In Ireland, Harcourt Technologies Ltd (HTL.tech) has completed Europe’s first 3D-printed social housing project compliant with ISO/ASTM 52939:2023 standards. With a 35% reduction in construction time, this project represents a major milestone in sustainable building practices.
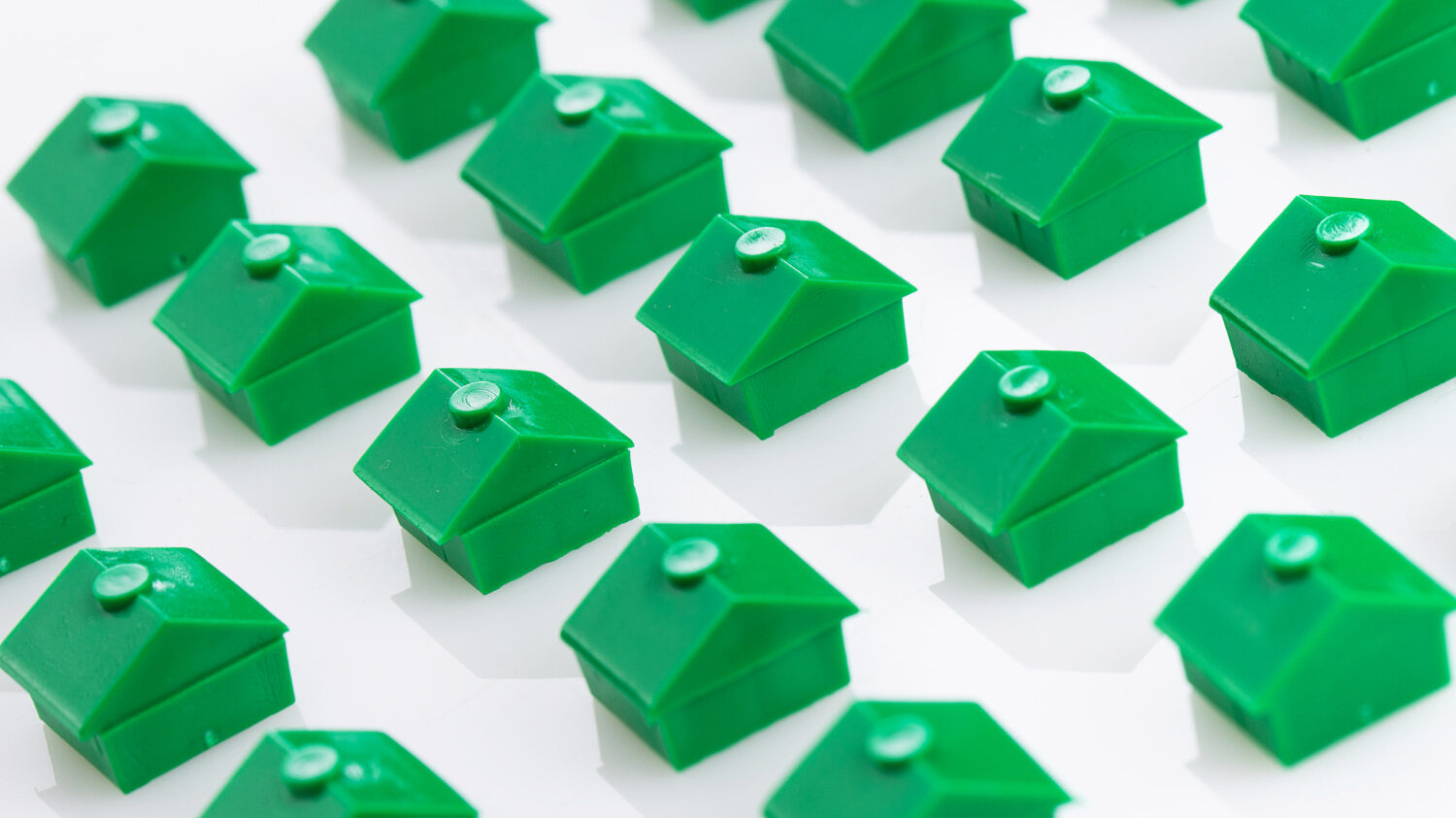
A technical and regulatory innovation for building construction in Europe
HTL.tech completed the construction of social housing in Grange Close in just 132 days, using the BOD2 3D printer from COBOD International. This achievement resulted in a 35% reduction in the usual construction timeline, which typically exceeds 200 days. The double-cavity load-bearing walls, printed without reinforcement, comply with EN206 and Eurocode 6 standards, ensuring structural solidity and increased durability. The superstructure was completed in just 12 days, showcasing the efficiency of 3D printing in construction.
Harcourt Technologies Ltd recognized for technological advancements
HTL.tech was awarded by the National Standards Authority of Ireland for integrating international standards into its 3D printing processes. Following this success, the company enhanced its printing capacity, increasing volumetric output by 40%. This improvement now allows print times to be reduced to just 9 days. In parallel, industry innovations such as the launch of the BOD3 printer for large-scale projects and the development of SEAM technology for facade components further demonstrate the potential of 3D printing in construction.
Picture by Freepik.
The articles published on Imprimy.com are for informational purposes only. They are intended to provide general advice and information related to 3D printing. Imprimy.com cannot be held responsible for the results obtained or the consequences arising from the application of the shared information. We recommend always checking the specific instructions for your hardware and materials before use.