Would you like to discover everything you need to know about layer height in 3D printing? At Imprimy.com, we are here to answer all your questions.
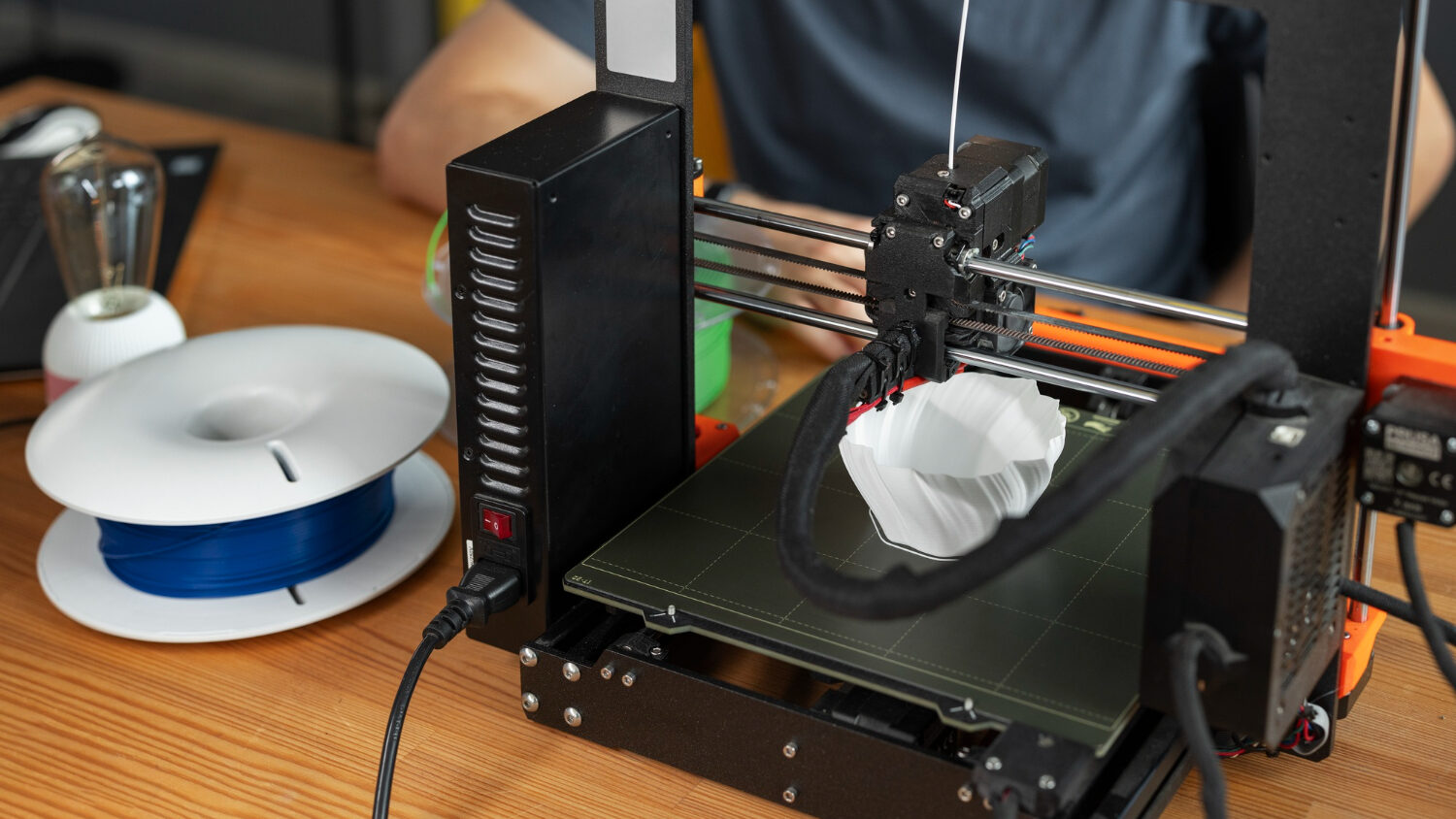
What is layer height?
Layer height is the thickness of each thin layer of filament deposited by the 3D printer to gradually build an object. It is typically measured in millimeters and determines the resolution of the print, thus affecting the quality, speed, and precision of the final object.
Technical definition of layer height
Layer height in 3D printing refers to the thickness of each successive layer of material deposited to form an object. It corresponds to the vertical resolution of the print. The lower the layer height, the finer and more precise the details of the part will be, but the longer the printing time will be. Conversely, a higher layer height allows for faster printing, at the expense of fine details and surface quality.
This parameter is defined in the slicing software and should be adjusted based on the specific printing requirements, the type of filament used, and the diameter of the printer’s nozzle.
Units of measurement for layer height
Layer height in 3D printing is typically measured in millimeters (mm) or microns (µm), where 1 micron equals 0.001 mm. Common values range from 0.05 mm (50 µm) for highly detailed prints to 0.3 mm (300 µm) or more for faster, less precise prints. The choice of unit depends on the context: slicing software and printer settings mainly use millimeters, while advanced technical specifications, especially in industrial settings, may be expressed in microns for greater precision.
Setting layer height in a slicer
To configure layer height in a slicer, you need to open your slicing software and access the print settings. In the section dedicated to quality or layers, you will find the “Layer Height” option, expressed in millimeters. You can select a value that suits your needs: a low height (e.g., 0.1 mm) for detailed rendering or a higher height (e.g., 0.3 mm) for faster printing. Some slicers also offer the option of variable layer height, which automatically adjusts this value based on the model’s details to optimize both quality and printing time. Once you’ve made your choice, simply start slicing and send the generated file to your 3D printer.
What is the influence of layer height on 3D printing?
Layer height directly affects the precision, speed, and quality of 3D printing: a smaller layer height improves resolution and fine details, but increases printing time and material consumption, while a larger height reduces time and printing costs but may result in a less smooth and less precise finish.
The impact on print quality
Layer height has a direct impact on print quality, especially on the fineness of details and the appearance of surfaces. A low layer height (e.g., 0.1 mm) allows for more precise objects with sharper contours and less visible layers, which is ideal for prints requiring careful aesthetic rendering or fine details. On the other hand, a higher layer height (e.g., 0.3 mm or more) results in more pronounced layers, which can give a less smooth appearance and accentuate the stair-stepping effect on inclined or curved surfaces. This parameter also influences the quality of small elements and engraved text, which will be better defined with finer layers. Thus, the choice of layer height depends on the balance sought between visual precision and printing speed.
The impact on print time
Layer height directly affects print time, as it determines the total number of layers required to build a part. A low layer height (e.g., 0.1 mm) significantly increases print time, as the printer must deposit more layers to reach the final height of the object. In contrast, a higher layer height (e.g., 0.3 mm) reduces this number, speeding up the process at the expense of less detailed precision. For example, a 50 mm tall part will require 500 layers with a thickness of 0.1 mm, compared to only 167 layers with a thickness of 0.3 mm, which can cut the print time by a factor of three. Therefore, the choice of layer height should be adjusted based on the desired level of detail and time constraints.
The impact on the mechanical strength of parts
Layer height affects the mechanical strength of 3D printed parts, primarily due to the adhesion between layers. A low layer height (e.g., 0.1 mm) promotes better fusion between the layers, reducing the risk of delamination and improving strength in the direction perpendicular to the layers. However, it can also lead to an increase in defects related to excessive extrusion or overheating. In contrast, a higher layer height (e.g., 0.3 mm) may make the part more fragile along the Z-axis, as the layers have a smaller contact surface and adhere less well to each other. However, in certain configurations, a higher layer height combined with an adjusted extrusion rate can improve overall strength by minimizing internal defects. Therefore, the choice of layer height should be made based on the part’s mechanical constraints and its print orientation.
How to choose the right layer height based on the needs?
To choose the right layer height based on the needs, opt for a smaller height (0.1 mm) for detailed and precise prints, such as decorative parts or prototypes, and a larger height (0.2-0.3 mm) for simpler objects or functional prototypes where print speed and strength are a priority.
A fine layer height (≤ 0.1 mm)
A fine layer height (≤ 0.1 mm) is ideal for prints requiring a high level of detail and smooth surfaces. It allows for parts with less visible layers, improving the aesthetics and precision of small elements like engravings or complex curves. This fineness is especially useful for figurines, jewelry, or detailed prototypes. However, it significantly increases print time, as the printer must deposit a larger number of layers to reach the final height of the object. Additionally, a very low layer height requires precise printer calibration and a clean nozzle to avoid clogging risks. This setting should therefore be prioritized when quality takes precedence over speed.
A standard layer height (0.15 – 0.2 mm)
A standard layer height, ranging from 0.15 to 0.2 mm, represents a good balance between print quality and execution speed. It allows for parts with a satisfactory level of detail while maintaining a reasonable print time. This thickness is ideal for most 3D prints, whether prototypes, functional parts, or decorative objects. With a height of 0.2 mm, the layers remain visible but relatively discreet, while a height of 0.15 mm further improves the finish while maintaining an acceptable print speed. This setting is often recommended by default in slicers, as it offers a good balance between precision and efficiency.
A high layer height (≥ 0.3 mm)
A high layer height (≥ 0.3 mm) significantly speeds up the print process by reducing the total number of layers required to make a part. It is particularly suitable for prints where speed takes precedence over fine details, such as prototypes, large parts, or functional objects that do not require a smooth finish. However, this height results in more visible layers, giving a less aesthetic appearance to the surfaces, and may also reduce adhesion between layers, potentially affecting strength along the Z-axis. To ensure good prints with a high layer height, it is recommended to use a wider diameter nozzle (e.g., 0.6 mm or 0.8 mm) to ensure more consistent extrusion and better mechanical strength.
What are the factors influencing the choice of layer height?
Factors influencing the choice of layer height include the desired level of detail, print speed, the type of filament used, the final use of the part, as well as the capabilities of the printer and the strength requirements of the object.
The type of printer and nozzle used
The type of printer and nozzle used directly influence the quality and speed of 3D printing. FDM (Fused Deposition Modeling) printers are the most common, and the nozzle size plays a crucial role in defining print details. Standard nozzles are usually 0.4 mm, but smaller nozzles allow for finer and more detailed layers, while larger nozzles speed up printing but reduce precision. The choice of printer, whether filament-based, resin-based, or another technology, as well as the nozzle, should be tailored to the project requirements to ensure optimal results.
The type of filament used
The type of filament used in 3D printing has a significant impact on the quality, durability, and final properties of the printed object. The most common filaments are PLA, PETG, ABS, and TPU, each with distinct characteristics.
- PLA, for example, is easy to print and provides a good surface finish, but it is less resistant to heat and mechanical stress.
- ABS is more robust and durable but requires higher temperatures for printing.
- PETG combines the ease of handling of PLA with the strength of ABS, while TPU is a flexible filament, ideal for objects that require some elasticity.
The choice of filament should consider the specific properties needed for the final object, which also affects the print speed and layer height chosen.
The final use of the part
The final use of the 3D printed part greatly influences the choice of print settings, such as layer height, filament type, and printer settings. For example, if the object is intended to be functional or subjected to mechanical stresses, a robust filament like ABS or PETG should be prioritized, along with a larger layer height to speed up printing while maintaining adequate strength. In contrast, for decorative parts or prototypes where fine details are important, a filament like PLA and a smaller layer height should be chosen to achieve a more precise and smoother finish. The final use will also determine whether features like flexibility, heat resistance, or transparency are necessary, thus guiding technical choices to ensure the part’s performance and durability.
What practical tips to apply for setting the right layer height?
To properly set the layer height, it is recommended to choose a height suitable for the desired resolution, start with a value of 0.2 mm for a good balance between quality and speed, and adjust based on the type of filament and the final use of the part.
Tips for optimizing slicing in the slicer
To optimize slicing in the slicer and improve print quality while reducing time and costs, several tips can be applied. First, adjusting the layer height based on the desired level of detail allows for a good balance between quality and speed; a larger layer height reduces print time, but a smaller one improves precision. Next, adjusting the infill settings can help lighten the object while maintaining its strength: a lower infill percentage reduces time and filament consumption, but care must be taken not to compromise strength.
The choice of print speed is also crucial: slower speeds improve layer quality and minimize defects but may increase print time. Additionally, using well-configured and suitable supports avoids adhesion issues or geometry errors, especially for complex parts. Finally, using retraction and optimizing the movement of the print head helps reduce stringing and blobs, ensuring better finishes.
Avoid common mistakes
To avoid common mistakes in 3D printing, several precautions must be taken. First, ensure that the print bed is properly leveled, as improper leveling can lead to poor adhesion of the first layer and warping throughout the part. Next, check that the nozzle and bed temperatures are suitable for the filament being used, as incorrect temperatures can cause clogs in the nozzle or poor surface quality.
It is also important to choose an appropriate print speed: too high a speed can result in under-extrusion or precision issues, while too slow a speed can unnecessarily extend print times. Additionally, keep an eye on filament retraction, as improper settings can cause oozing (undesired strings) or nozzle blockages.
Finally, don’t forget to check that the filament is clean and free from moisture, as moisture-absorbing filament can cause bloated prints and poor finishes. By following these best practices and regularly adjusting your settings, you will minimize the risk of mistakes and achieve higher quality prints.
Tests and adjustments to plan
Tests and adjustments are essential to ensure quality 3D prints, as each printer and project may require specific configurations. To start, it is recommended to perform a bed calibration test to check its leveling, ensuring a good first layer. You can also perform a test tower to assess layer height quality and dimensional accuracy at different print speeds. Another important test is the retraction test, which allows you to adjust retraction settings to avoid unwanted stringing and optimize the movement of the print head.
After testing these basic parameters, it is wise to make adjustments to the nozzle and bed temperatures based on the material used, as well as print speed settings to find a good balance between quality and speed. Finally, for complex prints, it may be necessary to test and adjust support parameters, such as density and support type, to ensure good stability of the object. These regular adjustments help prevent common errors, such as surface defects or warping, and ensure consistent print quality.
Conclusion: Layer height in 3D printing
In conclusion, layer height is a crucial factor in 3D printing that affects print quality, speed, and material usage. By selecting the appropriate layer height based on the specific needs of the print, such as detail level, strength, and final use, users can achieve the best balance between performance and efficiency. Testing and adjustments play a vital role in optimizing the settings for each project, ensuring consistent and high-quality results. Understanding how layer height interacts with other print parameters, such as filament type, print speed, and temperature, is key to mastering 3D printing and achieving optimal outcomes.
Picture by Freepik.
The articles published on Imprimy.com are for informational purposes only. They are intended to provide general advice and information related to 3D printing. Imprimy.com cannot be held responsible for the results obtained or the consequences arising from the application of the shared information. We recommend always checking the specific instructions for your hardware and materials before use.