Do you want to know more about 3D printing of wax? At Imprimy.com, we are here to answer all your questions related to this technology.
Wax 3D printing is a technique used to create precise wax models, often used in casting and prototyping processes.
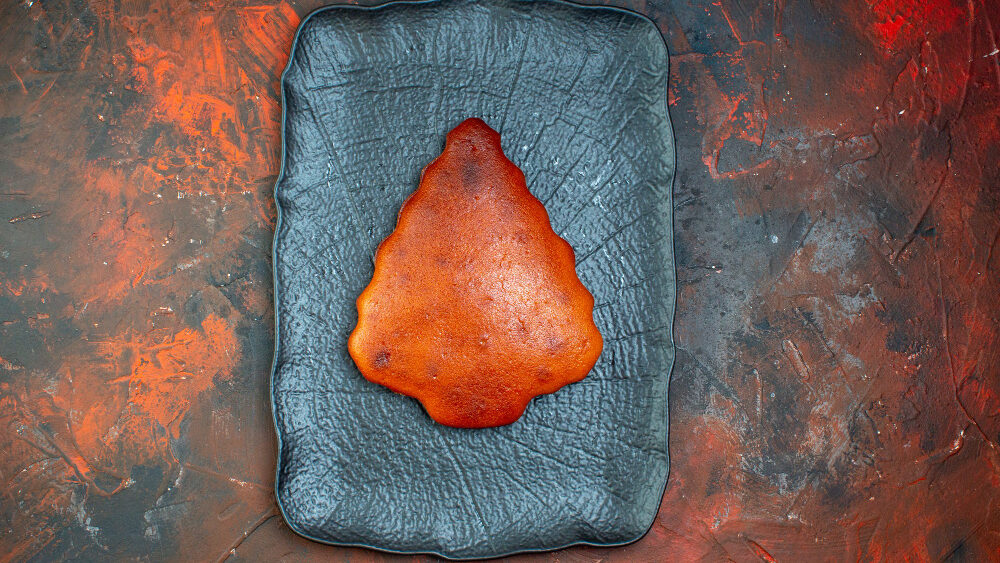
What is wax 3D printing?
Wax 3D printing is an additive manufacturing process that uses wax as a material to create objects layer by layer, often used for making casting models or prototypes.
Definition of wax 3D printing
Wax 3D printing is an additive manufacturing process that uses wax as the primary material to create three-dimensional objects. This technique is often used in fields such as jewelry, dentistry, and rapid prototyping.
The process typically involves the use of a 3D printer that deposits wax layer by layer, following a digital model, to build the final object.
Once the printing is complete, the wax object can be used directly or serve as a model for molding or casting processes.
Brief history of wax 3D printing
Wax 3D printing has evolved into a key method in additive manufacturing, especially for creating precise molds. Initially, wax was used in traditional processes such as lost-wax casting, where a wax model was coated with refractory material to create a mold.
With the advent of 3D printing, technologies like Multi Jet Modeling (MJM) enabled the deposition of molten wax layer by layer to form detailed models, often used in jewelry and dentistry for their precision and high surface finish.
What are the existing wax 3D printing techniques?
The main wax 3D printing techniques are indirect laser sintering (SLS), stereolithography (SLA) with castable resins, MultiJet Printing (MJP) using thermofusible wax, and Fused Deposition Modeling (FDM) adapted for certain specialized wax filaments.
Fused Deposition Modeling
Fused Deposition Modeling (FDM) is a widely used 3D printing technology. It was developed in the 1980s and popularized around 2009 thanks to media coverage. FDM works by extruding a thermoplastic filament through a heated nozzle, which deposits the material layer by layer to build a three-dimensional object.
This process is appreciated for its simplicity, relatively low cost, and its ability to use a variety of materials, such as ABS and PLA. FDM is commonly used for rapid prototyping, creating concept models, and producing functional parts in various industries, including aerospace, automotive, and medical.
Stereolithography
Stereolithography (SLA) is one of the earliest 3D printing technologies, developed in the 1980s. It uses an ultraviolet laser to polymerize a photosensitive liquid resin, layer by layer, to create three-dimensional objects.
This process allows for parts with high precision and a smooth surface finish, making it ideal for applications requiring fine details, such as in jewelry, dentistry, and industrial prototyping.
SLA is also valued for its ability to produce complex parts with intricate geometries that would be difficult to achieve with other manufacturing methods.
Other techniques for 3D wax printing
Wax 3D printing techniques include several innovative methods that allow the creation of wax models for various applications, especially in jewelry, dentistry, and prototype manufacturing. Here are some of the main techniques:
- Multi Jet Modeling (MJM): This technique uses 3D printers that deposit molten wax layer by layer through nozzles, similar to inkjet printing. It is often used for its ability to produce very fine details and high resolution.
- MultiJet Fabrication: This method is similar to stereolithography and allows creating wax parts with great precision, often used for applications requiring complex details.
- 3D printing with castable wax deposition: Used to create lost-wax molds, this technique enables the production of metal parts with high precision and excellent surface finish.
These techniques produce wax models that can then be used to create ceramic molds, into which metals are poured to form the final parts. Each method has its own advantages and is selected based on the specific needs of the application.
What are the advantages of wax 3D printing?
The main advantages of wax 3D printing are high precision, excellent surface quality, the ability to create complex shapes without molds, and its compatibility with lost-wax casting for the manufacture of metal parts.
Precision and details of wax 3D printing
Wax 3D printing is renowned for its ability to produce parts with high precision and fine details. Here are some key points about the precision and details of this technology:
- High Resolution: Wax 3D printers can achieve a layer resolution as fine as 25 microns (0.025 mm), enabling the creation of parts with an extremely high level of detail. This precision is essential for applications where fine details are crucial, such as in jewelry or dentistry.
- MJM: This technology, similar to inkjet printing, uses nozzles to deposit molten wax onto a platform, layer by layer. It allows creating parts with complex details and a smooth surface finish.
- Precision Applications: Wax 3D printing is often used in fields where precision is paramount. For example, in dentistry, it creates highly accurate tooth models, while in jewelry, it is used to manufacture complex parts with fine details.
- Lost-Wax Casting: This traditional technique, combined with wax 3D printing, allows creating ceramic molds with great precision. The 3D printed wax model is used to form the mold, which is then filled with metal to produce the final part.
- Surface Quality: Parts produced by wax 3D printing generally have a high surface quality, reducing the need for additional finishing. This is especially advantageous for applications requiring a smooth surface and sharp details.
Speed and efficiency of wax 3D printing
Wax 3D printing is known for its speed and efficiency, making it a valued technology across various industrial sectors. Here are some key points regarding these aspects:
- Reduced production time: Wax 3D printing significantly decreases the time required to produce wax models compared to traditional methods. This is especially advantageous for rapid prototyping and small batch production, where speed is essential to quickly iterate on designs.
- Process automation: Using 3D printers to create wax models automates much of the manufacturing process, reducing the need for manual intervention. This not only speeds up production but also minimizes human errors, improving overall efficiency.
- Resource optimization: Technologies like MJM enable precise and controlled deposition of wax, optimizing material usage and reducing waste. This contributes to a more efficient and cost-effective production.
- Integration with lost-wax casting: Wax 3D printing is often combined with lost-wax casting, where printed wax models are used to create ceramic molds. This integration allows the production of complex metal parts with high precision and surface finish, while maintaining a fast and efficient production process.
- Design flexibility: The ability to print complex designs directly from digital files allows designers and engineers to rapidly test and iterate on different versions of a product, which is crucial for innovation and product development.
Design flexibility of wax 3D printing
The design flexibility offered by wax 3D printing is one of its major strengths, allowing designers and engineers to create complex and detailed parts with great freedom. Here are some key aspects of this flexibility:
- Geometric complexity: Wax 3D printing enables the creation of complex geometries that would be difficult or even impossible to achieve with traditional manufacturing methods. This includes complex internal structures, thin walls, and fine details, which are particularly useful in fields like jewelry and aerospace.
- Customization and prototyping: The ability to print directly from digital files allows for easy and rapid customization of designs. This is especially advantageous for rapid prototyping, where designers can quickly iterate on different versions of a product to test and refine their designs.
- Integration with other technologies: Wax 3D printing can be combined with other manufacturing technologies, such as lost-wax casting, to produce complex metal parts. This integration combines the design flexibility of 3D printing with the material properties of metals.
- Design optimization: Computer-aided design (CAD) software allows optimizing designs for 3D printing by considering the specific constraints of the technology. This includes optimizing structures to reduce weight, improve strength, or facilitate assembly.
- Reduced manufacturing constraints: Unlike subtractive manufacturing methods, wax 3D printing does not impose the same constraints regarding shapes and structures. This allows designers to focus on the functionality and aesthetics of the part without worrying about manufacturing limitations.
What are the applications of wax 3D printing?
The main applications of wax 3D printing are found in jewelry, dentistry, the aerospace industry, the automotive sector, and art, particularly for the fabrication of precision molds through lost-wax casting.
Wax 3D printing in the jewelry industry
Wax 3D printing has revolutionized the jewelry industry by offering design and production possibilities that were previously difficult to achieve. Here’s how this technology is used in this sector:
- Creation of complex models: Wax 3D printing allows jewelers to create jewelry models with complex details and geometries that would be difficult or even impossible to achieve by hand. This includes designs with fine patterns, detailed textures, and complex internal structures.
- Lost-wax casting: One of the most common applications of wax 3D printing in jewelry is the lost-wax casting technique. The 3D printed wax models are used to create ceramic molds, into which molten metal is poured to produce the final piece. This method faithfully reproduces the wax model details in metal.
- Customization and rapid prototyping: Wax 3D printing allows for easy and fast customization of jewelry designs. Jewelers can quickly iterate on different versions of a design, test ideas, and make modifications without manually recreating each model. This speeds up the design process and reduces development costs.
- Waste reduction: By using wax 3D printing, jewelers can optimize material usage, reducing waste compared to traditional manufacturing methods. This is especially important for precious metals, where waste reduction can lead to significant cost savings.
- Quality improvement: The high precision and surface quality of 3D printed wax models result in high-quality final jewelry. Fine details and smooth finishes are easier to achieve, enhancing the appearance and value of the produced pieces.
- Innovation and creativity: Wax 3D printing opens new possibilities for innovation and creativity in jewelry design. Designers can explore shapes and structures that were previously impossible to realize, pushing the boundaries of what is possible in jewelry making.
Wax 3D printing in art and sculpture
Wax 3D printing has also found significant applications in the fields of art and sculpture, offering artists new possibilities to explore creativity and innovation. Here’s how this technology is used in this context:
- Creation of complex sculptures: Artists can use wax 3D printing to create sculptures with complex shapes and details that would be difficult to achieve by hand. This enables exploring new forms of artistic expression and pushing the boundaries of traditional sculpture.
- Model reproduction: Wax 3D printing is used to accurately reproduce existing models. This is especially useful for creating replicas of artworks or restoring damaged pieces, where fidelity to the original model is crucial.
- Experimentation with materials: Artists can experiment with different types of wax and printing techniques to achieve unique visual and textural effects. This opens new avenues for artistic expression and allows creating works that combine traditional and modern elements.
- Integration with other techniques: Wax 3D printing can be combined with other artistic methods, such as lost-wax casting, to create metal sculptures. This integration allows artists to benefit from the advantages of 3D printing while using traditional materials.
- Customization and uniqueness: Wax 3D printing enables artists to create unique and customized pieces, tailored to the specific needs of a project or client. This is especially advantageous for bespoke commissions, where the ability to quickly and precisely adapt the design is essential.
- Education and training: In the field of art education, wax 3D printing offers students the opportunity to learn and experiment with advanced technologies, preparing the next generation of artists and sculptors to work with modern tools.
Wax 3D Printing in Medicine and Dentistry
Wax 3D printing has also found important applications in the fields of medicine and dentistry, offering innovative solutions for creating customized medical and dental devices. Here’s how this technology is used in these sectors:
- Creation of dental models: In dentistry, wax 3D printing is used to create precise models of teeth and gums. These models are essential for planning orthodontic treatments, creating crowns, bridges, and other dental prosthetics. The precision of 3D printing allows for perfect fits, improving both comfort and functionality for patients.
- Prostheses and implants: Wax 3D printing is used to manufacture custom prostheses and implants. This enables doctors and dentists to create devices that perfectly match the unique anatomy of each patient, enhancing clinical outcomes and patient satisfaction.
- Maxillofacial surgery: In the field of maxillofacial surgery, wax 3D printing is used to create accurate anatomical models that help surgeons plan and simulate complex procedures. These models provide better visualization of anatomical structures and more precise surgical planning.
- Customized medical devices: Wax 3D printing enables the creation of personalized medical devices, such as splints, orthoses, and prosthetics, tailored to the specific needs of each patient. This improves not only comfort and functionality but also the effectiveness of treatments.
- Education and training: In medical and dental education, wax 3D printing is used to create realistic anatomical models that help students learn and practice complex procedures. This enhances the quality of training and better prepares future health professionals.
- Research and development: Wax 3D printing is also used in the R&D of new medical and dental devices. It allows researchers to quickly and efficiently test and refine new designs before mass production.
Other sectors using 3D wax printing
3D wax printing finds applications in various sectors due to its ability to produce precise and detailed parts. Here are some other sectors where this technology is used:
- Aerospace: In the aerospace industry, 3D wax printing is used to create models and prototypes of complex components. This allows engineers to test and validate designs before mass production, thus reducing costs and development time.
- Automotive: Automotive manufacturers use 3D wax printing to create prototypes of parts and design models. This facilitates the visualization and testing of new designs, as well as optimizing performance and aerodynamics of vehicles.
- Electronics: In the electronics sector, 3D wax printing is used to create molds and prototypes of electronic components. This allows for quick and efficient testing and refinement of new designs before mass production.
- Education and Research: Educational institutions and research centers use 3D wax printing to teach and explore new manufacturing techniques. This helps students and researchers become familiar with advanced technologies and develop new applications.
- Art and Design: Artists and designers use 3D wax printing to create sculptures, jewelry, and other complex artworks. This technology offers great design freedom and allows for the creation of unique and customized pieces.
- Mold Manufacturing: 3D wax printing is used to create precise molds for manufacturing parts in metal, plastic, and other materials. This is especially useful in industries where precision and surface quality are essential.
- Food Industry: Although less common, 3D wax printing can also be used in the food industry to create molds and models for the decoration and presentation of food.
What is the future of 3D wax printing?
The future of 3D wax printing is moving towards increased automation, better resolution, more advanced materials, and wider integration into production chains for sectors such as jewelry, healthcare, and aerospace.
Innovations and trends related to 3D wax printing
3D wax printing continues to evolve with innovations and trends that expand its applications and improve its capabilities. Here are some recent innovations and trends in this field:
- Material improvement: Research focuses on developing new wax formulations that offer better printability, greater strength, and improved surface finish. These advanced materials enable the creation of more complex and durable parts, opening new possibilities for industrial and artistic applications.
- Integration with other technologies: 3D wax printing is increasingly integrated with other additive manufacturing technologies, such as lost wax casting and stereolithography. This integration allows combining the advantages of different technologies to create parts with unique properties and characteristics.
- Automation and robotics: Automation of 3D wax printing processes, including the use of robots to handle and process parts, improves efficiency and precision in production. This helps reduce production time and increase repeatability of parts.
- Mass customization: The ability to produce customized parts in large quantities is a growing trend in 3D wax printing. This is particularly relevant in sectors like medicine and dentistry, where tailor-made devices are needed to meet individual patient needs.
- Sustainability and recycling: Environmental concerns drive innovations in wax material recycling and the use of biodegradable waxes. These efforts aim to reduce the environmental impact of 3D wax printing and promote more sustainable manufacturing practices.
- Education and training: 3D wax printing is increasingly used in educational programs to teach principles of additive manufacturing and computer-aided design (CAD). This prepares students to work with advanced technologies and innovate in their future careers.
- Expansion of applications: Applications of 3D wax printing continue to expand into new sectors such as aerospace, automotive, and electronics, where precision and complexity of parts are essential. This expansion is supported by advances in design software and printing technologies.
Growth potential of 3D wax printing
The growth potential of 3D wax printing is significant, driven by technological advances, growing demand for customized manufacturing solutions, and increased adoption across various industrial sectors. Here are some key factors contributing to this growth potential:
- Growing demand for customization: In sectors like medicine, dentistry, and jewelry, demand for personalized and tailor-made products continues to rise. 3D wax printing, with its ability to produce precise parts adapted to individual needs, is well-positioned to meet this demand.
- Technological advances: Progress in 3D printing technologies, including improvements in printers, design software, and materials, continues to expand the possibilities of 3D wax printing. These advances enable the creation of more complex, more durable, and higher quality parts, opening new applications and markets.
- Expansion of industrial applications: 3D wax printing finds new applications in sectors such as aerospace, automotive, and electronics, where precision and complexity of parts are critical. This expansion contributes to market growth.
- Adoption in education and research: Use of 3D wax printing in educational programs and research centers prepares the next generation of professionals to work with advanced technologies. This fosters innovation and development of new applications, thereby stimulating sector growth.
- Sustainability and eco-friendly practices: The trend toward more sustainable and eco-friendly manufacturing encourages adoption of technologies like 3D wax printing, which help reduce waste and optimize material use. This is especially attractive to companies seeking to improve their environmental footprint.
- Integration with other technologies: Integrating 3D wax printing with other additive manufacturing methods, such as lost wax casting and stereolithography, combines the advantages of different techniques to create parts with unique properties. This integration opens new opportunities for innovation and growth.
- Investments and industrial support: Investments in research and development, along with support from industries and governments, play a crucial role in the growth of 3D wax printing. These investments enable the development of new technologies, improve existing processes, and explore new applications.
Conclusion : 3D wax printing
3D wax printing is a cutting-edge technology offering high precision and detail, ideal for applications in jewelry, dentistry, and rapid prototyping. It uses specially formulated waxes for casting, allowing production cost savings through reduced material waste. This technology continues to evolve with constant improvements in materials, precision, and printing speed, making it a versatile and rapidly growing tool across multiple industries.
Picture by Kamran Aydinov from Freepik.
The articles published on Imprimy.com are for informational purposes only. They are intended to provide general advice and information related to 3D printing. Imprimy.com cannot be held responsible for the results obtained or the consequences arising from the application of the shared information. We recommend always checking the specific instructions for your hardware and materials before use.