Are you wondering about 3D powder printing and how it works? At Imprimy.com, we are here to answer all your questions on this topic.
3D powder printing is an advanced additive technology that allows the manufacturing of complex-shaped parts with high precision, using metal, ceramic, or plastic powders, and offers great potential for innovation, durability, and industrial expansion.
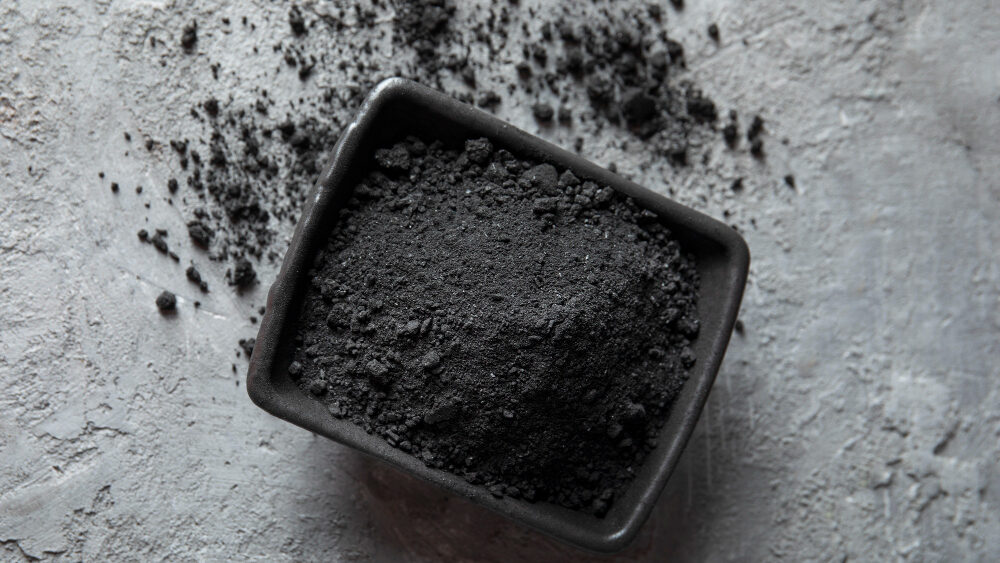
Qu’est-ce que l’impression 3D par poudre ?
3D powder printing is an additive manufacturing process that uses a fine powder (metallic, plastic, or ceramic) deposited in successive layers, then locally solidified by an energy source (such as a laser or electron beam) to create objects with complex shapes and high precision.
- Qu'est-ce que l'impression 3D par poudre ?
- What are the different existing 3D powder printing technologies?
- What materials are used in 3D powder printing?
- What are the advantages of 3D powder printing?
- What are the industrial applications of 3D powder printing?
- Future Perspectives of 3D Powder Printing
- Conclusion : Powder 3D Printing
Le processus de base de l’impression 3D poudre
3D powder printing follows a basic process that starts with the creation of a 3D model using CAD software. This model is then sliced into thin layers by slicing software.
The 3D printer deposits a thin layer of powder on the build platform. A laser or other heat source melts or fuses the powder according to the pattern of the current layer. This process repeats, layer by layer, until the object is fully formed.
Once printing is complete, the object is often subjected to thermal treatment to improve its mechanical properties. Finally, the excess powder is removed, and the object may undergo additional finishing such as sanding or painting.
Comparison with other 3D printing techniques
3D powder printing stands out from other 3D printing techniques in several key aspects.
Unlike Fused Deposition Modeling (FDM), which uses thermoplastic filaments, powder printing allows the creation of parts with often superior mechanical properties and better resolution.
Compared to Stereolithography (SLA), which uses liquid resins cured by laser, powder printing is generally better suited for materials like metals and certain technical polymers. Additionally, it enables the manufacturing of parts without requiring complex support structures, unlike SLA and FDM.
What are the different existing 3D powder printing technologies?
The main 3D powder printing technologies are SLM/DMLS, EBM, SLS, Binder Jetting, and MJF, each suited to specific materials and requirements in precision, strength, or production speed.
Laser Sintering
Laser sintering, also known as Selective Laser Sintering (SLS), is a 3D printing technique that uses a laser to fuse powder particles to create solid structures. The process begins by spreading a thin layer of powder on a build platform. The laser then traces the pattern of the object’s cross-section on this powder layer, sintering the particles together to form a solid layer.
The platform then lowers slightly, a new layer of powder is applied, and the process repeats until the object is fully built. SLS is especially valued for its ability to produce parts with robust mechanical properties and great design freedom, without requiring support structures. Commonly used materials include various polymers and metals.
Laser Fusion
Laser fusion, often called Selective Laser Melting (SLM) or Laser Powder Bed Fusion (LPBF), is an advanced 3D printing technique primarily used for metals. This process involves using a high-power laser to completely melt metal powder particles, creating fully dense and solid parts.
Unlike laser sintering, which only fuses particles at their melting point, laser fusion produces parts with mechanical properties comparable or even superior to those made by traditional methods. The process begins by spreading a thin layer of metal powder on a platform, followed by the selective melting of this powder according to the object’s cross-sectional pattern. The platform lowers, a new layer of powder is applied, and the process repeats until the part is fully built.
Binder Jetting
Binder Jetting is a 3D printing technique that uses a liquid binder to glue powder particles together, layer by layer, to create a solid object.
The process begins by spreading a thin layer of powder on a build platform. A binder is then selectively deposited on this powder layer using a print head, similar to an inkjet printer, to bind the particles according to the object’s cross-sectional pattern. Once a layer is completed, the platform lowers slightly, a new layer of powder is applied, and the process repeats.
After printing, the object is often subjected to thermal treatment or infiltrated with an additional material to improve its mechanical properties. Binder Jetting is valued for its ability to produce colored parts and to use a variety of materials, including metals, ceramics, and polymers. This technique is often used for applications requiring large parts or detailed models.
Other Emerging 3D Powder Printing Technologies
Emerging 3D powder printing technologies continue to evolve, offering new possibilities and improvements compared to traditional methods. Among these technologies are:
- Multi Jet Fusion (MJF): Developed by HP, this technology uses a fusion agent and a detailing agent to fuse powder particles, allowing faster production and parts with better mechanical properties.
- High-Speed Sintering (HSS): Similar to SLS, but uses an absorbing ink and a heat source to fuse powder particles, offering increased production speed.
- Selective Absorption Fusion (SAF): A technology that uses an absorbing agent to fuse powder particles with a heat source, enabling faster and more efficient production.
- Cold Spray: A technique where powder particles are accelerated at high speed to bond to a substrate, allowing the manufacture of metal parts without full melting, ideal for repairs and coatings.
- Electron Beam Melting (EBM): Uses an electron beam to melt metal powder in a vacuum environment, offering superior mechanical properties and better surface finish.
These emerging technologies aim to improve speed, precision, material properties, and the diversity of possible applications in 3D powder printing.
What materials are used in 3D powder printing?
The materials used in 3D powder printing mainly include metals, polymers, and ceramics, each selected for their mechanical, thermal, or biocompatible properties depending on the targeted industrial application.
The different types of powders used for 3D printing
The different types of powders used for 3D printing vary depending on the technologies and specific applications. Here are some of the main categories of powders:
- Polymers: Include materials like polyamide (PA12), polyamide 11 (PA11), and TPU (thermoplastic polyurethane). These powders are commonly used in technologies like SLS and Binder Jetting to produce flexible and durable parts.
- Metals: Include materials like stainless steel, titanium (Ti6Al4V), aluminum, and cobalt-chrome. These powders are used in technologies like SLM and EBM for applications requiring high strength and superior mechanical properties.
- Ceramics: Include materials like alumina and zirconia. These powders are used for applications requiring high heat and wear resistance.
- Composites: Combine polymer materials with fibers or particles to enhance mechanical properties. For example, polyamide powders reinforced with carbon fibers.
- Sands and molding materials: Mainly used in Binder Jetting to create molds and cores for casting.
- Reactive powders: Include materials that can undergo chemical reactions during the printing process to form specific compounds.
Material properties and specific applications used in 3D powder printing
The properties of materials used in 3D powder printing vary significantly depending on the type of powder and the technology employed. Here is an overview of the properties and specific applications for the main types of powders:
Properties | Applications | |
Polymers | Lightweight, flexible, corrosion-resistant, and good surface finish. | Rapid prototyping, functional parts for the automotive and aerospace industries, medical devices, and consumer products. |
Metals | High mechanical strength, heat resistance, thermal and electrical conductivity, and durability. | Components for the aerospace and automotive industries, medical implants, industrial tools, and machine parts. |
Ceramics | Heat resistance, wear resistance, and chemical stability. | Components for the electronics industry, parts for high-temperature environments, and biomedical applications. |
Composites | Improved mechanical properties such as stiffness and strength while maintaining light weight. | Structural parts for aerospace and automotive, sports equipment, and medical devices. |
Sands and Molding Materials | Good flowability, heat resistance, and ability to form fine details. | Molds and cores for casting, metal part prototypes, and architectural models. |
Reactive Powders | Ability to undergo chemical reactions to form specific compounds with unique properties. | Manufacturing of advanced materials for specific applications in electronics and chemistry. |
These properties allow engineers and designers to choose the most suitable material based on the specific requirements of their applications, whether it is strength, lightweight, heat resistance, or other critical characteristics.
What are the advantages of 3D powder printing?
The advantages of 3D powder printing include high precision and the ability to produce complex shapes impossible to achieve with traditional methods, reduced waste through optimized material use, design flexibility allowing customization, fast prototyping and production, as well as high mechanical strength suited for demanding industrial applications.
Precision and Fine Details
3D powder printing offers exceptional precision and fine details, allowing the creation of complex parts with great accuracy. This technology uses powder materials, such as metals or polymers, which are fused layer by layer to build three-dimensional objects.
Thanks to this method, it is possible to produce structures with fine details and intricate geometries that would be difficult or even impossible to achieve with traditional manufacturing techniques. 3D powder printing is especially valued in sectors like aerospace, medicine, and automotive, where precision and high-quality finishes are crucial.
The ability to create complex geometries
3D powder printing stands out for its ability to create complex geometries with high precision. This technology allows the manufacture of parts with complex shapes and fine details, which would be difficult or even impossible to achieve with traditional manufacturing methods.
By using powder materials, such as metals or polymers, 3D powder printing fuses these materials layer by layer to build three-dimensional objects. This approach is particularly advantageous in sectors like aerospace, medicine, and automotive, where the ability to produce complex geometries and detailed structures is essential to meet specific technical and functional requirements.
Strength and Durability of Parts Produced by 3D Powder Printing
3D powder printing is renowned for the strength and durability of the parts it produces. This technology allows the manufacture of components capable of withstanding high mechanical stresses and resisting wear, making them suitable for demanding applications across various industrial sectors. The materials used, such as metals and certain polymers, offer mechanical properties comparable or even superior to those of parts produced by traditional methods.
Thanks to a layer-by-layer fusion process, the resulting parts exhibit high density and structural integrity, contributing to their durability. These characteristics make 3D powder printing a preferred solution for industries like aerospace, automotive, and medicine, where the strength and longevity of components are essential.
Reduction of Material Waste through 3D Powder Printing
3D powder printing significantly contributes to the reduction of material waste in the manufacturing process.
Unlike traditional methods that often subtract material to create parts, 3D powder printing uses only the material needed to build the object layer by layer. This additive approach minimizes scrap and rejects, thus optimizing resource use.
Moreover, unused materials can often be recycled for subsequent prints, further reducing waste. This efficiency is particularly advantageous in industries where waste management and sustainability are priorities, such as aerospace and automotive.
What are the industrial applications of 3D powder printing?
The industrial applications of 3D powder printing cover various sectors such as aeronautics, automotive, medical, jewelry, space, and the energy industry.
Aerospace and Defense
3D powder printing plays a crucial role in the aerospace and defense sectors, offering significant advantages in terms of performance and innovation. In the aerospace industry, this technology enables the production of lightweight yet strong components, essential for improving aircraft efficiency and reducing fuel consumption.
For defense, it allows the rapid manufacturing of complex and customized parts to meet specific military equipment needs. The ability to create complex geometries and use high-performance materials makes 3D powder printing particularly suited to these demanding sectors, where precision, durability, and waste reduction are priorities.
Medical and Dental
3D powder printing has a significant impact in the medical and dental fields, offering innovative and customized solutions.
In the medical sector, this technology enables the creation of custom implants and prostheses precisely adapted to patients’ anatomy, thus improving comfort and treatment effectiveness.
In dentistry, it is used to produce crowns, bridges, and aligners with great precision, allowing perfect fit and better functionality. The ability to work with biocompatible materials and create complex geometries makes 3D powder printing a valuable tool for these applications, where customization and precision are essential for optimal results.
Automotive
3D powder printing plays a transformative role in the automotive sector, offering significant advantages in terms of innovation and efficiency. This technology enables the production of complex and lightweight parts, optimizing vehicle performance and reducing fuel consumption. Automotive manufacturers use 3D powder printing to quickly create prototypes, test new designs, and produce custom components that enhance aerodynamics and durability.
Moreover, the ability to produce parts with high precision and reduce material waste makes this technology particularly suited to the automotive industry, where resource optimization and customization are essential to meet market demands and environmental standards.
Jewelry and Art
3D powder printing opens new possibilities in the fields of jewelry and art, allowing creators to push the boundaries of their imagination.
In jewelry, this technology offers the ability to design unique and complex pieces with fine details and unmatched precision, while using precious materials like gold or silver.
For artists, 3D powder printing enables the creation of artworks with innovative shapes and textures that would be difficult to achieve with traditional techniques.
This flexibility and precision make 3D powder printing a valuable tool for craftspeople and artists seeking to explore new forms of expression and create customized and highly detailed pieces.
Other Industries
3D powder printing, also called powder bed fusion, plays an increasingly crucial role in various industries due to its ability to produce complex parts with high precision.
In aerospace, it enables the manufacturing of lightweight and durable components, optimizing device performance while reducing weight. The automotive industry uses it for prototype parts and limited series, accelerating development and vehicle customization.
In the medical field, this technology is essential for creating custom implants and biocompatible prostheses. It is also employed in jewelry and industrial design to create objects with complex shapes that are impossible to achieve with traditional methods.
Thanks to 3D powder printing, these sectors benefit from cost reduction, increased production flexibility, and shorter time-to-market.
Future Perspectives of 3D Powder Printing
The future perspectives of 3D powder printing include continuous improvements in materials and processes for better quality and strength, increased automation integrating artificial intelligence to optimize production, expansion into new markets such as space, biomedicine, and architecture, as well as a strong focus on sustainability with low-energy processes and improved powder recyclability.
Current Innovations and Research
Innovations and ongoing research in the field of 3D powder printing focus on improving materials, manufacturing processes, and the mechanical performance of produced parts.
Advanced work targets the development of new metallic, ceramic, and polymer powders, offering better thermal and mechanical properties, as well as greater recyclability.
At the same time, researchers optimize parameters of laser fusion and electron beam fusion to increase printing speed, precision, and surface quality. The integration of artificial intelligence and machine learning also enables finer process control and predictive maintenance of machines.
Finally, efforts are being made to make this technology more sustainable by reducing energy consumption and waste, while expanding its applications to sectors like space, advanced biomedicine, and microfabrication.
Growth Potential and Expansion into New Markets for Powder-Based 3D Printing
The growth potential and market expansion of powder-based 3D printing are significant, driven by increasing demand for customization, reduced production lead times, and energy efficiency.
Beyond established sectors like aerospace, automotive, and medical, this technology is opening up to emerging fields such as the space industry, where it enables the fabrication of parts resistant to extreme conditions, and architecture, allowing the creation of complex, customized structures. The fashion and luxury markets are also exploring this technique to produce innovative and exclusive accessories.
Moreover, growing adoption by SMEs and in developing countries strengthens this momentum, supported by cost reductions and the democratization of equipment. This potential is further fueled by the rise of new industrial applications, the growth of on-demand manufacturing platforms, and advancements in automation and digital integration, which ease entry into previously untapped markets.
Environmental Impact and Sustainability of Powder 3D Printing
The environmental impact and sustainability of powder 3D printing are generating growing interest, as this technology offers both ecological benefits and challenges to overcome. On the positive side, it enables a significant reduction in waste thanks to an additive process that uses only the necessary material, unlike subtractive methods.
Moreover, the recyclability of unused powders, especially metal powders, contributes to better resource management. It also promotes local and on-demand production, thereby reducing transport emissions and unnecessary inventory.
However, the carbon footprint can vary depending on the type of materials used, the energy consumption of equipment (notably high-power lasers), and the duration of manufacturing cycles. Research efforts are therefore focused on developing more sustainable powders, processes with lower energy consumption, and specific environmental standards to regulate its use.
Conclusion : Powder 3D Printing
In conclusion, powder 3D printing establishes itself as a disruptive technology with diverse and ever-evolving applications, meeting increasing demands for precision, customization, and performance. Its integration across various sectors such as aerospace, healthcare, luxury, and space exploration highlights its industrial potential and flexibility.
Driven by technological innovations and dynamic research, it paves the way for new markets while adapting to the imperatives of sustainability and reducing environmental impact. Despite remaining technical and energy-related challenges, powder 3D printing represents a promising solution for more agile, cost-effective, and sustainable production.
Picture by Freepik.
The articles published on Imprimy.com are for informational purposes only. They are intended to provide general advice and information related to 3D printing. Imprimy.com cannot be held responsible for the results obtained or the consequences arising from the application of the shared information. We recommend always checking the specific instructions for your hardware and materials before use.