Would you like to learn more about brass 3D printing and its specific features? At Imprimy, we are here to answer all your questions related to this topic.
Brass 3D printing allows the creation of metal parts with high precision and good mechanical strength.
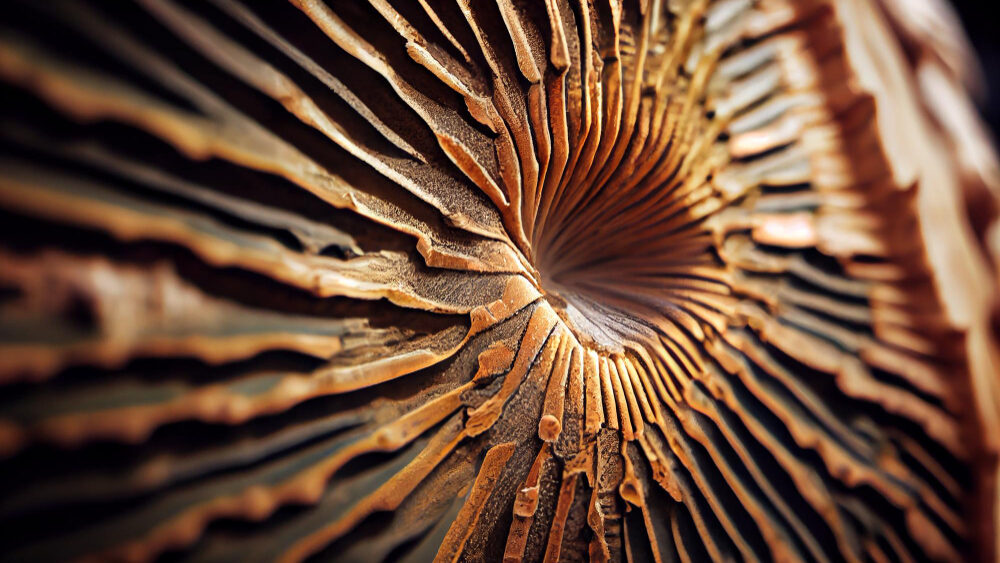
Reminder: What is brass and what is 3D printing?
Brass is a metal alloy mainly composed of copper and zinc, while 3D printing is an additive manufacturing technology that creates objects by layering materials.
Overview and Composition of Brass
Brass is a metal alloy mainly composed of copper and zinc, although other elements like lead, tin, or nickel may be added in small amounts to enhance certain properties. The composition of brass can vary, but it generally contains between 55% and 90% copper, with the remainder primarily being zinc.
This alloy is valued for its malleability, corrosion resistance, and aesthetic appearance, making it ideal for a wide range of applications, from musical instruments to faucets and decorative items. Brass is also easy to machine and solder, making it a highly versatile material in both industry and craftsmanship.
3D Printing Technologies and Advantages
3D printing, also known as additive manufacturing, is a production technology that creates objects by adding successive layers of material. Common technologies include Fused Deposition Modeling (FDM), Stereolithography (SLA), and Selective Laser Sintering (SLS).
3D printing offers many advantages, such as product customization, waste reduction compared to traditional manufacturing methods, and the ability to produce complex geometries that would be difficult or impossible to achieve otherwise. It also enables rapid prototyping, which speeds up the product development process and reduces associated costs. Additionally, this technology supports on-demand production, minimizing the need for storage and inventory.
What is Brass 3D Printing?
Brass 3D printing is an additive manufacturing process that uses brass, an alloy of copper and zinc, to create complex and durable metal parts.
The Use of Brass in 3D Printing
The use of brass in 3D printing is less common than that of other materials like plastics or more popular metals such as aluminum or stainless steel. However, brass can be used in metal 3D printing processes, particularly through technologies like Selective Laser Sintering (SLS) or Directed Energy Deposition (DED).
Brass is valued for its aesthetic properties, corrosion resistance, and thermal conductivity, making it an attractive material for specific applications. In the context of 3D printing, using brass allows for the creation of complex parts with fine details, while benefiting from the traditional advantages of brass such as durability and appealing appearance.
However, 3D printing with brass presents certain challenges, especially regarding temperature control and the need for specialized equipment capable of handling metal powders. Additionally, the cost and complexity of the process can be obstacles to wider adoption.
Challenges and Solutions in 3D Printing
3D printing presents several challenges, but solutions are being developed to overcome them. One major challenge is the limited range of materials, as not all materials are suitable for 3D printing, which can restrict potential applications. To address this, ongoing research aims to develop new materials compatible with 3D printing technologies.
Another challenge is production speed, which is often slower than traditional manufacturing methods. Technological advancements, such as improved printers and optimized processes, are being developed to increase printing speed.
The quality and precision of printed parts can also be an issue, with potential defects or inaccuracies. Advanced software solutions and more precise printing technologies are being created to improve the quality of printed components.
Finally, the cost of 3D printers and materials can be a barrier. However, as the technology becomes more widespread and economies of scale take effect, costs are expected to decrease, making 3D printing more accessible.
What Are the Applications of Brass 3D Printing?
The applications of brass 3D printing include the creation of industrial parts, electronic components, decorative objects, and medical prosthetics, thanks to its strength and thermal conductivity.
Industries Involved in Brass 3D Printing
Brass 3D printing attracts several industries due to the material’s unique properties, such as corrosion resistance, thermal conductivity, and aesthetic appeal. Here are some of the key industries:
- Aerospace industry: For components requiring good corrosion resistance and relatively light weight.
- Automotive industry: For decorative or functional parts where appearance and durability matter.
- Plumbing industry: For manufacturing faucets, valves, and other accessories where corrosion resistance is essential.
- Jewelry and decoration industry: To create complex, detailed pieces with an attractive finish.
- Music industry: For producing musical instruments, especially wind instruments, where brass is traditionally used.
- Electronics industry: For components requiring good thermal and electrical conductivity.
These industries benefit from brass 3D printing to produce custom parts, reduce material waste, and speed up prototyping and production.
Some Examples of Projects or Products Made with Brass 3D Printing
Brass 3D printing is still a niche field, but there are some notable examples of projects and products made with this technology:
- Musical instruments: Some manufacturers are experimenting with brass 3D printing to create parts for musical instruments, such as trumpet mouthpieces or saxophone components, leveraging the ability to create complex and custom geometries.
- Jewelry and accessories: Designers use brass 3D printing to create unique, customized jewelry, such as rings, bracelets, and pendants, benefiting from the aesthetic and durability of brass.
- Industrial components: In some cases, specific industrial components, such as valves or fittings, are made from brass through 3D printing for applications requiring corrosion resistance and good thermal conductivity.
- Art and sculptures: Artists use brass 3D printing to create sculptures and art installations, taking advantage of the technology’s ability to produce complex and detailed shapes.
- Rapid prototyping: In the field of prototyping, brass 3D printing allows for the quick creation of functional prototypes for testing and evaluation before mass production.
These examples illustrate how brass 3D printing can be used to create innovative and customized products across various industries.
How to Succeed with Brass 3D Printing?
To succeed with brass 3D printing, make sure to use a 3D printer suitable for metals, properly calibrate the printing parameters, and choose high-quality brass.
Choosing a 3D Printer for Brass Printing
To choose a 3D printer suitable for brass printing, it is essential to consider several key criteria. First, the printer must be compatible with metal filaments, often made of brass mixed with a polymer binder. Look for models equipped with a wear-resistant nozzle, such as a hardened steel or ruby nozzle, as brass is abrasive and can damage standard nozzles.
A high extrusion temperature is also necessary, typically between 200°C and 250°C, to ensure proper filament fusion. The presence of a heated bed is another important factor to prevent issues with part warping and detachment.
Finally, prioritize printers offering good stability and precision, with features like automatic bed leveling and a rigid structure to ensure high-quality prints.
Your 3D Printing Parameters
To print brass with a 3D printer, it is important to correctly configure the printing parameters to achieve optimal results. Here are some recommendations:
- Extrusion temperature: Brass requires a higher extrusion temperature than standard filaments. A range of 200°C to 250°C is typically recommended.
- Printing speed: Print at a moderate speed, usually between 30 mm/s and 50 mm/s, to ensure good fusion and layer adhesion.
- Layer height: Use a finer layer height, between 0.1 mm and 0.2 mm, to capture details and achieve a better surface finish.
- Infill: An infill rate of 30% to 50% is often sufficient to ensure the part’s strength while saving material.
- Cooling: Unlike other materials, brass may not require active cooling. Disable the cooling fan or use it at a low speed to avoid rapid cooling, which could cause cracks.
- Bed adhesion: Use a heated bed set to around 60°C to 80°C and apply an adhesive like stick glue or tape to improve adhesion and prevent warping.
- Retraction: Activate retraction to minimize filament oozing and improve surface quality, but adjust the retraction settings to avoid nozzle blockages.
By adjusting these parameters, you can optimize the quality of your brass prints and produce strong and detailed parts.
Post-Processing of Brass 3D Prints
Post-processing of brass 3D prints is a crucial step to enhance the quality and appearance of the produced parts.
After printing, brass parts may require several types of post-processing, such as sanding to remove surface imperfections, polishing to achieve a smooth and shiny finish, or thermal treatments to improve mechanical properties. Cleaning the parts is also essential to remove any powder or support residue.
Finally, coatings or surface treatments may be applied to protect against corrosion or for aesthetic reasons. These steps help optimize the performance and durability of the brass parts printed in 3D.
Conclusion: Brass 3D Printing
In conclusion, brass 3D printing offers exciting possibilities for creating complex and durable parts. With its mechanical properties and corrosion resistance, brass is an ideal material for many industrial and artistic applications.
However, to achieve high-quality parts, proper post-processing is often required. This includes steps such as sanding, polishing, and possibly thermal treatments or coatings. These processes not only improve the appearance of the parts but also enhance their performance and durability, making brass 3D printing an effective solution for a variety of applications.
Picture by vecstock from Freepik.
The articles published on Imprimy.com are for informational purposes only. They are intended to provide general advice and information related to 3D printing. Imprimy.com cannot be held responsible for the results obtained or the consequences arising from the application of the shared information. We recommend always checking the specific instructions for your hardware and materials before use.