Are you wondering about SLA 3D printing and its specific features? At Imprimy.com, we’re here to answer all your questions on the subject.
SLA 3D printing uses liquid resin and a UV laser to create high-precision objects.
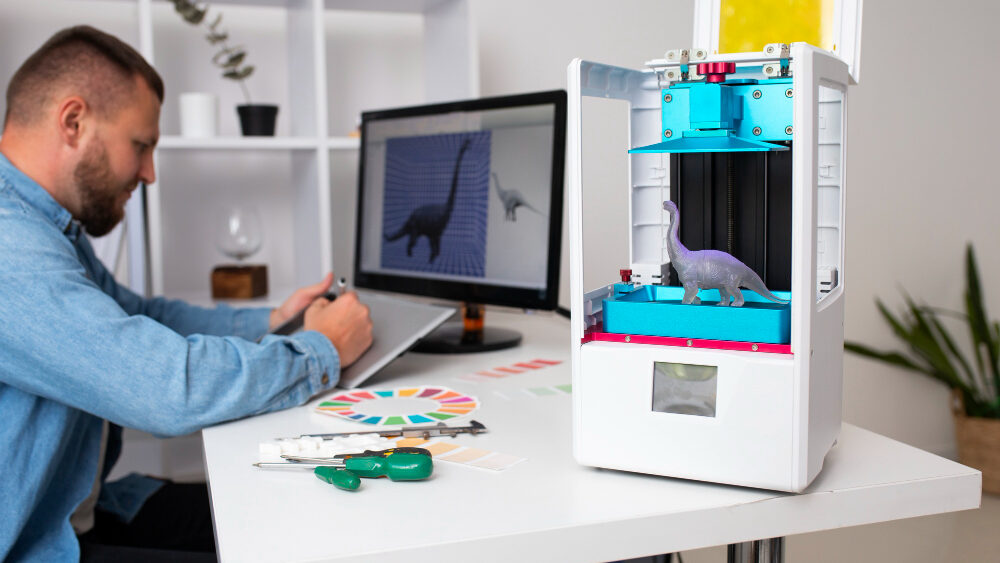
What is SLA 3D printing?
SLA 3D printing is a printing technology that uses a laser to solidify liquid resin and create 3D objects with high precision.
The definition of stereolithography
Stereolithography is an additive manufacturing technique that uses an ultraviolet laser to solidify a photosensitive resin layer by layer in order to create three-dimensional objects.
This process makes it possible to produce high-precision parts with fine details, making it a popular method in the fields of rapid prototyping and the production of complex parts.
The basic process of SLA 3D printing
The basic process of SLA 3D printing (Stereolithography) starts with the preparation of a digital 3D file of the object to be printed. This file is then sliced into thin cross-sectional layers using software.
The SLA printer uses an ultraviolet laser to harden a photosensitive liquid resin, layer by layer, following the contours defined by the digital file. A platform gradually moves downward after each solidified layer, allowing fresh resin to cover the surface for the next layer.
Once printing is finished, the object is removed from the machine and often undergoes cleaning and post-processing, such as additional curing under UV light, to improve its mechanical properties.
How does SLA 3D printing work?
SLA 3D printing works by solidifying, layer by layer, a liquid photosensitive resin using a UV laser, providing high precision and fine details.
SLA 3D printing step by step
Here are the detailed steps of the SLA 3D printing process:
- 3D model design: Create a 3D model of the object you want to print using CAD software (Computer-Aided Design).
- File preparation: Convert the 3D model into an STL file (Standard Tessellation Language), the standard format for 3D printing.
- Layer slicing: Use slicing software to divide the STL file into thin cross-sectional layers. This software also generates the supports needed for overhanging parts.
- Printer preparation: Fill the SLA printer’s resin tank with the appropriate photosensitive resin and ensure the build platform is clean and leveled.
- Layer-by-layer printing: The printer uses a UV laser to harden the resin, layer by layer, following the contours defined by the sliced file. The build platform moves downwards after each layer to allow fresh resin to cover the surface.
- Part cleaning: Once printing is finished, remove the part from the platform and clean it with a solvent, usually isopropanol, to remove excess resin.
- Post-processing: Subject the part to additional curing under UV light to improve its mechanical properties. Also remove the supports added during printing.
- Finishing: Sanding, painting, or other finishing techniques can be applied to achieve the desired surface and appearance.
The role of the UV laser and photosensitive resin in 3D printing
In the SLA 3D printing process, the UV laser and the photosensitive resin play crucial and complementary roles.
The ultraviolet laser is used to selectively trace and harden the photosensitive resin, layer by layer, according to the contours defined by the 3D model.
The photosensitive resin is a liquid material that chemically reacts to UV light by solidifying. This reaction, called photopolymerization, transforms the liquid resin into a solid, thus forming the successive layers of the printed object.
Together, the UV laser and the photosensitive resin enable the creation of objects with high precision and fine details, which are key characteristics of SLA technology.
Explanation of the layer-by-layer construction in SLA 3D printing
The layer-by-layer construction in SLA 3D printing is a precise process that allows the creation of three-dimensional objects from a digital model. Here’s how it works:
- Model preparation: The 3D model is first sliced into thin cross-sectional layers using software. Each layer represents a horizontal section of the final object.
- Start of printing: The SLA printer begins by immersing a build platform into a tank of photosensitive resin. The platform is positioned at a precise distance from the resin surface, corresponding to the thickness of the first layer.
- Resin curing: A UV laser traces the shape of the first layer on the resin surface, causing a photopolymerization reaction that hardens the exposed resin. This solidified layer adheres to the build platform.
- Platform movement: Once the first layer is cured, the build platform moves upward (or downward, depending on the printer model) by a distance equal to the thickness of the next layer. The liquid resin then covers the previously cured layer.
- Process repetition: The UV laser traces and cures the next layer of resin, which adheres to the previous layer. This process repeats for each layer of the model, gradually building the object from bottom to top.
- End of printing: Once all layers are printed, the object is removed from the build platform. It is then cleaned to remove excess resin and undergoes post-processing, such as additional curing under UV light, to improve its mechanical properties.
What are the applications of SLA 3D printing?
The main applications of SLA 3D printing include rapid prototyping, jewelry manufacturing, dental and medical models, as well as the creation of precise parts for industry and design.
The use of SLA 3D printing in various sectors
SLA 3D printing (Stereolithography) is used in various industries due to its ability to produce parts with high precision and fine details. Here are some examples of applications in different fields:
- Medicine and Dentistry: SLA is used to create prosthetics, dental implants, anatomical models for surgical planning, and custom medical devices. The precision of SLA allows producing parts tailored to the specific needs of patients.
- Aerospace and Automotive: In these industries, SLA is employed for rapid prototyping and manufacturing complex, lightweight parts, such as engine components, body parts, and tooling.
- Jewelry: Jewelers use SLA to create detailed and complex 3D jewelry models that are then cast in precious metals. This enables producing pieces with fine details and high accuracy.
- Electronics: SLA is used to manufacture custom housings, connectors, and other electronic components. Its ability to produce parts with tight tolerances is especially valuable in this sector.
- Art and Design: Artists and designers use SLA to create sculptures, models, and decorative objects with complex shapes and fine details.
- Education and Research: Academic institutions and research centers use SLA for prototype creation, materials research, and teaching additive manufacturing techniques.
- Toy Industry: SLA allows producing toys and figures with complex details and high-quality finishes.
Thanks to its precision and versatility, SLA 3D printing is a valuable tool across many sectors, enabling the creation of complex and customized parts with great efficiency.
Comparison with other 3D printing technologies
SLA 3D printing (Stereolithography) is an additive manufacturing technology that stands out from other 3D printing methods due to its unique characteristics. Here is a comparison with other common 3D printing technologies:
Materials | Precision | Applications | Cost | |
FDM | Uses thermoplastic filaments like ABS and PLA. | Less precise than SLA, with visible layers and a rougher surface finish. | Ideal for rapid prototyping, functional parts, and educational projects. | Generally less expensive than SLA for both hardware and operation.des filaments thermoplastiques comme l’ABS et le PLA. |
SLS | Uses polymer, metal, or ceramic powders. | Good precision, but the surface finish can be rough and may require post-processing. | Used for functional parts and prototypes in aerospace, automotive, and medical fields. | More expensive than SLA in terms of hardware and operation.céramique. |
DLP | Uses photosensitive resins similar to SLA. | Similar precision and smooth surface finish as SLA. | Used for similar applications as SLA, like jewelry, dentistry, and small detailed prototypes. | Comparable to SLA, but can be faster for some applications. |
SLM / DMLS | Uses metal powders. | Excellent precision for metal parts, with a good surface finish. | Used for functional metal parts in aerospace, automotive, and medical industries. | Very expensive in terms of hardware and operation.métalliques. |
Binder Jetting | Uses polymer, metal, or ceramic powders bound by a liquid binder. | Less precise than SLA, with a rough surface finish. | Used for prototypes and functional parts in various sectors. | Less expensive than SLA for some applications but may require post-processing.liquide. |
What materials are used in SLA 3D printing?
The materials used in SLA 3D printing are mainly liquid photosensitive resins, including standard resins, flexible resins, high-strength resins, biocompatible resins, and translucent resins, depending on the desired application.
Different types of resins available and their properties
For SLA 3D printing (Stereolithography), several types of resins are available, each offering specific properties suited to different applications.
- Standard resins are the most commonly used, offering a good balance between strength and precision, ideal for prototypes and detailed models.
- Flexible resins are designed to mimic rubber-like properties, providing high elasticity and impact resistance, perfect for parts requiring some flexibility.
- High-temperature resins can withstand high temperatures without deforming, making them suitable for applications in thermally demanding environments.
- Biocompatible resins are specially formulated for medical and dental applications, offering biological compatibility and non-toxicity.
- Finally, casting resins are optimized to create precise and detailed molds, allowing faithful reproduction of complex parts.
Each type of SLA 3D printing resin is selected based on the specific requirements of the project, such as durability, flexibility, or thermal resistance.
Material choice according to applications
The choice of materials for a specific application depends on several factors, including the required mechanical, thermal, chemical, and electrical properties, as well as economic and environmental considerations.
- For applications requiring high mechanical strength, materials like steel or titanium alloys are often preferred due to their high strength and durability.
- In high-temperature environments, materials such as superalloys or technical ceramics are used for their thermal stability and oxidation resistance.
- For electrical applications, materials like copper or aluminum are chosen for their high electrical conductivity.
- In the medical field, materials must be biocompatible and non-toxic, such as certain polymers or specific alloys.
- Finally, for applications requiring weight reduction, composite materials like carbon fiber are often used due to their high strength-to-weight ratio.
Therefore, the choice of material must be made according to the specific requirements of the application, considering both technical and economic constraints.
What are the tips to apply to succeed in your SLA prints?
To succeed in your SLA prints, it is essential to properly level the platform, use an appropriate resin, maintain a stable temperature, perform precise cleaning of the parts, and respect the post-curing times.
File preparation and machine setup
File preparation and machine setup are crucial steps to ensure a successful 3D print. To start, the 3D file must be designed or downloaded in a compatible format, usually STL or OBJ, and checked to make sure it contains no mesh errors.
Next, the file is imported into a slicing software where it is converted into layers and the printing parameters are set. These parameters include layer height, printing speed, nozzle and heated bed temperature, as well as infill and the supports needed for overhanging parts.
Once the file is prepared, the machine must be calibrated to ensure good first layer adhesion and precise bed leveling. It is also important to make sure the nozzle is clean and the filament is properly loaded.
Finally, before starting the print, it is advisable to double-check all settings to avoid print failures and achieve a high-quality result.
Some tips for post-processing and finishing parts
Post-processing and finishing of 3D printed parts are essential to obtain a high-quality final product. Here are some tips to optimize these steps:
- Cleaning: After printing, carefully remove supports and clean the part to eliminate material residues. Use tools like pliers or knives to remove supports without damaging the part.
- Sanding: To achieve a smooth surface, use sandpaper of different grits, starting with a coarse grit to remove imperfections and finishing with a fine grit for a smooth finish.
- Polishing: For resin parts, polishing with chemical or mechanical products can improve transparency and shine. Plastic parts can be polished using polishing compounds.
- Painting: Apply a primer coat before painting to improve paint adhesion. Use paints suitable for the material of the part for a durable and aesthetic finish.
- Heat treatment: For some resins or plastics, annealing can improve mechanical strength and reduce internal stresses.
- Assembly: If the part consists of several pieces, use adhesives or welding techniques suited to the material for a strong assembly.
- Coatings: Apply protective coatings to improve resistance to UV, water, or chemicals, depending on the intended application.
What is the future of SLA 3D printing?
The future of SLA 3D printing relies on advanced resins, increased printing speed, improved precision, as well as growing adoption in the medical, dental, aerospace, and microfabrication sectors.
Recent innovations and future trends in SLA 3D printing
Recent innovations and future trends in SLA (Stereolithography) 3D printing show a rapid and promising evolution. Both SLA and SLS technologies have experienced significant advances, with notable improvements in printing speed and material optimization. For example, companies like Bambu Lab and UltiMaker continue to push the limits of what is possible with 3D printing, focusing on faster and more efficient solutions. The integration of artificial intelligence and automation into 3D printing processes is a major trend, enabling increased optimization and better accessibility of the technology.
Additionally, the use of new materials, such as innovative filaments and advanced resins, opens the way to more diverse and specialized applications. Another area of innovation is the improvement of production capabilities, with machines like the SLA 750 by 3D Systems, offering complete solutions for additive manufacturing, including advanced post-processing systems and cloud-based production management software. These advances not only increase productivity and reliability, but also reduce costs and improve the quality of produced parts.
Looking ahead, SLA 3D printing is also transforming sectors like medicine, where custom implants and surgical models are increasingly used to improve surgical outcomes. Furthermore, the combination of 3D printing with other emerging technologies such as robotics and the Internet of Things (IoT) promises to unlock new possibilities and usher in an era of creativity, sustainability, and unprecedented innovation.
Growth potential and new applications of SLA 3D printing
SLA (Stereolithography) 3D printing presents considerable growth potential and continues to find new applications in various sectors. Here are some areas where this technology is making a significant difference:
- Medicine and Health: SLA 3D printing is increasingly used to create custom implants, prosthetics, and anatomical models for surgical planning. This helps doctors better prepare for procedures and improve patient outcomes.
- Aerospace and Automotive: In these industries, SLA printing is used for rapid prototyping and production of complex and lightweight parts. This reduces costs and development time, while enhancing component performance.
- Art and Design: Artists and designers use SLA printing to create detailed artworks and innovative design products. The precision and surface quality offered by this technology enable the realization of complex and aesthetic designs.
- Education and Research: Academic institutions use SLA 3D printing for scientific research and teaching, allowing students to visualize and manipulate complex 3D models, thereby improving their understanding of theoretical concepts.
- Consumer Goods: Companies use SLA printing to create customized products and functional prototypes, enabling rapid innovation and adaptation to specific consumer needs.
- Construction and Architecture: Although less common, SLA printing is beginning to be explored for creating detailed architectural models and innovative construction components.
Conclusion: SLA 3D printing
SLA (Stereolithography) 3D printing represents a cutting-edge technology in the field of additive manufacturing, offering vast and varied possibilities across many sectors. Thanks to its ability to produce parts with high precision and excellent surface quality, it has become an indispensable tool for rapid prototyping, the production of complex parts, and the creation of customized products.
Recent innovations in materials, such as advanced resins and photopolymers, as well as improvements in printing machines, have expanded the applications of SLA 3D printing. Sectors like medicine, aerospace, automotive, and even art and design benefit from this technology to create innovative and tailored solutions.
The integration of emerging technologies, such as artificial intelligence and the Internet of Things (IoT), promises to continue pushing the boundaries of what is possible with SLA 3D printing. These advances not only improve efficiency and productivity, but also pave the way for new applications and innovations.
In conclusion, SLA 3D printing is a constantly evolving technology with huge growth potential and increasingly diverse applications. It continues to transform manufacturing processes, offering faster, more efficient, and more customizable solutions, while opening new horizons for the future of manufacturing and design.
Picture by Freepik.
The articles published on Imprimy.com are for informational purposes only. They are intended to provide general advice and information related to 3D printing. Imprimy.com cannot be held responsible for the results obtained or the consequences arising from the application of the shared information. We recommend always checking the specific instructions for your hardware and materials before use.