly important role in the automotive sector, offering innovative solutions for vehicle manufacturing. This technology allows for the production of lighter and stronger parts, which is crucial for improving energy efficiency and vehicle performance. For example, 3D printing enables the reduction of component mass without compromising their performance, while optimizing costs and production timelines.
In the automotive sector, 3D printing is used at every stage of the manufacturing cycle, from prototyping to finished parts, including tooling. Materials like stainless steel are particularly valued for their corrosion resistance and durability, making them ideal for demanding applications in the automotive industry.
Furthermore, 3D printing allows for increased customization of parts, which is particularly advantageous for the production of custom vehicles or small batches. It also facilitates on-demand production, reducing the constraints associated with inventory management.
What are the challenges and limitations of stainless steel 3D printing?
The main challenges and limitations of stainless steel 3D printing are the high cost of equipment and materials, the need for complex post-processing (such as sintering or polishing), design constraints related to supports, the risk of porosity or internal defects, and a production speed that is often slower than that of traditional methods.
Technical challenges of stainless steel 3D printing
Stainless steel 3D printing presents several technical challenges that must be overcome to fully exploit its potential. Here are some of the main challenges:
- Quality and precision control: Stainless steel 3D printing requires extreme precision to produce parts with tight tolerances. Variations in the printing process can lead to defects such as porosity or cracks, affecting the strength and durability of the parts.
- Thermal stress management: The 3D printing process, especially for metals like stainless steel, involves high thermal gradients that can cause deformations or residual stresses in the parts. This requires advanced thermal control strategies to minimize these effects.
- Optimization of printing parameters: Parameters such as print speed, laser power, and temperature must be carefully optimized for each part and material type. Poor configuration can lead to defects or poor surface quality.
- Post-processing: Parts printed in 3D with stainless steel often require post-printing treatments such as polishing, heat treatment, or machining to achieve the desired mechanical properties and surface finish. These steps add complexity and cost to the manufacturing process.
- Material compatibility: While stainless steel is widely used, not all alloys are suitable for 3D printing. The development of new alloys specifically for 3D printing is an active research area to improve the properties of printed parts.
- Cost and accessibility: Metal 3D printers are expensive and require high initial investments. Additionally, training operators and maintaining equipment adds to the overall complexity and cost.
- Integration into existing production lines: Integrating stainless steel 3D printing into traditional manufacturing processes can be complex, requiring adaptations to workflow and production management systems.
By overcoming these challenges, stainless steel 3D printing can offer significant advantages in terms of design flexibility, waste reduction, and customization of parts, opening new possibilities in various industrial sectors.
Costs associated with stainless steel 3D printing
Stainless steel 3D printing involves several costs to consider. First, the equipment is a major factor: 3D printers capable of working with stainless steel are generally expensive.
Next, the cost of materials themselves, such as filaments or stainless steel powders, can be high. Operational costs, including energy and equipment maintenance, must also be taken into account.
Finally, staff training to operate these machines and post-processing costs, such as polishing and cleaning parts, are additional elements that should not be overlooked.
Material limitations of stainless steel 3D printing
Stainless steel 3D printing presents several significant material limitations. First, the process requires high technical expertise due to the very high melting temperatures of stainless steel, which can lead to challenges in design and thermal stability.
Additionally, the mechanical properties of printed parts can be affected by internal stresses caused by the manufacturing process, which may limit their strength and durability. The size limitations of current 3D printers can also pose issues for the production of large structures or bulk objects.
Finally, the costs associated with specialized equipment and materials for stainless steel 3D printing can be prohibitive, limiting its widespread adoption.
What is the future of stainless steel 3D printing?
The future of stainless steel 3D printing looks promising with advancements towards cost reduction, improved part quality, increased process automation, and growing adoption in the industrial, medical, and space sectors due to the demand for customized, lightweight, and high-performance parts.
Innovations in stainless steel 3D printing
Stainless steel 3D printing has seen several recent innovations that have expanded its applications and improved its capabilities. Among the notable advancements are the use of DMLS technology, which allows for the production of stainless steel parts with great precision and mechanical strength. Another innovation is Binder Jetting, an additive manufacturing method that uses a binding agent to create stainless steel parts, offering good high-temperature resistance and the ability to handle complex shapes.
Additionally, materials like Ultrafuse Stainless Steel 316L, an industrial metal filament made of 90% stainless steel and 10% polymer binder, allow for affordable and efficient 3D printing on standard FDM/FFF printers. These innovations not only enable the production of more durable and resistant parts, but also open up new applications in sectors such as aerospace, automotive, and medicine.
Research and development in stainless steel 3D printing
Research and development in the field of stainless steel 3D printing focuses on improving additive manufacturing technologies for stainless steel alloys.
Recent advancements include the optimization of printing parameters, such as deposition speed and temperature, to enhance the mechanical strength and surface finish of the produced parts. Researchers are also exploring new composite materials and post-processing techniques to strengthen the properties of stainless steel parts.
Additionally, the integration of artificial intelligence and machine learning allows for better prediction and control of manufacturing defects, paving the way for broader and more reliable industrial applications.
Future prospects of stainless steel 3D printing
The future prospects of stainless steel 3D printing are promising and extend across various industrial sectors. This technology, which has been constantly evolving since the 2010s, enables the creation of complex and customized parts with great precision, using a variety of materials such as stainless steel, plastic, and even innovative composites.
In the aerospace and automotive industries, stainless steel 3D printing offers possibilities for cost reduction and performance optimization of components, while enabling more sustainable and environmentally-friendly manufacturing. Furthermore, the integration of 3D printing into extreme environments, such as the International Space Station (ISS), demonstrates its potential for space applications and other demanding sectors. Advances in bio-printing also open up revolutionary prospects in the medical field, with the possibility of creating functional tissues and organs, thereby transforming regenerative medicine.
Finally, stainless steel 3D printing plays a key role in reducing construction waste, promoting sustainable and innovative construction practices.
Conclusion: Stainless Steel 3D Printing
Stainless steel 3D printing represents a major advancement in additive manufacturing, offering innovative and transformative possibilities for various industrial sectors. Thanks to its ability to produce complex and customized parts with great precision, this technology not only improves the efficiency and durability of production processes but also reduces costs and waste.
Its application extends from aerospace and automotive to medicine and construction, where it opens up revolutionary prospects, particularly with bio-printing for creating functional tissues and organs. Additionally, the use of stainless steel and other advanced materials in 3D printing meets the demands of the most challenging environments, including space.
In summary, stainless steel 3D printing is a key technology for the future of manufacturing, promising to radically transform production and innovation methods in many fields.
Picture by Freepik.
The articles published on Imprimy.com are for informational purposes only. They are intended to provide general advice and information related to 3D printing. Imprimy.com cannot be held responsible for the results obtained or the consequences arising from the application of the shared information. We recommend always checking the specific instructions for your hardware and materials before use.