Do you want to know everything about resin 3D printing? Imprimy is here to provide all the answers you’re looking for.
3D resin printing uses photopolymerization to solidify a liquid resin layer by layer thanks to a UV source, offering unmatched precision and fine details.
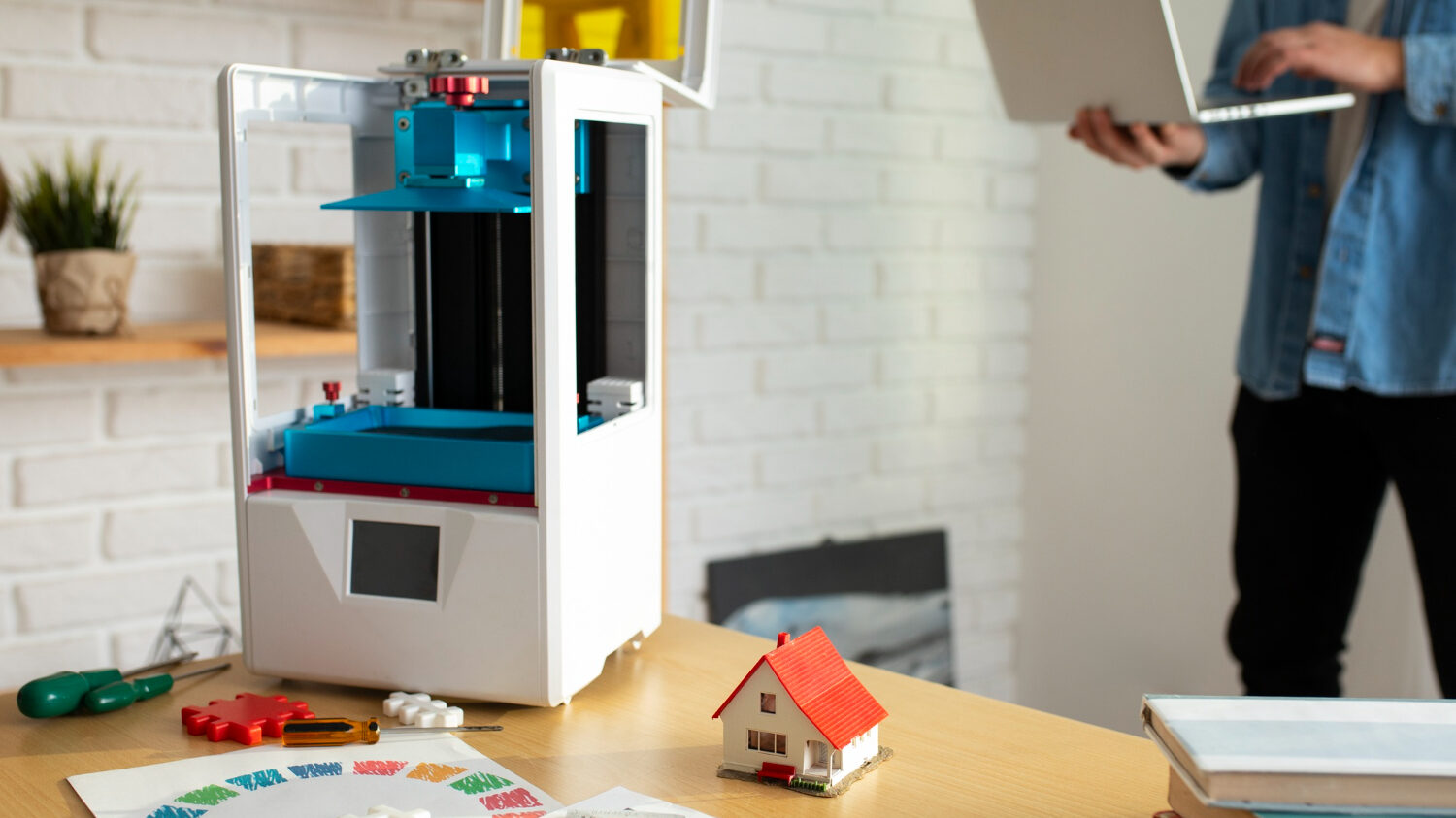
What is resin 3D printing?
Resin 3D printing works by solidifying a photosensitive resin layer by layer to create a solid three-dimensional model.
How resin 3D printing works
3D resin printing is based on photopolymerization, a process where a liquid resin is hardened layer by layer using a UV light source. This process mainly uses technologies like SLA (stereolithography) or DLP (Digital Light Processing).
The model is built from bottom to top, with each layer being solidified with high precision. This type of printing is ideal for objects requiring fine details and a smooth finish.
Types of resins used for 3D printing
There are several types of resins used in 3D printing, each suited to specific needs:
- Standard resin is ideal for visual prototypes thanks to its fine details,
- Flexible resin allows printing of flexible objects,
- High-strength resin is suitable for functional parts,
- Biocompatible resins are used in medicine or dentistry.
The choice of resin depends on the mechanical, aesthetic, or technical properties you are looking for.
What are the different applications of resin 3D printing?
Resin 3D printing allows for applications in many sectors such as jewelry, medicine, and modeling.
In the jewelry industry
3D resin printing is used in the jewelry industry to create precise models and casting molds. Thanks to its high precision and ability to reproduce fine details, 3D resin printing allows you to design complex models quickly.
Jewelers often use castable resins, which burn cleanly during the lost wax process. This reduces prototyping costs and speeds up production.
In the medical sector
In the medical sector, 3D resin printing allows the manufacture of customized devices with high anatomical precision. It is used to produce dental prostheses, surgical guides, and anatomical models for surgery planning.
Biocompatible resins ensure safe use in contact with the human body. This technology offers tailored adaptation and reduces manufacturing times.
In the high-precision prototyping sector
In the high-precision prototyping sector, 3D resin printing is especially valued for its fine details and high dimensional accuracy. It allows the creation of complex models with smooth surfaces and detailed geometries, often impossible to produce by other means.
Technical resins offer specific properties such as rigidity, thermal resistance, or transparency. This technology is ideal for functional testing and visual presentations. 3D resin printing helps accelerate product development while reducing costs.
For model making and figurines
3D resin printing is widely used in model making and figurine creation thanks to its high resolution and ability to reproduce small details. It allows the production of complex-shaped parts with a smooth finish, ideal for painting and customization.
Both hobbyists and professionals appreciate its precision for creating realistic miniatures. Standard or detailed resins are often preferred in this field.
What are the advantages of resin 3D printing?
Resin 3D printing is advantageous because it allows for precise results, a smooth surface, and high-quality finishes.
The precision and detail of resin 3D printing
3D resin printing stands out for its exceptional precision and ability to reproduce very fine details. Thanks to ultra-thin layers and the use of UV light, it offers a resolution far superior to that of FDM printers.
This allows the creation of objects with sharp edges, smooth surfaces, and complex shapes. It is therefore ideal for sectors demanding high visual quality.
A smooth surface and high-quality finishes
3D resin printing allows you to obtain a smooth surface and high-quality finishes straight from the printer. Thanks to layer-by-layer photopolymerization, objects show little or no visible layering, unlike other technologies such as FDM.
This finish quality reduces the need for post-processing. It is ideal for aesthetic parts, such as in jewelry, model making, or product design. The final result is often ready to be painted, molded, or used directly.
What are the disadvantages of resin 3D printing?
Resin 3D printing has some disadvantages in terms of equipment and material costs, size limitations, significant environmental impact, and a cumbersome post-printing process.
The costs of equipment and materials for resin 3D printing
The costs of equipment for 3D resin printing have dropped significantly in recent years, making this technology accessible to both individuals and professionals.
The purchase of a quality 3D resin printer starts around 200 to 500 euros, while professional models can exceed 3,000 euros. The price of resins varies according to their properties, ranging from 30 to 150 euros per liter.
You also need to budget for post-processing expenses (isopropyl alcohol, UV station, gloves, masks). Despite these costs, 3D resin printing remains competitive for producing precise and detailed items.
The size limitations of resin 3D prints
3D resin printing has size limitations due to the restricted build volume of the machines, especially consumer models. Most resin printers offer a build space between 10 and 20 cm in height. For larger objects, they need to be cut into multiple parts and assembled after printing.
Additionally, large prints require more resin and longer post-processing time, which can complicate production. These constraints make it a technology better suited for small, precise parts.
Post-printing processing of resin prints
Post-print processing is essential to ensure the strength and quality of resin-printed objects. It generally includes a rinse with isopropyl alcohol to remove uncured resin, followed by UV curing to fully harden the part.
This process improves the mechanical resistance of your 3D prints and stabilizes dimensions. Sanding or painting can also be done to perfect the finish. Without this treatment, parts remain fragile and sticky.
The environmental impact of resin 3D printing
3D resin printing has a greater environmental impact than other similar technologies due to the toxicity and difficulty of recycling photopolymer resins.
Uncured resins are polluting and require strict waste management. Additionally, post-processing often uses solvents like isopropyl alcohol, which must be handled carefully.
However, efforts are underway to develop eco-friendly resins and improve recycling. Responsible use remains essential to limit its ecological footprint.
What are the innovations and the future of resin 3D printing?
Resin 3D printing is expected to undergo many advancements in the future, related to both the resins and the evolution of 3D printers.
Improvements in the resins used for 3D printing
Les résines pour les impressions 3D ont connu de nombreuses améliorations leur permettant de répondre à des besoins variés. Les nouvelles formulations offrent une meilleure résistance mécanique, une plus grande flexibilité ou une transparence accrue.
Des résines biocompatibles et calcinables ont été développées pour des applications médicales et bijoutières. On observe aussi des avancées vers des résines plus écologiques et moins toxiques. Ces innovations élargissent les possibilités et améliorent la qualité des impressions.
The developments in resin 3D printers
3D resin printers have evolved significantly, now offering better resolution and increased printing speeds thanks to technologies like LCD and MSLA. The machines have become more compact, affordable, and easy to use, expanding their accessibility.
Manufacturers also integrate automatic calibration systems and built-in post-processing to simplify the process. These advancements enable more reliable printing and suitability for a wide range of applications.
Future applications of resin 3D printing
The future applications of 3D resin printing look promising, especially in the field of personalized medicine, with increasingly sophisticated custom implants and prostheses.
It could also revolutionize industrial manufacturing by producing complex functional parts at a lower cost. The rise of eco-friendly resins paves the way for more sustainable use.
Finally, 3D resin printing could expand into sectors like aerospace, robotics, and fashion, thanks to its precision and flexibility.
Conclusion : resin 3D printing
3D resin printing establishes itself as an essential technology thanks to its exceptional precision, high-end finishes, and ability to reproduce complex details. It finds varied applications, from jewelry to medicine, including prototyping and model making.
Despite some size limitations and an environmental impact that must be managed, its continuous advancements make this technology increasingly accessible and high-performing. 3D resin printing thus paves the way for more personalized, fast, and innovative manufacturing.
Picture by Freepik.
The articles published on Imprimy.com are for informational purposes only. They are intended to provide general advice and information related to 3D printing. Imprimy.com cannot be held responsible for the results obtained or the consequences arising from the application of the shared information. We recommend always checking the specific instructions for your hardware and materials before use.