Would you like to learn more about TPU in the context of 3D printing, its specifics, and how it works? At Imprimy.com, we are here to provide you with all the information you need to answer all your questions.
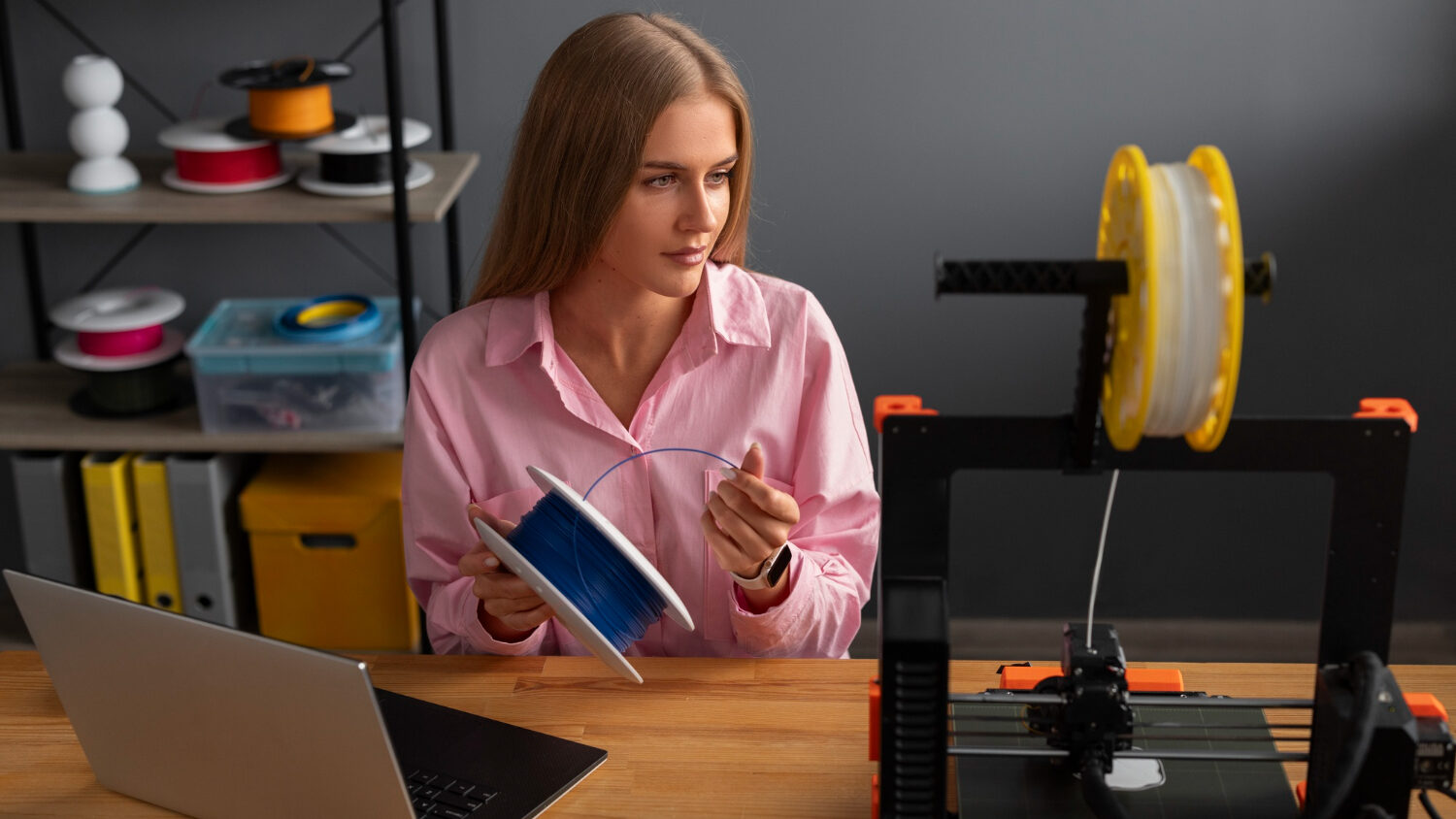
What is TPU?
TPU (Thermoplastic Polyurethane) is a flexible and durable material, often used in 3D printing, that combines elasticity, durability, and shock resistance.
The definition of TPU
TPU (Thermoplastic Polyurethane) is a flexible and durable thermoplastic material, often used in 3D printing due to its high elasticity and abrasion resistance. This plastic, which combines the properties of rigid plastic and rubber, offers valuable characteristics for applications requiring flexibility, shock resistance, and durability, such as in the manufacturing of soft objects, seals, protective gear, and even shoes.
Its ability to be easily reshaped when heated allows for easy modification while maintaining its strength. TPU is particularly valued for its resistance to wear and chemicals, making it an ideal choice for parts that need to withstand extreme conditions.
The differences between TPU and other materials
TPU stands out from other 3D printing materials like PLA, ABS, and PETG due to its unique combination of flexibility, shock resistance, and durability. While PLA is rigid and easy to print, TPU is more flexible, allowing for the creation of soft, elastic parts such as gaskets, seals, and flexible components. ABS, on the other hand, is more robust and heat-resistant but lacks the flexibility of TPU, making it less suitable for projects requiring elasticity.
Compared to PETG, which is also durable and resistant to impact, TPU is more elastic, making it ideal for use in applications such as soft-touch surfaces, protective covers, and sporting goods. PETG is often chosen for structural parts because of its stiffness, but TPU is the preferred choice when flexibility is essential.
In summary, TPU is distinguished from other common 3D printing materials by its ability to bend, flex, and withstand high-impact conditions, while materials like PLA, ABS, and PETG are chosen for different attributes like rigidity, strength, or ease of use.
Why use TPU in 3D printing?
TPU is used in 3D printing due to its clear advantages, particularly its elasticity and flexibility, which make it ideal for producing soft, durable, and shock-resistant parts. However, these same properties also present certain challenges, such as difficulty in feeding the filament through the extruder and handling flexibility during printing. Despite these challenges, TPU’s ability to withstand abrasion and chemical exposure makes it an excellent choice for applications requiring durability and impact resistance, such as gaskets, protective gear, and flexible custom parts.
The main advantages of TPU
- Flexibility: TPU is highly flexible and can bend and stretch without breaking, making it ideal for creating soft, elastic parts like gaskets, seals, and wearable items.
- Durability: TPU offers excellent resistance to abrasion, wear, and impact, ensuring that printed parts maintain their functionality even in harsh environments.
- Shock Absorption: The material’s elasticity allows it to absorb shock, making it ideal for applications like protective covers, cushioning, and sporting goods.
- Chemical Resistance: TPU is resistant to many chemicals, oils, and greases, which enhances its suitability for applications in industries like automotive and healthcare.
- Ease of Modification: TPU can be easily reshaped when heated, offering the flexibility to modify printed objects without compromising their strength.
- UV and Weather Resistance: TPU is resistant to UV light and weathering, making it an excellent choice for outdoor applications where parts need to withstand exposure to the elements.
- Comfort and Grip: Due to its soft nature, TPU provides comfort and a good grip, which is why it is often used in items like custom footwear, phone cases, and ergonomic tools.
The specific challenges of TPU
- Feeding the Filament: TPU’s flexibility can make it challenging to feed through the extruder, particularly in Bowden extruders. It can bend or buckle during the feeding process, leading to jams or inconsistent extrusion if not managed properly.
- Print Speed: Due to its flexibility, TPU requires slower print speeds (around 20-30 mm/s) to ensure smooth and accurate extrusion. Printing too quickly can lead to issues such as under-extrusion or poor layer adhesion.
- Adhesion Issues: TPU may not always adhere well to certain types of print beds, requiring specialized surfaces (like heated beds or adhesive sprays) to achieve proper adhesion and avoid warping or detaching during printing.
- Stringing and Oozing: TPU’s stringing tendency is more pronounced compared to more rigid materials like PLA or ABS. This means it may leave unwanted strands of filament between print areas, which can require extra post-processing to clean up.
- Overheating: While TPU is a thermoplastic, it can degrade if exposed to excessive heat, leading to poor print quality and material waste. It’s important to fine-tune the temperature settings for proper extrusion and to avoid overheating.
- Post-Processing: Due to its softness and flexibility, post-processing TPU prints (such as sanding or cutting) can be more challenging compared to rigid materials. The parts may require more careful handling to avoid damage.
What are the practical applications of TPU 3D printing?
TPU can be used in 3D printing across a wide range of fields such as the automotive industry, fashion, sports, and healthcare.
TPU in the automotive industry
TPU is increasingly used in the automotive industry due to its exceptional properties that meet the sector’s requirements. With its flexibility, shock resistance, and abrasion resistance, TPU is ideal for a variety of applications in automotive manufacturing.
Applications of TPU in the automotive industry:
- Soft and flexible parts: TPU is commonly used for producing gaskets, door handles, interior trims, cable protection, and seat covers. Its flexibility allows for the design of comfortable and durable parts that are also resistant to wear.
- Shock absorbers and impact protection: Due to its ability to absorb impacts, TPU is used for components like shock absorbers, bumper protectors, and vehicle protections to prevent damage during collisions or contact with other surfaces.
- Components resistant to extreme conditions: TPU performs well in harsh environments, resisting chemicals, moisture, and extreme temperatures. This makes it ideal for applications such as pipes, safety clothing, or engine components.
- Customization and accessories: TPU is also used in manufacturing custom parts for vehicle interiors, such as design elements, coatings, and accessories tailored to users’ preferences.
Advantages for the automotive industry :
- Durability: TPU has a long lifespan due to its resistance to wear, abrasion, and harsh conditions commonly encountered in the automotive industry.
- Lightweight: TPU helps reduce the weight of components, contributing to improved fuel efficiency and energy efficiency in vehicles.
- Environmental friendliness: As a thermoplastic material, TPU can be recycled, making it a valuable asset for the automotive industry, which is increasingly focused on environmental sustainability.
TPU in fashion and design
TPU is experiencing growing success in the fashion and design fields due to its unique characteristics, such as flexibility, resistance, and durability, making it an ideal material for creating innovative and functional items.
Applications of TPU in fashion and design:
- Fashion Accessories: TPU is used to create bracelets, bags, belts, and other accessories. Its flexibility and ability to be molded into various shapes make it a popular choice for custom, eye-catching designs.
- Footwear: TPU is utilized in the production of shoe soles, insoles, and decorative elements for footwear. It provides a balance of comfort, durability, and design versatility, ideal for both functional and stylish shoes.
- Jewelry: TPU is increasingly used in the creation of modern, custom jewelry pieces. Its translucent quality and ability to be shaped into bold, intricate designs make it perfect for unique jewelry collections.
- Wearable Technology: TPU’s comfort and durability make it an excellent material for smartwatch bands, fitness tracker straps, and other wearable tech accessories. It provides flexibility, strength, and style in one package.
- Textiles and Fabrics: TPU can be incorporated into waterproof fabrics and lightweight textiles, making it ideal for outerwear, bags, and sportswear that require both durability and functional style.
- Home Décor: TPU’s design potential also extends to home décor items such as custom cushions, pillows, or wall art, where its flexibility and durability bring an innovative edge to interior design.
Advantages of TPU in fashion and design:
- Flexibility and Versatility: TPU’s flexibility allows for the creation of a wide range of shapes and designs, making it ideal for custom fashion items, accessories, and footwear that require both comfort and style.
- Durability: TPU is highly durable and resistant to wear and tear, ensuring that products such as bags, bracelets, and shoes remain in excellent condition even after regular use, making it a practical choice for everyday fashion items.
- Water Resistance: TPU is water-resistant, making it perfect for creating waterproof fashion accessories like bags or outerwear, as well as for use in wearable tech that may be exposed to moisture.
- Aesthetic Appeal: TPU can be produced in a variety of colors, finishes, and translucent forms, allowing designers to create innovative, unique, and eye-catching designs that add a modern edge to fashion and accessories.
- Lightweight: TPU is a lightweight material, making it ideal for comfortable clothing, accessories, and footwear, offering both style and practicality without adding unnecessary bulk.
- Customization: TPU’s moldability and availability in various colors and textures allow for the personalization of fashion pieces, offering consumers the opportunity to express their unique styles through custom designs.
- Eco-Friendliness: TPU is a recyclable material, which aligns with the growing trend toward sustainability in the fashion industry, allowing designers and brands to reduce their environmental footprint. peut être facilement personnalisé par impression 3D, permettant ainsi de répondre aux besoins spécifiques de chaque créateur ou consommateur.
TPU in sports and leisure
TPU is a material that is increasingly finding applications in the sports and leisure industry due to its unique characteristics, such as flexibility, shock resistance, and durability. It is particularly suitable for creating sports equipment and leisure objects that require both high performance and optimal comfort.
Applications of TPU in sports and leisure:
- Protective Gear: TPU is used in the production of shin guards, mouthguards, knee pads, and other protective equipment. Its shock absorption properties and flexibility make it ideal for sports safety gear, offering comfort and protection.
- Sports Footwear: TPU is commonly found in the manufacturing of sports shoes and training footwear, providing the necessary flexibility, durability, and comfort for athletes during high-performance activities.
- Fitness Accessories: TPU is used in a variety of fitness accessories like exercise mats, yoga blocks, and resistance bands, where its durability and flexibility make it well-suited for heavy use in fitness routines.
- Outdoor Equipment: TPU is used in the design of camping gear, sleeping pads, waterproof bags, and other outdoor equipment, offering weather resistance and durability for activities in the elements.
- Leisure Equipment: TPU is also used in sporting goods like bike grips, fishing rod handles, golf club grips, and recreational toys, where its comfort, flexibility, and resistance to wear enhance the experience of users.
- Wearable Devices: TPU is found in the design of fitness trackers, smartwatches, and activity bands, providing both comfort and resilience for wearable devices that are used during physical activities.
Advantages of TPU in sports and leisure:
- Shock Absorption: TPU’s excellent ability to absorb impacts makes it ideal for protective gear, such as shin guards, mouthguards, and knee pads, providing superior protection and comfort.
- Flexibility: The material’s flexibility allows for high-performance equipment like sports footwear and fitness accessories, providing comfort and adaptability during various activities.
- Durability: TPU is highly durable, resistant to abrasion and wear, making it suitable for equipment that undergoes heavy use, such as bike grips, fishing rods, and camping gear.
- Weather Resistance: Its resistance to moisture and extreme temperatures makes TPU perfect for outdoor gear, like waterproof bags and sleeping pads, ensuring that products remain functional and intact in harsh weather conditions.
- Lightweight: TPU is a lightweight material, which is essential for sports equipment and fitness accessories where excess weight could hinder performance and comfort.
- Comfort: TPU’s flexibility and soft touch offer an added layer of comfort, making it ideal for products like sports shoes, wearable devices, and protective gear that are in direct contact with the body.
- Customization: TPU can be easily molded into various shapes and designs, enabling customization of products to meet specific performance needs or personal preferences in the sports and leisure industry.
TPU in health-related fields:
TPU is increasingly finding a place in health-related fields due to its characteristics that combine flexibility, durability, and biocompatibility. These properties make it particularly suitable for the manufacturing of medical equipment, care devices, and therapeutic accessories, where safety and comfort are paramount.
Applications of TPU in healthcare:
- Medical Devices: TPU is used in the production of catheters, surgical tubing, and medical hoses due to its biocompatibility, flexibility, and durability, ensuring safe and reliable use in medical procedures.
- Prosthetics and Orthotics: TPU is commonly used in prosthetic limbs, orthotic supports, and joint replacements. Its shock-absorbing properties, combined with flexibility, provide comfort and mobility for patients.
- Wound Care: TPU is utilized in the production of waterproof wound dressings, bandages, and medical tapes. Its breathable and elastic qualities make it ideal for protecting wounds while promoting the healing process.
- Personal Protective Equipment (PPE): TPU is used in face masks, gloves, and protective clothing. Its chemical resistance, elasticity, and durability make it ideal for providing protection in medical environments.
- Implants: TPU is increasingly used in medical implants, such as vascular grafts, dental implants, and surgical meshes. It provides the necessary strength, flexibility, and biocompatibility for implants in the body.
- Diagnostic Tools: TPU is used in diagnostic equipment like sensor pads, testing strips, and monitoring devices, where its flexibility and biocompatibility are essential for patient safety.
- Therapeutic Accessories: TPU is also found in products like compression sleeves, orthopedic supports, and therapeutic bandages, where its stretchability and comfort make it perfect for supporting and promoting healing in various medical conditions.
Advantages of TPU in healthcare:
- Biocompatibility: TPU is highly biocompatible, making it safe for use in medical devices and implants that come into contact with the human body, reducing the risk of irritation or allergic reactions.
- Flexibility and Comfort: TPU’s flexibility and soft feel provide comfort in devices like prosthetics, orthotics, and wound care products, ensuring they can be worn for long periods without causing discomfort.
- Durability: TPU is durable and resistant to wear, making it ideal for medical equipment and devices that need to withstand constant use while maintaining their functionality over time, such as surgical tubing or protective gear.
- Shock Absorption: TPU’s ability to absorb shocks makes it an excellent choice for applications such as prosthetics and orthopedic devices, offering enhanced protection and comfort for patients with mobility issues or injuries.
- Chemical Resistance: TPU is resistant to a variety of chemicals, including blood, salts, and disinfectants, which is crucial in medical environments where products must endure frequent cleaning and exposure to harsh substances.
- Moisture Resistance: TPU’s water-resistant properties are valuable for wound dressings, waterproof medical tapes, and protective clothing, ensuring that medical products maintain their integrity in humid or wet conditions.
- Lightweight: TPU’s lightweight nature contributes to the overall comfort and wearability of medical devices like masks or compression garments, reducing strain on patients or healthcare workers who wear them for extended periods.
- Customization: TPU can be easily molded and customized, allowing for the production of medical devices that are tailored to a patient’s specific needs, whether in terms of shape, size, or design, such as in prosthetics and orthotics.
How to print objects in TPU?
Printing objects in TPU requires some specific adjustments compared to more rigid materials like PLA or PETG, as TPU is a soft and flexible filament. Here are the three main sections to consider for successfully printing your TPU objects.
Printing settings adjustments
One of the first crucial steps for printing TPU is to properly adjust your 3D printer’s settings.
- Extruder Temperature: TPU requires an extrusion temperature of around 210-250°C, depending on the brand and model of the filament. It’s recommended to start at 220°C and adjust as necessary to achieve good filament flow without overheating.
- Printing Speed: TPU should be printed at a slower speed compared to rigid materials, typically around 20-30 mm/s. This helps prevent feeding issues and filament deformation, as TPU can have a tendency to twist.
- Heated Bed Temperature: Use a heated bed set between 40 and 60°C. A bed that is too hot can cause poor adhesion or warping, while a bed that is too cold may not maintain proper adhesion.
TPU Filament Handling
Handling TPU filament correctly is essential for successful 3D printing, as this flexible material can be tricky if not managed properly. Here are some key considerations for managing TPU filament:
- Storage: TPU filament is hygroscopic, meaning it absorbs moisture from the air, which can cause print defects like bubbling or poor adhesion. Store TPU filament in a dry place, preferably in a sealed bag with desiccants or in a filament dryer to keep it moisture-free.
- Feeding the Filament: Due to its flexibility, TPU can be challenging to feed into the extruder. Ensure that the filament spool is unwinding smoothly without any tangles or snags. Use a direct-drive extruder if possible, as it is better suited for flexible filaments like TPU. If using a Bowden tube, ensure it’s not too long or restrictive, as this can cause feeding issues.
Filament Pathway: Avoid any sharp turns or long pathways in the filament path to reduce the risk of kinking or tangling. A smooth and straight filament path will help the TPU flow easily into the extruder and improve print consistency.
Bed Preparation and Finishing
Proper bed preparation is crucial to ensure strong adhesion of the TPU object during the print.
- Use a well-prepared bed: TPU requires good adhesion to the print bed. To achieve this, you can use a sticky surface like masking tape or a special adhesive coating for 3D printing. A heated bed with a PEI coating or a glass surface with hairspray or glue can also improve adhesion.
- Adjust the first layers: It’s important not to crush the first layers to allow the TPU to adhere well without distortion. You can adjust the nozzle height to optimize the first print layer.
- Post-processing: Once the print is complete, if necessary, gently detach the supports or trim excess material. TPU can sometimes be a bit more difficult to handle after printing because of its flexibility, so patience is key.
By following these three steps, you can enhance your TPU prints and produce soft, durable, and high-quality objects.
Conclusion: 3D TPU Printing
In conclusion, TPU 3D printing is a highly versatile and valuable option for producing flexible, durable, and shock-resistant objects. Despite requiring specific adjustments in printing settings and handling, such as controlling temperature, speed, and bed preparation, the benefits of using TPU make it an excellent choice for a wide variety of industries and applications.
From automotive parts to medical devices, sports equipment, and fashion, TPU provides unmatched flexibility and resilience. By following the right techniques and ensuring careful management throughout the printing process, you can achieve high-quality prints that meet both functional and aesthetic requirements.
Picture by Freepik.
The articles published on Imprimy.com are for informational purposes only. They are intended to provide general advice and information related to 3D printing. Imprimy.com cannot be held responsible for the results obtained or the consequences arising from the application of the shared information. We recommend always checking the specific instructions for your hardware and materials before use.