Do you have questions about 3D printers capable of printing zirconium? At Imprimy.com, we are here to answer all your questions.
3D printers using zirconium make it possible to create ceramic parts with great precision and excellent thermal resistance.
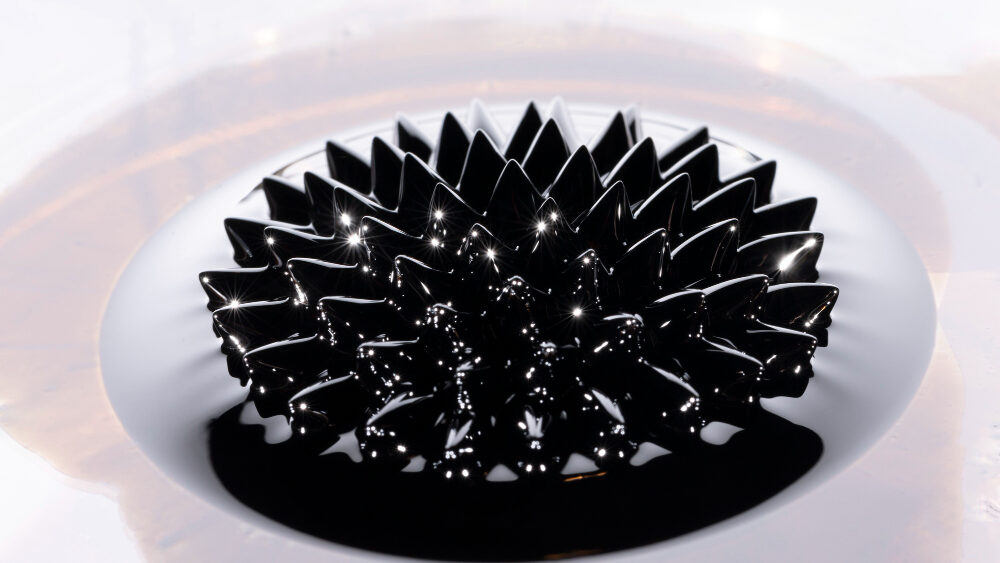
What is Zirconium?
Zirconium is a chemical element with the symbol Zr, primarily used for its corrosion resistance and in metal alloys.
The Physical and Chemical Properties of Zirconium
Zirconium is a transition metal known for its corrosion resistance, making it useful in chemically aggressive environments. It has a density of about 6.52 g/cm³ and a high melting point of approximately 1,855 °C, making it suitable for high-temperature applications.
Chemically, zirconium is resistant to most acids and bases, although it can react with certain concentrated acids like hydrofluoric acid. It also forms a protective oxide layer on its surface, which enhances its corrosion resistance.
Zirconium has relatively low thermal conductivity and moderate mechanical strength, but it is often alloyed with other metals to improve these properties.
The Advantages of Zirconium Compared to Other Materials
Zirconium offers several advantages over other materials, particularly due to its exceptional corrosion resistance, making it ideal for use in chemically aggressive environments such as in the chemical industry. It also has good high-temperature resistance, thanks to its high melting point, making it suitable for extreme conditions.
In addition, zirconium is lightweight compared to other corrosion-resistant metals like stainless steel, which can be beneficial in applications where weight is a critical factor. Its biocompatibility is another major asset, allowing it to be used in medical implants without causing undesirable reactions in the human body.
Finally, zirconium has a low neutron absorption cross-section, making it a material of choice for nuclear applications, especially in nuclear fuel cladding.
Common Applications of Zirconium in Various Industries
Zirconium is widely used across multiple industries due to its unique properties.
In the nuclear industry, it is primarily used for fuel cladding because of its low neutron absorption and corrosion resistance.
In the chemical sector, zirconium is valued for its resistance to acids and bases, making it ideal for chemical reactors and processing equipment.
In the medical field, its biocompatibility allows it to be used in surgical implants and prosthetics.
The aerospace industry also uses zirconium for components that require heat and corrosion resistance.
Finally, zirconium is used in the jewelry industry to create synthetic gemstones, such as cubic zirconia, which mimics the appearance of a diamond.
What 3D Prints Can Be Made with Zirconium?
With zirconium, you can produce 3D-printed ceramic parts for applications in the medical, aerospace, and industrial fields.
Challenges and Solutions Related to the Use of Zirconium in 3D Printing
Using zirconium in 3D printing presents several challenges, mainly due to its physical and chemical properties.
One major challenge is its high-temperature reactivity, which can lead to unwanted reactions with atmospheric gases, affecting print quality. To overcome this, controlled environments, such as vacuum chambers or inert gas atmospheres, are often used.
Another issue is zirconium’s relatively low thermal conductivity, which can result in temperature gradients and residual stresses in printed parts. This can be mitigated by optimizing process parameters such as scan speed and laser power to ensure even heat distribution.
Additionally, zirconium is prone to crack formation during the rapid solidification typical of 3D printing. The use of preheating strategies and post-process heat treatments can help reduce this problem.
Finally, the limited availability and high cost of pure zirconium can also pose challenges. Using zirconium alloys or composites offers a more cost-effective solution while retaining the desired properties.
Specific Techniques for 3D Printing with Zirconium
3D printing with zirconium requires specialized techniques to overcome the challenges associated with this material. Here are some commonly used methods:
- Controlled environments: Using vacuum chambers or inert gas atmospheres (like argon) is essential to prevent oxidation and other unwanted reactions at high temperatures.
- Process parameter optimization: Precise adjustment of laser power, scan speed, and scan strategy helps ensure uniform heat distribution and minimizes residual stresses.
- Preheating: Preheating the zirconium powder and the build platform helps reduce temperature gradients and the risk of cracking.
- Post-processing heat treatment: Applying thermal treatments after printing can relieve residual stress and improve the mechanical properties of printed parts.
- Use of alloys: Employing zirconium alloys can enhance printability and the final properties of parts while also reducing the cost of using pure zirconium.
- Real-time monitoring: Implementing real-time monitoring systems allows for tracking the printing process and detecting potential defects as they occur.
These techniques make it possible to leverage the unique properties of zirconium while mitigating the challenges of its 3D printing.
What Are the Advantages of Using Zirconium in 3D Printing?
The advantages of using zirconium in 3D printing include:
- High heat resistance: Ideal for high-temperature applications.
- Excellent durability: Provides long-lasting performance under harsh conditions.
- Good biocompatibility: Suitable for medical applications, such as implants and prosthetics.
These properties make zirconium a versatile and reliable material for advanced manufacturing.
Enhanced Strength and Durability of Zirconium
Zirconium is known for its enhanced strength and durability, making it a material of choice for various demanding applications.
Its exceptional corrosion resistance—thanks to the formation of a protective oxide layer on its surface—protects it from chemical and environmental attacks. This feature is especially valuable in aggressive environments, such as those in the chemical and nuclear industries.
In terms of mechanical strength, zirconium offers a good balance of toughness and ductility, although it is often alloyed with other metals to enhance these properties. Zirconium alloys are commonly used to increase tensile strength and hardness, while maintaining strong corrosion resistance.
Its durability is further supported by its ability to withstand high temperatures, making it suitable for high-temperature applications. Additionally, its biocompatibility and wear resistance make zirconium a long-lasting material for medical implants and prosthetics.
Finally, zirconium exhibits strong fatigue resistance, which is crucial for applications exposed to cyclic loading, such as in the aerospace industry.
Corrosion and High-Temperature Resistance
Zirconium is especially valued for its corrosion resistance and ability to withstand high temperatures, making it an ideal material for demanding environments.
Its corrosion resistance comes mainly from the formation of a zirconium oxide layer (ZrO₂) on its surface. This layer is highly stable and firmly bonded to the metal, acting as a protective barrier against chemical attacks. As a result, zirconium can resist corrosion in a wide range of aggressive environments, including acids, bases, and seawater. This property is particularly useful in the chemical industry, where zirconium is used in reactors and processing equipment.
Regarding high-temperature resistance, zirconium has a high melting point of around 1,855 °C, making it suitable for high-temperature applications. Its ability to maintain mechanical strength and dimensional stability at elevated temperatures makes it highly valuable in the aerospace and nuclear industries. In addition, zirconium’s low thermal conductivity can be advantageous in applications that require thermal insulation.
Potential Applications of 3D-Printed Zirconium
3D printing with zirconium paves the way for numerous potential applications across various industries, thanks to the unique properties of this material. Here are some of the most promising applications:
- Aerospace Industry: Zirconium can be used to manufacture lightweight and heat-resistant components, such as engine parts and spacecraft structures, due to its high-temperature resistance and low density.
- Nuclear Industry: 3D-printed zirconium can be used to create nuclear reactor components, such as fuel cladding, thanks to its low neutron absorption and corrosion resistance.
- Medical and Dental Fields: The biocompatibility of zirconium makes it an ideal material for medical and dental implants, such as hip prostheses and dental crowns, which can be customized to perfectly fit patients.
- Chemical Industry: Corrosion-resistant equipment, such as chemical reactors and heat exchangers, can be made from zirconium for use in chemically aggressive environments.
- Jewelry: Zirconium can be used to create customized and durable jewelry, including rings and bracelets, due to its wear resistance and ability to be polished to a shiny finish.
- Electronics: Electronic components requiring heat and corrosion resistance, such as sensor housings and connectors, can benefit from the use of 3D-printed zirconium.
- Automotive Industry: Engine parts and exhaust components can be made from zirconium to enhance durability and heat resistance.
What Are the Future Prospects of Zirconium in 3D Printing?
The future prospects of zirconium in 3D printing include significant advancements in personalized dentistry, with increased potential thanks to digital technology and 3D printing for custom dental restorations. There are also promising applications in the biomedical and aerospace sectors due to its exceptional mechanical properties.
Future Innovations in 3D Printing of Zirconium
Future innovations in 3D printing of zirconium are likely to further transform manufacturing capabilities across various industries. Here are some of the potential innovations to watch:
- Development of New Alloys: Research and development of zirconium-specific alloys for 3D printing could enhance mechanical properties, corrosion resistance, and printability, opening the door to new applications.
- Improvement of Processing Techniques: Advances in heat treatment and post-processing techniques could provide better control over the properties of 3D-printed zirconium parts, thereby improving their performance and durability.
- Optimization of Printing Parameters: The use of artificial intelligence (AI) and machine learning to optimize real-time printing parameters could improve the quality and precision of zirconium-printed parts.
- Use of Composites: The integration of composite materials with zirconium could combine its advantages with those of other materials, such as the lightness of polymers or the strength of ceramics.
- Multi-Material 3D Printing: The ability to print parts using multiple materials, including zirconium, could enable the creation of components with varied and optimized properties for specific applications.
- Enhanced Build Environments: The development of advanced build chambers, capable of better controlling atmosphere and temperature, could allow for zirconium parts to be printed with higher quality and accuracy.
- Recycling and Sustainability: Innovations in zirconium powder recycling and waste reduction could make 3D printing with zirconium more sustainable and economically viable.
These innovations could not only improve the current capabilities of zirconium 3D printing but also unlock new possibilities for its use in previously unexplored applications.
Ongoing Research and Technological Developments in 3D Printing of Zirconium
Ongoing research and technological developments in the field of 3D printing of zirconium are focused on several key aspects to improve and expand its applications. Here are some highlights:
- Improving Material Properties: Research is focused on adapting materials for 3D printing processes by developing new zirconium grades that meet targeted properties such as mechanical strength and durability.
- Additive Manufacturing Technologies: Advances are being made in additive manufacturing technologies for zirconium, particularly using processes like powder bed fusion and wire-based deposition. These technologies enable the creation of complex parts with high precision.
- Biomedical Applications: Zirconium is especially valued in the biomedical field for its biocompatibility and strength. Research is underway to develop 3D-printed implants and prosthetics made of zirconium, offering customized and long-lasting solutions for patients.
- Process Optimization: Efforts are also directed toward optimizing 3D printing processes for zirconium by improving the accuracy, speed, and quality of printed parts. This includes developing new post-processing techniques to enhance the final properties of components.
- Collaborations and Patents: Collaborations between research institutions and industries are essential for the development of new technologies and the acquisition of patents. These partnerships combine academic and industrial expertise to accelerate innovation in zirconium 3D printing.
These developments show that zirconium 3D printing is a dynamic and rapidly expanding field, with potential applications in multiple sectors, especially aerospace, biomedicine, and industry.
Market Growth Potential for 3D Printers Using Zirconium
The market for 3D printers using zirconium shows significant growth potential, driven by several key factors and emerging trends in the 3D printing industry. Here are some highlights:
- Growth of the Global 3D Printing Market: The global 3D printing market is rapidly expanding, with forecasts indicating substantial growth. For example, the market is expected to reach USD 63.46 billion by 2027, with a compound annual growth rate (CAGR) of 29.48%. This growth is supported by the increasing adoption of the technology across various sectors, including aerospace, automotive, healthcare, and more.
- Rising Adoption in Industrial Sectors: 3D printing is increasingly used for serial production of parts, especially in the medical, aerospace, and automotive industries. This trend creates major opportunities for advanced materials like zirconium, which is valued for its strength and biocompatibility.
- Technological Innovations: Advances in 3D printing processes, such as Selective Laser Sintering (SLS) and Electron Beam Melting (EBM), allow for more efficient use of materials like zirconium. These technologies improve the precision and quality of produced parts, enabling new applications.
- Investments and Government Support: Governments and public institutions play a key role in supporting the growth of the 3D printing market through grants and dedicated initiatives. This fosters innovation and the adoption of new technologies, including the use of advanced materials like zirconium.
- Material Diversification: The diversification of materials used in 3D printing—including ceramics and composites—creates new opportunities for zirconium use. 3D printers capable of handling a variety of materials are increasingly in demand, which could boost demand for zirconium-compatible printers.
- Regional Growth: Regions such as Latin America and China are experiencing high average annual growth rates in the 3D printing sector, which could further stimulate demand for zirconium-using printers in these expanding markets.
Conclusion: Zirconium 3D Printers
Zirconium 3D printers represent a significant advancement in the field of additive manufacturing, offering exceptional precision and durability capabilities.
Thanks to the use of zirconium, a material known for its corrosion resistance and biocompatibility, these printers are particularly well-suited for applications in the medical and aerospace sectors. They enable the creation of complex parts with high-quality surface finishes, making them ideal for the production of prosthetics and medical implants.
Moreover, their ability to operate at high temperatures sets them apart from other 3D printing technologies, further expanding their range of applications. As such, zirconium 3D printers are a valuable tool for industries that demand high performance and long-term reliability.
Picture by Freepik.
The articles published on Imprimy.com are for informational purposes only. They are intended to provide general advice and information related to 3D printing. Imprimy.com cannot be held responsible for the results obtained or the consequences arising from the application of the shared information. We recommend always checking the specific instructions for your hardware and materials before use.