Do you want to learn more about SLS 3D printing and its specificities? At Imprimy, we are here to answer all your specific questions about SLS 3D printing.
SLS 3D printing uses a laser for powder sintering to create 3D objects.
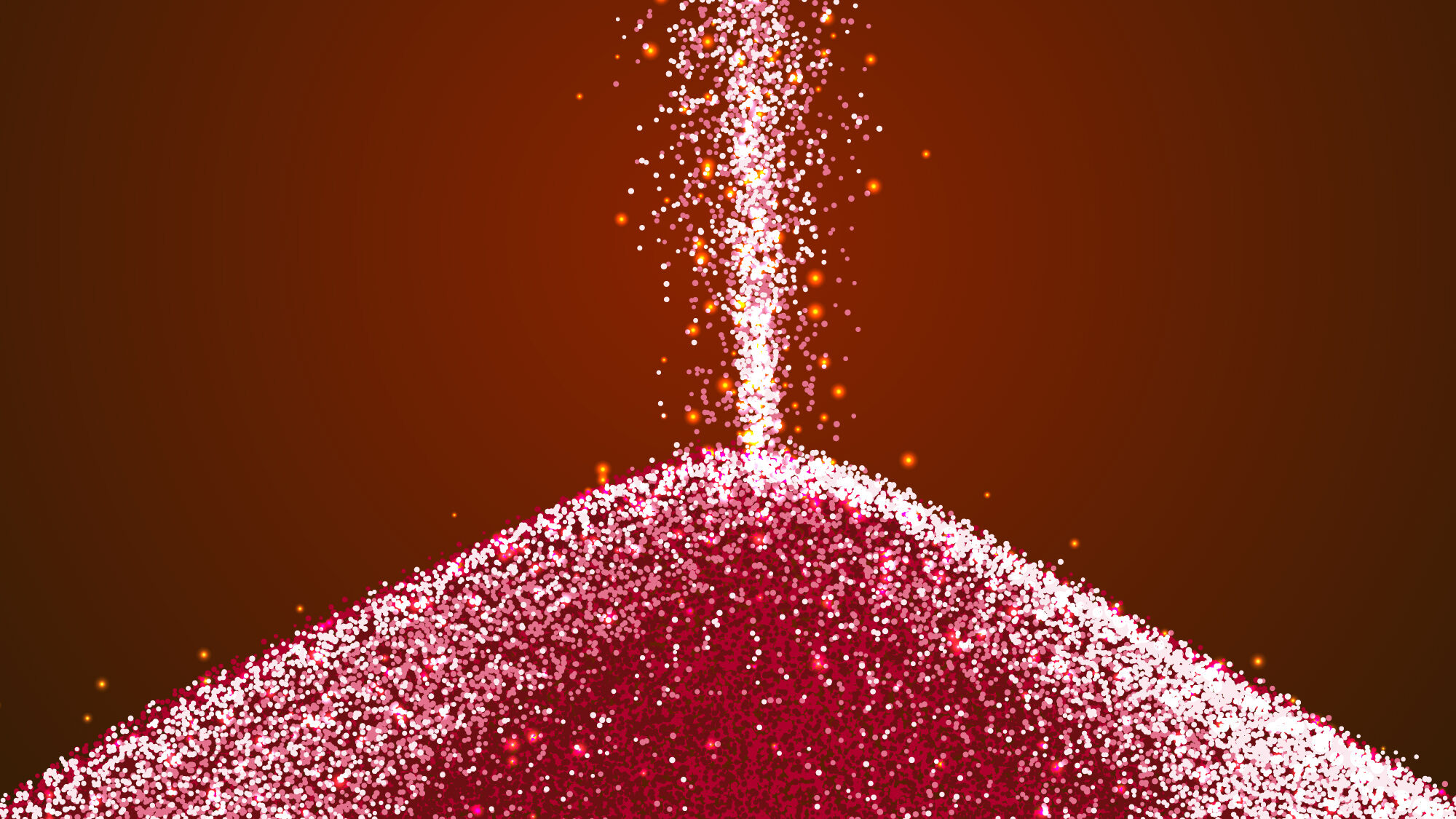
What is SLS 3D printing?
SLS 3D printing (Selective Laser Sintering) is an additive manufacturing technology that uses a laser to fuse powder particles (typically nylon or other polymers) to create 3D objects layer by layer.
Definition and Explanation of SLS Technology
SLS technology is an additive manufacturing process that uses a laser to fuse powder particles, typically made of plastic, metal, or ceramic, to create objects layer by layer.
This process begins with the spreading of a thin layer of powder onto a platform, followed by a laser scanning that fuses the particles according to a predefined digital model. Once a layer is completed, the platform lowers slightly, a new layer of powder is applied, and the process repeats until the object is fully formed.
SLS is particularly valued for its ability to produce complex and durable parts without requiring support structures, making it ideal for applications in the aerospace, medical, and automotive sectors.
Comparison with Other 3D Printing Technologies
SLS technology stands out from other 3D printing methods in several key aspects.
Unlike FDM (Fused Deposition Modeling), which uses melted filaments deposited layer by layer, SLS does not require support structures, allowing for the creation of more complex and detailed geometries.
Compared to stereolithography (SLA), which uses a liquid resin hardened by a laser, SLS can work with a wider variety of materials, including metals and high-performance polymers, thus offering more resistant and durable parts.
Additionally, unlike binder jetting, where a binder is used to solidify the powder, SLS produces parts with better mechanical properties due to the complete fusion of particles.
Finally, although SLS is generally more expensive and complex than other technologies like FDM, it offers superior design freedom and production quality, making it ideal for demanding industrial applications.
The History and Development of SLS Technology
SLS technology was developed in the late 1980s by Carl Deckard and Dr. Joe Beaman at the University of Texas at Austin. Their pioneering work led to a patent in 1989, marking the beginning of the use of lasers to fuse powder particles and create three-dimensional objects.
In the 1990s, the technology began to attract industry attention, and companies like DTM Corporation started to commercialize SLS machines.
In 2001, 3D Systems, a leading company in the field of 3D printing, acquired DTM Corporation, thereby strengthening the position of SLS in the additive manufacturing market.
Over the years, significant advances have been made in terms of usable materials, precision, and production speed, making SLS increasingly accessible and efficient for a variety of industrial applications.
Today, SLS is widely used in sectors such as aerospace, automotive, and medical, thanks to its ability to produce complex and durable parts.
How Does SLS 3D Printing Work?
SLS 3D printing works by scanning a laser over a powder surface to fuse the particles according to a 3D model, thereby creating successive layers that form the final object.
Detailed Description of SLS 3D Printing
SLS 3D printing is an additive manufacturing process that uses a laser to fuse powder particles and create three-dimensional objects. The process begins by spreading a thin layer of powder, usually made of plastic, metal, or ceramic, onto a build platform.
A laser then scans the surface of the powder, following a predefined digital model, and fuses the particles together to form a solid layer. Once a layer is complete, the platform lowers slightly, and a new layer of powder is applied.
This process repeats layer by layer until the object is fully formed. One of the main advantages of SLS is that it does not require support structures, allowing the creation of complex and detailed geometries that would be difficult—or even impossible—to achieve with other 3D printing methods.
Additionally, SLS can produce parts with excellent mechanical properties, making it ideal for applications in demanding sectors such as aerospace, automotive, and medical.
Role of the Laser in Powder Sintering
In the Selective Laser Sintering (SLS) process, the laser plays a central role by providing the energy needed to fuse powder particles and form solid objects.
The laser is precisely directed onto the surface of the powder according to a predefined digital model, allowing specific areas to be selectively sintered. When the laser hits the powder, it heats the particles to a temperature high enough to melt or soften them, causing them to fuse together.
This fusion process creates a solid layer corresponding to a cross-section of the final object. Once a layer is complete, a new layer of powder is applied, and the process repeats until the object is fully formed.
The precision and power of the laser are crucial for producing parts with high resolution and optimal mechanical properties.
Materials Used in SLS 3D Printing
SLS 3D printing uses a variety of powder-based materials, each offering specific properties tailored to different applications. The most commonly used materials include:
- Polymers: Polymers are the most widely used materials in SLS. Polyamide (PA), also known as nylon, is particularly popular due to its strength, durability, and flexibility. Other polymers like TPU (thermoplastic polyurethane) are used for applications requiring elasticity and abrasion resistance.
- Metals: Metal powders such as stainless steel, titanium, aluminum, and cobalt-chrome are used to produce strong and durable parts. These materials are often employed in the aerospace, automotive, and medical sectors.
- Ceramics: Though less common, ceramic powders can also be used in SLS to create parts with specific properties, such as heat resistance and chemical resistance.
- Composites: Composite materials, which combine polymers with carbon or glass fibers, are used to enhance the mechanical properties of parts, such as stiffness and tensile strength.
The choice of material depends on the specific requirements of the application, such as mechanical strength, flexibility, heat resistance, and durability.
The Different Stages of the SLS 3D Printing Process
The SLS 3D printing process involves several key steps to transform powder into a solid object. Here are the main stages of the process:
- 3D Model Preparation: The process begins with the creation of a 3D model of the object using CAD software (Computer-Aided Design). This model is then converted into a format compatible with the 3D printer, typically the STL (Standard Tessellation Language) format.
- Machine Preparation: The SLS machine is prepared by filling the build chamber with the chosen powder, usually polyamide (nylon), metal, or ceramic. The build platform is set to its initial height.
- Powder Spreading: A thin layer of powder is spread across the build platform using a roller or a blade. The layer thickness is typically on the order of tens of microns.
- Laser Sintering: A laser scans the powder surface according to the predefined digital model. The laser heats the powder particles to a temperature high enough to melt or soften them, causing them to fuse together and form a solid layer.
- Platform Lowering: Once a layer is completed, the build platform lowers slightly—typically by the thickness of one layer—and a new powder layer is spread. The laser sintering process is then repeated for this new layer.
- Process Repetition: The steps of powder spreading, laser sintering, and platform lowering are repeated layer by layer until the entire object is formed.
- Cooling: After printing, the object is left in the machine to cool slowly. This helps minimize internal stresses and prevent deformation.
- Cleaning and Finishing: The object is removed from the machine and cleaned to eliminate excess powder. Additional post-processing steps such as sanding, polishing, or painting may be applied to improve the appearance and mechanical properties of the object.
Each of these steps is crucial for producing a high-quality final object with the desired mechanical and aesthetic properties.
What are the advantages of SLS 3D printing?
The advantages of SLS 3D printing include the ability to produce complex parts without support structures, good material strength, and the possibility of using a wide range of polymers.
Design freedom and geometric complexity
Design freedom and geometric complexity are two of the main advantages of SLS 3D printing. This technology allows the creation of parts with complex shapes and internal structures that would be impossible to produce using traditional manufacturing methods.
Thanks to design freedom, designers can innovate without the usual constraints, while optimizing the performance and functionality of the parts.
The geometric complexity offered by SLS also helps reduce part weight while maintaining mechanical strength, which is especially beneficial in industries such as aerospace and medical.
Strength and durability of produced parts
The strength and durability of parts produced by Selective Laser Sintering (SLS) are key features that make this technology particularly attractive for various industrial applications.
Parts made by SLS are known for their high mechanical strength, comparable to parts produced by traditional manufacturing methods. This strength is due to the dense and homogeneous structure of the parts, which minimizes weak points.
Additionally, the durability of SLS parts is enhanced by their ability to withstand harsh environments, including high temperatures and chemically aggressive conditions.
The absence of support structures
The absence of support structures is one of the major advantages of SLS technology.
Unlike other 3D printing methods that require supports to hold overhanging parts during the manufacturing process, SLS does not need them. This is because parts are built within a bed of unfused powder, which acts as a natural support during printing.
This feature not only reduces production time and the amount of material used, but also simplifies post-processing, as there is no need to remove supports after printing.
This makes SLS particularly efficient for creating complex geometries and interlocking parts, while optimizing resource usage.
The possibility of mass production and mass customization
The possibility of mass production and mass customization are two major strengths of SLS technology. Thanks to its ability to produce parts without requiring specific tooling, SLS enables efficient and cost-effective series production, even for small batches.
At the same time, this technology facilitates mass customization, as it allows designs to be easily modified without significant additional costs. This means that each part can be tailored to the specific needs of a customer or application, while maintaining high production efficiency.
What are the different applications of SLS 3D printing?
The applications of SLS 3D printing include the manufacturing of medical prostheses, the production of aerospace parts, the creation of industrial prototypes, and the fabrication of automotive components.
SLS 3D printing in the aerospace sector
SLS 3D printing plays a crucial role in the aerospace sector by enabling the manufacturing of lightweight and complex components that meet the industry’s strict requirements. This technology is especially valued for its ability to produce strong and durable parts while reducing component weight, which is essential for improving the energy efficiency of aircraft.
Thanks to SLS 3D printing, aerospace companies can optimize supply chains, reduce production lead times, and minimize material waste compared to traditional manufacturing methods. Additionally, this technology offers great design freedom, facilitating the creation of customized and innovative parts that would be difficult or even impossible to make with conventional techniques.
Some companies have obtained certifications for structural components produced by SLS, marking a significant advance in adopting this technology for critical applications.
Significant investments are also being made in companies specializing in additive manufacturing for aerospace.
SLS 3D printing in the automotive industry
SLS 3D printing plays an increasingly important role in the automotive industry, offering innovative solutions for manufacturing complex and customized parts. This technology is especially valued for its ability to produce lightweight and durable components, essential for improving vehicle performance and efficiency.
Automakers use SLS printing to create functional prototypes and production parts, ranging from mechanical elements under the hood to interior components like air vents and seals.
Some companies use SLS printers to manufacture custom parts for concept car prototypes, thereby reducing production time and costs.
SLS printing also offers great design flexibility, facilitating the creation of unique and innovative parts tailored to specific customer requirements. This is particularly useful for vehicle customization, as seen in the adaptation of police vehicles with specific components.
Moreover, SLS 3D printing is used to produce replacement parts that are no longer available on the market, ensuring fidelity to the original technical and visual specifications.
Some companies have also adopted this technology to produce critical components, reducing both design and manufacturing lead times while minimizing waste.
SLS 3D printing in the medical field
Selective Laser Sintering (SLS) 3D printing is helping to transform the medical sector, offering innovative solutions for manufacturing personalized and complex medical devices. This technology is especially valued for its ability to produce prostheses, implants, and even organs from biocompatible materials, tailored to the specific needs of patients.
SLS printing enables the creation of complex biological structures, such as artificial corneas and organic tissues, paving the way for major advances in personalized medicine. It is also used to manufacture dental prostheses and other medical devices, providing increased precision and durability.
Moreover, SLS 3D printing is used to produce accurate anatomical models, allowing surgeons to plan and practice complex surgeries before performing them on patients. This not only improves surgical accuracy but also reduces risks and operation times.
SLS printing is also employed for creating personalized pills and capsules, enabling controlled drug release and the combination of multiple substances in a single compartment.
SLS 3D printing for consumer goods
SLS 3D printing plays an increasingly important role in the production of consumer goods, offering innovative solutions for manufacturing personalized and high-quality products. This technology is especially valued for its ability to produce strong, precise, and functional parts, suitable for a wide range of applications in the consumer goods sector.
SLS printing allows manufacturers to create custom products that meet the specific needs of consumers. For example, some companies use this technology to produce personalized glasses, where customers can virtually try on frames and choose from a range of color and design options before the glasses are 3D printed.
Moreover, SLS 3D printing is used for the creation of fashion products as well as in the beauty industry.
Other innovative applications of SLS 3D printing
Selective Laser Sintering (SLS) 3D printing finds innovative applications across various sectors, offering unique and personalized solutions. Here are some notable examples:
- Consumer Goods: In the consumer goods sector, SLS printing enables the creation of custom products such as glasses, clothing, and fashion accessories. This offers consumers unique products tailored to their specific needs.
- Food Industry: 3D food printing also uses SLS technology to create custom desserts and pastries. This allows chefs and food companies to offer innovative and personalized products that meet individual consumer preferences.
- Art and Design: Artists and designers use SLS printing to create complex artworks and innovative designs, including sculptures, jewelry, and decorative elements that benefit from the design freedom this technology offers.
- Education: In education, SLS printing is used to produce models and teaching tools that help students better understand complex concepts in science, engineering, and medicine.
These applications demonstrate how SLS 3D printing continues to transform various industries by offering innovative and personalized solutions.
What are the challenges and limitations of SLS 3D printing?
The challenges and limitations of SLS 3D printing include high costs of materials and machines, often rough surface finish, and restrictions on the size of produced parts.
Cost of machines and materials for SLS 3D printing
The cost of machines and materials for SLS 3D printing can vary significantly depending on factors such as machine size, manufacturing quality, and materials used. Here’s an overview of the associated costs:
Cost of SLS Machines
- Entry-level machines:
These SLS printers typically cost between €10,000 and €50,000. They are generally smaller with limited production capacity but suitable for small businesses or prototyping workshops. - Professional machines:
Industrial-grade SLS machines cost between €50,000 and €200,000. They offer better precision, larger build volume, and advanced features for producing high-quality parts. - High-end industrial machines:
These top-tier machines can exceed €200,000, designed for large-scale production with advanced capabilities, high capacity, and excellent precision.
Cost of SLS Materials
- Nylon powders:
The most common SLS material, nylon powders range from €50 to €150 per kilogram, depending on quality and supplier. Nylon is valued for its strength, durability, and flexibility. - Metal powders:
Used for applications requiring greater strength and durability, metal powders cost between €100 and €300 per kilogram. These are widely used in the aerospace, automotive, and medical industries. - Other materials:
Powders like carbon-fiber-reinforced or glass-fiber-reinforced polyamide range between €100 and €250 per kilogram. These offer improved mechanical properties for specialized applications.
Additional Costs
- Maintenance and consumables:
Costs for maintenance, spare parts, and consumables such as filters and nozzles add to the overall expenses. These are necessary to ensure machine reliability and longevity. - Training and technical support:
Operator training and technical support can also represent an additional expense, especially for complex industrial machines.
Surface finishing and post-processing
Surface finishing and post-processing are crucial steps in improving the appearance and mechanical properties of parts produced by SLS 3D printing. After printing, SLS parts often have a porous and rough surface, requiring additional treatments to meet the desired specifications.
Common techniques include:
- Polishing: Can be done manually or with machines to achieve a smooth surface.
- Sandblasting: Uses abrasive particles to remove powder residues and soften the surface texture.
- Infiltration: Often applied to reduce porosity and increase part density by filling the pores with resins or metals, which also improves strength and durability.
These processes enable the production of finished parts with optimized properties tailored for specific applications.
Limitations in size and precision
The limitations in size and precision of SLS 3D printing are important factors to consider during the design and manufacturing of parts.
- Precision limitations: While SLS offers good resolution, precision can be limited by factors such as powder particle size, laser power, and process parameters. Achieving fine details and tight tolerances can be challenging, often necessitating additional post-processing to meet the desired specifications.
- Size limitations: SLS machines typically have a limited build chamber, which restricts the maximum size of parts that can be produced in one piece. Larger parts often require printing in multiple sections followed by assembly, which increases complexity and cost.
Environmental and safety considerations
Environmental considerations and safety are essential aspects of the SLS 3D printing process.
- Environmental aspects: The use of polymer powders presents challenges related to waste management and recycling. Unused powder particles must be properly recycled or disposed of to prevent pollution. Additionally, energy consumption of SLS machines is often high due to the operating temperatures required.
- Safety aspects: Operators need protection from inhalation of fine powder particles, which can be harmful to health. Use of personal protective equipment (PPE) like masks and gloves, along with adequate ventilation systems, is necessary to minimize risks. Handling of lasers and high temperatures also requires strict safety protocols to prevent accidents.
These considerations are critical to ensure both environmental responsibility and operator safety in SLS 3D printing.
What are the future prospects for SLS 3D printing?
The future prospects for SLS 3D printing include improvements in speed and precision, the expansion of available materials, and greater integration into industrial manufacturing processes.
Innovations and ongoing research
The innovations and ongoing research in the field of SLS 3D printing in 2025 are marked by several significant advances. Research and development efforts focus on creating more durable and environmentally friendly materials, addressing criticisms about the environmental impact of this technology. Additionally, major innovations include the development of new materials and the improvement of printing techniques to meet the demands of faster and more efficient mass production.
Another notable advance is the introduction of the SLS 300 Powder Recycling Station (PRS), planned for 2025, which allows the automatic recycling of unused powder and mixes it with fresh material, thus optimizing resource use.
Furthermore, SLS 3D printing is increasingly integrated into various sectors, including medicine, where it is used to create anatomical models and innovative medical devices, and aerospace, where it enables the production of complex parts for space travel.
Finally, France positions itself as a leader in 3D printing, especially for the integration of electronic circuits directly into objects, thanks to increased research and development investments and government support.
Growth potential and new applications of SLS 3D printing
The growth potential and new applications of SLS 3D printing are vast and constantly expanding. In 2025, this technology continues to develop and integrate into various industrial sectors, offering innovative solutions and transforming manufacturing processes.
One of the main new applications of SLS 3D printing is in the field of medicine, where it is used to create anatomical models and custom medical devices, thereby improving training and research in areas such as vascular surgery and pulmonary diseases.
In the aerospace sector, SLS printing is used to produce a range of complex parts for space travel, demonstrating its ability to meet the strict requirements of this field.
SLS 3D printing also finds applications in the food industry, where it is used to create packaging and manufacturing chain components, as well as to explore the concept of 4D printing, which adds a temporal dimension to printed products, allowing shape and property changes in response to external stimuli.
Moreover, SLS 3D printing is increasingly adopted in sectors such as automotive and sports and leisure, where it enables the creation of lightweight and durable parts, thus optimizing performance and efficiency.
With increasing research and development investments and government support, France positions itself as a leader in 3D printing, notably for the integration of electronic circuits directly into objects, paving the way for new innovations and applications.
The impact of SLS 3D printing on manufacturing and mass production
SLS 3D printing has a significant impact on the manufacturing industry and mass production, transforming traditional processes and opening up new possibilities. This technology enables the creation of complex and customized parts without requiring expensive molds or tooling, thereby reducing production costs and manufacturing lead times.
One of the main advantages of SLS 3D printing is its ability to produce parts with great design freedom, allowing for geometries that would be impossible or very costly to achieve with traditional manufacturing methods. This includes the creation of complex internal structures and lightweight parts optimized for specific performance.
In terms of mass production, SLS printing offers a flexible and adaptable solution. Manufacturers can quickly switch from one design to another without having to reconfigure entire production lines, which is especially beneficial for small batch production or custom parts. Additionally, SLS printing enables efficient material use, as unused powder can often be recycled, reducing waste and raw material costs.
The integration of SLS 3D printing into production chains also allows for inventory reduction, as parts can be manufactured on demand, minimizing storage needs and overproduction risks.
Finally, SLS 3D printing fosters innovation across various sectors, including aerospace, automotive, and medicine, by enabling rapid prototyping and the production of final parts with optimized mechanical properties.
Conclusion: SLS 3D printing
SLS 3D printing represents a major breakthrough in the field of additive manufacturing, offering transformative possibilities for various industrial sectors. This technology enables the creation of complex and customized parts with great design freedom, without the need for expensive molds or tooling, significantly reducing production costs and manufacturing lead times.
One of the key strengths of SLS 3D printing is its ability to produce parts with geometries that would be difficult or even impossible to achieve using traditional manufacturing methods. This includes the creation of complex internal structures and lightweight parts, optimized for specific performance.
In terms of mass production, SLS printing offers a flexible and adaptable solution, allowing manufacturers to quickly switch from one design to another without reconfiguring entire production lines. This is particularly advantageous for small batch or custom part production. Moreover, this technology promotes efficient material use, as unused powder can often be recycled, reducing waste and raw material costs.
The integration of SLS 3D printing into production chains also enables inventory reduction, as parts can be manufactured on demand, minimizing storage needs and overproduction risks.
Finally, SLS 3D printing drives innovation across sectors such as aerospace, automotive, and medicine, by enabling rapid prototyping and the production of final parts with optimized mechanical properties. This technology continues to redefine manufacturing standards, offering faster, more flexible, and cost-effective solutions for mass production.
Thus, SLS 3D printing is a key technology for the future of manufacturing, delivering significant advantages in flexibility, efficiency, and innovation, and is set to play an increasingly central role in the global manufacturing industry.
Picture by Freepik.
The articles published on Imprimy.com are for informational purposes only. They are intended to provide general advice and information related to 3D printing. Imprimy.com cannot be held responsible for the results obtained or the consequences arising from the application of the shared information. We recommend always checking the specific instructions for your hardware and materials before use.