Would you like to know how to create effective and strong joints in your 3D prints? Imprimy is here to meet all your needs.
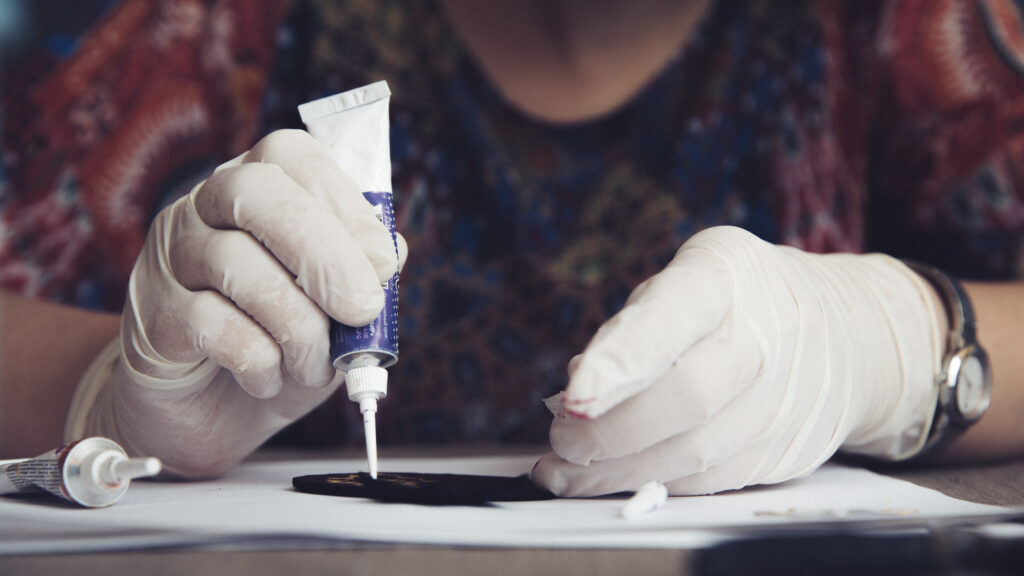
What is a joint in 3D printing?
A joint represents a connection point between different elements of your 3D prints. Their presence helps provide a clear and specific structure to your 3D prints during the finishing process.
The definition of joints in 3D printing
The joints of 3D prints are defined as the connection points between different parts of a printed object, allowing for the creation of more complex and functional structures while maintaining their integrity and strength. These joints can vary depending on the chosen assembly methods, such as snap-fit, screw, adhesive, or welded joints, each having its own characteristics and applications.
Joints play a crucial role in the durability of the assembly, influencing the object’s ability to bear mechanical loads and withstand usage constraints. Proper design of joints is therefore essential to optimize the strength and functionality of printed parts, taking into account the materials used and the specific requirements of the application.
The role of joints in 3D printed structures
Joints in 3D printed structures serve as essential connection points that enable multiple parts to be securely assembled into a single, functional object. They help to create more complex geometries and allow for modular designs, where individual components can be easily joined, replaced, or modified.
Joints also contribute significantly to the overall strength and stability of the structure by distributing mechanical stresses and ensuring the integrity of the printed parts during use. Properly designed joints enhance the durability and performance of 3D printed objects, making them suitable for a wide range of applications, from simple models to highly functional, load-bearing structures.
The differences between joints in 3D printing and assemblies
Joints in 3D printing refer specifically to the connection points designed within or between parts of a single or multi-part printed object. They are often integral to the printed structure and focus on creating seamless or functional connections, such as snap-fit joints, dovetails, or threaded inserts. Joints prioritize precision, material integrity, and the efficiency of combining parts during or after printing.
Assemblies, on the other hand, involve the process of combining multiple components—whether 3D printed or made from other materials—into a complete system or product. Assemblies often include additional elements like screws, adhesives, or external fasteners and require external tools or processes to complete. Assemblies may also address broader considerations, such as dynamic movement between parts, multi-material integration, compliance with specific mechanical or aesthetic requirements.
In summary, joints are a subset of design features within 3D printing, focusing on part-to-part connections, while assemblies encompass the broader process of constructing and integrating multiple components into a functional whole.
What types of joints exist in 3D printing?
There are different types of joints that can be adapted to your 3D prints.
Interlocking Joints
Interlocking joints are designed to connect 3D printed parts by fitting them together through complementary shapes, creating a secure and often tool-free connection. These joints rely on precise tolerances and geometric features, such as tabs, slots, or dovetails, to ensure a snug fit.
Advantages:
- Easy assembly without the need for adhesives or fasteners.
- Reversible in many cases, allowing disassembly and reassembly.
- Provides strong lateral stability.
Applications:
- Modular designs requiring easy assembly.
- Prototypes with adjustable configurations.
- Functional parts where aesthetics and seamless connections are important.
Proper design and calibration during printing are crucial to achieving effective interlocking joints, as they depend heavily on the accuracy of the 3D printer and the material used.
Screw Joints
Screw joints are connections that use screws or bolts to fasten 3D printed parts together, typically involving internal or external threads designed directly into the print or combined with threaded inserts.
Advantages:
- Provide strong, secure, and reusable connections.
- Allow for easy disassembly and reassembly.
- Suitable for parts subjected to mechanical loads.
Applications:
- Assemblies requiring frequent maintenance or adjustments.
- Structures that need high strength and durability.
- Combining 3D printed parts with non-printed components.
Tips for Design:
- Use threaded inserts for improved durability, especially with plastic parts.
- Ensure accurate tolerances to avoid misalignment.
- Reinforce the area around the screw holes to prevent cracking under load.
Screw joints are versatile and reliable, making them a popular choice for functional 3D printed assemblies.
Adhesive Joints
Adhesive joints use glues, epoxies, or other bonding agents to securely connect 3D printed parts. This method creates a strong and permanent connection between components.
Advantages:
- Simple and cost-effective.
- Ideal for joining irregular or complex shapes.
- Suitable for materials that don’t easily support mechanical fasteners.
Applications:
- Permanent assemblies where disassembly is not required.
- Prototypes or finished parts requiring seamless connections.
- Combining 3D printed parts with non-printed materials.
Tips for Use:
- Surface Preparation: Clean and sand the surfaces to improve adhesion.
- Adhesive Choice: Select adhesives compatible with the printing material (e.g., cyanoacrylate for PLA or ABS).
- Application: Apply evenly and avoid excessive amounts to prevent weak bonds or visible residue.
- Curing Time: Allow adequate curing time for maximum bond strength.
Adhesive joints are an excellent option for achieving durable and aesthetic connections, particularly when mechanical fasteners are impractical or undesirable.
Welded Joints
Welded joints involve fusing 3D printed parts together using heat, friction, or chemical solvents to create a strong, seamless connection. This method is particularly effective for thermoplastic materials like PLA, ABS, or PETG.
Advantages:
- Produces a durable, often seamless bond.
- Ideal for joining large or multi-part prints into a single unit.
- Eliminates the need for additional fasteners or adhesives.
Types of Welding in 3D Printing:
- Heat Welding:
- Uses a soldering iron or heat gun to melt the edges of parts and fuse them together.
- Commonly used for PLA and ABS.
- Friction Welding:
- Involves rotating a plastic rod at high speed to generate heat and bond parts.
- Provides precise control and strong bonds.
- Chemical Welding:
- Uses solvents like acetone (for ABS) to dissolve and fuse the material at the joint.
- Creates a seamless connection when properly applied.
Applications:
- Large parts printed in multiple sections due to size constraints.
- Functional prototypes or final parts requiring high strength.
- Artistic or decorative pieces where seamless joints are aesthetically important.
Tips for Successful Welding:
- Ensure clean and properly aligned surfaces before welding.
- Practice on scrap material to perfect the technique.
- Use consistent heat or pressure to avoid uneven bonds.
Welded joints are a reliable and effective method for creating strong, permanent connections in 3D printed projects, especially when aesthetic and structural integrity are critical.
Materials and Their Influence on Joints in 3D Printing
The choice of material for 3D printing significantly affects the strength, durability, and type of joints that can be effectively used in an assembly. Different materials have unique mechanical properties and behavior under stress, which influence joint performance.
The impact of different printing materials on the performance of joints
The impact of different printing materials on joint performance is crucial to consider when designing and manufacturing 3D objects, as each material has distinct mechanical, thermal, and chemical properties that influence the strength and durability of joints. For example, materials like ABS and PETG offer good tensile strength and some flexibility, which can enhance joint performance, especially when using screws or welding, by absorbing stress without cracking.
On the other hand, more brittle materials like PLA, while easy to print, may be more prone to breaking at joint points, especially if the design does not account for their limitations. Additionally, adhesion between surfaces is also influenced by the material; for instance, glued joints require specific adhesives suited to the chemical properties of the materials, while welded joints require thermal compatibility to ensure effective fusion.
In summary, the choice of printing material is essential for optimizing joint performance, and careful evaluation of material properties helps ensure the robustness and functionality of 3D printed assemblies.
Comparisons between Plastics, Resins, and Metals in 3D Printing
The comparisons between plastics, resins, and metals in 3D printing reveal significant differences that influence the material choice based on the specific project requirements. Plastics, such as ABS and PLA, are widely used due to their ease of printing, lightweight nature, and affordable cost. They offer good flexibility and adequate strength for many applications but may be less suitable for demanding environments due to their sensitivity to heat and humidity.
Resins, often used in stereolithography (SLA), allow for very fine details and smooth surface finishes, making them ideal for prototypes or aesthetic parts. However, they can be more fragile than plastics and often require post-processing to enhance their durability.
In contrast, metals like stainless steel or aluminum provide exceptional strength and long-term durability, making them the preferred choice for industrial applications or parts subjected to high mechanical stress. However, their high cost and specific technical requirements for printing, such as high temperatures and specialized equipment, limit their use.
In summary, the choice between plastics, resins, and metals depends on the desired characteristics, required performance, and budget allocated for the 3D printing project.
Best Practices for Choosing Materials Based on Joints in 3D Printing
The best practices for selecting materials based on joints in 3D printing involve a thorough assessment of the functional, mechanical, and environmental requirements of your project. First, it’s essential to consider the mechanical strength needed for the joints, as materials like ABS and PETG offer better toughness and impact resistance compared to more fragile materials like PLA.
Next, consider the type of joint you plan to use; for example, welded joints require compatible thermoplastic materials that can be effectively fused, while glued joints should match the chemical properties of the chosen adhesive. It’s also important to consider the environment in which the object will be used; materials resistant to heat or humidity, such as composites or certain technical plastics, may be necessary for specific applications.
Finally, it’s recommended to conduct performance tests to validate the material choice, by testing prototypes to identify potential issues related to the joints before large-scale production. By following these best practices, you can optimize the durability and functionality of your 3D printed assemblies while meeting the specific requirements of your project.
What are the design techniques for effective joints?
There are various techniques that allow you to verify the proper functioning of the joints integrated into your 3D prints.
The importance of design on joints
The importance of design on joints in 3D printing cannot be overstated, as careful planning and a thoughtful approach can significantly influence the performance, durability, and functionality of assemblies. Proper design allows for the optimization of connection points, taking into account tolerances and specific dimensions to ensure a perfect fit between parts, whether using snap-fit joints, screws, or welding. Furthermore, choosing the most appropriate joint type based on the materials used and the mechanical stresses the object will face is crucial; for example, robust joints may be required for industrial applications, while lighter designs may suffice for prototypes.
Particular attention to the arrangement of joints can also facilitate the printing process by minimizing the need for supports and reducing manufacturing time. By integrating these considerations from the design phase, you can not only improve the quality of assemblies but also optimize the overall performance of 3D printed parts, contributing to the success of your projects.
The use of 3D modeling software to optimize joints
The use of 3D modeling software to optimize joints in 3D printing is essential for ensuring the quality and robustness of assemblies. These tools allow for the precise design and simulation of joints, considering dimensions, tolerances, and appropriate connection types, making it easier to anticipate potential issues before the printing phase. With advanced features like stress simulation and force analysis, the software enables the evaluation of joint performance under various conditions, allowing for design adjustments to improve strength and durability.
Additionally, these tools facilitate the integration of specific features, such as channels for inserting screws or snap-fit mechanisms, while optimizing the printing process by minimizing the need for supports and improving material efficiency. In summary, the use of 3D modeling software is a crucial step in designing 3D printed assemblies, ensuring functional and reliable joints while maximizing the performance of the produced parts.
Considerations for joint placement during design
Considerations for joint placement during the design of 3D printed objects are crucial for ensuring the integrity and functionality of assemblies. First, it is important to position the joints in areas that minimize mechanical stresses, avoiding potential weak points where forces may accumulate, which could lead to failures. Next, the choice of joint type should match the intended use of the object; for example, screw joints may be preferred for parts that require frequent disassembly, while glued joints may be suitable for structures requiring aesthetic finishes.
Moreover, the direction of printing and the configuration of the part must be taken into account, as these can affect the strength of the joints; strategic placement can also help reduce print defects and improve surface quality. Finally, the accessibility of joints for assembly and maintenance should be considered during design, ensuring that assembly operations are simple and efficient. By integrating these considerations from the early stages of design, you can optimize joint performance and ensure the durability of 3D printed parts.
Conclusion: 3D Printing Joints
In conclusion, joints in 3D printing play a pivotal role in ensuring the strength, durability, and functionality of assembled parts. Whether through snap-fit, screw, adhesive, or welded joints, careful design, material selection, and placement are essential for achieving reliable and robust connections.
By using 3D modeling software to simulate and optimize joint designs and considering factors such as mechanical stresses, material compatibility, and ease of assembly, you can significantly improve the quality of your printed parts. Properly executed joints not only contribute to the structural integrity of 3D printed objects but also enhance their overall performance, making them a crucial aspect of successful 3D printing projects.
Picture by azerbaijan_stockers from Freepik.
The articles published on Imprimy.com are for informational purposes only. They are intended to provide general advice and information related to 3D printing. Imprimy.com cannot be held responsible for the results obtained or the consequences arising from the application of the shared information. We recommend always checking the specific instructions for your hardware and materials before use.
Check our other contents about 3D prints finishing:
Color 3D printing
Would you like to learn more about color 3D printing and its various applications? At…
Large-format 3D printing
Are you wondering about large-format 3D printing and the possibilities it can offer? At Imprimy,…
Remove the supports from a 3D print
To learn more about 3D printing supports and how to remove them properly, Imprimy.com is…