Are you wondering about titanium 3D printing? At Imprimy.com, we’re here to answer all your questions related to 3D printing.
Titanium 3D printing makes it possible to produce strong, lightweight, and corrosion-resistant parts, ideal for the aerospace, medical, and automotive sectors.
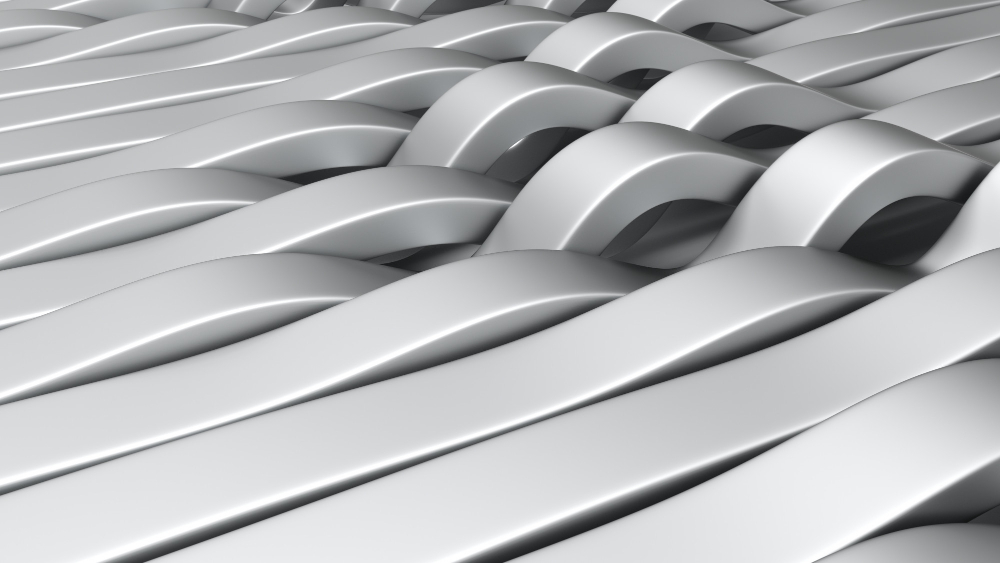
What is titanium 3D printing?
Titanium 3D printing is an additive manufacturing process that uses titanium powder melted layer by layer, often by laser beam or electron beam, to create complex, lightweight, and durable objects, mainly used in the aerospace, medical, and industrial fields.
Definition of titanium 3D printing
Titanium 3D printing is an additive manufacturing process that uses titanium, a metal known for its strength, lightness, and biocompatibility. This process involves the use of a 3D printer to deposit successive layers of titanium powder, which are then fused using a laser or an electron beam. This technology is widely used in the aerospace, medical, and automotive sectors to produce complex and customized components with high precision and excellent surface finish.
Technologies used for titanium 3D printing
The technologies used for titanium 3D printing mainly include two methods: DMLS (Direct Metal Laser Sintering) and SLM (Selective Laser Melting). These technologies use a laser to fuse successive layers of titanium powder, allowing the creation of precise and lightweight metal parts. DMLS and SLM are particularly well-suited for applications in the aerospace, automotive, and medical sectors, thanks to the high laser resolution and the fineness of the powder layers.
Advantages of using titanium in 3D printing
The use of titanium in 3D printing offers several significant advantages. First, titanium is known for its high mechanical strength and lightness, making it an ideal material for applications requiring components that are both strong and lightweight.
In addition, titanium has excellent corrosion resistance, making it suitable for use in harsh environments or those exposed to corrosive substances. Another major advantage is its biocompatibility, meaning it is well tolerated by the human body, making titanium especially useful for medical implants and prosthetics.
Finally, thanks to the precision of 3D printing technologies like DMLS and SLM, it is possible to create titanium parts with complex geometries and fine details, offering great design freedom and enabling the production of custom components with high accuracy.
What are the applications of titanium 3D printing?
The main applications of titanium 3D printing are found in the aerospace, medical, and automotive sectors, as well as in research.
Titanium 3D printing in the aerospace industry
Titanium 3D printing plays a crucial role in the aerospace industry, offering significant benefits in terms of lightness, strength, and durability.
This technology allows for the production of complex and custom-made components, such as turbine blades, structural supports, and engine parts, which are essential for the performance and efficiency of aircraft. Using titanium in 3D printing also helps reduce component weight, which is critical for improving fuel efficiency and lowering carbon emissions in aviation.
In addition, titanium 3D printing results in less material waste compared to traditional manufacturing methods, making it both cost-effective and environmentally friendly. Some companies have already integrated 3D-printed titanium parts into their aircraft. These parts are often produced using advanced technologies that allow for high precision and excellent surface finish.
Moreover, titanium 3D printing offers unprecedented design flexibility, enabling engineers to create complex geometries that would be difficult—or even impossible—to achieve with traditional manufacturing methods. This paves the way for continuous innovation in the design and production of aerospace components.
Titanium 3D printing in the medical sector
Titanium 3D printing is playing a transformative role in the medical sector, offering innovative and customized solutions for a variety of applications. Here are some of the main uses and advantages:
- Custom prosthetics and implants: Titanium is widely used to create tailor-made prosthetics and implants, such as jaws, bones, and joints. These implants are designed to perfectly match the unique anatomy of each patient, improving both comfort and functionality.
- Maxillofacial and dental surgery: In the dental field, titanium 3D printing is used to produce crowns, bridges, and dental implants. It also allows the creation of surgical guides for precise procedures, reducing risks and improving outcomes.
- Bone reconstruction: Titanium is ideal for bone reconstruction, especially in cases of trauma or congenital malformations. Titanium implants are durable and biocompatible, making them suitable for long-term integration into the human body.
- Bioprinting and tissues: While titanium is primarily used for hard structures, 3D printing in the medical sector is also expanding to bioprinting of soft tissues. This opens the door to the creation of artificial tissues and organs, though this technology is still in its early stages.
- Cost and time reduction: 3D printing helps reduce both costs and production times for medical devices. It eliminates the need for expensive molds and enables fast, localized production, which is especially beneficial for custom devices.
- Training and surgical planning: 3D-printed models are also used for surgeon training and preoperative planning. They allow doctors to practice complex procedures and better understand the specific anatomy of patients before surgery.
Titanium 3D printing in the automotive industry
Titanium 3D printing is a cutting-edge technology gaining popularity in the automotive industry due to its many advantages. Titanium, known for its strength, lightness, and durability, is an ideal material for manufacturing automotive components.
Thanks to 3D printing, manufacturers can create complex parts with high precision, while reducing material waste. This technology also allows for increased customization and lower production costs, as it eliminates the need for expensive molds and traditional manufacturing processes.
Furthermore, the use of titanium in the automotive industry contributes to improving vehicle performance, particularly in terms of fuel consumption and emission reduction.
Titanium 3D printing applied to other industries
Titanium 3D printing finds applications in various industries due to its unique properties.
Sectors like chemical and marine industries are beginning to explore this technology to produce corrosion-resistant parts capable of withstanding harsh environments. Finally, titanium 3D printing is also used in general industrial applications where material waste reduction and the creation of lightweight designs are crucial.
What is the manufacturing process for titanium 3D printed objects?
The manufacturing process for titanium 3D printed objects begins with the creation of a 3D digital model, followed by the layer-by-layer deposition of titanium powder fused by a laser or electron beam, and ends with steps of cooling, cleaning, and sometimes thermal or mechanical treatments to improve the mechanical properties and surface finish.
Preparation of the 3D model for titanium printing
The preparation of a 3D model for titanium printing is a meticulous process that begins with the design of the model, where geometry optimization and wall thickness are essential to ensure structural strength while reducing weight. It is crucial to add support structures to prevent deformations during printing, which will be removed later.
The model must then be exported in a compatible format, such as STL or 3MF, and checked to correct any errors. The orientation of the model on the print bed and the configuration of printer settings, like temperature and print speed, are also important steps to optimize surface quality and minimize supports.
Finally, after printing, support removal and the application of additional finishing processes, such as polishing or thermal treatment, are necessary to improve the mechanical properties and appearance of the printed part.
The titanium 3D printing phase
The titanium 3D printing phase is a complex process that requires careful attention to several aspects to ensure the quality and precision of the final part. Here are the key steps of this phase:
Printer preparation:
- Calibration: Make sure your 3D printer is properly calibrated to ensure accurate printing. This includes calibrating the axes, temperature levels, and speed parameters.
- Material loading: Load the titanium powder into the printer. Titanium is generally used in the form of fine powder for 3D printing technologies such as SLM or Directed Energy Deposition (DED).
Printing parameters:
- Temperature: Set the printer’s temperature according to titanium specifications. Titanium requires high temperatures to properly melt and solidify.
- Print speed: Configure the print speed to optimize the part quality. Too high a speed can cause defects, while too slow increases production time.
- Layer thickness: Define the layer thickness based on the desired resolution. Thinner layers allow for better precision but increase the printing time.
Printing process:
- Start of printing: Begin the printing process. The printer deposits the titanium powder layer by layer and uses a laser or electron beam to melt and solidify each layer.
- Monitoring: Monitor the printing process to quickly detect and correct potential issues, such as warping or fusion defects.
Post-processing adapted to titanium 3D prints
The post-processing of 3D printed titanium parts is a crucial step to improve their mechanical properties, appearance, and functionality. Here are the main post-processing methods suitable for titanium 3D prints:
Support removal:
After printing, the support structures added during preparation must be carefully removed. This can be done manually or with specialized tools to avoid damaging the part.
Cleaning:
- Residual powder cleaning: Titanium printed parts may have residual powder that needs to be removed, using soft brushes or ultrasonic cleaning systems.
- Chemical cleaning: Use chemical solutions to eliminate powder residues and surface contaminants.
Thermal treatment:
- Annealing: Annealing is a heat treatment process where the part is heated to a specific temperature and then slowly cooled to relieve internal stresses and improve ductility.
- Solution treatment and aging: These processes can be used to improve the strength and hardness of the titanium part.
Surface finishing:
- Polishing: Mechanical or electrolytic polishing can be used to achieve a smooth and shiny surface, enhancing the appearance and reducing surface roughness.
- Machining: Precision machining may be necessary to meet final dimensional tolerances and specific surface finishes.
Inspection and quality control:
- Visual inspection: Check the part visually for surface defects and imperfections.
- Non-destructive testing (NDT): Use NDT methods such as radiography or ultrasound to detect internal defects and ensure the integrity of the part.
What are the challenges and limitations of titanium 3D printing?
The main challenges and limitations of titanium 3D printing include the high cost of materials and equipment, the need for strict conditions, long production times, risks of internal defects, and complex post-processing requirements to ensure the quality and reliability of the parts.
Costs associated with titanium 3D printing
The costs associated with titanium 3D printing can vary depending on several factors. First, the price of titanium powder, which is generally high due to the rarity and properties of the material, represents a significant part of the total cost. Next, the manufacturing process, including machine preparation, energy consumption, and printing time, also influences the cost. 3D printers capable of working with titanium are often expensive to purchase and maintain. Additionally, post-processing fees, such as polishing and thermal treatments, are necessary to achieve the desired mechanical properties, adding another layer of costs.
Finally, the complexity of the part and the production quantity play a crucial role, as complex geometries may require more time and materials, while economies of scale can reduce the cost per unit for mass production.
The complexity of titanium 3D printing
Titanium 3D printing presents several complexities that distinguish it from other additive manufacturing processes. Titanium is a reactive material that requires specific processing conditions to avoid defects such as porosity or cracks. Process parameters like temperature, deposition speed, and build atmosphere must be carefully controlled to ensure the quality of the part.
Moreover, the management of titanium powder is crucial, as it must be handled in inert environments to prevent contamination or undesired reactions. The design of parts must also consider the constraints related to 3D printing, such as the need for supports for complex geometries and residual stresses that can develop during the process.
Finally, post-processing, including support removal, polishing, and thermal treatments, adds an additional layer of complexity to achieve the desired mechanical and surface properties.
Limitations of titanium 3D printing
Titanium 3D printing has several limitations that can affect its adoption and effectiveness across various industries. One of the main constraints is the high cost associated with both the material and the process, making this technology less accessible for small businesses or budget-limited projects.
Additionally, the size of parts is often limited by the capacity of 3D printing machines, which can restrict applications for large components. Surface quality and dimensional accuracy can also pose challenges, often requiring additional post-processing steps to meet the required specifications. Another limiting factor is the production speed, which is generally slower than traditional manufacturing methods, making it less ideal for mass production.
Finally, the mechanical properties of titanium printed parts can vary and require careful optimization of process parameters to meet the demands of critical applications.
Innovations and the future of titanium 3D printing
The innovations and future of titanium 3D printing rely on the development of faster and more precise machines, new optimized alloys, and advanced simulation software, as well as on the integration into mass production. This paves the way for a more sustainable, customized, and competitive manufacturing in sectors such as medicine, aerospace, and defense.
Research and development in titanium 3D printing
Research and development in the field of titanium 3D printing focus on several fronts to overcome current challenges and expand potential applications. Efforts concentrate on optimizing process parameters to improve part quality and reduce defects such as porosity.
Researchers are also exploring new powder processing methods to enhance the reactivity and handleability of titanium. Another key area is the development of more advanced 3D printing machines capable of producing larger and more complex parts with better precision. Innovation in post-processing techniques is also crucial to improve the mechanical properties and surface finish of printed parts.
Finally, research is underway to reduce costs associated with titanium 3D printing by exploring material alternatives and more efficient production methods.
Future prospects of titanium 3D printing
The future prospects of titanium 3D printing are extremely promising, especially in the sectors of aeronautics, medicine, and automotive, thanks to its unique properties such as high mechanical strength, lightweight, and biocompatibility. The evolution of additive manufacturing technologies enables the production of complex, customized, and material-optimized parts, thereby reducing waste and production costs.
Furthermore, advances in printing speed, powder quality, and process repeatability make this technology increasingly viable for large-scale production, paving the way for innovative applications in strategic fields.
Environmental impact of titanium 3D printing
The environmental impact of titanium 3D printing presents both advantages and challenges: on one hand, this technology allows for a significant reduction of waste compared to traditional subtractive manufacturing methods, an optimization of material use, and a decrease in the carbon footprint related to transportation thanks to the possibility of local production.
However, it remains energy-intensive, particularly due to the high temperatures required for the fusion of titanium and the production of metal powder, which is a complex and energy-consuming process. Therefore, it is essential to improve energy efficiency and develop recycling loops to limit the overall environmental impact.
Conclusion: Titanium 3D Printing
In conclusion, titanium 3D printing represents a technological revolution with diverse and strategic applications, offering notable advantages in terms of part performance, customization, and waste reduction.
Despite challenges related to its energy cost and powder production, its ongoing development, combined with sustainable innovations, makes it a future solution for industries seeking lightweight, strength, and precision.
Picture by kjpargeter from Freepik.
The articles published on Imprimy.com are for informational purposes only. They are intended to provide general advice and information related to 3D printing. Imprimy.com cannot be held responsible for the results obtained or the consequences arising from the application of the shared information. We recommend always checking the specific instructions for your hardware and materials before use.