Are you wondering if it’s possible to install threaded inserts into your 3D prints and how to do it? At Imprimy, we are here to explain everything.
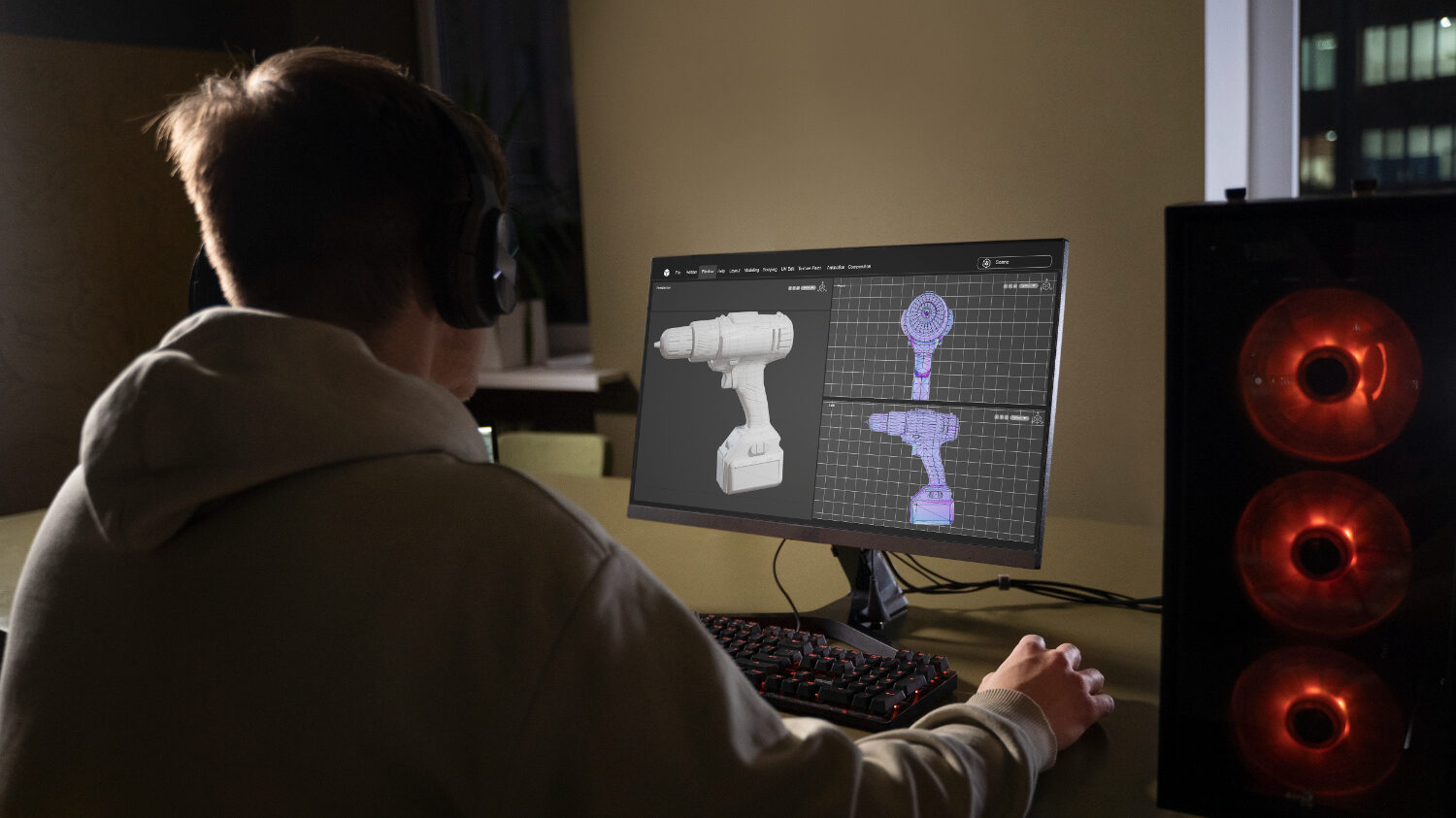
Introduction: Why Use Threaded Inserts in 3D Printing?
3D printing allows for the creation of specific parts that may require certain special additions to be fully functional, such as the inclusion of threaded inserts.
- Introduction: Why Use Threaded Inserts in 3D Printing?
- What is a threaded insert?
- "What are the different types of threaded inserts in 3D printing?
- How to choose the right insert for your 3D printing project?
- What are the tips and best practices for using threaded inserts in your 3D prints?
- Conclusion: Why adopt threaded inserts in your 3D printing projects?
Quick Reminder on 3D Printing
3D printing, also known as additive manufacturing, is a process where material is added layer by layer to create a three-dimensional object based on a digital model. This technology allows for the production of complex shapes and custom designs that would be difficult or impossible to achieve with traditional manufacturing methods.
The process begins by designing the object using computer-aided design (CAD) software. The digital file is then sent to the 3D printer, which melts or softens the material (such as PLA, ABS, or resin) and deposits it layer by layer to build the final piece.
3D printing offers a wide range of applications, from rapid prototyping and creating functional parts to producing artistic and decorative objects. It allows for high customization and is widely used in industries such as automotive, aerospace, healthcare, and consumer goods.
Solutions for Integrating Robust Fasteners in 3D Printed Objects
Integrating strong and reliable fasteners into 3D printed parts can be crucial for ensuring the functionality and durability of your objects. While 3D printed materials are versatile, they may not always have the mechanical strength required for screws or bolts to securely attach. Here are several solutions to incorporate robust fastening systems into 3D printed objects:
- Threaded Inserts:
- Heat-set Inserts: Brass inserts that are heated and pressed into the printed part, creating durable and reusable threads for screws and bolts. Ideal for high-stress areas or parts that need frequent assembly and disassembly.
- Press-fit Inserts: These inserts are pressed directly into the holes in your 3D printed parts without the need for heat. They provide strong, reliable threading for fastening.
- Design your 3D part with holes that match the insert size.
- Heat-set inserts require a soldering iron or special tool to embed the insert.
- Press-fit inserts can be inserted with manual pressure or a clamp.
- Self-Tapping Screws: Self-tapping screws are designed to tap their own threads into a material, making them a straightforward option for adding fixations. These screws can be driven directly into the plastic without the need for inserts, making them ideal for lightweight applications.How to Use:
- Include pre-designed pilot holes in your 3D model.
- Choose a screw size that fits well with the material and ensures a secure hold.
- Threaded Holes: If you need to fasten parts together without using inserts, you can design your 3D print with threaded holes, allowing you to screw directly into the material. This approach works best with denser and stronger materials like nylon, carbon fiber composites, or certain resins.How to Use:
- Design the hole with the correct dimensions for the screw to fit directly into.
- Ensure the 3D print’s material has enough strength to hold the threads without breaking.
- Embedded Nuts: Nuts can be embedded in your 3D print to create secure fastening points. This method works by designing your part to include a cavity for the nut, which can then be used to secure bolts or screws. The nut is either placed manually or pressed into the cavity before the print completes.How to Use:
- Plan the cavity size in your design to securely hold the nut.
- Use super glue or heat (for plastic nuts) to secure the nut in place after insertion.
- Plastic Rivets and Clips: For non-permanent fastening or for attaching parts without screws, you can use plastic rivets or clips. These can be designed into your 3D model as an alternative to threaded fasteners, providing a simple yet effective way to secure components.How to Use:
- Design the rivet holes or clip features into your model.
- Assemble by pressing the clips or rivets into place.
- Bonding and Adhesives: While not a traditional fastening method, adhesives can be an effective way to bond parts together. Special 3D printing glues, cyanoacrylate (super glue), or epoxy resins can be used to join components, providing a strong bond for areas that don’t require mechanical fasteners.
- How to Use:
- Apply glue or adhesive to the joining surfaces.
- Hold the parts together until the adhesive cures.
- How to Use:
By using these techniques, you can ensure that your 3D prints are not only functional but also capable of holding up under mechanical stress. Selecting the right solution depends on the application, material, and required strength for the parts you’re creating.
What is a threaded insert?
Threaded inserts are mechanical components used to create assemblies. They can be made from various materials and used in different ways.
The definition of a threaded insert
A threaded insert is a mechanical component used to create a threaded hole in a material, allowing screws or bolts to be securely fastened. It is typically made from metal or plastic and is designed to reinforce the material, providing better durability and the ability to handle repeated fastening and unfastening. Threaded inserts are commonly used in 3D printing, woodworking, and metalworking for creating strong, reusable connections in materials that may not naturally hold threads.
Common materials for threaded inserts
Threaded inserts in 3D printing are typically made from robust materials to ensure maximum strength in assemblies. The most common materials include brass, which is often favored for its resistance to corrosion and its ability to firmly anchor in the plastics used in 3D printing. Stainless steel is also widely used for applications requiring high mechanical strength and durability. Lastly, aluminum can be a lightweight and durable option, especially for parts that will not be subjected to extreme stress.
Each material has specific advantages depending on the use and environmental conditions the final object will be exposed to.
The difference between directly printed threads and threaded inserts
The main difference between directly printed threads and threaded inserts lies in the durability and strength of the fastenings. Directly printed threads in 3D are created using the same material as the part itself, which can make them less durable, especially when repeatedly screwed and unscrewed. They are likely to wear out quickly, particularly if the part is subjected to mechanical forces or vibrations.
On the other hand, threaded inserts, typically made of metal, are inserted after printing. They provide a much stronger and more durable fastening, allowing for multiple screwing and unscrewing without degrading the part, which is crucial for assemblies subjected to high stresses.
The advantages of threaded inserts in 3D printing
Threaded inserts offer several notable advantages in 3D printing. First, they provide enhanced robustness compared to directly printed threads, allowing for a strong fastening that can withstand mechanical forces and vibrations. Additionally, threaded inserts facilitate repeated assembly and disassembly without damaging the surrounding material, which is crucial for parts requiring maintenance or modification.
Furthermore, they allow for greater customization of projects, as they can be selected based on specific load and application requirements. Lastly, using threaded inserts can also reduce the risk of defects during printing by avoiding issues related to internal threads, which can be challenging to print correctly.
“What are the different types of threaded inserts in 3D printing?
There are several types of threaded inserts used in 3D printing, each with characteristics suited for different assembly and durability needs. Here are the main types:
- Heat-Inserted Threaded Inserts (Heat-Set Inserts): These inserts are inserted into the 3D printed part using heat (usually a hot air gun or soldering iron). The heat slightly melts the surface of the plastic, allowing the insert to set securely into the material. This type is popular for its ease of installation and strength.
- Screw-In Threaded Inserts: These inserts are installed by simply screwing them into a pre-drilled hole in the 3D printed part. They are often used in harder materials and require precise drilling to ensure correct installation. This type provides a very strong and reliable connection.
- Press-Fit Threaded Inserts: These inserts are designed to be pressed into slightly smaller holes in the printed part without the need for heat or screws. They secure themselves using prongs or barbs that spread inside the material. This type is convenient for fast installation and does not require special tools.
- Metal Threaded Inserts (Metal for Plastic): Made of metal, typically brass, stainless steel, or aluminum, these inserts are designed for use in 3D printed plastic parts. They provide enhanced mechanical strength and are ideal for applications requiring solid and durable fastening.
- Self-Tapping Threaded Inserts: These metal inserts have both internal and external threads, allowing them to insert into the plastic material while cutting a thread inside. They are designed for easy installation and provide a very strong connection, especially in softer materials like PLA or ABS.
These various types of threaded inserts offer customization depending on strength requirements, ease of installation, and specific needs of each 3D printing project.
The advantages and disadvantages of each insert depending on the needs
When choosing between different types of threaded inserts for your 3D printing projects, it’s essential to compare their advantages and disadvantages based on your specific needs. Heat-set inserts offer a very strong and durable fixation, ideal for applications requiring high mechanical resistance, but their installation requires a heating tool and careful handling, which can complicate the process.
Threaded inserts are easy to install, allowing for quick and secure fastening, but they may not be suitable for very fragile materials due to the risk of cracking during tapping. Press-fit inserts, on the other hand, are quick to install without specific tools, making them convenient, but their fixation may be less strong in applications subject to high forces. Lastly, adhesive inserts are ideal for heat-sensitive materials and provide a smooth surface, but their installation requires drying time and careful surface preparation, which can lengthen the production time.
In summary, the choice of insert will depend on your specific application, the nature of the materials used, and whether or not disassembly is required.
How to choose the right insert for your 3D printing project?
Choosing the right threaded insert for your 3D printing project depends on several factors specific to your application.
The different types of printing materials and their influence on the choice of insert
The choice of 3D printing materials significantly influences the type of threaded insert to use in order to ensure the strength and durability of the assembly. Common plastics like PLA are easy to print, but they are more brittle, which may limit the use of screw or press-fit inserts, as they could cause cracking. In this case, heat-set or adhesive inserts are often preferred, as they provide a stronger fixation without requiring aggressive tapping. Thermoplastics like ABS offer better heat and impact resistance, allowing for the use of screw inserts, though heat-set inserts remain a solid option for demanding applications.
Flexible plastics such as TPU require press-fit or adhesive inserts, as conventional insertion methods may not provide adequate adhesion. Finally, for metal or composite parts, screw-inserts are ideal due to their increased strength, but adhesive inserts can also be effective if a smooth surface is desired. Ultimately, the choice of insert will depend not only on the mechanical requirements of the application but also on the specific properties of the printing material used.
The intended use of the insert
The intended use of threaded inserts plays a crucial role in selecting the type of insert to integrate into a 3D printed part. If the insert is intended for a permanent assembly, glued or heat-set inserts are often the best options, as they provide a strong and durable fixation suited for harsh conditions. In applications requiring frequent disassembly, such as prototypes or modular assembly parts, threaded or press-fit inserts are preferred, as they allow for screwing and unscrewing without damaging the surrounding material.
If the part needs to withstand high loads or mechanical stresses, it is essential to choose inserts that ensure adequate strength; in this case, metal inserts, such as heat-set or threaded inserts, are often required. Furthermore, if the insert is exposed to harsh environmental conditions, such as humidity or extreme temperatures, it is important to select an appropriate insert material, such as stainless steel for its corrosion resistance.
In summary, the intended use of the insert will influence not only the type of insert to choose but also the material and installation method, to ensure the performance and durability of assemblies in your 3D printing projects.
The dimensions and tolerances of inserts
The dimensions and tolerances of threaded inserts are essential aspects to consider when integrating these components into 3D printed parts, as they directly influence the quality and strength of the assembly. The dimensions of the inserts should be carefully selected based on the type of screw or bolt intended, taking into account the diameter, length, and thread pitch to ensure a perfect fit.
Tolerances are also crucial, as they determine the precision with which the insert fits into the pre-drilled hole; tight tolerances are recommended to ensure a solid fixation, while overly loose tolerances can lead to excessive play, compromising the strength of the assembly. It is important to account for potential variations in the 3D printing process, such as shrinkage or deformation, which can affect the final dimensions of the parts, and make allowances to compensate for these variations. In summary, the choice of insert dimensions and tolerances should be tailored to the specifics of the application and the material used, to ensure a reliable and durable assembly in your 3D printing projects.
The loads and mechanical resistances of inserts
The loads and mechanical resistances of threaded inserts are crucial for ensuring the strength and durability of assemblies in 3D printing projects. Inserts should be selected based on the types of loads they will bear, whether static forces (such as the weight of a part) or dynamic forces (vibrations or impacts). Metal inserts, such as heat-set or threaded inserts, provide better mechanical resistance and are suitable for high loads, while plastic inserts are better suited for lighter applications.
The distribution of loads is also critical: poor placement can create weak points and compromise the integrity of the part. Finally, the strength of the insert also depends on the surrounding material, whose mechanical properties influence the overall effectiveness of the assembly. A good choice of insert, based on the expected loads and resistances, ensures a reliable and durable assembly.
What are the tips and best practices for using threaded inserts in your 3D prints?
By applying some simple tips, you can ensure the best use of your threaded inserts.
Properly prepare the part by taking tolerances into account
Properly preparing a 3D printed part by taking tolerances into account is crucial to ensure a precise and functional assembly. During the design phase, it is essential to define appropriate dimensions and tolerances for threaded inserts and assembly areas, considering possible variations due to the printing process, such as shrinkage or material deformation. It is advisable to allow for wider tolerances in parts that require a fit, while ensuring that the contact surfaces are sufficiently accurate to avoid excessive play.
Using 3D modeling software can help simulate and optimize these tolerances before printing, ensuring that the finished part will meet the functional and mechanical requirements of the intended application. In summary, giving careful attention to tolerances when preparing parts improves the quality of the assembly and the overall performance of printed objects.
Ensure the use of appropriately sized insertion holes.
Ensuring the use of appropriately sized insertion holes is essential for successfully integrating threaded inserts into 3D printed parts. During the design phase, it is crucial to accurately define the diameter and depth of the holes based on the specifications of the chosen inserts, taking into account the recommended tolerances for the type of insert used.
A hole that is too small can cause difficulties during insertion or damage the part, while a hole that is too large can compromise the fixation and mechanical strength of the assembly. It is also important to verify that the insertion holes are correctly positioned to ensure optimal alignment of the components, which contributes to the stability and durability of the finished part. In summary, adhering to the proper dimensions of insertion holes is critical to ensuring the functionality and strength of assemblies in your 3D printing projects.
Use the right tools for insertion
Using the right tools for inserting threaded inserts into 3D printed parts is crucial to ensure efficient and secure installation. Depending on the type of insert chosen, specific tools such as heat guns for heat-set inserts or appropriate wrenches for threaded inserts may be necessary to ensure correct positioning and avoid damaging the part. A good tool also facilitates control over the insertion depth, which is essential for maintaining the integrity of the part and ensuring a strong fixation.
Additionally, using quality tools reduces the risk of deforming the inserts or surrounding materials, thus contributing to the durability and functionality of the final assembly. In summary, choosing the right tools is fundamental to optimizing the insertion process and ensuring the performance of printed parts.
Test the strength of the insert after insertion to verify its robustness
Testing the strength of the insert after insertion is a crucial step to verify its robustness and ensure the reliability of the final assembly in 3D printing projects. This verification can be done through various methods, such as tensile or compression tests, to ensure that the insert can withstand the mechanical forces it will encounter in real-world use.
Fatigue testing is also recommended, as it simulates repeated loading cycles, allowing for the evaluation of the insert’s durability and long-term performance. By incorporating these tests into the development process, you can identify potential weaknesses or failures and make the necessary adjustments before mass production. In summary, rigorous testing of the insert’s strength after installation is essential to ensure the safety and effectiveness of assemblies in your 3D printing applications.
Perform tests on sample parts before moving on to complex projects
Performing tests on sample parts before moving on to complex projects is a crucial step in the 3D printing process, as it allows you to identify and address potential technical or design issues at an early stage. By creating simple prototypes, you can assess the performance of threaded inserts, test tolerances, and verify the robustness of assemblies without risking the compromise of larger and more costly projects. These tests also provide an opportunity to experiment with different materials and printing techniques to optimize choices for specific applications.
By incorporating this testing phase into the development process, you increase the chances of success for future projects, ensuring that the implemented solutions meet functional and mechanical requirements. In summary, testing on sample parts is an essential practice for minimizing risks and improving the quality of final results in your 3D printing projects.
Conclusion: Why adopt threaded inserts in your 3D printing projects?
Adopting threaded inserts in your 3D printing projects offers several significant advantages. They provide a robust and reliable solution for creating strong, durable assemblies that can withstand mechanical stresses and repeated use. Threaded inserts help improve the overall performance of 3D printed parts by ensuring secure connections for screws and bolts, making them ideal for applications that require repeated assembly or disassembly.
Furthermore, using threaded inserts allows for better material efficiency and enhances the versatility of your designs by enabling the use of different materials for the inserts and the 3D printed parts themselves. When combined with proper design considerations, such as precise dimensions, appropriate tolerances, and correct insertion techniques, threaded inserts can dramatically increase the longevity and functionality of your printed assemblies.
In summary, incorporating threaded inserts into your 3D printing projects ensures that your designs are both stronger and more versatile, enhancing their overall reliability and durability. By choosing this approach, you guarantee the quality of your final products and reduce the risks associated with poor assembly or weak connections.
Picture by Freepik.
The articles published on Imprimy.com are for informational purposes only. They are intended to provide general advice and information related to 3D printing. Imprimy.com cannot be held responsible for the results obtained or the consequences arising from the application of the shared information. We recommend always checking the specific instructions for your hardware and materials before use.