Are you interested in 3D printing and its application in the automotive industry? At Imprimy.com, we are here to answer all your questions.
3D printing is transforming the automotive industry by enabling the flexible, fast, and sustainable production of complex and customized parts, while reducing costs and waste, although challenges remain regarding regulations and initial costs.
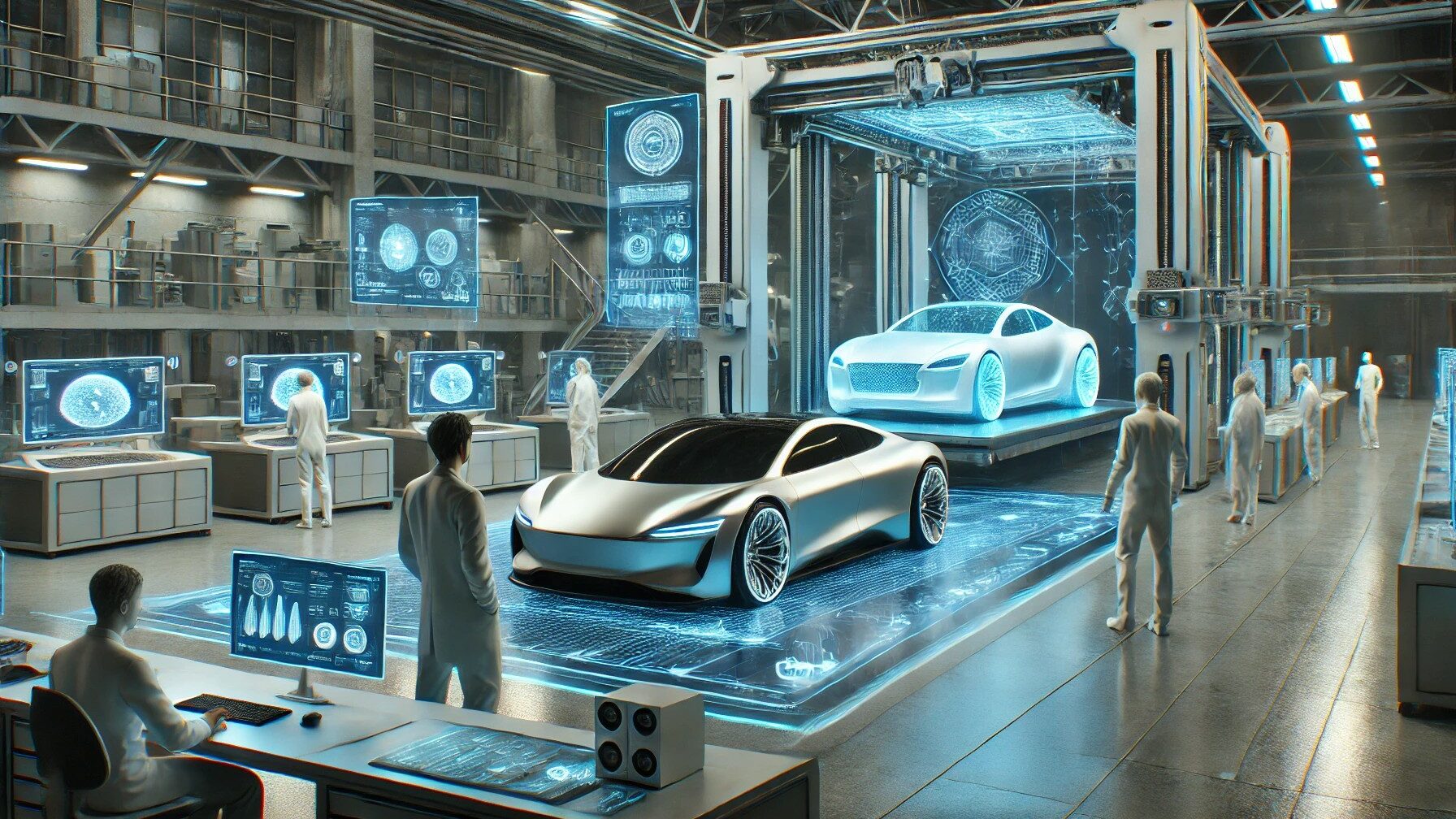
What is automotive 3D printing?
Automotive 3D printing is an additive manufacturing technology that creates vehicle parts and components by depositing materials layer by layer, providing greater flexibility and customization in production.
- What is automotive 3D printing?
- What are the advantages of 3D printing in the automotive industry?
- What are the practical applications of 3D printing in the automotive industry?
- What are the challenges and limitations of 3D printing in the automotive industry?
- What are the future prospects of 3D printing?
- Conclusion: 3D printing in the automotive industry
How 3D Printing Works
3D printing, also known as additive manufacturing, is a process of creating three-dimensional objects by adding material layer by layer. The process relies on a digital model, often designed using CAD software, which is then sliced into thin virtual layers.
The 3D printer deposits or solidifies the material, usually plastic, resin, or metal, according to the model’s instructions, thus building the object from the bottom up. This process allows for high precision and the ability to create complex shapes that would be difficult or impossible to achieve with traditional manufacturing methods.
The adoption of 3D printing in the automotive industry
The adoption of 3D printing in the automotive industry is rapidly expanding, offering significant benefits in terms of flexibility, innovation, and efficiency. Automakers are integrating this technology for rapid prototyping, enabling them to test and iterate designs faster than ever before.
Moreover, 3D printing facilitates the customization of vehicles, catering to specific customer demands without the constraints of traditional manufacturing methods. It also enables on-demand production of spare parts, reducing waiting times and storage costs.
Companies like BMW, Ford, and Volkswagen are heavily investing in this technology, not only for the production of plastic parts but also to explore the printing of metal components, paving the way for a revolution in the automotive supply chain.
What are the advantages of 3D printing in the automotive industry?
The advantages of 3D printing in the automotive industry include cost reduction through the elimination of expensive tooling and a decrease in material waste, customization of parts to meet specific customer needs, the speed of prototyping allowing for frequent iterations and accelerated testing, as well as improved durability through the use of recyclable materials and the optimization of structures for better energy efficiency.
Cost reduction through 3D printing in the automotive industry
Cost reduction through 3D printing in the automotive industry is one of the main advantages driving automakers to adopt this technology. By eliminating the need for expensive tooling and molds for parts production, 3D printing allows for significant savings, especially for small batches or customized parts. Additionally, it reduces material waste since only the necessary amount is used, unlike subtractive manufacturing methods.
3D printing also simplifies the supply chain by producing parts on demand, thus eliminating storage costs and waiting times. Finally, the ability to rapidly iterate designs and test prototypes without the high costs associated with tooling modifications also contributes to an overall reduction in development costs.
Customization of 3D printing for your car
3D printing customization for your car opens up new possibilities for vehicle owners looking to add a unique touch to their automobile. With this technology, you can create custom parts, such as steering wheel covers, mirror housings, or body elements, that reflect your personal style.
3D printing also allows for the restoration of obsolete or hard-to-find parts, providing a practical solution for classic or vintage cars. Additionally, it makes it easier to create custom prototypes to test new design ideas without the high costs associated with traditional production methods. This flexibility allows car enthusiasts to unleash their creativity and customize their vehicles in a unique and affordable way.
Durability of 3D printing in the automotive field
The durability of 3D printing in the automotive industry is a crucial aspect that contributes to the growing adoption of this technology. 3D printing helps reduce material waste by using only the necessary amount to produce a part, unlike traditional manufacturing methods, which often generate significant waste.
Moreover, it promotes the use of recyclable and biodegradable materials, such as certain plastics and resins, thus reducing the carbon footprint. The ability to produce parts on demand eliminates the need for excess inventory, reducing the energy costs associated with storage and stock management.
Finally, 3D printing helps extend the lifespan of vehicles by facilitating the production of spare parts, even for older models, reducing the need to replace the entire vehicle. These environmental benefits make 3D printing a sustainable and promising solution for the automotive industry.
What are the practical applications of 3D printing in the automotive industry?
The practical applications of 3D printing in the automotive industry include rapid prototyping to test and validate designs before mass production, the production of complex and lightweight final parts, repair and maintenance through on-demand production of spare parts, as well as the customization of components to meet specific customer needs, thus improving the performance and durability of vehicles.
Rapid prototyping for 3D printing in the automotive industry
Prototyping in 3D printing for the automotive industry is a key application that allows manufacturers to quickly test and validate new designs before moving to mass production. With this technology, engineers can create physical models of parts or components in just a few hours, significantly accelerating the development process.
3D printing enables frequent iterations and modifications without the high costs associated with traditional tooling. This fosters innovation and creativity, as designers can experiment with different shapes and structures without major constraints.
Additionally, 3D printed prototypes provide an accurate representation of final parts, allowing for functional testing and adjustments before mass production. This approach reduces the risk of costly errors and enhances the overall efficiency of the vehicle development cycle.
Production of final parts for automobiles using 3D printing
The production of final parts for automobiles using 3D printing is a major advancement that is transforming the traditional production line. This technology allows for the manufacturing of complex and lightweight parts, optimized for specific performances, which is particularly advantageous for components requiring high precision or unique shapes.
3D printing also enables the reduction of the number of components by consolidating several parts into one, thus simplifying assembly and improving reliability. The materials used, such as high-performance polymers and metals, offer durability and strength comparable to, or even superior to, traditionally manufactured parts.
Moreover, the ability to produce parts on demand reduces production lead times and storage costs, while providing increased flexibility to quickly meet market needs or specific customer requirements. This innovative approach contributes to a more agile and sustainable production process in the automotive industry.
Repair and maintenance through 3D printed spare parts
Repair and maintenance of vehicles are greatly facilitated by the production of 3D printed spare parts. This technology allows for the rapid on-demand production of parts, reducing repair times, especially for older or rare models whose parts are no longer available on the market.
3D printing also enables the customization of spare parts to meet specific needs, thus improving the performance and durability of vehicles. Repair shops can store digital files instead of physical parts, reducing storage costs and allowing for more efficient inventory management.
Moreover, the ability to produce spare parts locally reduces transportation costs and the carbon footprint associated with the supply chain. This flexibility and responsiveness make 3D printing particularly valuable for maintenance operations, helping to extend the lifespan of vehicles and enhance their reliability.
What are the challenges and limitations of 3D printing in the automotive industry?
The main challenges and limitations of 3D printing in the automotive industry are the slow production speed, the high cost of materials, the lower mechanical strength compared to traditional methods, and the size constraints of the printed parts.
The quality and reliability of 3D printed parts
The quality and reliability of 3D printed parts are major concerns in the automotive industry, where safety and performance are paramount. Technological advancements have significantly improved the precision and strength of parts produced through 3D printing. Materials used, such as high-performance polymers and metal alloys, are rigorously tested to meet industry standards. Additive manufacturing processes allow precise control over the internal structure of parts, optimizing their strength and durability.
However, challenges remain, particularly concerning the repeatability and consistency of material properties between production batches. To overcome these obstacles, strict quality control procedures are implemented, including fatigue, strength, and environmental compatibility tests.
Moreover, collaboration between automotive manufacturers and 3D printing technology suppliers contributes to the continuous improvement of processes and innovation in materials, ensuring that 3D printed parts meet the high standards of the automotive industry.
Regulations and safety standards of 3D printing
Regulations and safety standards for 3D printing in the automotive industry are essential to ensure the reliability and safety of the parts produced. 3D printed parts must comply with the same strict standards as those manufactured through traditional methods, particularly regarding strength, durability, and performance.
Regulatory bodies establish strict guidelines for automotive components. Automakers and 3D printing technology suppliers collaborate to develop testing protocols specific to the materials and processes used in 3D printing. These protocols include fatigue tests, impact resistance, and environmental compatibility testing.
Additionally, specific certifications may be required for materials and 3D printing processes, ensuring their compliance with industry standards. The rapid evolution of technology requires continuous updates to regulations to adapt to new discoveries and innovations in the field of 3D printing, ensuring that the produced parts meet the highest safety requirements.
High initial cost of industrial 3D printers
The high initial cost of industrial 3D printers represents a major challenge for their widespread adoption in the automotive industry. These high-precision machines require a significant investment, not only in terms of purchase but also for installation and maintenance.
Industrial 3D printers are equipped with advanced technologies that allow them to work with a variety of materials, including metals and high-performance polymers, which contribute to their high cost. Additionally, training personnel to operate and maintain these machines optimally represents an additional investment.
However, despite these initial costs, the long-term benefits, such as waste reduction, production flexibility, and the ability to create complex and customized parts, can offset this initial investment. Therefore, companies must carefully assess the potential return on investment and consider the long-term savings before committing to the acquisition of industrial 3D printers.
What are the future prospects of 3D printing?
The future prospects of 3D printing in the automobile industry include increased vehicle customization, reduced production costs, faster manufacturing of prototypes and spare parts, as well as a growing use of lighter and more durable materials.
Technological innovations in 3D printing
Technological innovations in the field of 3D printing continue to transform the automotive industry, opening up new possibilities for the design and manufacturing of vehicles.
Notable advancements include the development of new materials, such as high-performance polymers and metal alloys, which offer increased strength and durability. Multi-material manufacturing techniques now allow the combination of different types of materials within a single part, enhancing its mechanical and functional properties.
Moreover, large-scale 3D printers enable the production of larger components, expanding potential applications in the automotive sector. Advances in computer-aided design (CAD) software and topological optimization make it easier to create lightweight, optimized structures, reducing the weight of vehicles and improving their energy efficiency.
Finally, the integration of sensors and Internet of Things (IoT) technologies in 3D printed parts allows real-time monitoring of their performance, contributing to predictive maintenance and the continuous improvement of manufacturing processes. These innovations position 3D printing as a key technology for the future of the automotive industry, promoting more agile, sustainable, and customized production.
The impact on the automotive industry
The impact of 3D printing on the automotive industry is profound and multidimensional, transforming various aspects of design, manufacturing, and the supply chain.
First, 3D printing enables greater flexibility in production, facilitating the creation of customized and complex parts that would be difficult or expensive to achieve with traditional methods. This ability to produce parts on demand reduces production time and storage costs, contributing to more efficient inventory management.
Furthermore, 3D printing fosters innovation by allowing for rapid iterations of prototypes, accelerating the development of new vehicles and technologies. It also supports sustainability initiatives by reducing material waste and enabling the use of recyclable materials. Integrating 3D printing into the automotive production chain can also reduce long-term costs, despite the high initial investment, by optimizing processes and reducing tooling needs.
Finally, 3D printing paves the way for decentralized production, enabling the local manufacturing of parts and thereby reducing transportation costs and carbon footprint. These cumulative impacts position 3D printing as a catalyst for transformation in the automotive industry, paving the way for more agile, sustainable, and innovative production.
Emerging trends in 3D printing in the automotive industry
Emerging trends in 3D printing in the automotive industry are opening new perspectives for innovation and efficiency. Among these trends, 3D printing of metals is gaining popularity, enabling the production of robust and durable structural parts, essential for critical vehicle components.
Hybrid manufacturing, which combines 3D printing with traditional manufacturing techniques, offers increased flexibility and optimizes production processes. Additionally, large-scale 3D printing allows for the production of larger components, such as body panels or internal structures, thus expanding potential applications.
The integration of smart sensors in 3D printed parts facilitates real-time monitoring and predictive maintenance, enhancing the reliability of vehicles. Furthermore, advanced composite materials and biomaterials are being explored for their lightweight and durable properties, contributing to more energy-efficient vehicles.
Finally, automation and artificial intelligence are playing an increasing role in optimizing 3D printing processes, enabling more efficient designs and faster production. These trends demonstrate that 3D printing is set to become a cornerstone of innovation in the automotive industry, promoting smarter, sustainable, and customized production.
Conclusion: 3D printing in the automotive industry
The adoption of 3D printing in the automotive industry has revolutionized how vehicles are designed, manufactured, and maintained. With the ability to create customized parts, reduce production costs, and accelerate prototyping, this technology offers significant advantages over traditional manufacturing methods.
By enabling the production of complex and lightweight components, 3D printing allows for greater innovation and flexibility, while also supporting sustainability efforts through material reduction and the use of recyclable materials. Furthermore, it facilitates local production and on-demand manufacturing, reducing transportation costs and the carbon footprint.
As technology continues to advance, new trends such as metal printing, hybrid manufacturing, and the integration of smart sensors will further enhance the potential of 3D printing in the automotive sector. The future holds great promise for more efficient, personalized, and sustainable vehicle production, positioning 3D printing as a key enabler of innovation in the automotive industry.
Image generated by DALL·E, an artificial intelligence model developed by OpenAI.
The articles published on Imprimy.com are for informational purposes only. They are intended to provide general advice and information related to 3D printing. Imprimy.com cannot be held responsible for the results obtained or the consequences arising from the application of the shared information. We recommend always checking the specific instructions for your hardware and materials before use.