In Lünen, Germany, the first residents have moved into a six-unit apartment building entirely 3D-printed. The construction of the building took only 118 hours, while the entire project lasted about 1.5 years. This innovative initiative paves the way for broader integration of 3D printing in the construction sector.
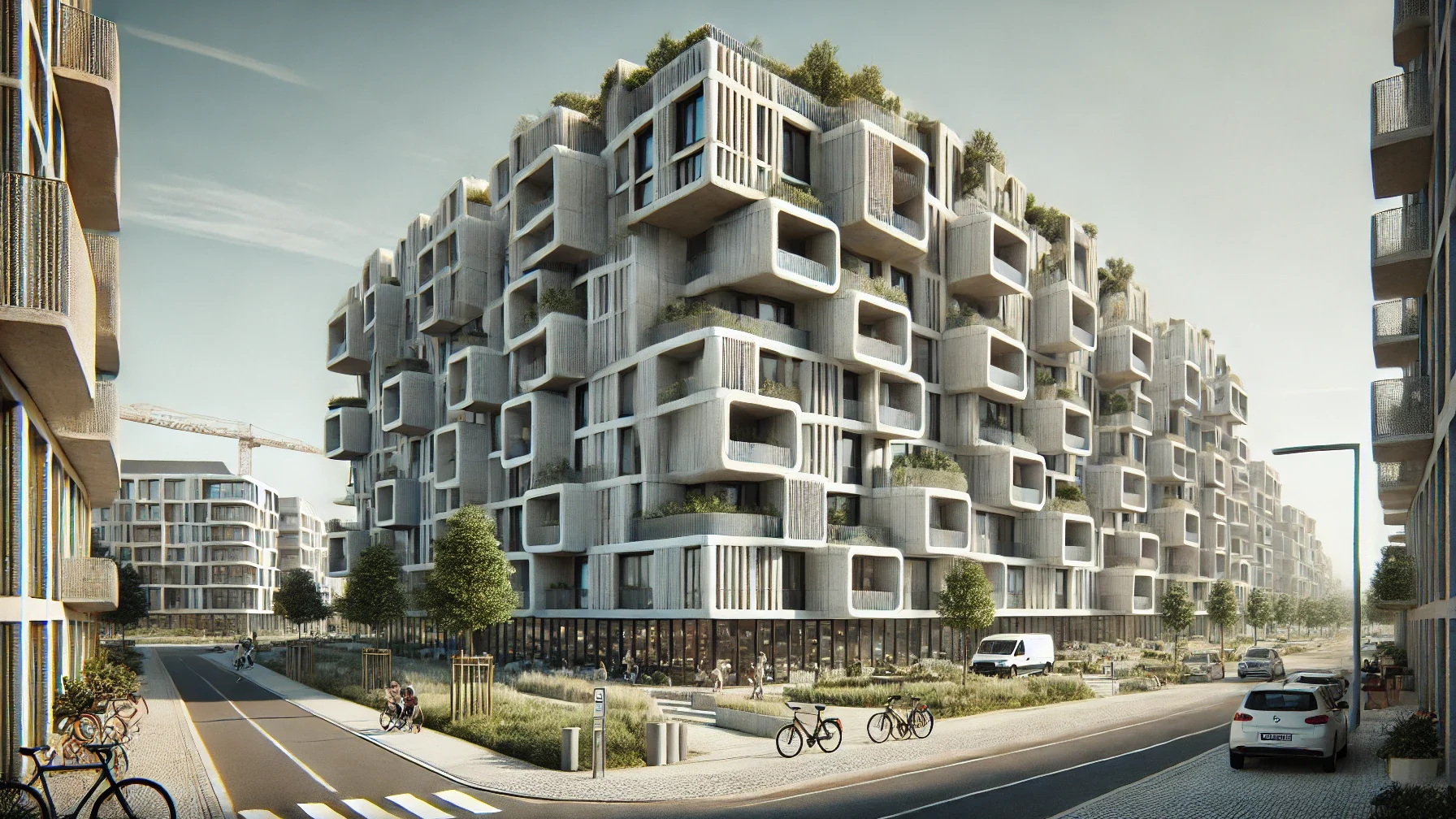
High Initial Costs but Promising Optimization
Led by the WBG Lünen cooperative, the project aimed to demonstrate that 3D printing can be used for standard, functional housing. The total cost amounted to €1.9 million, making it more expensive than conventional construction—a cost justified by its experimental nature. However, according to Jan Hische, a board member of the cooperative, significant savings could be achieved in the future through process standardization.
Affordable Housing for Tenants
Despite the high construction cost, rents remain affordable at six euros per square meter, ranging from €366 to €486 per apartment. Residents appreciate the uniqueness of their new home, though some wished that more interior elements, like the bathroom, had the distinctive 3D-printed housing look. This project is part of a growing trend in social housing, with similar initiatives underway in Ireland, Australia, and beyond.
Image generated by DALL·E, an artificial intelligence model developed by OpenAI.
The articles published on Imprimy.com are for informational purposes only. They are intended to provide general advice and information related to 3D printing. Imprimy.com cannot be held responsible for the results obtained or the consequences arising from the application of the shared information. We recommend always checking the specific instructions for your hardware and materials before use.