Do you want to 3D print tools but don’t know where to start or what the implications are? At Imprimy, we’re here to answer all your questions.
3D printing tools allows you to create custom, lightweight, and durable utility objects quickly and at low cost.
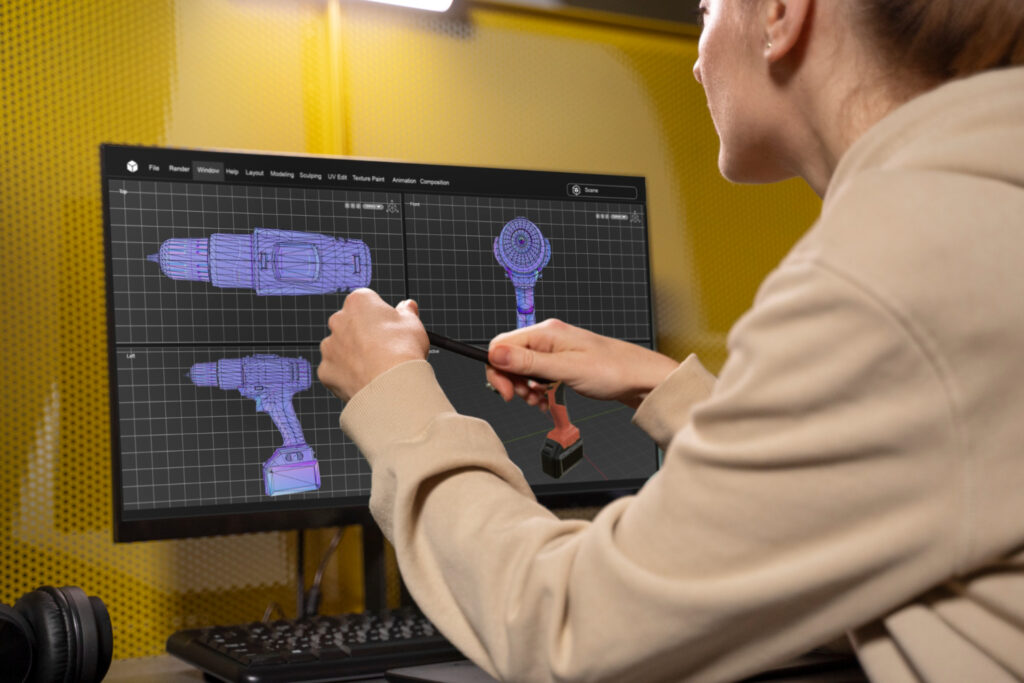
What are the advantages of 3D printing tools?
The advantages of 3D printing tools include:
- Use of advanced materials for greater durability
- Customization of designs
- Reduced production costs
- Faster manufacturing
Customization of 3D-printed tools
The customization of 3D-printed tools allows the creation of tailored solutions adapted to specific needs, offering unmatched flexibility compared to traditional manufacturing methods. This ability to adapt each tool to the precise requirements of a task or user improves efficiency and performance, while reducing costs associated with the mass production of standardized tools.
Moreover, customization fosters innovation by enabling rapid iterations and real-time adjustments, which is especially beneficial in fields like medicine, where personalized surgical tools can improve patient outcomes.
Cost reduction in 3D printing tools
Cost reduction is one of the main advantages of 3D printing tools. By eliminating the need for expensive molds and complex manufacturing processes, 3D printing allows you to produce tools on demand, thereby reducing costs related to mass production and storage.
Additionally, the ability to quickly create prototypes and iterate enables you to test and optimize designs without incurring the high expenses associated with traditional methods. The use of less expensive materials and the reduction of waste also contribute to significant savings, making 3D printing especially attractive for small and medium-sized businesses aiming to innovate while controlling their costs.
Speed of production for 3D-printed tools
The speed of production of 3D-printed tools is a major advantage that allows you to quickly respond to urgent needs and design changes. Unlike traditional manufacturing methods, which can take weeks or months to produce a tool, 3D printing enables you to create prototypes and final tools in just a few hours.
This speed is especially beneficial in sectors where time is critical, such as aerospace and medicine, where custom parts can be produced on demand. Moreover, the ability to perform rapid iterations allows engineers and designers to test and refine their designs more efficiently, accelerating the innovation process and reducing time to market.
Durability of 3D-printed tools
The durability of 3D-printed tools is a crucial aspect that largely depends on the materials used and manufacturing techniques. Recent advances in 3D printing materials, such as reinforced polymers and metals, enable the creation of robust and wear-resistant tools that can compete with those made by traditional methods.
Moreover, 3D printing promotes more efficient use of resources by reducing material waste, contributing to a more environmentally friendly production. The ability to repair or replace only damaged parts of a 3D-printed tool also extends its lifespan, reducing the need for frequent replacements and associated costs.
What are the practical applications of 3D printing tools?
The practical applications of 3D printing tools include:
- Custom manufacturing for industry
- Rapid repair
- Prototype creation
- Design of ergonomic and specialized tools
3D printing tools in the manufacturing industry
3D printing of tools in the manufacturing industry is revolutionizing production processes by offering innovative and efficient solutions. This technology allows the creation of custom tools tailored to the specific needs of production lines, thereby improving efficiency and precision in operations.
3D printing also enables the rapid production of prototypes and spare parts, reducing downtime and maintenance costs.
Furthermore, the use of advanced materials and the ability to manufacture complex shapes pave the way for new designs and the optimization of existing tools, contributing to more flexible and competitive production.
3D printing tools in medicine
3D printing of tools in medicine offers significant advantages by enabling the creation of custom surgical tools and prosthetics tailored to the specific needs of patients. This technology allows for the production of custom medical instruments, improving the precision of surgical procedures and reducing the risk of infection.
Additionally, 3D printing facilitates the rapid fabrication of anatomical models for preoperative planning, helping surgeons better prepare for complex operations.
The use of biocompatible materials and the ability to create complex internal structures also pave the way for innovations in implants and medical devices, thereby improving patient outcomes and reducing overall healthcare costs.
3D printing tools in aerospace
3D printing of tools in the aerospace sector offers innovative solutions for manufacturing lightweight and strong parts, essential for airplanes and rockets. This technology allows the creation of complex and customized tools adapted to the industry’s strict performance and safety requirements.
3D printing also reduces production lead times and costs associated with traditional manufacturing, while enabling rapid iterations for design optimization. The use of advanced materials, such as titanium and alloys, allows for the production of durable tools capable of withstanding the extreme conditions encountered in space, thus contributing to innovation and operational efficiency in aerospace.
3D printing tools in education
3D printing of tools in the education sector offers unique opportunities to enhance learning and stimulate students’ creativity. This technology allows educators to create physical models and customized teaching tools, making it easier to understand complex concepts in science, technology, engineering, and mathematics (STEM).
Students can also use 3D printing to bring their ideas and projects to life, developing practical skills in design and manufacturing. Integrating 3D printing into educational programs promotes an interactive and hands-on approach to learning, preparing students for the technological challenges of tomorrow and encouraging innovation from a young age.
What materials are used in 3D printing tools?
Materials used in 3D printing tools include:
- Metals like stainless steel and titanium for greater strength
- PLA and ABS (plastics)
- Nylon (durable)
- Composites (such as carbon fiber)
Plastic materials used in 3D printing tools
Plastic materials used in 3D printing tools offer a wide variety of options to meet different manufacturing needs. Among the most commonly used plastics are PLA (polylactic acid), valued for its ease of printing and biodegradability, and ABS (acrylonitrile butadiene styrene), known for its strength and durability. These materials enable the creation of lightweight and customized tools, suitable for applications requiring moderate resistance and flexibility.
Technical plastics, such as PETG and nylon, offer advanced properties like improved chemical and thermal resistance, thus expanding the possibilities for use in more demanding environments. The continuous development of plastic materials for 3D printing promises to further enhance the performance and durability of printed tools while reducing costs and production waste.
Metals used for 3D printing tools
Metals used for 3D printing tools offer robust and durable properties, suited for demanding industrial applications. Among commonly used metals are titanium, known for its lightweight and exceptional strength, making it ideal for aerospace and medical implants. Stainless steel is also highly valued for its corrosion resistance and durability, making 3D-printed tools suitable for harsh environments.
Aluminum alloys are appreciated for their strength-to-weight ratio, while nickel alloys, such as Inconel, offer high resistance to heat and corrosion, ideal for extreme condition applications.
Using these metals enables the creation of robust and precise tools capable of meeting the most stringent technical requirements, while benefiting from the advantages of additive manufacturing, such as customization and waste reduction.
Composite materials used for 3D printing tools
Composite materials used for 3D printing tools combine the advantages of different materials to offer enhanced properties, such as increased strength and optimal lightness. Among commonly used composites, carbon fiber reinforced polymers are especially valued for their exceptional strength-to-weight ratio, ideal for applications requiring high robustness without adding excessive weight.
Glass-based composites provide good mechanical resistance and dimensional stability, while metallic composites incorporate metal particles into a polymer matrix to improve thermal and electrical conductivity.
These materials enable the creation of highly customized and high-performance tools, suitable for demanding industrial environments, while benefiting from the flexibility and efficiency of additive manufacturing.
Challenges and limitations of 3D printing tools
The challenges of 3D printing tools include:
- High cost of advanced materials and industrial-grade printers
- Limited mechanical strength of some materials
- Sometimes insufficient precision
- Long printing times
Quality and durability of 3D printed tools
The quality and durability of 3D printed tools strongly depend on the materials used and manufacturing parameters. Technological advances now enable the production of tools with precision and finish comparable to those made by traditional methods. The use of high-performance materials, such as metals and composites, improves the strength and longevity of tools, making them suitable for demanding industrial applications.
However, durability can vary depending on the design and maintenance of the tools. Post-processing techniques, such as polishing and heat treatment, can also reinforce the structure of 3D printed tools, ensuring optimal performance in harsh environments.
High initial cost of equipment for 3D printing tools
The high initial cost of equipment for 3D printing tools is a major obstacle for many companies, especially small and medium-sized enterprises (SMEs). Acquiring high-quality industrial 3D printers, capable of producing robust and precise tools, requires a significant financial investment. This cost includes not only the purchase of equipment but also design and management software, as well as training personnel to effectively operate this technology.
Moreover, specialized materials used in 3D printing, such as metals and composites, can also be expensive. However, despite these initial expenses, companies can benefit in the long term from reduced production costs, greater design flexibility, and improved operational efficiency, making the investment potentially profitable.
Training and skills required for 3D printing tools
The training and skills necessary to print 3D tools are essential to fully leverage this technology. Users must not only master Computer-Aided Design (CAD) software to create precise 3D models, but also understand the specific parameters of 3D printers, such as temperature, printing speed, and material selection. A deep knowledge of material properties is crucial to choose the appropriate material based on the intended application of the tool.
Moreover, skills in post-processing, such as polishing and heat treatment, are required to improve the finish and durability of printed tools. Continuous training and hands-on experience enable operators to troubleshoot common issues, optimize production processes, and innovate tool designs, contributing to a more efficient and cost-effective use of 3D printing.
What is the future of 3D printing of tools?
The future of 3D printing tools is moving towards higher-performance materials, increased printing speed, optimized automation, and innovative concepts such as self-repairing tools or smart tools integrating sensors.
Technological innovations facilitating 3D printing of tools
Technological innovations play a crucial role in facilitating and improving 3D printing of tools. Advances in materials, such as the development of new composites and alloys, allow for the creation of more robust and durable tools. Progress in design and simulation software offers enhanced capabilities to optimize structures and predict tool performance before printing.
Moreover, the integration of artificial intelligence (AI) and machine learning in additive manufacturing processes enables automated defect detection and real-time optimization of printing parameters. Post-processing technologies, such as automated polishing and advanced heat treatments, improve the finish and strength of printed tools.
Finally, the evolution of 3D printers themselves, with multi-material capabilities and increased printing speeds, paves the way for more flexible and efficient production, meeting the growing demands for customization and speed across various industrial sectors.
Market trends in 3D tool printing
The market trends in 3D tool printing show rapid growth and increased adoption across various sectors. The market is expected to experience a growth of 22.66% over the next five years, with market size forecasts reaching $227.3 billion by 2036. This expansion is supported by technological innovations, such as automated 3D printing and the integration of advanced materials like polymers and metals.
North America remains a leader in the adoption of 3D printing, with ongoing investments in research and development and strategic partnerships between major companies. 3D printing is increasingly used for mass production, surpassing its initial role in rapid prototyping, thanks to advances in additive manufacturing technologies.
The applications of 3D printing are diversifying, with growing use in sectors such as aerospace, automotive, healthcare, and construction, where customization and on-demand production are increasingly valued. Challenges persist, notably in terms of high purchase and maintenance costs, as well as the need for testing standards to ensure the quality of printed products.
Environmental impact of 3D printed tools
The environmental impact of 3D printed tools is a complex topic that presents both advantages and challenges. On one hand, 3D printing can reduce material waste and energy consumption compared to traditional manufacturing methods, as it allows producing objects using only the necessary amount of material, without significant scraps. Moreover, 3D printing enables local manufacturing, thereby reducing carbon emissions related to transport and logistics.
However, 3D printing also presents environmental challenges. 3D printers often consume a lot of electricity, and some materials used, like ABS, are petroleum-derived and non-biodegradable, which raises waste management issues. Additionally, some 3D printing processes require the use of potentially toxic chemicals, such as photopolymer resins.
Efforts are underway to improve the sustainability of 3D printing, notably through the use of recycled and biodegradable materials, as well as by optimizing manufacturing processes to reduce energy consumption and waste. The adoption of circular economy practices, such as recycling printing materials, can also help reduce the environmental footprint of this technology.
Conclusion: 3D Printing of Tools
In conclusion, 3D printing of tools represents a major technological breakthrough that is transforming various industrial sectors by offering innovative and efficient solutions. This technology allows the creation of customized and complex tools, tailored to specific needs, while reducing costs and production times compared to traditional methods. The use of advanced materials, such as polymers, metals, and composites, improves the durability and performance of printed tools.
However, the adoption of 3D printing also presents challenges, notably high initial costs, the need for training and skills, as well as environmental impact. Ongoing efforts to improve the sustainability of 3D printing, through the use of recycled materials and the optimization of manufacturing processes, are essential to address these concerns.
As the technology evolves, 3D printing of tools is expected to play an increasingly important role in modern manufacturing, promoting innovation and meeting the growing demands for customization and efficiency across various industrial sectors.
Picture by Freepik.
The articles published on Imprimy.com are for informational purposes only. They are intended to provide general advice and information related to 3D printing. Imprimy.com cannot be held responsible for the results obtained or the consequences arising from the application of the shared information. We recommend always checking the specific instructions for your hardware and materials before use.