Would you like to learn more about how carbon 3D printing works? At Imprimy, we are here to explain everything to you.
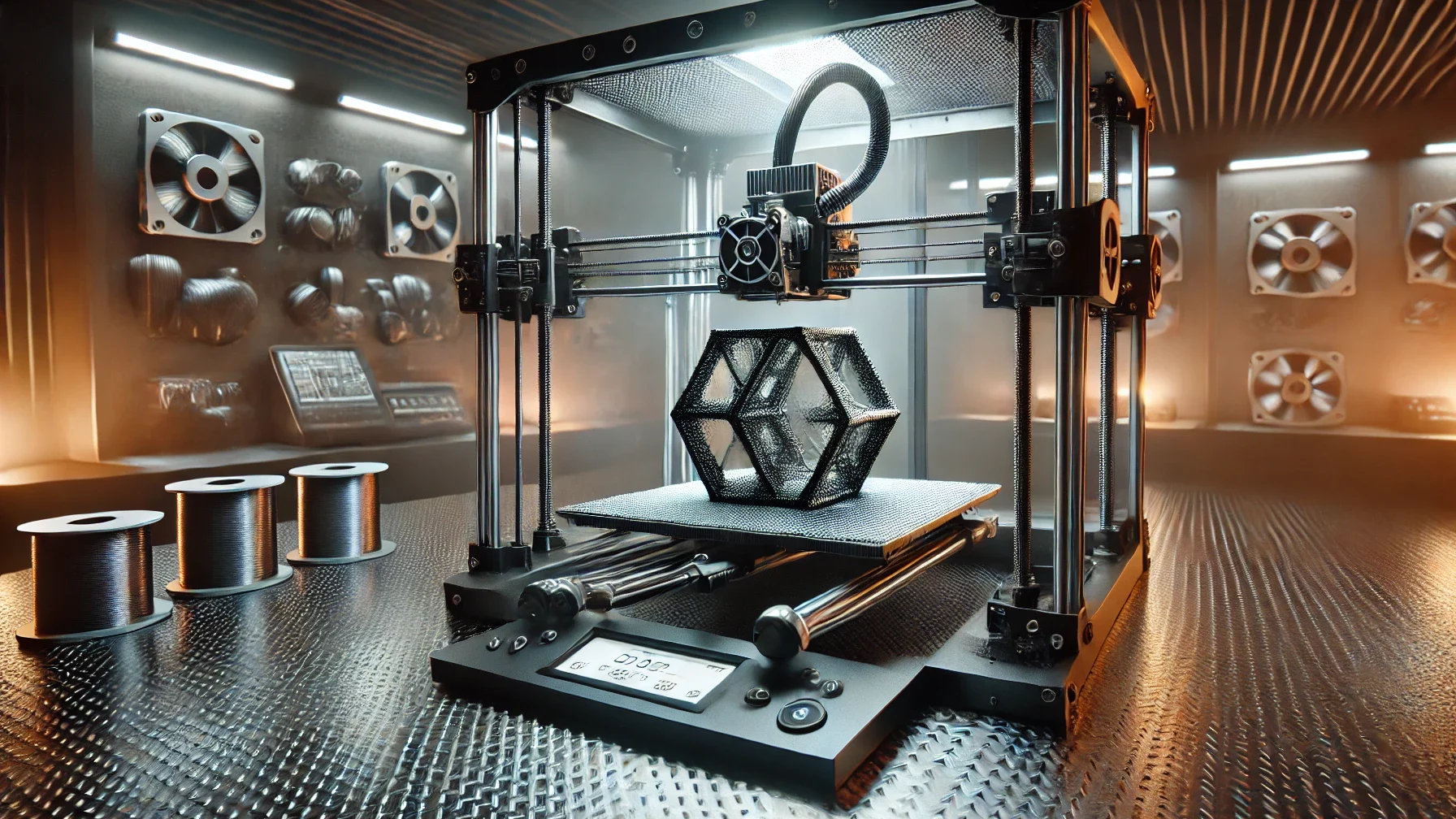
Qu’est-ce que l’impression 3D carbone ?
Carbon 3D printing allows for the printing of plastic filaments containing a certain proportion of carbon, making the resulting objects more resistant.
What is carbon 3D printing?
Carbon 3D printing refers to the additive manufacturing process that uses composite materials reinforced with carbon fibers, which are integrated into a plastic base. This technology enables the production of objects that are both lightweight and extremely strong, offering superior mechanical properties compared to traditional plastics.
Carbon 3D printing is particularly valued in demanding industries such as aerospace, automotive, and medical, where strength, lightness, and durability of parts are crucial. Thanks to these advanced materials, this manufacturing method allows for the creation of complex, high-precision parts while reducing the overall weight of products.
Materials Used in Carbon 3D Printing
Carbon 3D printing relies on composite materials that combine a plastic matrix with carbon fibers to enhance strength and durability. The most commonly used materials include:
- Nylon with carbon fiber: Offers high mechanical strength, wear resistance, and lightweight properties, making it ideal for engineering applications.
- Polycarbonate (PC) with carbon fiber: Provides excellent impact resistance and thermal stability, suitable for automotive and aerospace parts.
- PEEK (Polyether Ether Ketone) with carbon fiber: A high-performance material known for its superior heat resistance and chemical resistance, commonly used in the medical and aerospace industries.
- ABS with carbon fiber: A cost-effective option that improves stiffness and durability while maintaining ease of printing.
These materials allow for the creation of lightweight, high-strength components that outperform traditional plastics in demanding applications.
Differences Between Carbon 3D Printing and Traditional 3D Printing
Carbon 3D printing differs from traditional 3D printing in several key aspects, particularly in terms of materials, strength, and applications:
- Materials Used
- Traditional 3D printing primarily uses plastics such as PLA, ABS, or PETG.
- Carbon 3D printing incorporates carbon fibers into a plastic matrix (e.g., Nylon, PEEK, or Polycarbonate), significantly improving mechanical properties.
- Strength and Durability
- Standard 3D printed parts are generally less resistant to stress and wear.
- Carbon fiber-reinforced parts are lighter, stronger, and more durable, making them suitable for demanding engineering applications.
- Printing Process
- Traditional 3D printing mainly uses FDM (Fused Deposition Modeling) or SLA (Stereolithography).
- Carbon 3D printing often utilizes FDM with composite filaments or advanced continuous fiber reinforcement (CFR) techniques for enhanced performance.
- Applications
- Traditional 3D printing is commonly used for prototyping, hobby projects, and consumer products.
- Carbon 3D printing is favored in aerospace, automotive, and medical industries, where high-strength, lightweight, and durable parts are essential.
- Cost and Accessibility
- Traditional 3D printing is more affordable and widely accessible.
- Carbon 3D printing requires specialized materials and printers, making it more expensive but offering superior performance.
Overall, carbon 3D printing provides a significant advantage in strength-to-weight ratio and durability, making it ideal for high-performance engineering applications.
Advantages of Carbon 3D Printing
The main advantages of carbon 3D prints are that they are lightweight, durable, and also precise, which makes them particularly effective for applications related to specific sectors.
The lightness and strength of carbon 3D printing
Carbon 3D printing stands out for its ability to combine lightness and strength, two essential characteristics that make it a preferred choice in sectors such as aerospace, automotive, and medical. Thanks to the integration of carbon fibers into plastic filaments, the printed parts are significantly lighter than those made with traditional materials like ABS or PLA, while maintaining great strength.
The carbon fibers reinforce the structure of the objects, increasing their rigidity and resistance to tensile, compressive, and torsional forces. This dual advantage allows for the production of parts that can bear heavy loads while being lighter, which is particularly crucial in applications where every gram counts, such as in the manufacturing of parts for vehicles or aerospace equipment.
The durability of carbon 3D printing
The durability of carbon 3D printing is one of its main strengths, thanks to the properties of the carbon fibers integrated into the filaments. These fibers give the printed parts increased resistance to wear, shocks, and extreme conditions such as high temperatures, humidity, or corrosive environments.
Unlike traditional plastics, carbon-based composite materials are less likely to warp or degrade over time, allowing the printed objects to maintain their shape and mechanical properties in the long term. This durability makes carbon 3D printing particularly suited for industrial and professional applications where the longevity and performance of parts are crucial, such as in the aerospace, automotive, or medical sectors.
The precision and finishes of carbon 3D printing
The precision and finishes of carbon 3D printing are remarkably high thanks to the characteristics of the materials used and the advanced manufacturing technology. The carbon fibers enhance the dimensional stability of the parts, allowing for high-precision prints, even for complex and detailed objects. This precision results in parts with tight tolerances and accuracy in shaping.
Moreover, the finishes of the printed objects are often smoother and of better quality compared to traditional plastics, thanks to the additional rigidity of the composite filament. This allows for less rough surfaces, with a better aesthetic appearance and reduced need for post-processing.
The applications of carbon 3D printing in specific sectors
Carbon 3D printing finds applications in several specific sectors where its characteristics of lightness, strength, and durability are particularly sought after.
In the aerospace industry, it is used to manufacture engine parts, drone structures, and satellite components, where weight reduction is crucial without compromising strength.
In the automotive sector, it allows for the creation of lightweight and resistant vehicle parts, such as engine mounts, body components, or prototypes, contributing to improved vehicle performance while reducing fuel consumption.
In medicine, carbon 3D printing is used to create customized implants, prosthetics, and light yet robust medical devices, offering high precision and perfect adaptation to patients’ needs.
The sports sector also benefits from this technology for creating performance equipment, such as bicycles, tennis rackets, or protective gear, where every gram counts and wear resistance is essential.
Finally, in the fields of design and architecture, carbon 3D printing is used to create models, decorative objects, or light yet sturdy structures, combining aesthetic appeal and functionality.
What are the different applications of carbon 3D printing?
Carbon 3D prints prove to be particularly useful in many industries such as the automotive industry, aerospace, medicine, and even leisure.
Carbon 3D printing in the automotive industry
Carbon 3D printing in the automotive industry offers many possibilities to improve performance, reduce weight, and optimize the production of parts. Thanks to the lightness and strength of carbon fiber-based composite materials, this technology allows for the creation of stronger parts while reducing their weight, which improves the energy efficiency of vehicles and reduces fuel consumption.
Carbon 3D printing is particularly used to produce prototypes, engine parts, suspension components, body parts, and even custom interior accessories. By reducing the need for traditional tooling, this method also shortens production times and facilitates the manufacturing of complex parts at more competitive costs.
Additionally, carbon 3D printing allows for greater customization of parts while ensuring high precision and quality. This technology is especially beneficial in the production of performance vehicles, where every gram counts, but it also finds its place in the manufacturing of parts for electric vehicles, contributing to a more sustainable future.
Carbon 3D printing in aerospace
Carbon 3D printing plays an increasingly crucial role in the aerospace industry, where weight reduction and performance improvement are major challenges. Carbon fiber-based materials offer a unique combination of lightness, strength, and rigidity, making them ideal for manufacturing parts intended for extreme environments, such as aircraft engines, rocket structures, or satellite components.
In this sector, 3D printing allows for the production of complex and custom-made parts that are impossible to produce with traditional methods, while reducing the weight of the printed objects, contributing to better energy efficiency and reduced operational costs. This technology also helps reduce prototype production times and component manufacturing, accelerates the development of new technologies, and enhances the performance of aerospace systems.
Carbon 3D printing in medicine
Carbon 3D printing is finding increasingly important applications in the medical field thanks to its unique properties of lightness, strength, and durability. It allows for the manufacturing of custom-made parts, such as implants, prosthetics, and medical devices, offering advanced personalization and a perfect fit for the specific needs of patients.
For example, orthopedic implants and prosthetics printed in 3D with carbon fiber-reinforced materials are both light and robust, offering excellent resistance to shocks and wear while being comfortable to wear.
Additionally, carbon 3D printing enables the creation of complex structures, such as fixation grids or support devices, that would be difficult to produce with traditional methods. This technology also facilitates the manufacturing of precise, lightweight surgical tools tailored to specific procedures, reducing surgical time and improving treatment efficiency.
Finally, carbon 3D printing offers prospects in the field of regenerative medicine, with potential applications in creating supports for cell growth or even bio-printed structures for tissue repair.
Carbon 3D printing in sports and leisure
The sports and leisure sector benefits from carbon 3D printing, thanks to its ability to produce lightweight, strong, and high-performance equipment. The carbon fibers used in the filaments allow for the design of objects that combine great resistance to mechanical stresses while being light, which is crucial for many sports equipment. For example, in cycling, ultra-light and strong bike frames are manufactured using carbon 3D printing, providing enhanced performance and reduced fatigue for cyclists.
In the field of motor racing or motocross, carbon 3D printing allows for the production of lightweight vehicle parts, such as engine mounts, mirrors, or body components, thereby reducing the overall weight of the vehicles while ensuring their strength and safety. Protective gear, such as helmets, knee pads, or elbow pads, can also benefit from this technology to provide optimal protection while being lighter and more comfortable.
Carbon 3D printing also opens up new possibilities in the manufacturing of customized accessories and leisure objects, such as tennis rackets, golf clubs, or surfboards, allowing athletes and enthusiasts to benefit from equipment perfectly suited to their needs and performance.
Carbon 3D printing in design and architecture
Carbon 3D printing in design and architecture offers innovative possibilities for creating lightweight yet robust objects and structures.
Thanks to the combination of the properties of carbon fibers, this technology allows for the design of complex architectural elements, both aesthetic and functional, while reducing the weight and cost of materials. Architects and designers can create building models, facades, or decorative elements with exceptional levels of detail and precision, while optimizing the durability and strength of the structures.
Carbon 3D printing also allows for the design of custom parts for unique architectural projects, such as structural supports or modular elements, which are often impossible to achieve with traditional manufacturing methods. Furthermore, this technology promotes the reduction of waste and improves the efficiency of manufacturing processes, which is particularly advantageous in an industry increasingly focused on sustainable solutions.
Finally, in the field of object design, carbon 3D printing allows for the creation of furniture, lighting fixtures, and accessories with cutting-edge designs, while ensuring excellent stability and great lightness.
What are the challenges of carbon 3D printing?
The challenges of carbon 3D printing are related to the costs of materials, the wear of your machine, the specific equipment you need to acquire, and the specific difficulties associated with these 3D prints.
The cost of materials for carbon 3D printing
The cost of materials for carbon 3D printing is generally higher than that of traditional plastics due to the advanced properties of composite filaments. The filaments made from carbon fibers are often mixed with plastics like PLA, PETG, or nylon, and the carbon fibers add significant value in terms of strength, lightness, and durability. As a result, these materials are often more expensive than standard filaments, with prices varying significantly depending on the type of filament used.
Additionally, carbon 3D printing requires special printers, often equipped with hardened metal nozzles to withstand the abrasiveness of the fibers, which can lead to additional investment costs.
However, while the initial cost is higher, using carbon 3D printing can offer good value for money in sectors where the performance, lightness, and durability of parts are crucial. The benefits of these materials often justify the extra investment.
The wear of printers used for carbon 3D printing
The wear of printers used for carbon 3D printing is an important factor to consider, as carbon fiber-reinforced filaments are abrasive and can cause premature wear of the printer components.
While carbon fibers improve the strength and lightness of printed parts, they are extremely hard and can quickly wear out the standard stainless steel nozzles of 3D printers. This is why it is often recommended to use hardened metal nozzles, such as those made from tempered steel or tungsten-reinforced brass, which are more resistant to abrasion and capable of withstanding the demands of composite materials.
Additionally, the print heads, tubes, and other parts in contact with the materials may also experience faster wear, which may require frequent replacements to maintain print quality and avoid breakdowns. Although carbon 3D printing requires more rigorous maintenance and specific equipment, it allows for the production of high-performance and durable parts, justifying the investment in suitable printers and high-quality replacement parts.
Specialized equipment for carbon 3D printing
Specialized equipment for carbon 3D printing is designed to meet the specific demands of carbon fiber-reinforced composite materials. This equipment includes 3D printers with features that allow these abrasive materials to be processed and ensure high-quality prints.
- 3D printers with hardened metal nozzles: Since carbon filaments are abrasive, standard 3D printers with brass nozzles can wear out quickly. This is why hardened metal nozzles, such as those made of tempered stainless steel or tungsten, are necessary to prevent premature wear and ensure print accuracy.
- 3D printers with reinforced extruders: The extruders of 3D printers specialized in carbon printing are often reinforced to handle composite materials and withstand the abrasive properties of carbon fibers. Some printers use extrusion systems with enhanced motors and components to ensure a constant filament flow without blockages.
- High-temperature 3D printers: Carbon filaments often require higher extrusion temperatures to ensure proper material fusion. Specialized carbon 3D printers are equipped with high-performance heaters and thermostats to maintain a stable temperature, allowing for the printing of materials like carbon fiber-reinforced nylon.
- Heated platforms and advanced cooling systems: Carbon 3D printing often requires precise temperature management to avoid warping during the print. This is why specialized printers feature heated platforms and enhanced cooling systems to ensure good layer adhesion and prevent internal stresses that could affect the quality of the part.
- Advanced control and modeling software: To optimize the use of composite materials, some 3D printers come with specialized software that helps adjust print settings based on the specific characteristics of carbon materials, such as their flexibility and fiber orientation.
These specialized pieces of equipment fully leverage the properties of carbon and other composites, ensuring more precise, durable, and high-quality prints for industrial applications, such as in the aerospace, automotive, or medical industries.
The difficulties associated with carbon 3D printing
Carbon 3D printing presents several challenges, mainly due to the specific properties of carbon fiber-reinforced composite materials. Here are some common difficulties encountered when using these materials:
- Wear of equipment: Carbon fibers are extremely abrasive, which can cause rapid wear of standard 3D printer nozzles. This requires the use of hardened metal nozzles, such as tempered stainless steel or tungsten, to prevent damage to printer parts and ensure high-quality printing.
- Need for specialized equipment: Carbon 3D printing often requires specialized printers with reinforced components, such as suitable extruders and heating systems capable of reaching higher temperatures. These printers are generally more expensive and require a larger initial investment compared to standard printers.
- Adhesion and warping issues: Carbon materials tend to contract as they cool, which can cause warping, especially for larger parts. This requires the use of heated platforms and rigorous temperature management to ensure proper layer adhesion and avoid deformation problems.
- Need for optimized printing parameters: Printing with composite materials requires carefully adjusted printing settings, such as extrusion temperature, print speed, and cooling. This can make process optimization more complex, and poor settings can lead to defects in the printed part, such as poorly fused layers or surface imperfections.
- High cost of materials: Carbon filaments, especially those reinforced with carbon fibers, are more expensive than conventional materials like PLA or ABS. This price difference can be a barrier, particularly for large-scale projects, although the performance benefits can offset the initial investment.
- Complexity of design: Although carbon 3D printing allows for the creation of highly solid and lightweight parts, designs must be adapted to the material’s properties. The structures need to be optimized to avoid stresses or weak points that could compromise the strength or durability of the part once printed.
Despite these challenges, carbon 3D printing offers significant advantages in terms of performance, lightness, and durability, and continues to be an increasingly popular solution for high-end industrial applications.
How to get started with carbon 3D printing?
To get started with carbon 3D printing, you need to choose a suitable 3D printer, select the right filament, and properly calibrate your machine.
Choosing a 3D printer suitable for carbon 3D printing
Choosing a 3D printer suitable for carbon 3D printing is crucial to ensure the quality, durability, and performance of the printed parts. Here are some important criteria to consider when purchasing a printer for printing carbon fiber reinforced materials:
- Hardened metal nozzles: Carbon filaments are abrasive and can quickly wear out standard brass nozzles. Therefore, it’s essential to choose a printer equipped with hardened metal nozzles (such as tempered stainless steel or tungsten) capable of withstanding the wear caused by carbon fibers.
- Reinforced extruder: The extruders must be designed to handle robust composite materials. A quality extruder should provide a constant filament flow, even for abrasive materials, and resist wear while allowing smooth extrusion.
- Heated platforms: To avoid warping of printed parts, a heated platform is essential. The surface of the platform must be able to maintain a stable temperature throughout the print to ensure good layer adhesion, especially for composite materials like carbon fiber.
- High extrusion temperature: Carbon filaments require high extrusion temperatures, typically around 230-280°C, depending on the type of filament. It’s important to check that the printer has a high-performance heating system to reach and maintain these temperatures steadily.
- Cooling and ventilation systems: Carbon 3D printing requires precise temperature control, both for extrusion and cooling. Good thermal management ensures that the material solidifies correctly and prevents warping or defects.
- Closed print chamber: A closed print chamber helps maintain a stable temperature and reduces the risk of warping by better controlling the manufacturing environment. It’s especially useful for materials requiring precise heat management, such as carbon fiber reinforced composites.
- Compatibility with composite materials: It’s important to verify that the 3D printer is specifically compatible with carbon fiber reinforced filaments. Some printers are specially designed for printing these materials and may offer preconfigured settings to optimize prints.
- Reliability and durability: Carbon 3D printing tests the printer’s components, especially due to abrasive materials. Therefore, it’s important to choose a 3D printer known for its reliability and durability in demanding production environments.
- Price: 3D printers suitable for carbon 3D printing are more expensive than standard printers due to the reinforced components and advanced technologies. It’s essential to assess your budget and determine if the investment in high-quality equipment is justified by the intended use.
Selecting the right carbon 3D filament
Selecting the right carbon 3D filament is essential to ensure the success of your prints and achieve parts that meet your requirements in terms of performance, strength, and quality. Here are the main criteria to consider when choosing the best carbon 3D filament for your needs:
- Base filament type: Carbon fiber filaments are often combined with plastic materials such as PLA, PETG, nylon, or TPU. Each type of plastic has specific properties, so the choice of filament will depend on the intended application.
- PLA carbon: Easy to print, ideal for prototypes or decorative parts, but less durable than other materials.
- Nylon carbon: Excellent for strength, flexibility, and durability. Recommended for applications requiring robust and flexible parts.
- PETG carbon: A good balance between strength and ease of printing, with better resistance to high temperatures and impacts than PLA.
- TPU carbon: Flexible and strong, ideal for soft yet durable parts, such as seals or protective components.
- Carbon fiber fill percentage: Carbon-based filaments contain a variable percentage of carbon fibers, typically between 10% and 30%. A higher percentage of carbon fibers will make the filament more rigid and durable, but it will also be more abrasive and require a more robust printer. The choice of fiber percentage depends on the application:
- Filaments with 10-15% carbon fibers: Suitable for less demanding applications where lightweight and resistance to warping are essential, but without requiring extreme strength.
- Filaments with 20-30% carbon fibers: Recommended for highly resistant parts, such as mechanical components, functional prototypes, or parts requiring increased rigidity.
- Specific properties of carbon filaments:
- Heat resistance: Some carbon filaments are better suited for high temperatures, which is essential for applications in hot environments (e.g., engines, parts exposed to heat).
- Impact and wear resistance: Carbon-reinforced filaments are often chosen for their ability to resist wear and mechanical stress, making them suitable for industrial applications or parts subject to high forces.
- Lightweight: Carbon fibers provide rigidity while keeping the weight low, which is crucial for applications in sectors like aerospace, automotive, or sports.
- Printer compatibility: Ensure that your 3D printer is compatible with carbon fiber reinforced filaments. These materials are abrasive, so it’s recommended to use a printer equipped with hardened metal nozzles, a reinforced extruder, and a heated platform to avoid premature wear issues and ensure good layer adhesion.
- Ease of printing: Although carbon 3D printing is more technical than printing standard materials, some filaments are formulated to make their use easier. Check if the chosen filament has specific recommendations regarding extrusion temperature, printing speed, and cooling requirements. Some carbon filaments are designed to be easier to print and less sensitive to issues like warping or deformation.
- Aesthetic and finish: Carbon filaments can provide a textured look and a matte finish, which is appreciated for applications where the appearance of the part is important, such as prototypes or design parts.
- Cost: Carbon fiber reinforced filaments are generally more expensive than standard plastics. Be sure to assess your budget based on the specific needs of your projects. If you’re looking to reduce costs, you may also consider filaments with a lower percentage of carbon fibers.
Settings required for carbon 3D printing
The settings required for carbon 3D printing include several key aspects. First, it is crucial to choose the right carbon fiber-based filament, compatible with your printer.
Next, the extrusion temperature should be set correctly, typically between 200°C and 250°C, depending on the type of filament used. The print speed should also be adjusted to optimize accuracy and avoid premature wear of the printer.
Another important point is configuring the heated bed, usually between 50°C and 100°C, to improve material adhesion to the print surface. Finally, it is recommended to use hardened metal nozzles to avoid abrasion of the components due to the carbon fibers, ensuring better printer longevity.
Conclusion: Carbon 3D printing
In conclusion, carbon 3D printing offers significant advantages in terms of strength, durability, and lightweight design. However, to achieve high-quality results, it’s essential to select the right filament, configure your printer correctly, and use compatible components such as hardened metal nozzles and a heated bed.
While the technology comes with its challenges, such as the need for precise settings and robust equipment, the potential for creating high-performance parts makes it a valuable tool in industries like aerospace, automotive, and engineering. With proper care and attention, carbon 3D printing can deliver excellent results for demanding applications.