Are you wondering about ceramic 3D printing and how it works? At Imprimy.com, we are here to provide answers to all your questions related to ceramic 3D printing.
Ceramic 3D printing is an additive manufacturing technology that uses ceramic materials to create complex and durable objects.
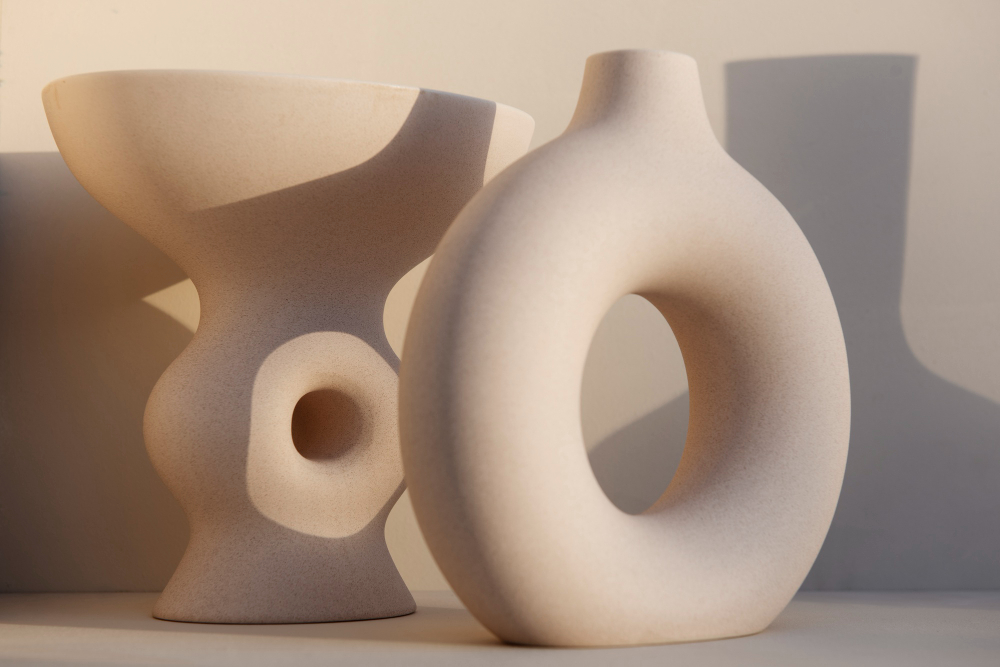
What is ceramic 3D printing?
Ceramic 3D printing is a manufacturing process that uses ceramic materials to create three-dimensional objects by layer-by-layer deposition.
- What is ceramic 3D printing?
- What technologies are used in ceramic 3D printing?
- What materials are used for ceramic 3D printing?
- What are the applications of ceramic 3D printing?
- What are the advantages of ceramic 3D printing?
- What are the challenges and limitations of ceramic 3D printing?
- What is the future of ceramic 3D printing?
- Conclusion : Ceramic 3D printing
Definition and explanation of the ceramic 3D printing process
Ceramic 3D printing is an additive manufacturing process that allows the creation of ceramic objects from a digital model. This process uses a specialized 3D printer that deposits successive layers of ceramic material, often in the form of paste or powder, to build the object layer by layer.
Once the printing is complete, the object is usually subjected to a thermal treatment called sintering, which involves heating the material at a high temperature to solidify it and give it its final strength. This technique is especially valued for its ability to produce complex and customized shapes that would be difficult—or even impossible—to achieve using traditional manufacturing methods.
Applications of ceramic 3D printing include the creation of art pieces, medical prosthetics, and industrial components.
Comparison with other types of 3D printing (plastic, metal, etc.)
Ceramic 3D printing stands out from other types of 3D printing, such as those using plastic or metal, due to its material properties and specific applications. Unlike plastic 3D printing, which is widely used for rapid prototyping and producing lightweight parts with materials like ABS or PLA, ceramic printing offers superior thermal resistance and durability, ideal for applications requiring non-conductive and heat-resistant materials.
Compared to metal 3D printing, often used for structurally robust and conductive parts in aerospace and automotive industries, ceramic printing is preferred for applications where corrosion resistance and insulating properties are crucial.
However, ceramic printing can be more complex and costly due to the necessary thermal treatments, whereas plastic printing is generally more accessible and faster.
What technologies are used in ceramic 3D printing?
The main technologies used in ceramic 3D printing are paste deposition (robocasting), stereolithography (SLA) with ceramic-filled resins, binder jetting, and post-print sintering to solidify the parts.
Description of the different technologies
Ceramic 3D printing technologies mainly vary based on the material deposition and processing methods. Here are some of the main technologies:
- SLA (Stereolithography): Uses a photosensitive resin loaded with ceramic particles. A UV laser solidifies the resin layer by layer, and the object is then sintered to remove the resin and densify the ceramic.
- FDM (Fused Deposition Modeling): Although less common for ceramics, this method uses a ceramic filament that is melted and deposited. After printing, parts undergo thermal treatment to eliminate binders and sinter the ceramic.
- DLP (Digital Light Processing): Similar to SLA but uses a projector to cure an entire layer of resin at once, which can speed up the printing process.
- Binder Jetting: A liquid binder is deposited onto a bed of ceramic powder to form the object’s layers. After printing, parts are sintered to achieve the necessary strength.
- Ceramic Paste Extrusion: A ceramic paste is extruded through a nozzle to build the object layer by layer. This method is often used for artistic applications and large parts.
Each technology has its advantages and limitations, and the choice often depends on the specific application, the complexity of the part, and the required material properties.
Advantages and disadvantages of each technology
The different ceramic 3D printing technologies each have specific advantages and disadvantages:
Advantages | Disadvantages | |
SLA | High precision and resolution, smooth surfaces, ability to produce fine details. | High cost of specialized resins, need for post-processing to remove resin and sinter the ceramic, size limitations of parts. |
FDM | Accessible and low-cost machines, easy to use, possibility to use ceramic filaments. | Limited resolution, need for post-processing to achieve optimal ceramic properties, risk of deformation during sintering. |
DLP | Faster printing speed than SLA, good precision and resolution. | High resin cost, need for post-processing, size limitations of parts. |
Binder Jetting | Ability to produce large parts, no need for support structures, possibility to use a variety of ceramic powders. | Limited resolution, need for post-processing to remove binder and sinter the ceramic, risk of porosity in final parts. |
Ceramic Paste Extrusion | Ability to produce large parts, simple process, low material cost. | Limited resolution, need for post-processing to achieve optimal ceramic properties, risk of deformation during drying and sintering. |
Each technology has its strengths and weaknesses, and the choice depends on the specific project requirements, such as precision, part size, and budget.
What materials are used for ceramic 3D printing?
The materials used for ceramic 3D printing mainly include alumina, zirconia, silicon carbide, silicon nitride, as well as technical clays and ceramic-filled photopolymer resins.
Different types of ceramics used in ceramic 3D printing
In ceramic 3D printing, several types of ceramics are used, each offering specific properties suited to different applications:
- Clay-based ceramics: Used for artistic and decorative applications, often chosen for their ease of use and low cost.
- Technical ceramics:
- Alumina (Al₂O₃): Known for its mechanical strength and thermal stability, used in industrial and medical applications.
- Zirconia (ZrO₂): Offers high strength and good biocompatibility, often used for dental implants and prosthetics.
- Silicon nitride (Si₃N₄): Used for applications requiring wear resistance and high-temperature stability.
- Bioactive ceramics: Such as hydroxyapatite, used in the medical field for bone regeneration due to their biological compatibility.
- Piezoelectric ceramics: Used in electronic applications and sensors due to their ability to convert mechanical energy into electrical energy.
- Porous ceramics: Used in filtration and catalysis applications because of their porous structure.
The choice of ceramic type depends on the required properties for the specific application, such as mechanical strength, thermal stability, biocompatibility, and other functional characteristics.
Material properties and their impact on the final product
The properties of ceramic materials used in 3D printing have a significant impact on the final product, influencing its performance, durability, and application field. Here are some key properties and their impact:
- Mechanical strength: Ceramics like alumina and zirconia offer high mechanical strength, making them suitable for applications requiring robustness, such as industrial components and medical implants.
- Thermal stability: Ceramic materials are known for their heat resistance, making them ideal for applications in high-temperature environments, like engine parts and exhaust systems.
- Biocompatibility: Ceramics such as hydroxyapatite and zirconia are biocompatible, meaning they can be used in medical applications without causing adverse reactions in the human body.
- Porosity: Some ceramics can be designed to be porous, useful for filtration and catalysis applications, where a large surface area is needed for chemical reactions.
- Electrical properties: Piezoelectric ceramics can convert mechanical energy into electrical energy, making them useful in sensors and actuators.
- Corrosion resistance: Ceramics are generally corrosion resistant, suitable for chemically aggressive environments.
- Electrical insulation: Ceramics are often used as electrical insulators, crucial for applications in the electronics industry.
The choice of ceramic material thus depends on the specific requirements of the application, and the material’s properties directly influence the functionality and durability of the final product.
What are the applications of ceramic 3D printing?
The main applications of ceramic 3D printing are found in the sectors of aerospace, medicine (implants and prosthetics), automotive, electronics, the luxury industry (jewelry, watches), and art/design for the fabrication of complex parts that are heat-resistant and corrosion-resistant.
Application sectors of ceramic 3D printing
Ceramic 3D printing finds applications across various sectors, leveraging the unique properties of ceramic materials. Here are some of the main application sectors:
- Medicine and healthcare: Used to create dental implants, bone prosthetics, and medical devices thanks to the biocompatibility and strength of ceramics.
- Aerospace and defense: Ceramic components are used for their thermal resistance and durability in extreme environments, such as engine parts and protection systems.
- Art and design: Artists and designers use ceramic 3D printing to create complex artworks and unique decorative pieces.
- Electronics: Ceramics are used to manufacture electronic components, insulators, and sensors due to their electrical properties and stability.
- Automotive industry: Ceramic parts are used for their wear resistance and thermal stability, notably in exhaust systems and braking components.
- Energy: Ceramics are employed in the production of fuel cells, batteries, and other energy devices due to their ionic conductivity and corrosion resistance.
- Filtration and catalysis: Porous ceramics are used for filtration and catalysis applications, where a large surface area is needed for chemical reactions.
- Research and development: Ceramic 3D printing is also used in scientific research to develop new materials and explore innovative applications.
These applications demonstrate the versatility of ceramic 3D printing and its potential to meet specific needs across diverse fields.
Concrete examples of use in each sector
Here are some concrete examples of ceramic 3D printing applications across different sectors:
- Medicine and healthcare:
- Dental implants: Creation of zirconia crowns and bridges for durable and aesthetic dental restorations.
- Bone prosthetics: Manufacturing hip and knee prostheses in alumina for strong and biocompatible implants.
- Aerospace and defense:
- Engine components: Production of ceramic turbine blades for aircraft engines, offering heat resistance and increased durability.
- Protection systems: Manufacturing thermal shields for spacecraft, able to withstand extreme temperatures.
- Art and design:
- Sculptures and artistic installations: Creating complex art pieces and ceramic wall decorations, leveraging the freedom of shape offered by 3D printing.
- Tableware and decorative objects: Production of vases, plates, and other custom decorative items.
- Electronics:
- Electronic components: Manufacturing ceramic printed circuit board substrates for high-frequency applications.
- Sensors and actuators: Use of piezoelectric ceramics for pressure sensors and actuators in electronic devices.
- Automotive industry:
- Exhaust systems: Production of ceramic exhaust components for better heat and corrosion resistance.
- Braking components: Manufacturing ceramic brake discs for improved performance and durability.
- Energy:
- Fuel cells: Use of ceramics for solid electrolytes in solid oxide fuel cells (SOFC).
- Batteries: Development of ceramic battery components to improve safety and performance.
- Filtration and catalysis:
- Industrial filters: Manufacturing ceramic filters for air and water purification in industrial environments.
- Catalysts: Use of porous ceramics as catalyst supports for chemical reactions.
- Research and development:
- New materials: Exploration of ceramic composites for innovative applications in various fields.
- Rapid prototyping: Use of ceramic 3D printing for prototype development in scientific research.
These examples highlight the diversity and potential of ceramic 3D printing across many fields, offering innovative and customized solutions.
What are the advantages of ceramic 3D printing?
The advantages of ceramic 3D printing include design freedom, the fabrication of complex parts, high thermal and chemical resistance, high precision, as well as the reduction of waste and manufacturing costs for small production runs.
Customization and complexity of shapes printed in 3D using ceramics
Ceramic 3D printing offers unique possibilities in terms of customization and complexity of shapes, allowing the creation of objects that would be difficult or even impossible to produce with traditional manufacturing methods. Here are some key aspects:
- Design freedom: 3D printing enables the creation of complex shapes and intricate geometries that cannot be produced by conventional molding or machining techniques. This includes lattice structures, internal cavities, and textured surfaces.
- Customization: Each piece can be personalized to meet specific needs, whether for medical applications such as custom implants, or for unique artistic objects. This allows precise adaptation to individual requirements.
- Topology optimization: 3D printing techniques enable the optimization of part topology, reducing weight while maintaining mechanical strength. This is especially useful in sectors like aerospace and automotive, where weight reduction is critical.
- Integration of multiple functions: It is possible to integrate several functions into a single part, such as internal cooling channels or support structures, improving the overall product performance.
- Reduction of assemblies: 3D printing allows manufacturing parts in one piece, reducing the need for multiple assemblies. This simplifies production and improves the reliability of components.
- Rapid prototyping: The ability to quickly produce prototypes enables fast iterations and design testing, accelerating the development process of new products.
Thanks to these advantages, ceramic 3D printing opens new horizons across various fields, allowing designers and engineers to push the boundaries of creativity and innovation.
Waste reduction and material efficiency in ceramic 3D printing
Ceramic 3D printing offers significant advantages in terms of waste reduction and material efficiency, contributing to more sustainable and cost-effective production. Here are some key points:
- Optimal material usage: Unlike subtractive manufacturing methods such as machining, where a large amount of material is lost as chips, ceramic 3D printing is an additive process. This means material is deposited only where needed, thereby reducing waste.
- Recycling of powders and resins: In technologies like Binder Jetting, unused ceramic powders can often be recycled and reused for subsequent prints, minimizing waste and lowering material costs.
- Reduction of raw material stock: 3D printing enables on-demand production, meaning parts can be made when needed, reducing the necessity to hold large stocks of raw materials and finished products.
- Structure optimization: Thanks to computer-aided design (CAD) and topology optimization, parts can be designed to use a minimum of material while maintaining strength and functionality. This helps reduce part weight and save materials.
- Reduction of production errors: 3D printing offers high precision and repeatability, lowering the risk of production errors and consequently reducing waste caused by defective parts.
- Energy resource savings: Although ceramic 3D printing may require thermal treatments such as sintering, the overall efficiency of the process can lead to reduced energy consumption compared to traditional manufacturing methods.
Cost reduction potential of ceramic 3D printing
Ceramic 3D printing offers significant potential for production cost reduction, providing economic advantages compared to traditional manufacturing methods. Here are some key aspects:
- Material waste reduction: As mentioned earlier, 3D printing is an additive process, meaning it uses only the necessary material to build the part, minimizing waste and lowering raw material costs.
- Fewer production steps: 3D printing enables the manufacturing of complex parts in a single step, eliminating the need for multiple fabrication, assembly, and finishing processes. This reduces labor costs and operational expenses.
- Customization without extra cost: Unlike traditional manufacturing methods, where customization can lead to significant additional expenses, 3D printing allows custom parts to be produced without a significant cost increase.
- Stock reduction: The ability to produce parts on demand reduces the need to maintain large stocks of finished products and raw materials, lowering storage and inventory management costs.
- Design optimization: Thanks to computer-aided design (CAD) and topology optimization, parts can be designed to use the minimum material while maintaining strength and functionality, reducing material costs.
- Rapid and iterative prototyping: 3D printing enables fast prototyping, accelerating the development of new products and reducing costs associated with design errors and market delays.
- Tooling cost reduction: 3D printing eliminates the need for expensive molds and tooling required for traditional manufacturing methods, which is especially advantageous for small production runs.
- Energy efficiency: Although ceramic 3D printing may require thermal treatments, the overall efficiency of the process can lead to a reduction in energy consumption compared to traditional manufacturing methods.
What are the challenges and limitations of ceramic 3D printing?
The main challenges and limitations of ceramic 3D printing are the fragility of parts before sintering, the complexity of post-processing, the high cost of materials and equipment, the slow printing speed, and the difficulty of large-scale implementation.
Technical problems and material constraints of ceramic 3D printing
Ceramic 3D printing, although offering many advantages, also presents technical problems and material constraints that can limit its application and effectiveness. Here are some of the main challenges:
- Fragility of materials: Ceramics are inherently fragile and sensitive to cracks, which can cause problems during printing and post-processing. This requires careful handling to avoid damage.
- Necessary post-processing: Most ceramic 3D printed parts require post-processing, such as sintering, to achieve their final mechanical properties. This process can be energy-intensive and may cause deformations or cracks.
- Size limitation of parts: Due to machine constraints and risks of deformation during sintering, the size of ceramic 3D printed parts is often limited.
- Resolution and surface finish: Although ceramic 3D printing can produce fine details, the resolution and surface finish may not be as good as with traditional manufacturing methods, potentially requiring additional finishing steps.
- Design constraints: Designing parts for ceramic 3D printing must consider process constraints, such as avoiding large overhangs and providing support structures for complex geometries.
- Cost of materials and equipment: Ceramic materials and specialized 3D printing equipment can be expensive, which may limit the accessibility of this technology for some applications.
- Production speed: Ceramic 3D printing can be slow compared to other manufacturing methods, limiting its use for mass production.
- Anisotropic properties: 3D printed parts may exhibit anisotropic properties, meaning their mechanical properties vary depending on the printing direction, which can affect performance.
- Material compatibility: Not all ceramic materials are suitable for 3D printing, and developing new compatible materials with 3D printing technologies is an active research area.
These technical challenges and material constraints require ongoing research and innovation to improve ceramic 3D printing processes and expand their application scope.
Costs and accessibility of ceramic 3D printing technologies
The costs and accessibility of ceramic 3D printing technologies can vary significantly depending on several factors, which influence their adoption across different sectors. Here are some key points to consider:
- Equipment cost: Ceramic 3D printers are generally more expensive than standard 3D printers due to the complexity of the involved technologies. Prices can range from tens of thousands to several hundred thousand euros, depending on the size, precision, and capabilities of the machine.
- Material cost: Ceramic materials used in 3D printing, such as powders and resins, can be expensive. Specialized materials like zirconia and alumina are often costlier than standard materials used in other types of 3D printing.
- Maintenance and operating costs: Ceramic 3D printers require regular maintenance to ensure proper functioning. This may include replacement of worn parts, machine calibration, and staff training, which add to the operating costs.
- Post-processing: Post-processing steps like sintering may require additional equipment and significant energy costs, increasing the overall production cost.
- Accessibility: Due to the high costs of equipment and materials, ceramic 3D printing is often more accessible to large companies and research institutions than to small businesses or individuals. However, the rise of online 3D printing services and shared manufacturing centers can make this technology more accessible.
- Training and expertise: Effective use of ceramic 3D printing technologies requires technical expertise and specialized training, which can represent an additional investment of time and resources for organizations looking to adopt this technology.
- Innovation and development: Ongoing technological advances and continuous innovation in ceramic 3D printing may lead to cost reductions and improved accessibility in the future. Current research on new materials and processes could make this technology more affordable and widely available.
Challenges related to the durability and strength of parts produced by ceramic 3D printing
Parts produced by ceramic 3D printing face specific challenges in terms of durability and strength, which can influence their performance and applicability. Here are some of the main challenges:
- Inherent fragility: Ceramics are naturally fragile and sensitive to shocks and cracks. This fragility can be exacerbated by the 3D printing process, where microscopic defects can form and weaken the structure.
- Anisotropy of properties: 3D printed parts may exhibit anisotropic properties, meaning their strength and durability can vary depending on the printing direction. This can cause structural weaknesses in certain orientations.
- Deformations during sintering: The sintering process, required to densify ceramic parts, can cause deformations and residual stresses, affecting the dimensional accuracy and mechanical strength of the final parts.
- Porosity: 3D printed parts may contain pores and internal defects, which can reduce their mechanical strength and durability. Managing porosity is crucial to achieve parts with optimal properties.
- Fatigue resistance: Ceramics can be sensitive to fatigue, where cyclic loads can cause crack propagation and premature failure. This is especially concerning for applications subjected to dynamic loads.
- Thermal stability: While ceramics are generally stable at high temperatures, rapid temperature changes can induce thermal stresses and cracks, affecting the durability of parts.
- Wear resistance: In applications where parts face friction and abrasion, the wear resistance of 3D printed ceramics can be a challenge, requiring surface treatments or coatings.
- Material compatibility: Not all ceramic materials are suitable for 3D printing, and developing materials with better strength and durability is an active area of research.
To overcome these challenges, continuous research and innovations are needed to improve ceramic 3D printing processes, optimize processing parameters, and develop new materials with enhanced properties.
What is the future of ceramic 3D printing?
The future of ceramic 3D printing looks promising thanks to technological advances, increased automation, diversification of materials, and its growing integration into the medical, aerospace, and high-precision industries.
Innovations and ongoing research in ceramic 3D printing
Research and innovation in the field of ceramic 3D printing are dynamic, aiming to overcome current challenges while expanding application possibilities. Here are some of the main innovations and research directions underway:
- Development of new materials: Researchers are working on formulating new ceramic and composite materials suited for 3D printing, offering better mechanical properties, improved heat resistance, and increased durability.
- Improvement of printing technologies: Advances are being made in printing technologies such as stereolithography (SLA), selective laser sintering (SLS), and binder jetting to improve precision, speed, and quality of printed parts.
- Optimization of post-processing: Research focuses on optimizing sintering and other thermal treatments to reduce deformations, improve part density, and minimize residual stresses.
- Integration of modeling and simulation: The use of digital modeling and simulation to predict and optimize the properties of 3D printed parts, as well as to understand failure mechanisms, is an active research area.
- Multi-material 3D printing: Researchers are exploring the possibility of printing with multiple materials simultaneously, enabling parts with varied properties and integrated functionalities.
- Improvement of durability and strength: Efforts are underway to enhance fatigue resistance, impact resistance, and thermal stability of ceramic 3D printed parts to broaden their range of applications.
- Development of repair and recycling techniques: Research on techniques for repairing damaged ceramic parts and recycling used ceramic materials is ongoing to improve durability and reduce waste.
- Biomedical applications: Ceramic 3D printing is increasingly used for biomedical applications, such as creating scaffolds for tissue engineering and custom implants, due to its biocompatibility and ability to mimic biological structures.
- Integration of artificial intelligence: The use of AI and machine learning to optimize printing parameters, predict material properties, and automate part design is an emerging field.
These ongoing innovations and research efforts promise to expand the capabilities of ceramic 3D printing, making the technology more accessible, efficient, and versatile for a growing range of applications.
Future perspectives and trends for ceramic 3D printing
The future perspectives and trends for ceramic 3D printing are promising, with technological advances and innovations that could transform various sectors. Here are some key potential trends and developments:
- Material improvement: The development of new ceramic and composite materials offering enhanced properties such as better strength, greater durability, and improved biocompatibility is a major trend. This could expand applications in fields like aerospace, medicine, and electronics.
- Advanced printing technologies: The evolution of printing technologies such as stereolithography (SLA), selective laser sintering (SLS), and binder jetting will improve precision, speed, and quality of printed parts.
- Integration of artificial intelligence (AI): The use of AI and machine learning to optimize printing parameters, predict material properties, and automate part design is an emerging trend that could revolutionize the manufacturing process.
- Multi-material 3D printing: The ability to print with multiple materials simultaneously will enable the creation of parts with varied properties and integrated functionalities, opening new possibilities for complex applications.
- Biomedical applications: Ceramic 3D printing is increasingly used for biomedical applications, such as creating scaffolds for tissue engineering and custom implants, thanks to its biocompatibility and ability to mimic biological structures.
- Durability and recycling: Research on techniques for repairing damaged ceramic parts and recycling used ceramic materials is ongoing to improve durability and reduce waste, contributing to a circular economy.
- Mass customization: The ability to produce customized parts at scale without significant cost increases is a trend that could transform sectors like medicine, automotive, and aerospace.
- Collaboration and partnerships: Collaboration between research institutions, technology companies, and end-user industries is essential to accelerate innovation and develop new applications for ceramic 3D printing.
- Education and training: Developing specialized educational programs and training to prepare the next generation of professionals in ceramic 3D printing is crucial to support growth and innovation in the field.
Conclusion : Ceramic 3D printing
Ceramic 3D printing represents a revolutionary technology that opens new perspectives across various sectors, from medicine to aerospace, as well as art and electronics. Thanks to its ability to produce complex, customized, and durable parts, this technology offers significant advantages compared to traditional manufacturing methods.
However, despite its many strengths, ceramic 3D printing faces technical challenges and material constraints, such as the fragility of ceramics, the need for post-processing, and limitations in terms of size and resolution. The high costs of equipment and materials can also limit its accessibility.
Nonetheless, ongoing innovations and active research in this field promise to overcome these obstacles. The development of new materials, improvement of printing technologies, integration of artificial intelligence, and exploration of new biomedical applications are all avenues that could transform ceramic 3D printing into an even more powerful and versatile technology.
In the future, ceramic 3D printing could play a key role in mass customization, sustainability, and innovation across various sectors, thereby contributing to a more circular economy and a more technologically advanced society. With continuous progress and collaborations between research institutions and industries, the future prospects for ceramic 3D printing are broad and promising.
Picture by Pikisuperstar by Freepik.
The articles published on Imprimy.com are for informational purposes only. They are intended to provide general advice and information related to 3D printing. Imprimy.com cannot be held responsible for the results obtained or the consequences arising from the application of the shared information. We recommend always checking the specific instructions for your hardware and materials before use.