Are you wondering about 3D printing with aluminum and its specificities? At Imprimy, we are here to answer all your questions related to 3D prints made with this metal.
Aluminum 3D printing allows you to quickly manufacture lightweight, strong, and complex parts with great precision. This type of 3D printing is ideal for certain sectors such as aerospace, automotive, and industry.
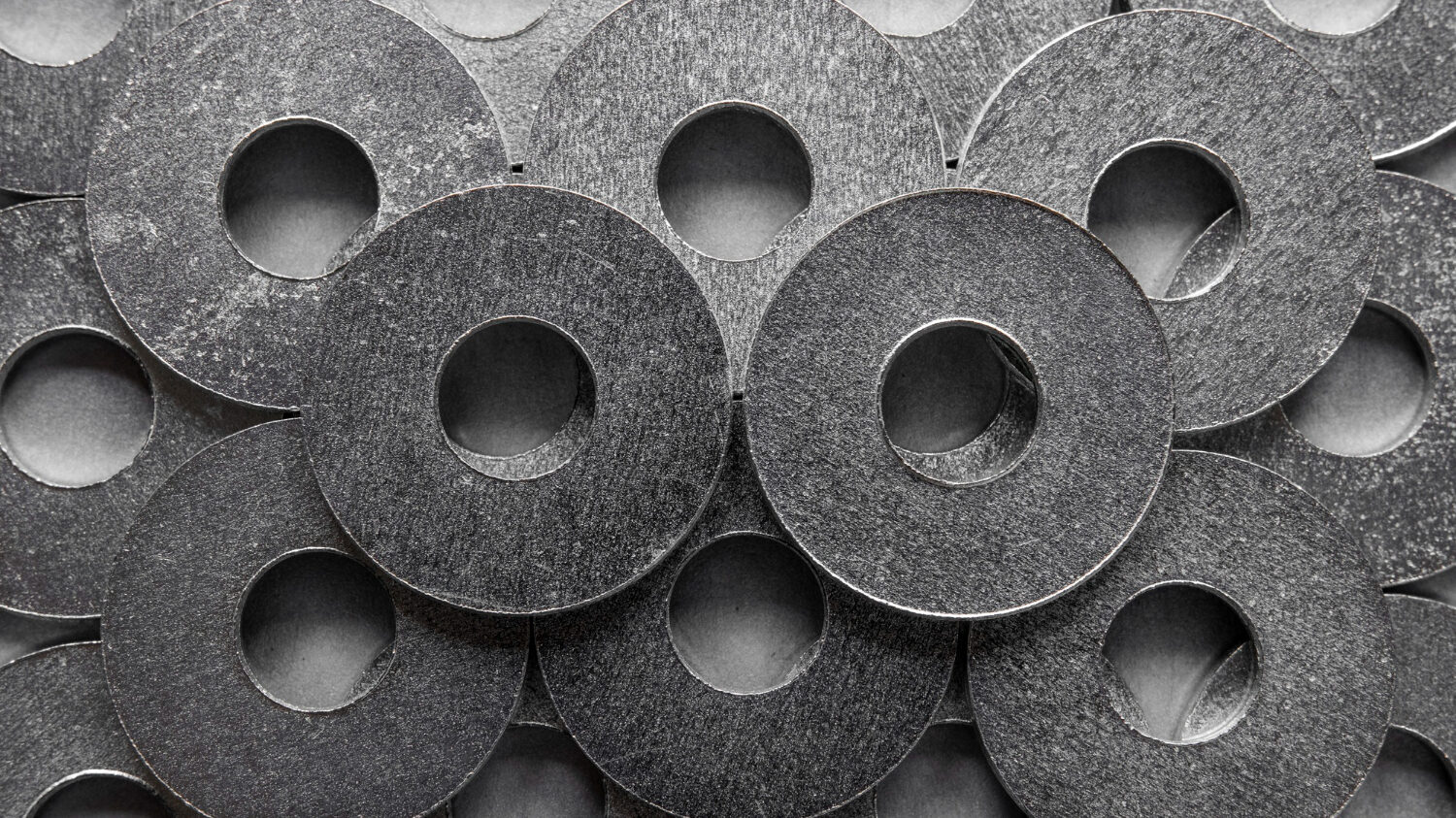
What is aluminum 3D printing?
Aluminum 3D printing is an additive manufacturing process that creates objects by layering aluminum powder fused together by a laser or an electron beam. This method allows the production of lightweight, strong, and customized parts with potentially complex shapes.
The definition of aluminum 3D printing
Aluminum 3D printing is an additive manufacturing process that uses aluminum powder to create three-dimensional objects layer by layer. This technology allows you to produce complex and customized parts with high precision, offering advantages such as reduced material waste and the ability to create structures that are both lightweight and strong.
Applications of aluminum 3D printing include aerospace, automotive, and the production of industrial prototypes, where durability and material performance are crucial.
Technologies used in aluminum 3D printing
The main technologies used in aluminum 3D printing include Selective Laser Melting (SLM) and Selective Laser Sintering (SLS). These methods involve the use of lasers to melt or sinter aluminum powder layer by layer, enabling the creation of complex and precise structures.
Another emerging technology is binder jetting, in which a binder is applied to the aluminum powder to solidify each layer before the final sintering process.
All these technologies allow you to produce parts with high mechanical properties, suitable for demanding applications in sectors such as aerospace and automotive.
Materials used in aluminum 3D printing
The materials used in aluminum 3D printing mainly include aluminum alloy powders, such as AlSi10Mg and AlSi7Mg, which are valued for their lightweight, corrosion resistance, and mechanical properties. These alloys are chosen for their ability to be precisely melted and solidified by lasers, enabling the creation of complex and durable parts.
These metal powders are finely calibrated to ensure optimal print quality and a smooth surface finish, which are essential for demanding applications and the production of industrial prototypes.
What are the advantages of aluminum 3D printing?
The main advantages of aluminum 3D printing include lightweight, excellent mechanical strength, the ability to create complex geometries, reduced material waste, time savings in prototyping and production, as well as easy customization of parts.
Customization and flexibility of aluminum 3D printing
Aluminum 3D printing offers exceptional customization and flexibility, allowing the creation of tailor-made parts suited to specific needs without the limitations of traditional manufacturing methods.
The ability to quickly adjust designs and produce unique parts or small batches enables you to meet the demands of rapid prototyping and on-demand production, providing high flexibility in sectors such as industry and medicine, where innovation and adaptability are crucial.
Cost reduction with aluminum 3D printing
Aluminum 3D printing enables significant cost reduction through several key advantages. It eliminates the need for expensive molds and special tooling, thereby lowering initial production costs.
In addition, this technology minimizes material waste, since only the required amount of aluminum powder is used, reducing raw material costs. The ability to produce complex parts in a single step also decreases labor and post-processing costs.
Finally, aluminum 3D printing allows for on-demand production, avoiding storage costs and overproduction, which is especially beneficial for small batches and prototypes.
Time savings with aluminum 3D printing
Aluminum 3D printing offers a considerable time savings by accelerating the manufacturing process. It allows you to go directly from digital design to production without going through intermediate steps like creating molds or tooling, thus reducing prototyping and time-to-market.
The ability to produce complex parts in a single operation eliminates the need for assembly and multiple manufacturing steps, shortening the production cycle.
Additionally, design adjustments can be made quickly and easily, enabling rapid iteration and immediate adaptation to project needs, which is especially advantageous in highly dynamic sectors.
Lightweight and strength of 3D printed aluminum
3D printed aluminum combines lightweight and strength, making it ideal for applications requiring high performance. The aluminum alloys used offer excellent corrosion resistance and robust mechanical properties, while being much lighter than other metals like steel. This lightness helps reduce the weight of components, improving energy efficiency and performance.
Moreover, 3D printing allows you to create optimized structures with complex geometries, further enhancing the strength and durability of the produced parts.
What are the industrial applications of aluminum 3D printing?
The industrial applications of aluminum 3D printing include the manufacturing of aeronautical parts, automotive components, industrial tooling, custom medical devices, as well as parts for aerospace and motorsports.
Aluminum 3D printing in aerospace
Aluminum 3D printing is revolutionizing the aerospace sector by enabling the creation of lightweight and strong components, essential for improving energy efficiency and aircraft performance. This technology allows you to produce complex and customized parts, such as fuselage structures, engine components, and support systems, with unmatched precision and flexibility.
By reducing the number of necessary parts and optimizing designs, aluminum 3D printing helps lower costs and production times, while improving the durability and reliability of components. The 3D printed aluminum alloys offer excellent corrosion resistance and mechanical properties suited to the strict requirements of the aerospace industry.
Automotive and aluminum 3D printing
In the automotive sector, aluminum 3D printing is transforming the design and manufacturing of components by offering lightweight, strong, and customized solutions. This technology allows the creation of complex parts such as engine components, chassis structures, and body elements with enhanced precision and flexibility. It also helps reduce vehicle weight and improve energy efficiency.
Aluminum 3D printing also speeds up the prototyping and production process, enabling rapid iterations and faster time-to-market. 3D printed aluminum alloys offer excellent corrosion resistance and robust mechanical properties, meeting the durability and performance requirements of the automotive industry.
Aluminum 3D printing in electronics
In the electronics sector, aluminum 3D printing offers significant advantages by enabling the creation of lightweight, durable, and customized components. You can use this technology to manufacture enclosures, heat sinks, and support structures with increased precision and flexibility, thereby enhancing the performance and durability of electronic devices.
Aluminum 3D printing also allows for the production of complex parts in small batches or custom-made, meeting the specific needs of prototypes and niche products. 3D printed aluminum alloys offer excellent thermal conductivity and mechanical properties suited to the demands of the electronics industry, contributing to product innovation and efficiency.
Aluminum 3D printing in the medical field
In the medical field, aluminum 3D printing opens up new possibilities for creating surgical instruments, implants, and custom medical devices. This technology enables the production of lightweight, strong, and precise components, tailored to the specific needs of patients and healthcare professionals.
Aluminum 3D printing facilitates the creation of custom prosthetics, complex surgical tools, and support structures for medical equipment, improving the quality of care and patient outcomes.
Certain 3D printed aluminum alloys can offer excellent biocompatibility and robust mechanical properties, meeting the strict requirements for sterilization and durability in the medical sector.
Aluminum 3D printing in association with other industries
Aluminum 3D printing is used across various industries, offering significant advantages in customization, flexibility, and performance.
In the manufacturing industry, it enables the creation of molds, jigs, and complex machine parts, reducing both costs and production times.
In the construction sector, aluminum 3D printing is used to fabricate lightweight and strong structures, such as facade elements and custom architectural components.
In the defense industry, it allows for the production of robust and precise parts for military equipment, improving durability and operational efficiency.
Finally, in the consumer goods sector, aluminum 3D printing makes it possible to create innovative, custom-made products that meet specific consumer needs.
3D printed aluminum alloys provide the mechanical properties and corrosion resistance required across these diverse sectors, driving innovation and efficiency.
What are the challenges and limitations of aluminum 3D printing?
The main challenges and limitations of aluminum 3D printing include the high cost of equipment and materials, the complex control of printing parameters, thermal stresses that can cause deformation, sometimes rough surface finishes, and strict regulatory approval requirements in certain industries.
A high initial investment to start aluminum 3D printing
Aluminum 3D printing requires a high initial investment due to the complexity and cost of specialized equipment, such as metal 3D printers, high-precision lasers, and advanced control systems. The materials, especially high-quality aluminum alloy powders, also represent a significant portion of the upfront costs.
Additionally, staff training and the acquisition of suitable design and production management software contribute to this investment.
Despite these initial costs, aluminum 3D printing offers many long-term advantages, including waste reduction, improved production efficiency, and the ability to create complex, custom parts — which can offset the investment through substantial savings and performance gains.
The technical complexity of aluminum 3D printing
Aluminum 3D printing involves notable technical complexity, requiring advanced expertise and specialized equipment. The process uses SLM (Selective Laser Melting) or SLS (Selective Laser Sintering), where high-precision lasers melt or sinter layers of aluminum powder to create three-dimensional structures.
Precise control of manufacturing parameters—such as laser power, deposition speed, and temperature—is critical to producing high-quality parts.
Additionally, post-processing steps like heat treatment, polishing, and quality inspections add further complexity and require specialized skills.
Mastering these technologies and processes demands thorough training and a well-adapted infrastructure, which poses a challenge for companies looking to adopt this technology.
The mechanical properties of 3D printed aluminum
3D-printed aluminum exhibits remarkable mechanical properties, making it ideal for demanding applications. The most commonly used alloys offer high tensile strength, exceptional hardness and resilience, while remaining lightweight. These properties enable the creation of strong and durable parts capable of withstanding heavy loads and resisting wear.
Additionally, 3D printing allows for the optimization of structures to enhance fatigue resistance and thermal stability, which is crucial in sectors like aerospace, automotive, and industrial manufacturing.
The ability to produce complex and custom geometries further enhances these mechanical properties, delivering superior performance compared to traditional manufacturing methods.
Post-processing of 3D printed aluminum parts
The post-processing of your 3D-printed aluminum parts is essential to enhance their mechanical properties and surface finish. These operations include:
- Heat treatment, which increases the hardness and strength of the parts by reducing internal stresses.
- Polishing and sandblasting, used to improve the surface quality, remove irregularities, and achieve a smooth finish.
- Precision machining, which adjusts the final dimensions and adds specific features such as threads or bores.
- Finally, treatments like anodizing or coating can be applied to improve corrosion resistance and durability.
These post-processing steps are crucial to ensure that your 3D-printed parts meet the performance and quality requirements of specific industries.
What is the future of aluminum 3D printing?
The future of aluminum 3D printing is moving toward faster printing speeds, lower costs, improved part quality, broader integration into industrial production chains, and the development of new alloys to meet advanced technical requirements.
Technological advancements in aluminum 3D printing
Technological advancements in aluminum 3D printing are rapid and promising, continually improving the precision, speed, and quality of the parts produced. Innovations in high-precision lasers enable finer and faster printing, while developments in artificial intelligence and machine learning optimize manufacturing parameters for more reliable results.
The integration of new materials and advanced alloys expands application possibilities, offering enhanced mechanical and thermal properties.
Moreover, progress in automation and robotics reduces manual intervention, increasing efficiency and process repeatability. Advanced design software enables simulation and optimization of complex structures, helping to lower costs and shorten development timelines.
New materials usable in 3D printing
New materials usable in 3D printing greatly expand the possibilities of aluminum-based additive manufacturing. These include advanced polymers with improved mechanical and thermal properties, exotic metals like titanium and superalloys for applications requiring extreme strength, and fiber-reinforced composites (with carbon or glass fibers) for increased lightness and robustness.
Technical ceramics, such as alumina and zirconia, are also being explored for their hardness and heat resistance.
Additionally, biomaterials and biodegradable materials are opening new paths in the medical field for implants and temporary devices.
These material innovations push the boundaries of 3D printing, providing custom solutions for diverse and demanding applications.
Growing adoption of aluminum 3D printing
The growing adoption of aluminum 3D printing is driven by its many advantages, including customization, cost reduction, shorter production times, and improved mechanical properties of the manufactured parts. Industries such as aerospace, automotive, medical, and industrial manufacturing are among the first to integrate this technology to create complex and lightweight components that meet high performance standards.
Continuous technological advancements, such as improved lasers, design software, and materials, are making aluminum 3D printing more accessible and efficient. This growing adoption is also supported by research and development initiatives, as well as partnerships between companies and academic institutions, which explore new applications and optimize manufacturing processes.
Conclusion: aluminum 3D printing
Aluminum 3D printing represents a major breakthrough in the field of additive manufacturing, combining lightweight, mechanical strength, and precision. Thanks to technologies like laser powder bed fusion, this method enables the production of complex parts that were previously impossible to design using traditional methods.
It is especially valued in the aerospace, automotive, and medical sectors, where performance and weight optimization are essential.
Picture by freepik.
The articles published on Imprimy.com are for informational purposes only. They are intended to provide general advice and information related to 3D printing. Imprimy.com cannot be held responsible for the results obtained or the consequences arising from the application of the shared information. We recommend always checking the specific instructions for your hardware and materials before use.