Do you have questions about plastic 3D printing and are looking for answers? At Imprimy, we are here to explain everything to you.
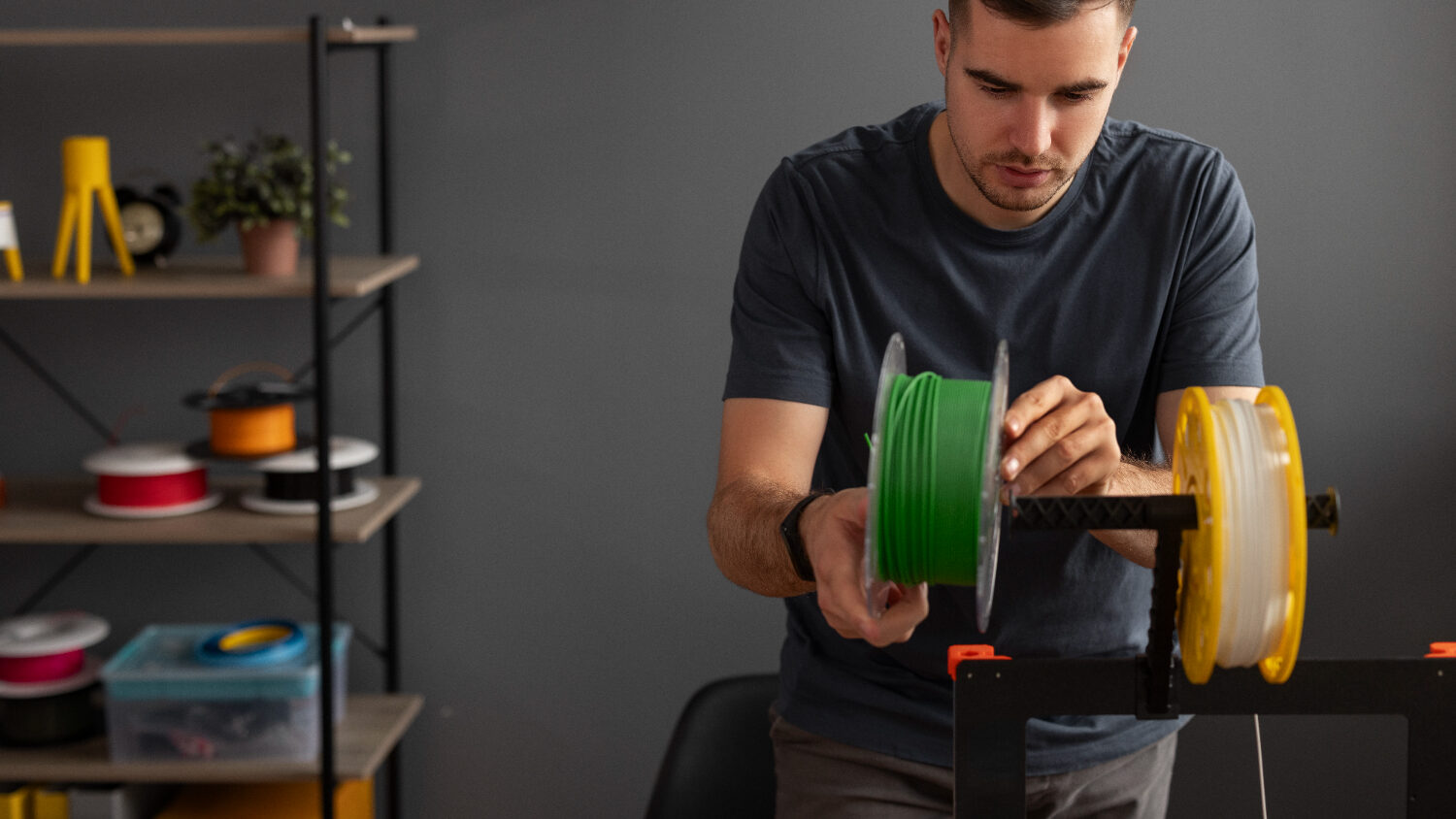
What are the different types of plastics used in 3D printing?
You have the option to print common thermoplastics, technical materials, or even composite materials.
Common thermoplastics in 3D printing
Common thermoplastics in 3D printing include:
- PLA (Polylactic Acid) – A biodegradable and easy-to-use plastic, ideal for beginners.
- ABS (Acrylonitrile Butadiene Styrene) – Known for its strength and durability, often used in functional parts.
- PETG (Polyethylene Terephthalate Glycol) – A strong and flexible material with good chemical resistance.
- Nylon – Known for its strength, flexibility, and wear resistance, often used for functional parts.
- TPU (Thermoplastic Polyurethane) – A flexible material, commonly used for rubber-like parts.
These materials are widely used due to their versatility, ease of printing, and various mechanical properties.
Technical materials for plastic 3D printing
Technical materials for 3D plastic printing include:
- PC (Polycarbonate) – Known for its high strength, heat resistance, and optical clarity, making it suitable for engineering and industrial applications.
- PEEK (Polyether Ether Ketone) – A high-performance thermoplastic offering exceptional strength, chemical resistance, and thermal stability, used in aerospace and medical industries.
- PEI (Polyetherimide) – A strong and heat-resistant material often used for parts requiring high performance, like in automotive and aerospace sectors.
- ASA (Acrylonitrile Styrene Acrylate) – Resistant to UV degradation and weathering, making it ideal for outdoor applications.
- Ultem (PEI) – Known for its excellent mechanical properties and high thermal stability, often used for advanced engineering parts.
These materials are designed for more demanding applications that require higher strength, temperature resistance, or chemical resistance than standard thermoplastics.
Composite plastic materials for 3D printing
Composite plastic materials for 3D printing include:
- Carbon Fiber Reinforced Filaments – These filaments, often based on PLA, ABS, or Nylon, are infused with carbon fibers, providing enhanced strength, stiffness, and lightweight properties for structural parts.
- Glass Fiber Reinforced Filaments – Similar to carbon fiber composites but using glass fibers, these filaments offer improved mechanical properties, such as better durability and resistance to wear, while being less brittle than carbon fiber.
- Kevlar Reinforced Filaments – Infused with Kevlar fibers, these filaments are known for their toughness and resistance to abrasion, making them ideal for heavy-duty applications.
- Wood-filled Filaments – Composites that blend wood fibers with PLA, giving prints a wood-like appearance and texture, suitable for decorative items.
- Metal-filled Filaments – These are PLA or other base materials mixed with metal powders (such as bronze, brass, or copper), resulting in prints with a metallic finish and added weight.
These composite materials combine the properties of traditional thermoplastics with added benefits like increased strength, flexibility, or unique aesthetics, allowing for more specialized applications in 3D printing.
What are the different possible applications for plastic 3D printing?
Plastic 3D printing has various applications in industrial fields, domestic uses, and specific sectors.
3D plastic printing in industrial fields
3D plastic printing plays a key role in industrial fields by offering flexible, fast and cost-effective solutions for various applications. It is widely used for rapid prototyping, allowing companies to design, test and improve products before mass production, thus reducing lead times and development costs.
The automotive and aerospace industries use this technology to create lightweight and complex functional parts, such as brackets or technical components, often made with technical or composite plastic materials. In the manufacturing sector, 3D printing is also used to produce tools, molds and custom parts, tailored to the specific needs of production lines. In addition, it contributes to industrial maintenance by enabling the rapid recreation of spare parts or obsolete components, thus ensuring better inventory management and reducing production downtime.
The domestic uses of 3D plastic printing
3D plastic printing has become widely democratized for domestic use, offering individuals the ability to design and manufacture everyday objects. It allows, in particular, to create customized parts, such as toys, decorative accessories, or even practical tools adapted to specific needs. DIY enthusiasts appreciate this technology to produce spare parts for repairing household equipment, thus extending their lifespan while reducing costs.
In addition, home 3D printing encourages creativity by allowing the realization of customized projects, whether for interior design, hobbies or even education, thanks to accessible materials such as PLA, which is easy to use and environmentally friendly.
Finally, with increasingly affordable printers and online communities sharing free models, 3D printing is becoming a powerful tool to personalize and simplify everyday life.
3D plastic printing for specific sectors
3D plastic printing finds remarkable applications in several specific sectors thanks to its flexibility and the diversity of available materials. In the medical field, it allows for the fabrication of customized prostheses, anatomical models for surgical planning, and even tailor-made equipment, often based on PLA or biodegradable polymers.
In the fashion and design industry, this technology is used to create unique jewelry, clothing or accessories, using technical or composite plastics for both aesthetic and functional results.
What are the advantages and disadvantages of 3D plastic printing?
Printing with plastic materials offers you many advantages, but also some specific disadvantages.
The advantages of 3D plastic printing
3D plastic printing offers many advantages that make it an innovative and accessible technology. It allows for complete customization, making it possible to manufacture unique objects or objects tailored to specific needs, whether for domestic or industrial use. Thanks to its additive manufacturing process, it significantly reduces waste compared to traditional methods, using only the necessary amount of material.
Moreover, it is fast for prototyping, thus accelerating product development and reducing time-to-market. The diversity of available plastic materials, ranging from common thermoplastics to reinforced composites, makes it possible to meet a wide range of applications, from simple objects to technical parts. Finally, this technology is increasingly affordable, both in terms of printers and materials, making its use accessible to individuals and small businesses.
The disadvantages of 3D plastic printing
3D plastic printing, despite its many advantages, also has some drawbacks. Environmentally, the use of non-biodegradable plastics like ABS can generate waste that is difficult to recycle, although alternatives like PLA are more environmentally friendly. The slowness of the process is also a limitation, as manufacturing objects, especially large ones, can take several hours or even days. In terms of quality, some printed parts may lack robustness or have visible layers, making them less suitable for applications requiring a flawless finish or high mechanical resistance.
Furthermore, 3D plastic printers, although more accessible, require technical learning to optimize settings and avoid printing failures. Finally, the cost of technical materials or advanced equipment can still be a barrier for complex or professional projects.
Conclusion: plastic 3D printing
In conclusion, 3D plastic printing represents a major technological advancement, offering numerous advantages such as customization, waste reduction and great flexibility in the manufacturing of various objects. It finds applications in a multitude of sectors, ranging from home creation to high-tech industries, including medicine and design.
However, its disadvantages, including its environmental impact, the slowness of the process and some technical limitations, must be taken into account. Despite these challenges, continuous innovation and cost reduction allow 3D plastic printing to become more democratic and open new perspectives, both for individuals and professionals.
Picture by Freepik.
The articles published on Imprimy.com are for informational purposes only. They are intended to provide general advice and information related to 3D printing. Imprimy.com cannot be held responsible for the results obtained or the consequences arising from the application of the shared information. We recommend always checking the specific instructions for your hardware and materials before use.