Do you want answers to all your questions about 3D print warping? At Imprimy.com, we’re here to help you.
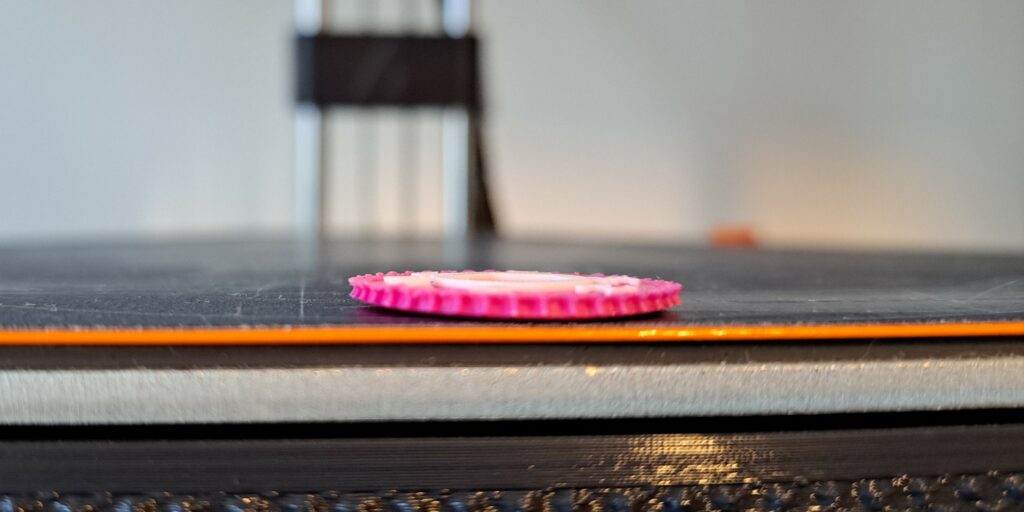
What is 3D print warping?
Warping is a deformation that occurs when one of your 3D prints detaches from the print bed during the manufacturing process.
Definition of warping
The definition of warping is the deformation that occurs when a 3D print lifts or distorts, usually at the edges or corners, due to uneven cooling or thermal contraction of the material during the printing process.
The different symptoms of warping
The different symptoms of warping include:
- Lifting Corners or Edges: The corners or edges of the print may lift off the print bed, creating a noticeable gap.
- Uneven Surface: The surface of the print may become wavy or distorted, with areas higher than others.
- Cracks or Gaps: Cracks or gaps may form in the layers of the print, especially as the material cools unevenly.
- Warped Shape: The overall shape of the object becomes misshapen, often causing parts of it to bend or curl upward.
- Poor Adhesion: The layers of the print may not bond well, leading to poor adhesion between layers or to the print bed.
These symptoms indicate that warping is occurring and can affect the quality and accuracy of the print.
What are the main causes of warping in 3D printing?
The main causes of warping in 3D printing come from the printing temperature, the print surface, filament retraction, machine maintenance, and the design of the model you want to print.
The temperature of the print surface
The temperature of the print surface plays a crucial role in managing warping in 3D printing. If the print surface is too cold, the material can cool down too quickly, causing excessive shrinkage and deformation at the edges of the part. Insufficient temperature can exacerbate the warping issue by reducing adhesion between the layers and the bed.
On the other hand, maintaining the print surface at an optimal and stable temperature promotes uniform adhesion and reduces the risk of deformation. Heated beds are often used to maintain a constant temperature, thus minimizing the effects of warping and improving the overall quality of your prints. Properly adjusting the print surface temperature is essential for achieving precise and high-quality results in your 3D printing projects.
The temperature of the nozzle
The temperature of the nozzle and the extruded material plays a significant role in preventing warping during 3D printing. If the extrusion temperature is too high, the material may cool too quickly after being deposited, causing uneven shrinkage and leading to warping. On the other hand, if the extrusion temperature is too low, the material may not properly adhere to the print surface, resulting in weak adhesion between layers and increasing the risk of warping.
To avoid warping, it is crucial to set the extrusion temperature within the recommended range for the specific filament you are using. This ensures that the material flows smoothly and adheres well to the surface while also cooling at a controlled rate, reducing the chances of deformation.
The issue of material retraction
The retraction of the material is an important factor in preventing warping in 3D printing. Retraction refers to the process where the filament is pulled back into the nozzle when the printer head moves between areas without printing. If the retraction settings are not properly adjusted, it can lead to excessive filament being pulled back, or in some cases, not enough retraction, both of which can contribute to warping.
If there is too much retraction, the filament might not be extruded smoothly when needed, causing uneven layer deposition and leading to warping. Conversely, insufficient retraction can cause the nozzle to drip material when moving between print areas, which can lead to unwanted blobs or strings that impact the adhesion of layers and cause warping.
To prevent warping, it’s essential to fine-tune the retraction settings, including the distance and speed, according to the type of filament used and the specific 3D printer. This ensures better material flow and adhesion, reducing the chances of deformation during the printing process.
The design and geometry of the model
The design and geometry of the model are key factors in preventing warping in 3D printing. A model with poor geometry can exacerbate the effects of warping, especially if sharp angles, large flat surfaces, or extended sections are present. It is advisable to design models with appropriate supports and avoid large horizontal planes that cool quickly and cause deformation.
Incorporating design elements such as reinforcements or grid structures can also help reduce thermal stress and improve adhesion to the print bed. By optimizing the geometry of your model to minimize large areas of rapid cooling and integrating features that promote better adhesion, you can significantly reduce the risks of warping and improve the quality of your 3D prints.
Cleaning the print surface
Cleaning the print surface is an essential factor in preventing warping in 3D printing. A dirty or poorly prepared print bed can lead to poor adhesion of the first layer, which increases the likelihood of warping. Dust, oil, or leftover filament can interfere with the adhesion of the material to the bed, causing uneven cooling and warping at the corners or edges of the print.
To ensure proper adhesion, it is important to regularly clean the print surface using isopropyl alcohol or a suitable cleaning solution. Additionally, make sure the print bed is free from debris and well-maintained to achieve a clean, smooth surface that improves print quality and reduces the risk of warping.
What are the effects of warping on 3D prints?
Warping generally impacts the quality of your parts, increasing both the print time and the manufacturing costs of your parts.
The impact of warping on the quality of your parts
The impact of warping on the quality of your 3D printed parts can be significant and varied. When warping occurs, the edges or corners of the parts can deform, compromising the adhesion between layers and the dimensional accuracy of the object. These deformations can result in visible irregularities on the surface, cracks, or detachment, affecting both the aesthetic and functional aspects of the part.
Additionally, parts showing signs of warping may not fit correctly with other components or fulfill their intended function, leading to fit or performance issues. Effective management of warping is therefore crucial to ensure that your printed parts meet the expected quality outcomes, maintaining their structural integrity and flawless finish.
The consequences on cost and printing time
The consequences of warping on cost and printing time can be significant. When a warping issue occurs, it can lead to defects that require rework or repair of the parts, thus increasing the number of prints needed and, consequently, production costs.
Additionally, the time lost in addressing warping-related issues and restarting prints can extend the project timeline. The adjustments and tests required to correct the effects of warping also add time to each production cycle. By minimizing warping through proper adjustments and careful preparation, you can not only reduce the costs associated with defective parts but also optimize manufacturing time, ensuring more efficient and cost-effective production.
How to prevent and correct warping during the 3D printing process?
To prevent and correct the effects of warping on your 3D prints, you should optimize the printing temperature, use specific surfaces, and possibly modify the model to ensure a successful print.
Optimizing the printing temperature
Optimizing the printing temperature is crucial to minimize the effects of warping and improve the quality of your 3D printed parts. By correctly adjusting the nozzle and print bed temperatures, you can promote better layer adhesion and reduce the risk of deformation. It’s important to follow material-specific recommendations, as each type of filament has an optimal temperature range for proper extrusion and cooling.
A temperature that’s too high can lead to excessive extrusion and poor layer adhesion, while a temperature that’s too low can cause inadequate material fusion and deformation. By precisely calibrating your 3D printer’s temperature and ensuring the print surface remains at a stable temperature, you can significantly reduce warping, enhance dimensional accuracy, and achieve high-quality results in your 3D printing projects.
The use of print surfaces and adhesives
The use of print surfaces and adhesives is an effective strategy to combat warping in 3D printing. By choosing suitable print surfaces, such as heated beds or textured surfaces, you can improve the adhesion of the model’s first layers, helping to prevent deformations and edge lifting. Heated surfaces maintain a stable temperature, reducing material shrinkage during cooling.
Additionally, applying specific adhesives, such as sprays or tapes designed for 3D printing, can enhance adhesion between the model and the bed, thus minimizing the risk of warping. By combining a quality print surface with the appropriate adhesives, you create a favorable environment for uniform and stable adhesion, contributing to more accurate prints and reducing deformation issues.
Improving the model design
Improving the model design is essential for reducing the risk of warping and ensuring optimal print quality. By adjusting the geometry of your 3D model, you can minimize large flat surfaces and sharp angles, which are more likely to deform during cooling. Incorporating reinforcement structures or supports can help stabilize parts of the model that are prone to lifting.
It is also useful to add details such as rounded edges instead of right angles, which helps distribute thermal stress more evenly. By designing models with features that promote good adhesion to the bed and minimal shrinkage, you can reduce the effects of warping, improve the accuracy of your prints, and achieve more reliable results. Thoughtful design is, therefore, a key element in optimizing your 3D printing projects and ensuring high-quality parts.
Controlling the printing environment.
Controlling the printing environment is crucial for preventing warping and ensuring the quality of your 3D printed parts. Maintaining a stable ambient temperature around the printer helps avoid sudden fluctuations that can cause material deformation during cooling. Using printers equipped with enclosed chambers or heated enclosures can help stabilize the temperature and reduce drafts that negatively affect the printing process.
Additionally, controlling the humidity in the environment can also play an important role, as excessive humidity can affect material properties, increasing the risk of warping. By ensuring that the printing environment is stable and well-controlled, you promote better adhesion between layers and uniform solidification, which contributes to achieving high-quality 3D prints without unwanted deformations.
What are the tools and accessories to fight warping?
To improve adhesion in your 3D prints, you can consider heated beds, specific materials, or even test certain settings in your slicing software.
3D printers with heated beds
3D printers equipped with heated beds offer a significant advantage in managing warping. By maintaining the bed at a constant temperature, these printers promote better adhesion of the model’s first layers, reducing the risk of deformation and edge lifting during cooling. Heated beds help minimize the effects of material shrinkage by maintaining uniform heat, which contributes to more even solidification.
This not only reduces warping issues but also improves the overall quality of your prints by ensuring strong adhesion throughout the process. By incorporating a heated bed into your 3D printer, you optimize your printing conditions and achieve more precise and reliable results while reducing defects associated with warping.
The use of special materials and coatings
The use of special materials and coatings can significantly help manage warping in 3D printing. Some materials are designed to reduce the tendency for shrinkage and minimize deformation during cooling. For example, low-shrinkage filaments or composite materials with specific additives can offer better stability and improved adhesion to print surfaces.
Additionally, applying special coatings to the bed, such as adhesive films or sprays, can enhance adhesion by preventing edge lifting. These coatings create a more adhesive surface, reducing the risk of warping. By selecting the appropriate materials and using suitable coatings, you can optimize printing conditions and achieve more precise, higher-quality parts while minimizing the effects of warping.
Slicing software and printing settings
Slicing software and printing settings play a crucial role in managing warping in 3D printing. Slicing software allows you to adjust various parameters that can influence the tendency for warping, such as nozzle temperature, bed temperature, print speed, and fill density. By adjusting these settings based on the material and model characteristics, you can improve layer adhesion and reduce deformation.
For example, some software offers options to add supports or specific adhesion structures that help stabilize parts during printing. By using these tools to optimize your printer settings, you can reduce the risk of warping and achieve more reliable, higher-quality results. Proper configuration of print settings is therefore essential for minimizing deformation issues and ensuring the success of your 3D printing projects.
Conclusion: 3D Print Warping
Warping is a common challenge in 3D printing that can affect the quality and accuracy of your prints. It occurs when material shrinkage during cooling leads to deformation, often causing edges to lift or parts to become misaligned. However, by understanding its causes and implementing preventive measures, such as optimizing print temperature, using heated beds, choosing the right materials, adjusting design geometry, controlling the printing environment, and fine-tuning print settings, you can minimize warping and improve print quality.
Incorporating these strategies ensures better adhesion between layers, more stable prints, and ultimately higher-quality results. By addressing warping at every stage of the 3D printing process, you can produce more reliable and precise parts, reducing material waste and improving overall production efficiency.
Photo by Imprimy.com
The articles published on Imprimy.com are for informational purposes only. They are intended to provide general advice and information related to 3D printing. Imprimy.com cannot be held responsible for the results obtained or the consequences arising from the application of the shared information. We recommend always checking the specific instructions for your hardware and materials before use.